Cresce sempre più la necessità di soluzioni per gestire il calore in eccesso nei prodotti elettronici. I rapidi sviluppi tecnologici hanno fatto aumentare questo requisito, la stessa cosa accade per quanto riguarda i PCB. In questo numero, gli esperti di NCAB descrivono gli sviluppi in quest’area e i metodi disponibili per la gestione termica.
più articoli sull’argomento:
Nei moderni sistemi elettronici, e soprattutto nelle applicazioni di potenza, dobbiamo sempre porre attenzione su due principali aspetti; efficienza e gestione termica. L’efficienza determina quanta potenza viene effettivamente trasferita senza perdite. La gestione termica cerca di garantire che i dispositivi nel sistema possano funzionare pur rimanendo a un livello di temperatura accettabile. Fondamentalmente, la gestione termica si riferisce ai metodi utilizzati per trasferire il calore in eccesso da un luogo a un altro.
Tradizionalmente questo veniva ottenuto fissando un dissipatore di calore esterno su un particolare componente che generava calore. Ma cosa succede se il PCB stesso genera il calore? O se il tuo componente non consentisse fisicamente di fissare un dissipatore di calore sopra?
La corrente che non viene trasferita correttamente si trasforma inevitabilmente in energia termica. Questa energia termica deve essere rimossa, in modo da non provocare un aumento della temperatura dei dispositivi. Se questo non è adeguato potrebbe portare danni ai componenti o comunque ad una riduzione della loro vita.
Nel caso di dispositivi elettronici e PCB, il nostro obiettivo è trasferire il calore in eccesso lontano dal componente, dissipando il calore all’interno o attraverso il PCB da un lato all’altro. A volte lo facciamo in combinazione con soluzioni attive come la ventilazione e dissipatore di calore esterno o raffreddamento a liquido.
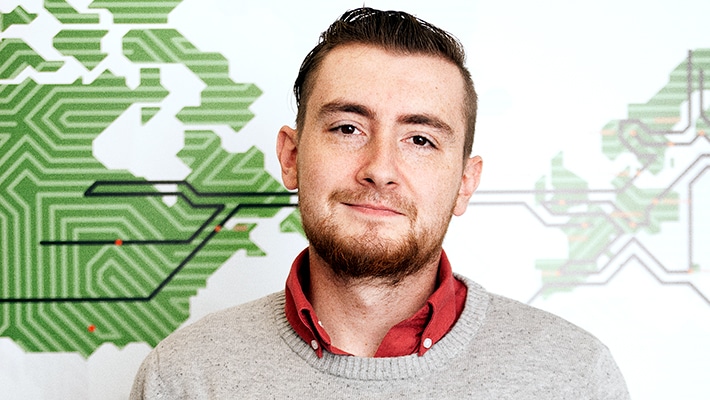
“È necessario essere creativi e trovare nuovi approcci per dissipare o convogliare il calore in eccesso.”
Jeffrey Beauchamp
Technical/Engineering Manager, NCAB Group USA
L’innovazione aumenta la necessità di gestione termica
Negli ultimi anni, abbiamo assistito ad una costante crescita e del bisogno di soluzioni tecniche per la gestione termica nei sistemi elettronici. Jeffrey Beauchamp, Technical Manager presso NCAB Group USA e Mario Cianfriglia, Field Application Engineer presso NCAB Group Italy, spiegano come questa esigenza sia stata guidata dalle innovazioni tecniche del settore.
“Una delle tendenze più importanti nella produzione di elettronica in questo momento riguarda la miniaturizzazione, con prodotti e componenti sempre più piccoli, nonché circuiti stampati più compatti. Ciò rende sempre più difficile applicare soluzioni tradizionali come i dissipatori di calore perché occupano troppo spazio. Quindi devi essere creativo e trovare nuovi approcci per dissipare o reindirizzare il calore in eccesso “, spiega Jeffrey Beauchamp.
Un altro nuovo fattore che i progettisti devono affrontare è la gestione delle temperature più elevate generate da nuovi componenti che eseguono più funzioni, processi di calcolo a velocità più elevate, questo porta i componenti a dover dissipare piu energia termica.
