Soft cost drivers – an important factor
That reason is whether your role is managerial, commercial or technical there is a good chance that you have an interest in ensuring that the printed circuit boards you are purchasing, designing or assembling are as efficient as they can be in terms of achieving what we see as the lowest total cost, without compromising functionality or reliability of the end product.
Ruben Contreras, Field Application Engineer from NCAB Group’s U.S. West Coast office, recently wrote an excellent blog relating to the Hard Cost Drivers in PCB production , covering aspects that relate to physical printed circuit board itself. Examples being copper weights and build complexity. Today, I will attempt to cover the other category – Soft Cost Drivers.
Activity Based Costing – Soft Cost Drivers
Anyone involved in manufacturing will, at some point, have been introduced to the ABC principle for identifying and allocating costs in manufacturing – Activity Based Costing. This principle looks at identifying the costs of production hours, extra engineering hours, production delays or stops or managing unexpected risks. This is similar when it comes to considering Soft Cost Drivers in PCB production – identifying those elements that unless considered can lead to delays in engineering, lost time and mis-specifiying demands that only serve to either drive cost upwards or fail to identify what is needed to achieve the desired quality or long term reliability – this is not sustainable PCB production in our eyes.
Quality first
The first driver for consideration is that of a lack of vital information that is either necessary to complete a quotation or, even worse, necessary to complete the pre-production engineering efficiently at the very start of the process. The problem is that when vital information is missing this will cause a delay in production as you have to review the data again, looking for missing information and in the vast majority of cases this leads to engineering questions being raised at the very start. This costs time and quite frequently the lost time can lead to costly delays as this is typically associated with new data, for new projects, when time to market is critical.
If we do not stop to seek clarification then it is entirely possible that customer expectations will not be adequately understood and errors may be introduced at this stage – errors that will be carried all the way through production, so that no matter how well the PCB is made, it will be delivered on time, yet perfectly wrong. Of course, some producers may elect to make assumptions with data and unclear demands…. but taking such a risk is not in line with the Quality First values at NCAB.
Examples of missing vital information may include:
- Desired base material characteristics
- Impedance demands
- Missing specifications
- Unclear surface finish
- Missing build detail such as total thickness tolerances, dielectric requirements
- Soldermask information
Over specification is also a risk
Following on from lack of vital information, we also encounter instances where we see the opposite challenges – that of over specification. This is where we experience too much information provided with the data and the challenge here is that it may often take more time to review every single piece of information in order to determine which elements are critical for the manufacture and verification or acceptance of the PCB. The risk here is not only lost time, but also of potentially missing something critical. Equally, we may come across instances where there is so much information provided that we see conflicting demands and, again, this is something that will cause the order to be placed on hold whilst clarification is sought to determine exactly what is needed or what takes precedence.
Examples of over specification may include:
- Long specifications submitted with each new project, even if already submitted as part of the agreements package as we have to review.
- References to specifications that are either outdated or not widely used outside of the country where they originated. In many cases the responsibility is on manufacturing to identify and seek approval for a recognized equivalent.
- Over specification of demands that are either not applicable for the technology in question or carry excessive reliability demands despite the actual purpose of the product. These demands can drive cost upwards.
Knowing when to use and not to use IPC class 3
The third element relates to the final example as detailed above – that of excessive reliability demands associated with calling out the need for IPC class 3 without truly understanding what IPC class 3 demands actually entails. Such a broard statement can lead to significant consequences in terms of the cost of the PCB being supplied and also a narrowing of the supply chain options for producing volume orders.
In some industries the demand for IPC class 3, including the related demands for process control and verification, may be absolutely necessary, yet in some cases it may not. Consider a PCB that is part of a life critical product where uninterrupted use is an absolute must where no downtime can be tolerated and consider one which is used in a consumer product. It is clear that the former warrants the high level of verification according to IPC-6012 and the significant costs that come with it.
In summary, the call for class 3 does not automatically relate to advanced products or designs, but it does ensure that the high level of verification provides confidence that the PCB is fit for the advanced purposes of the end product.
Get it right from start
It is said, that a little knowledge in the wrong hands can be dangerous. Yet, it poses an even greater risk when there is a lack of knowledge or a lack of willingness to get it right as early as possible in the process. We often see poor elements of design, wasteful panelisaton or unsuitable materials being requested and sometimes, we do see a lack of willingness to make the required levels of changes. Often we are told that “it’s only the prototype, we can fix it later”, yet the design is approved and the changes never happen.
However….. if we can engage and build on the desire to get it right from the start, then we can share knowledge and experience so that the end result is a reliable PCB, delivered on time with zero defects, produced sustainably at the lowest total cost.
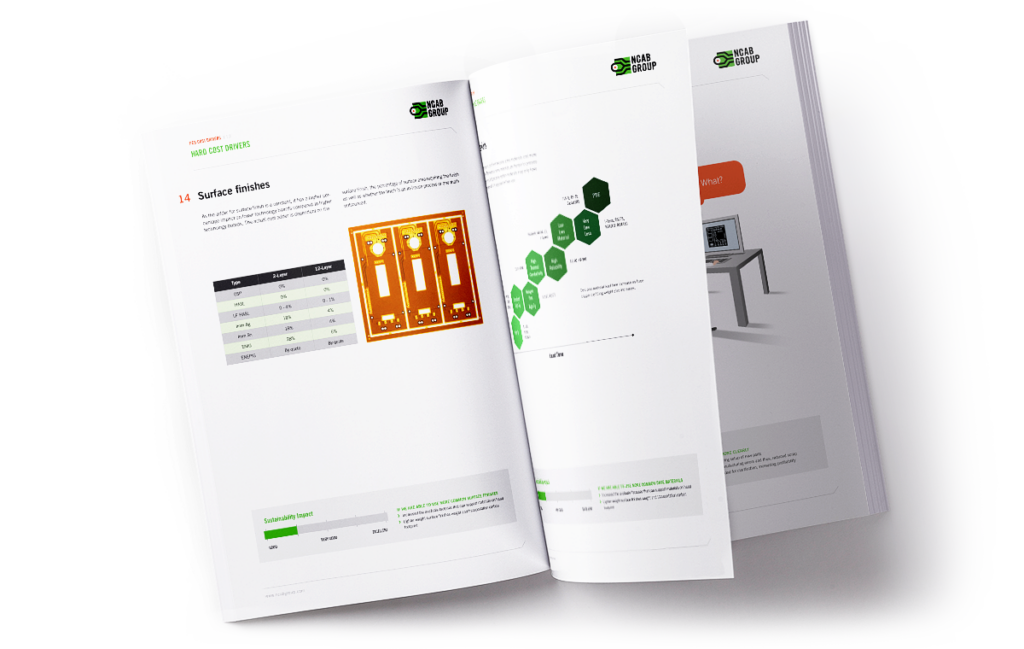
What drives the cost of a circuit board?
And how do those factors in turn impact the sustainability? To avoid large cost drivers we have developed a tool that can support you.