Al fine di ottenere i migliori risultati sul prodotto elettronico è necessario preservare la qualità dei circuiti stampati in attesa dei processi di assemblaggio. In questo articolo vedremo come un corretto imballo permetta di preservare l’usabilità e le performance dei PCB. I circuiti stampati possono infatti essere sensibili a diversi fattori.
La finitura superficiale ha lo scopo di agevolare la bagnabilità e proteggere il rame sottostante dall’ossidazione. Anche la finitura superficiale ha però bisogno di protezione da danneggiamenti, ossidazioni, contaminazioni, temperatura elevata e umidità. Inoltre, anche i materiali di base che compongono i PCB devono essere protetti, soprattutto dall’umidità. Durante le fasi di saldatura, i circuiti vengono sottoposti ad elevate temperature che possono causare difettosità evidenti o latenti, tra le quali la temuta delaminazione.
Un corretto imballo, unitamente a condizioni ambientali controllate, è in grado di preservare i circuiti stampati da deterioramento per tutta la durata della shelf life, garantendo il miglior risultato possibile in fase di saldatura.
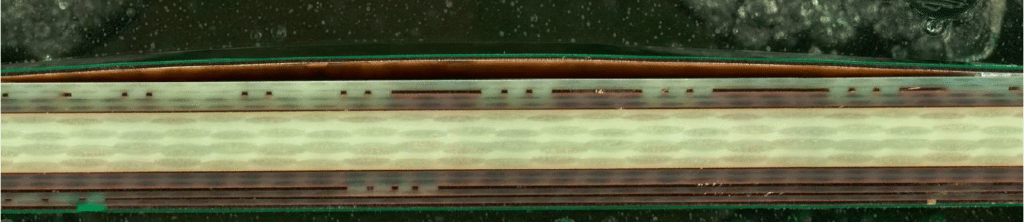
Il ruolo dell’umidità
L’umidità è sicuramente un nemico dei circuiti stampati. È necessario approfondire questo argomento per meglio comprendere il ruolo dell’imballo nel settore dei PCB. I materiali di base hanno tendenza igroscopica, ovvero possono assorbire il vapore acqueo presente nell’ambiente esterno. Risulta quindi fondamentale impiegare laminati a basso assorbimento di umidità. I circuiti flessibili e rigido-flessibili sono particolarmente soggetti a questo fenomeno, perché l’assorbimento di umidità dei materiali flessibili satura a percentuali su massa fino a 20 volte maggiori rispetto al FR4. Se vuoi approfondire il tema dei laminati, puoi confrontarti con i nostri tecnici.
Il problema primario associato all’assorbimento di umidità nei materiali di base dei PCB è relativo all’espansione del vapore per effetto delle temperature in fase di assemblaggio. Il fenomeno può portare a delaminazioni, separazioni dei fori metallizzati, separazione dei conduttori interni dai fori, sbollature del solder resist. L’umidità può inoltre agevolare il deterioramento delle finiture superficiali.
Per evitare di impiegare circuiti umidi, è essenziale contenere il livello di umidità residua al termine del processo di produzione dei PCB. Il personale NCAB monitora costantemente i processi produttivi per garantire livelli di umidità accettabili. Lo standard IPC-1602, che tratta la manipolazione e la conservazione dei circuiti stampati, consiglia di mantenere il contenuto di umidità prima dell’imballo sotto al valore di 0.1% rispetto alla loro massa, quando il processo cui sono destinati è di tipologia lead free.
L’imballo deve essere sottovuoto, per evitare di inglobare vapore acqueo all’origine e deve inoltre costituire una barriera adeguata alla permeazione dell’umidità dall’esterno, che può avvenire durante la fase di trasporto e per tutta la durata di conservazione a magazzino. Anche in questo caso NCAB è attiva nella validazione degli imballi ammessi. Nonostante ciò, è essenziale che la merce venga stoccata in magazzini idonei: umidità relativa sotto al 60% e temperatura inferiore a 25°C.
Imballi e WVTR
Il parametro WVTR (Water Vapor Transmission Rate) è il tasso di permeabilità al vapore acqueo, viene misurato in grammi che attraversano l’unità di superficie in 24 ore alla temperatura di 40°C. Per limitare questo passaggio di umidità, NCAB definisce materiali, spessori e modalità di imballaggio. In alcuni casi, come per circuiti molto sensibili o quando sono richiesti lunghi tempi di conservazione, può essere utile concordare l’impiego dei cosiddetti MBB, Moisture Barrier Bag. Si tratta di involucri che contengono uno strato alluminio, al fine di ridurre ulteriormente la trasmissione di vapore acqueo. Gli MBB devono avere un WVTR inferiore a 0.031 g/m2 in 24 ore, in accordo a IPC-1602 e J-STD-033. NCAB vincola l’impiego di MMB che rispettino questo valore e i relativi metodi di prova associati.