“In sostanza i PCB sono costretti ad essere miniaturizzati, per poter utilizzare componenti elettronici sempre più piccoli, in cui le interconnessioni si sono evolute in termini di quantità x centimetro quadrato (Cm2). Tutto questo per ospitare componenti di ultima generazione con pitch 0,4 mm o inferiore, che gestiscono i segnali digitali e di potenza “, afferma Mario Cianfriglia.
”In sostanza, si è obbligati a miniaturizzare i PCB per utilizzare componenti elettronici di dimensioni sempre più ridotte.”
Mario Cianfriglia
Field Application Engineer, NCAB Group Italy
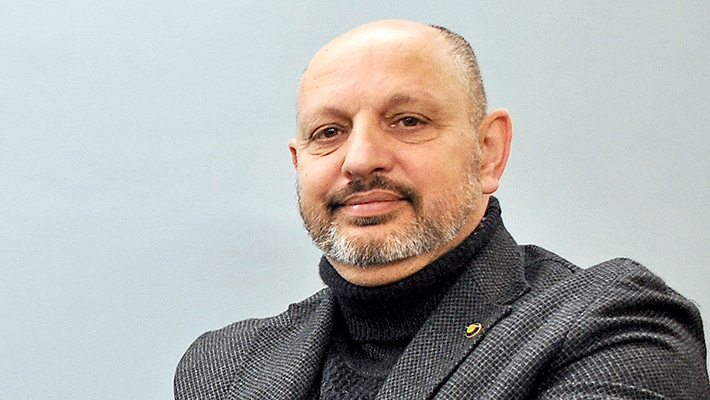
Gestione termica delle applicazioni, una sfida importante
Mario Cianfriglia sottolinea inoltre che i progettisti stanno affrontando nuove sfide da quando l’elettronica ha iniziato ad essere integrata in un numero sempre crescente di applicazioni.
“In alcuni casi, la gestione del calore può essere estremamente impegnativa, ad esempio nel settore energetico, nelle applicazioni industriali o nel settore automobilistico, soprattutto quando si tratti di veicoli elettrici. Lo stesso vale per applicazioni più complesse, come quelle impiegate nelle telecomunicazioni o nei sistemi radar” afferma. Con l’avvento del 5G, la quinta generazione delle comunicazioni mobili, i prodotti elettronici incorporeranno un numero crescente di componenti che funzioneranno a velocità ancora più elevate, generando maggiore calore da dover dissipare. Allo stesso tempo, sarà assolutamente essenziale garantire l’integrità del segnale nelle applicazioni 5G.
“I PCB sono attualmente in grado di gestire segnali da 3 a 5 GHz, ma con la piena funzionalità del 5G dovranno gestire segnali di circa 25 GHz e oltre.”
Mario Cianfriglia
Field Application Engineer, NCAB Group Italy
“Questa è l’ultima frontiera della tecnologia, dove è essenziale l’integrità del segnale. I PCB sono attualmente in grado di gestire segnali da 3 a 5 GHz, ma con la piena funzionalità del 5G dovranno gestire segnali di circa 25 GHz e oltre. Per garantire l’integrità del segnale in tutte le condizioni operative, è molto importante disporre della corretta gestione termica. I PCB con segnali ad alta frequenza devono essere progettati; con uno stack-up adeguato, materie prime speciali, un determinato percorso delle tracce e i piani di massa, piani di alimentazione e segnale”, afferma Mario Cianfriglia.
“Stiamo appena iniziando a vedere un aumento della domanda per la gestione termica e penso che probabilmente continuerà ad aumentare. Si spera che con esso arrivino nuove misure più avanzate per la gestione delle problematiche legate al calore “, afferma Jeffrey Beauchamp.
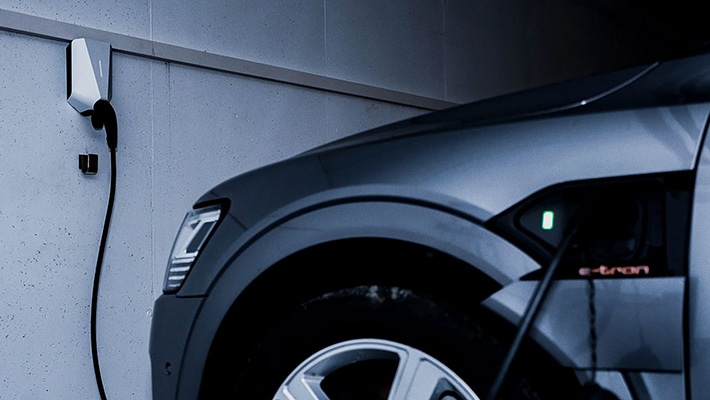
Software di analisi consentono di prevenire i problemi
Nello sviluppo del progetto, vengono utilizzate varie tecniche per individuare potenziali problemi legati al calore. Sono stati sviluppati pacchetti software per le analisi preventive. È importante che tutto sia dimensionato correttamente già in fase di progettazione delle schede. Qui è necessario conoscere i requisiti dei componenti, le dimensioni della traccia e dello spazio in base a ciò che dovranno supportare — in termini di velocità del segnale e potenza — e selezionare lo spessore adatto del rame e del materiale di base.
