To achieve the best results in electronic products, it is crucial to preserve the quality of printed circuit boards (PCBs) while waiting for the assembly processes.This blog post will explore how proper packaging allows you to preserve the usability and performance of PCBs, which can be sensitive to several factors.
The surface finish of a PCB is intended to facilitate wettability and protect the underlying copper from oxidation. However, the surface finish itself also needs protection from damage, oxidation, contamination, high temperatures, and humidity. In addition, the base materials of PCBs must be protected, especially from moisture. During the soldering phases, the circuits are subjected to high temperatures that can lead to evident or latent defects, including the dreaded delamination, which can significantly affect performance. Proper packaging, together with controlled environmental conditions, preserves the printed circuit boards from deterioration throughout their shelf life, ensuring the best possible result in the soldering phase.
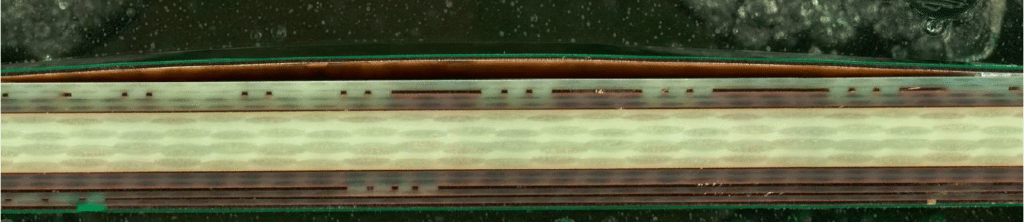
The Role of Humidity
Moisture is undoubtedly an enemy of printed circuit boards. To better understand the importance of packaging in the PCB industry, we need to delve deeper into the topic. Base materials exhibit hygroscopic behavior, meaning they can absorb water vapor from the environment. Therefore, it is essential to use laminates with low moisture absorption. Flex and Rigid-Flex PCBs are particularly susceptible to this phenomenon, as the humidity absorption of flex materials can saturate at a percentage by weight up to 20 times greater than standard FR4. If you want to learn more about materials, you can talk to our technicians.
The primary issue associated with moisture absorption in PCB base materials is the expansion of vapor due to the high temperatures of assembly processes. This can lead to delamination, separation of the metallized holes, inner layer separation, and solder resist defects. Additionally, moisture accelerates the deterioration of surface finishes.
To avoid using wet circuits, it is essential to keep the residual moisture level low at the end of the PCB manufacturing process. NCAB staff continuously monitor production processes to ensure acceptable humidity levels. The IPC-1602 standard, which deals with the handling and storage of printed circuit boards, recommends keeping the moisture content before packaging below 0.1% of their mass, when the process they are intended for is lead-free. Vacuum packaging prevents PCBs from incorporating water vapor, creating also an adequate barrier against the permeation of moisture during transportation and storage. Also in this case, NCAB is active in the validation of the packaging by the supplier. Nonetheless, all this must be supported by customers’ warehouse conditions: maintaining relative humidity below 60% and temperature below 25°C.
Packaging and WVTR
The Water Vapor Transmission Rate (WVTR, or water vapor permeability rate) is measured in grams of water vapor passing through a unit surface within 24 hours at a temperature of 40°C. To minimize this moisture transmission, NCAB defines materials, thicknesses, and packaging methods. In some cases, such as for highly sensitive circuits or when long storage times are required, it may be advisable to use Moisture Barrier Bags (MBBs). These are bags that contain an aluminum layer to further reduce the transmission of water vapor. MBB must have a WVTR of less than 0.031 g/m2 in 24 hours, according to IPC-1602 and J-STD-033. NCAB ensures that whenever the use of MBBs is agreed upon with customers, the products meet this standard and its corresponding test methods.
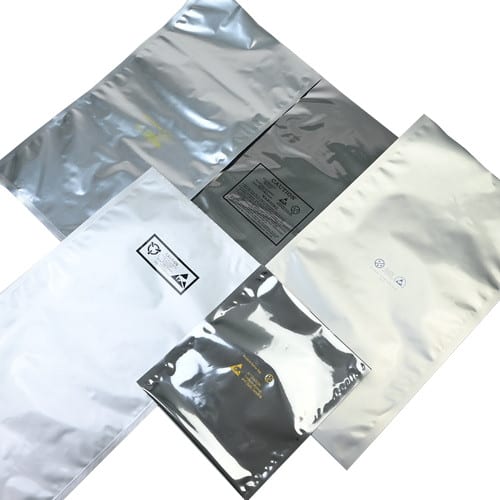
Moisture Indicators and Desiccant Materials
Humidity indicators and desiccant materials can be added to the packaging, but they are included only upon customer request. Humidity Indicator Cards (HICs) are small cards with spots pre-impregnated with chemical compounds that change color when specific relative humidity thresholds are exceeded. Their change in color is not equivalent to a defect; rather, it provides information about the maximum humidity level reached inside the package containing the PCBs. This information can help determine whether baking is necessary—a topic we will discuss later.