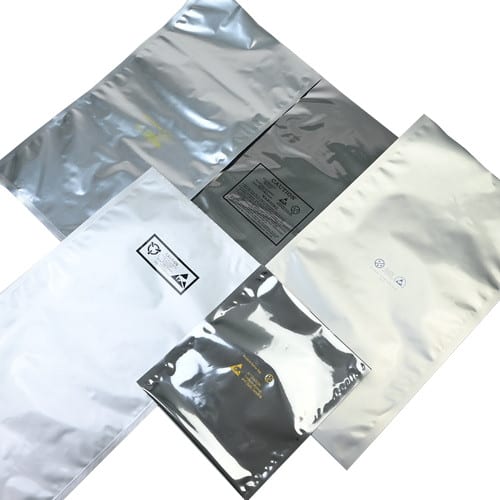
Indicatori di umidità e materiali essiccanti
All’interno degli imballi è utile prevedere anche indicatori di umidità e materiali di essiccazione. Gli indicatori di umidità – HIC Humidity Indicator Cards – sono cartoline che presentano alcuni spot pre-impregnati di composti chimici in grado di virare di colore al superamento di diverse soglie di umidità relativa. Il cambio del loro colore non è equivalente ad un difetto: forniscono l’importante informazione del massimo livello di umidità raggiunto all’interno del pacchetto contenente i PCB, e questo è di aiuto nel decidere se effettuare o meno il baking. Più avanti discuteremo del baking. I materiali essiccanti assorbono il vapore acqueo che permea all’interno del pacchetto durante trasporto e conservazione, allo scopo di contrastare l’aumento di umidità nell’imballo.
Se gli Indicatori e sali sono richiesti, devono essere certificati Sulphur Free, per evitare il rilascio di composti corrosivi come acido solfidrico o anidride solforosa. Anche in questo contesto, NCAB vincola le specifiche di prodotto e le modalità di inserimento nell’imballo.
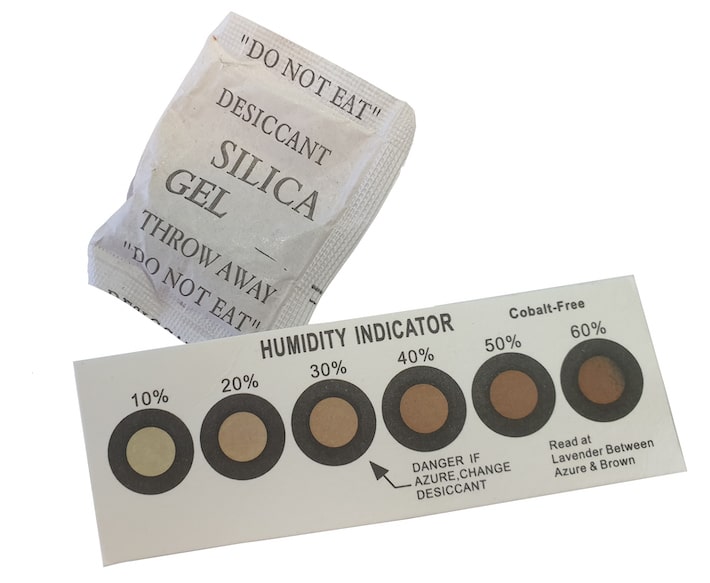
Baking PCB
Nel caso in cui gli indicatori segnalino un livello di umidità considerato critico, è possibile valutare comunque l’impiego dei circuiti stampati in seguito al processo di baking. Per i circuiti flessibili e rigido-flessibili, considerando il loro maggior comportamento igroscopico, il baking dovrebbe sempre essere effettuato.
La procedura consiste nell’esporre i PCB a temperature nell’intorno di 105-125 °C, da 2 a 6 ore, per rimuovere umidità dal materiale di base. Se vuoi approfondire le modalità e i parametri del baking, puoi scaricare le raccomandazioni di NCAB qui.
A complex procedure
È però importante considerare che il baking può ridurre la bagnabilità della finitura superficiale per effetto delle ossidazioni e per la crescita dello strato intermetallico (IMC), poiché entrambi i fenomeni sono agevolati dall’aumento di temperatura. Questo significa che il baking non è una passeggiata. Meglio evitare di dover ricorrere al baking, attraverso buone pratiche di stoccaggio ed eventualmente considerare l’impiego di MBB. Se la procedura di baking è comunque necessaria, è raccomandato utilizzare parametri conservativi, così come impiegare un forno sottovuoto o ad azoto, che risulti inoltre pulito da agenti contaminanti.
La tabella seguente mostra come le diverse finiture superficiali reagiscono al baking e fornisce importanti informazioni per evitare problemi di saldatura.
HASL | Se lo spessore è inferiore a 0.77 µm, la finitura può diventare completo IMC. |
OSP | Forno ad azoto, ossigeno < 100 ppm, 105°C per 1 ora. Se è più critic, necessario deposito di nuovo OSP. |
ISn | La crescita del IMC può compromettere la saldabilità, soprattutto al termine della shelf life. |
IAg | Zolfo o Cloro causano tarnishing (è visibile a partire da 5 nm di spessore, compromette la saldabilità a partire da 50 nm). |
ENIG/ENEPIG | Ossigeno può superare lo strato di oro e ossidare lo strato di nickel. Forno ad azoto, ossigeno < 100 ppm. |
In questo articolo abbiamo spiegato come l’imballo dei circuiti stampati, oltre a dover proteggere dai rischi di danneggiamento fisico e contaminazione, deve costituire una barriera efficace contro l’umidità. È anche importante sapere che, nonostante abbiamo un approccio generale, ogni ufficio NCAB ha requisiti specifici. Quindi, per avere maggiori informazioni su imballo e stoccaggio, puoi metterti in contatto con il tuo ufficio locale. Saremo lieti di supportarti.