Esistono inoltre strumenti di analisi termica, molti pacchetti software vengono utilizzati per un’analisi preventiva, in cui tutto può essere dimensionato a livello di progettazione. È necessario conoscere le esigenze dei componenti, dimensionare la traccia e lo spazio in base a ciò che devono supportare in termini di segnali veloci e potenza, selezionare il giusto peso o spessore del rame e un laminato di base adeguato. L’ispezione visiva, ha senso sui PCB semplici, dedicati essenzialmente alla potenza. Il riscaldamento provoca nel tempo il deterioramento del laminato di base e porta alla carbonizzazione delle resine, per cui nella prima fase si osserva un imbrunimento della zona dove si sviluppa energia termica.
È possibile simulare il funzionamento dell’oggetto PCBA e verificare con termocamere a infrarossi dove la temperatura è oltre quanto consentito. Ma a questo punto siamo già in una zona di non ritorno, dove il progetto è già definito. Questa è solo una condizione adatta per identificare un’anomalia.
Il nostro suggerimento è sempre quello di essere coinvolti nella prima fase del progetto, dove il vostro fornitore di PCB può fornire suggerimenti e mettere il progettista nelle condizioni di fare un ottimo lavoro “, dice Mario Cianfriglia.
Da dove nasce il bisogno di gestione termica
- Miniaturizzazione, con un numero sempre maggiore di componenti su PCB più compatti
- L’elettronica viene integrata in un numero crescente di applicazioni.
- I componenti diventano più veloci e quindi generano più calore.
- La nuova tecnologia si traduce in frequenze di segnale più elevate e gestione della potenza che generano più calore
- L’integrità del segnale diventa più importante con il 5G, che aumenta la sensibilità alla gestione del calore
Coinvolgere gli specialisti nella fase iniziale
“I progettisti davvero capaci eseguono simulazioni termiche prima di costruire le schede e hanno un’idea di ciò che potrebbero vedere. Ma molte aziende non dispongono delle capacità per eseguire calcoli termici complessi né hanno il software necessario, quindi applicano semplicemente le migliori pratiche e si pongono il problema solo quando questo emerge. Poi a volte si rivolgono a noi dopo aver eseguito test e aver rilevato problemi legati al calore”, afferma Jeffrey Beauchamp.
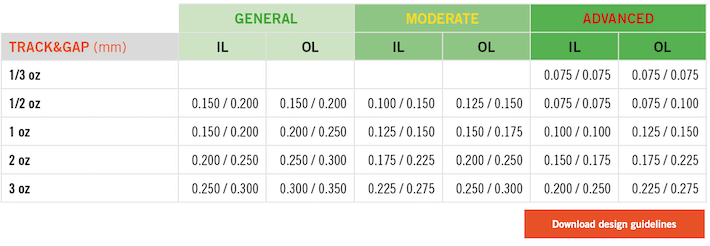
Raccomanda invece alle aziende di coinvolgere specialisti come NCAB già nella fase iniziale del processo di progettazione.
“Scegliere sin da subito l’alternativa giusta, consente di risparmiare tempo e denaro.”
Jeffrey Beauchamp,
Technical/Engineering Manager, NCAB Group USA
“In questo modo potremmo suggerire uno stack-up o un materiale alternativo ed evitare i problemi in modo semplice e rapido”, afferma e continua: “A volte ciò potrebbe non bastare e dovremmo trovare una soluzione più complessa. Ma è pur sempre vantaggioso coinvolgerci prima, perché può essere sia dispendioso in termini di tempo sia in termini economici. Ciò che sarebbe ricostruire una scheda e testarla di nuovo. In NCAB, insistiamo sempre ad operare bene sin dall’inizio, a maggiora ragione quando si tratta di gestione termica, questo principio è ancora più importante perché questi tipi di schede sono più costose da produrre. Scegliere sin da subito l’alternativa giusta consente di risparmiare tempo, problemi e denaro.”