The desiccant materials absorb the water vapor that permeates the packaging during transportation and storage of the printed circuits, helping to counteract the increase in humidity in the packaging. If indicators and desiccant materials are requested, they must be certified as sulphur-free to prevent the release of corrosive compounds, such as hydrogen sulphide or sulphur dioxide. In such cases, NCAB specifies the product requirements and defines the methods for incorporating these materials into the packaging.
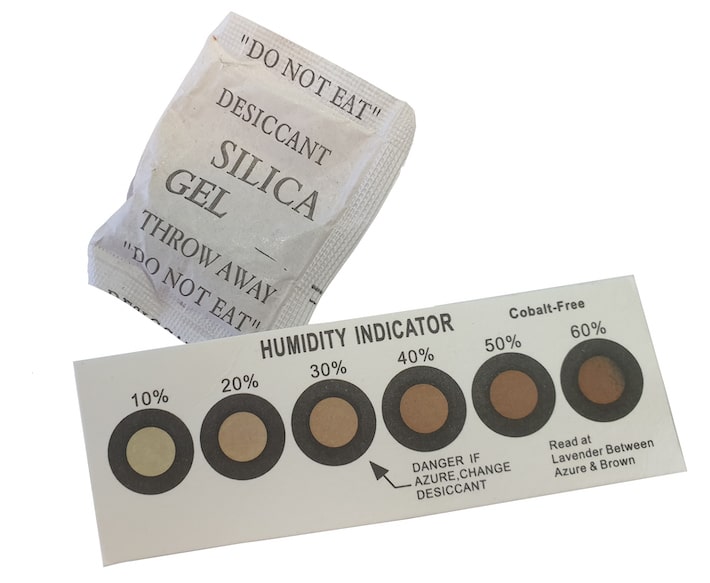
Baking PCB
If the indicators report a critical humidity level, it is still possible to evaluate the use of printed circuit boards through a process called baking. For flex and rigid-flex PCBs, which exhibit higher hygroscopic behavior, baking should always be performed.
The baking procedure involves exposing PCBs to temperatures between 105–125°C for 2 to 6 hours to remove moisture from the base material. Once baked, PCBs should be assembled as soon as possible, ideally within 24 hours. For more details on the methods and parameters of baking, you can download NCAB’s recommendations for rigid PCBs here.
The choice of baking parameters also depends on the design. Copper planes, for example, can hinder moisture from escaping, potentially requiring additional time in the oven.
A complex procedure
However, it is important to note that baking can reduce the wettability of the surface finish due to oxidation and the accelerated growth of intermetallic compounds (IMC), both of which are exacerbated by heat. This makes baking a complex procedure. It is generally best to avoid baking by implementing proper storage practices and using Moisture Barrier Bag (MBB) packaging.
If baking is still needed, the adoption of conservative parameters is recommended, as well as the use of a vacuum or nitrogen oven, which shall be cleaned of contaminants. The following table outlines how different surface finishes react to baking and provides essential information for avoiding solderability issues.
HASL | Thickness below 0.77 µm can result as complete IMC. |
OSP | Nitrogen oven, oxygen < 100 ppm, 105°C for 1h. If more critical condition, new OSP deposition required. |
ISn | IMC grow can compromise solderability, above all at shelf life end. |
IAg | Sulphur or Chlorine cause tarnishing (visible at 5 nm thickness, compromises solderability starting from 50 nm). |
ENIG/ENEPIG | Oxygen can pass gold layer and oxidate nickel layer. Nitrogen oven, oxygen < 100 ppm. |
In this blog post, we have explained how PCB packaging not only protects against physical damage and contamination but also acts as a critical barrier against humidity. It is important to note that, while we follow a general approach, each NCAB region may have specific requirements. Therefore, for more information on the topics of packaging or storage of goods, you can get in touch with your local NCAB contact. We will be happy to support you.