Our factories conduct rigorous quality and reliability tests on each new batch prior to dispatch, all of which are documented in the NCAB Group Certificate of Conformity. However, we continue to take ownership of the qualification and release of products be this during volume supply or during our procurement and factory qualification processes.
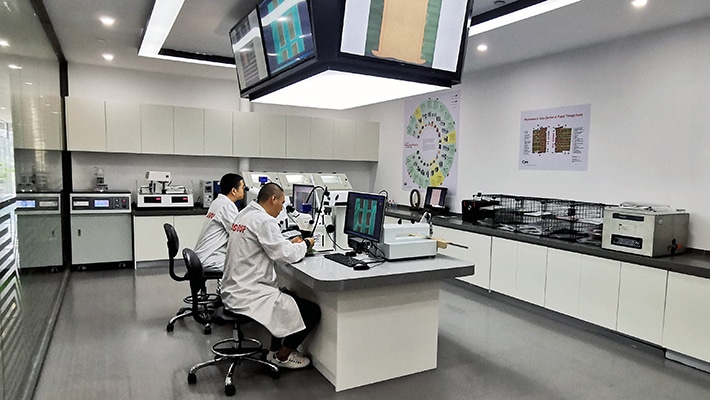
NCAB Group´s labs evaluates and supports a comprehensive first article inspection process and assures that the products we are receiving are as ordered. We can also carry out root cause analysis of both assembled or bare boards if required, without the need or the additional time involved in sending boards back to our factories for analysis. This allows us to quickly grasp any issue and feedback to the factories quickly and accurately.