Come si gestisce il calore in eccesso a livello di scheda nuda?
Ci sono diversi modi per gestire il calore in eccesso a livello di scheda nuda. Poniamo qualche domanda su questo tema a Jeffrey Beauchamp e Mario Cianfriglia.
Quando è necessario prendere in considerazione soluzioni speciali per la gestione termica a livello di scheda nuda e non solo a livello di assieme?
Jeffrey Beauchamp (JB): “A livello di assieme, il calore viene dissipato nell’atmosfera utilizzando tubi di calore o dissipatori di calore, se necessario con un qualche tipo di raffreddamento a ventilazione o a liquido. Se questo non risolve il problema del calore, è necessario esaminare le soluzioni a livello di scheda nuda. Il livello di assieme e il livello della scheda nuda vanno di pari passo. Perché il livello di assieme preleva il calore e lo sposta nell’atmosfera, mentre a livello di scheda nuda preleviamo il calore e lo spostiamo in superficie attraverso la scheda stessa, affinché il raffreddamento possa avvenire.”
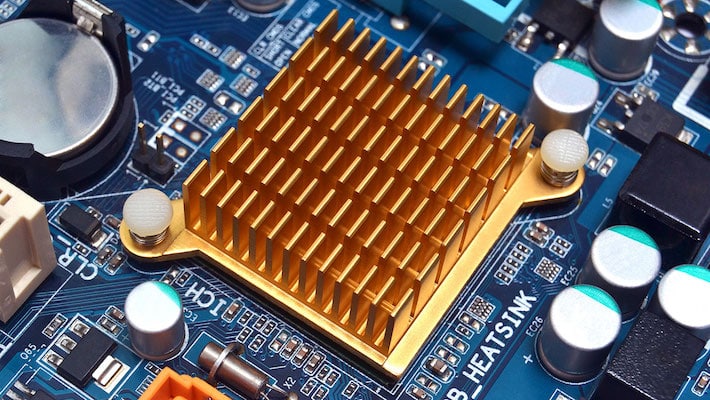
Come si gestisce il calore in eccesso a livello di scheda nuda?
Mario Cianfriglia (MC): “In un progetto correttamente gestito, la fase di progettazione avrebbe dovuto già considerare come posizionare i componenti sul scheda e il dimensionamento delle tracce. È anche importante assicurarsi che lo spessore del rame sia sufficiente per evitare l’accumulo di calore oltre i livelli di tolleranza impostati. I progettisti devono tenere traccia di tutti i dati per i componenti e dei materiali di base utilizzati. Devono anche conoscere la temperatura alla quale dovrà operare il PCB, per identificare il materiale più adatto in termini di Tg, temperatura di transizione vetrosa e Td, temperatura di decomposizione. Il PCB non deve mai avvicinarsi alle temperature alle quali i materiali si decompongono perché questo causa un guasto prematuro del PCB. “
JB: “A livello di scheda, esistono alcuni modi per spostare il calore in eccesso. Il più semplice è fissare il PCB su una piastra di alluminio. Lo vediamo sui PCB con tecnologia inferiore, il tipo più semplice di progetto. In combinazione con thermal prepreg, si ottiene una gestione termica di base. Il passo successivo sarebbe una base metallica isolata, il cosiddetto PCB con IMS (Insulated Metal Substrate – substrato metallico isolato), che vediamo molto spesso nell’illuminazione industriale. In genere, questo viene utilizzato nelle schede con un solo strato. In questo caso, una piastra di base in metallo, di solito alluminio, è coperta da un sottile strato di prepreg e poi da una lamina di rame. L’IMS può essere utilizzato anche in schede da due fino a quattro strati, anche se la progettazione risulta più complessa. Alcuni dei fari per auto di livello superiore sono realizzati con un IMS a strato singolo, o metal flex piegato in forma.”
“Il PCB non deve mai avvicinarsi alle temperature alle quali i materiali potrebbero decomporsi e causare un guasto prematuro del circuito stampato.”
Mario Cianfriglia
Field Application Engineer, NCAB Group Italy
MC: “Lo Step successivo per la gestione termica, oltre all’IMS, è un Via Farm. Qui entriamo in un ambito molto più complesso, sicuramente per i processi coinvolti nella produzione di questi oggetti. In sostanza entrano in gioco tutte le possibili tecnologie per rendere i fori più conduttivi, sotto il profilo termico. Un deposito di rame molto spesso sulla parete dei fori, riempimento poi i fori con resine conduttive e non conduttive, infine cappando la superficie del foro con rame. Tutto questo per produrre un tappeto o griglia di fori in grado di trasportare grandi quantità di energia termica. Qui il progettista deve avere ben presenti tutti i parametri operativi dell’oggetto ed è necessario capire dove collocare determinati componenti “.
JB:“Il rame è secondo solo al diamante come materiale conduttivo sotto il profilo termico. Quindi si può dire in tutta sicurezza che è ottimale per spostare il calore. Con i via farm, creiamo, per così dire, più percorsi attraverso i quali il calore viene trasportato via.”
MC: “Infine, un metodo noto come Copper coin (moneta di rame) è la soluzione più avanzata per la gestione termica. Si tratta di elementi in rame, di dimensioni e geometrie ben determinate – cilindriche o cubiche – e di altezza variabile. Sono spesso a forma di T per trasferire quanto più calore possibile sul lato opposto della scheda. Questa tecnologia viene utilizzata per raffreddare componenti attivi come ad esempio i QFD (Quad-refiled Flat Package). Per raffreddare il più possibile il componente, un copper coin viene posto in prossimità della parte inferiore del componente, deve poggiare sulla superficie del rame. Ci sono diverse tecniche per inserire questi copper coin sulle PCB. Possono essere incollate sulla superficie o nelle cavità, integrate all’interno del circuito stampato durante il processo di stampa multistrato, o montate a pressione, tipo press-fitt.”
JB: “Il Copper Coin dovrebbe essere preso in considerazione quando altre alternative non hanno funzionato. Talvolta ci vengono poste delle domande su questa tecnologia da parte di clienti che hanno avuto problemi con la gestione termica durante il test sulle schede. Ma spesso non si rendono conto di quanto sia complicato e costoso introdurre questo tipo di soluzione in una costruzione già esistente. Potrebbe sembrare facile inserire un pezzo di rame solido che facilita la dissipazione del calore, ma le modifiche strutturali richieste possono essere davvero impegnative. Spesso esistono soluzioni più semplici ai problemi. Non è necessario ricorrere a un bazooka per sbarazzarsi di una zanzara, dal momento che esistono strumenti più semplici per farlo.”
“Il rame è secondo solo al diamante come materiale conduttivo sotto il profilo termico.”
Jeffrey Beauchamp,
Technical/Engineering Manager, NCAB Group USA
Quali sono i vantaggi e gli svantaggi dei diversi metodi di gestione termica?
MC: “In definitiva, è l’applicazione che determina quale soluzione scegliere per gestire i problemi termici. Ciò che governa principalmente la scelta è probabilmente nella maggior parte dei casi il costo, che a sua volta è correlato al livello di sofisticazione della tecnologia in questione “.
JB: “Il vantaggio della moneta di rame consiste nel raggiungimento di un’eccellente conduttività termica. Il componente è incollato direttamente al rame e al dissipatore di calore. Tuttavia, come ho già detto, ci sono notevoli svantaggi in termini di costi e complessità. Questo metodo pone elevate sfide in fase di progettazione e vi è solo un numero limitato di fabbriche che sono in grado di produrre tali schede.
Al contrario, il vantaggio del via farm è che quasi ogni fabbrica può gestirlo; si tratta solo di praticare dei vias termici. Il costo di produzione è quindi relativamente basso. Né comporta interventi consistenti nella struttura. Si aggiungono più vias termici, operazione che di per sé limita lo spazio sulla superficie disponibile, ma rimane comunque una soluzione più semplice da realizzare rispetto alla moneta di rame. Uno svantaggio del via farm è che si deve utilizzare più rame in fase di placcatura, e questo aspetto, considerati gli attuali aumenti dei prezzi, ha un impatto significativo sui costi. In alternativa, è possibile utilizzare resine epossidiche termoconduttive, ma anche questa soluzione è relativamente costosa e non altrettanto conduttiva allo stesso livello.
Per entrambe le soluzioni, ovvero la moneta di rame e il via farm, vi è anche un potenziale svantaggio in quanto offrono un trasferimento termico così buono che l’assemblaggio può essere effettivamente difficile per chi stia assemblando la scheda. Quando parliamo con un progettista di PCB, gli consigliamo sempre di contattare il produttore di Pcb e chi fa il montaggio dei componenti.
I vantaggi dell’IMS è che è semplice, efficiente e moderatamente producibile. Gli svantaggi sono che limita drasticamente il numero di livelli che si possono ottenere. L’IMS a uno strato è molto comune. Un IMS a due strati lo è meno, gli stili di progettazione sono piuttosto limitati. Un IMS a tre strati è molto raro. NCAB può supportare IMS con un numero di strati che può arrivare a quattro, ma non è facile. Rimane sempre meno costoso di una scheda con moneta in rame, ma richiede requisiti molto specifici per lo stack-up, ecc.”
“Siamo in grado di far fronte all’intera gamma della gestione termica, dall’IMS al via farm fino alla moneta di rame, praticamente ovunque ci troviamo geograficamente.”
Jeffrey Beauchamp,
Technical/Engineering Manager, NCAB Group USA
Cosa può offrire NCAB in questo ambito?
MC: “Siamo in grado di supportare i nostri clienti su tutte le tecnologie, dove ci sono diversi parametri da tenere in considerazione. Grazie alla nostra vasta esperienza nella progettazione e nella produzione di PCB, possiamo consigliare le scelte più adatte per una specifica applicazione. Abbiamo anche fabbriche in grado di produrre questi prodotti. Prima riusciamo ad essere coinvolti in un progetto, migliori sono le condizioni per aiutare i clienti a trovare la soluzione migliore possibile.”
JB: “Siamo in grado di far fronte all’intera gamma della gestione termica, dall’IMS al via farm fino alla moneta di rame, praticamente ovunque ci troviamo geograficamente. Possiamo offrire il nostro aiuto in ogni fase, dai prototipi alla produzione di grandi volumi. La gestione termica è davvero un’area in cui i clienti possono trarre grandi vantaggi dalla nostra esperienza, soprattutto considerando la crescente domanda di soluzioni speciali. Dubito che chiunque altro abbia una conoscenza così approfondita delle soluzioni possibili, dal momento che affrontiamo problemi di questo tipo ogni giorno.”
Tre metodi principali per la gestione del calore nelle schede a circuito stampato
- IMS (substrato metallico isolato) – dove la scheda è costituita da una piastra metallica – normalmente alluminio – in cui una lamina di rame è legata ad un prepreg in resina o una speciale resina termoconduttiva.
- Via farm – dove usi più fori e aumenti la quantità di rame nella parete del foro e usi resina epossidica conduttiva per dissipare il calore..
- Copper coin (Moneta di rame) – dove elementi supplementari di rame sono posizionati sotto componenti specifici e dissipano direttamente il calore.
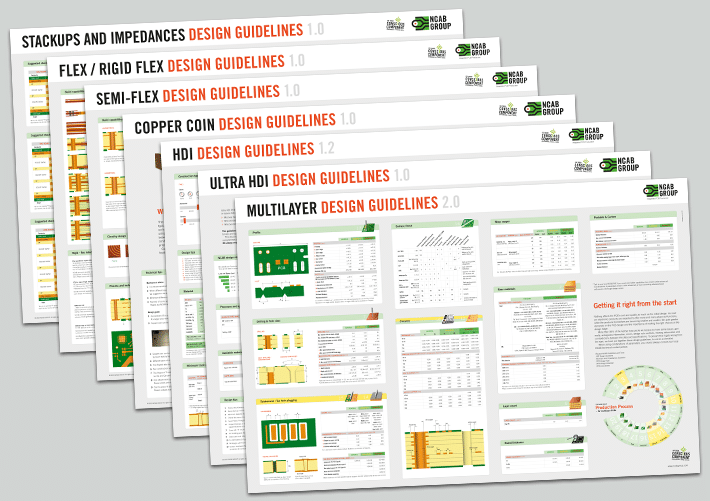
PCB design guidelines
Get it right from the start with our PCB design guidelines. To prevent getting it wrong from the start, we have put together our design guidelines, to use as a checklist.