Seven printed circuit board labs in three continents at your service
Within NCAB Group we have seven labs in three continents that are supporting all our companies. Below you can take a closer look inside them.
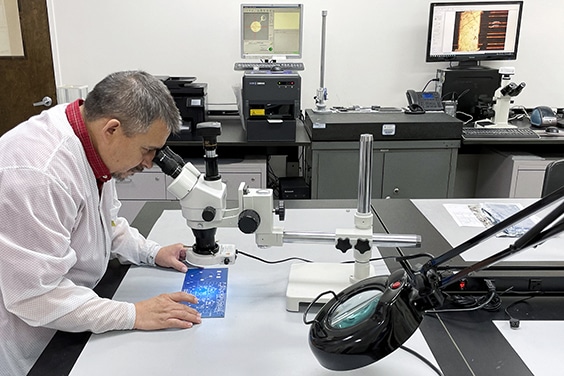
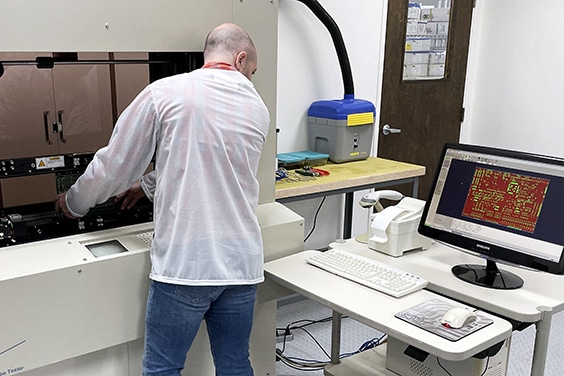
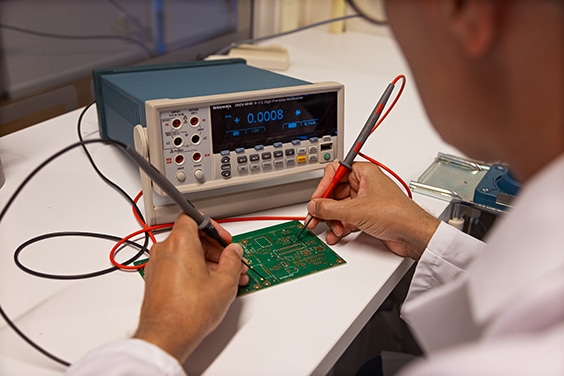
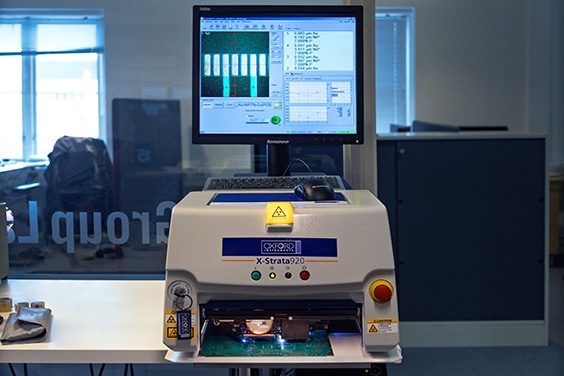
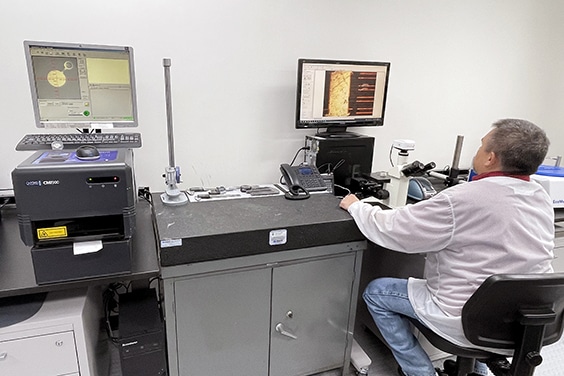
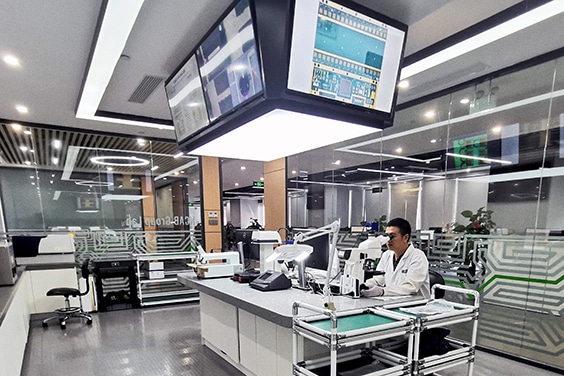
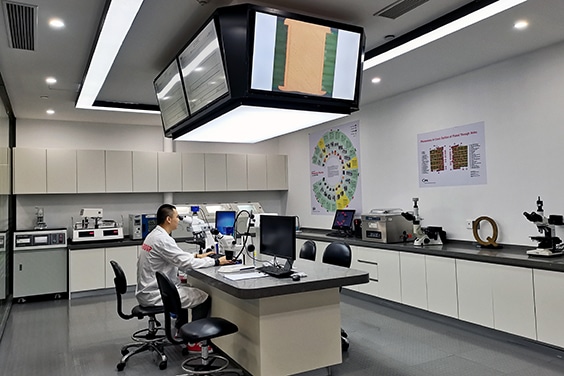
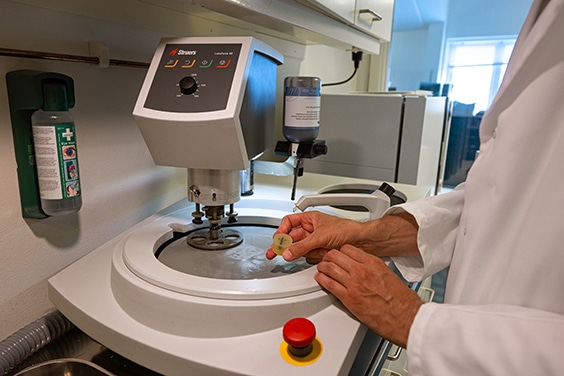
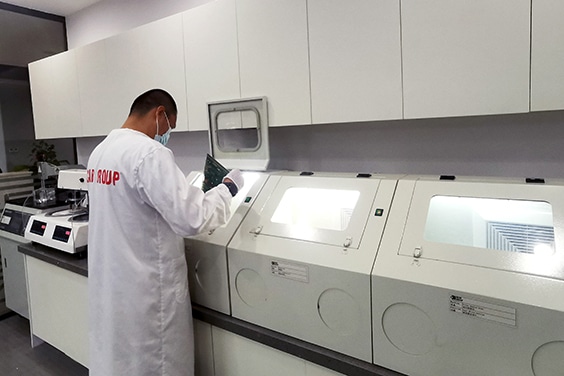
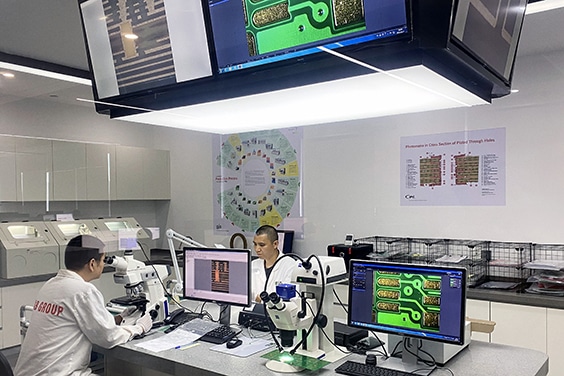
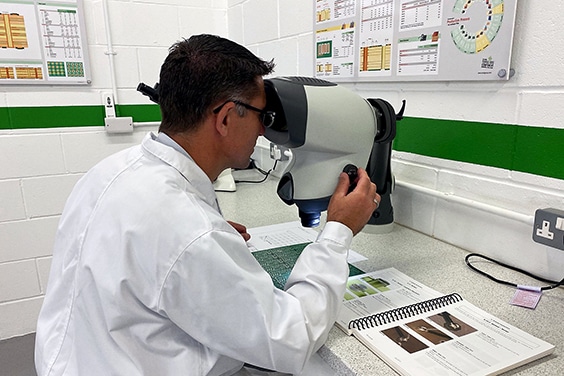
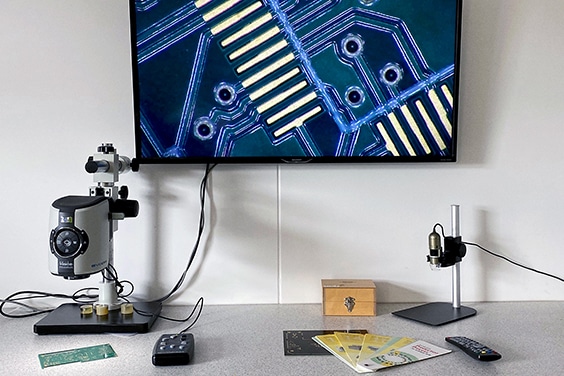
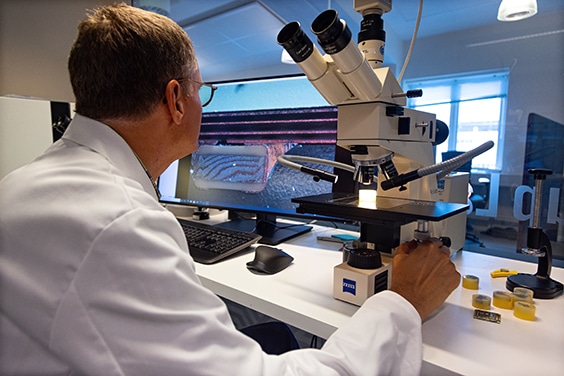
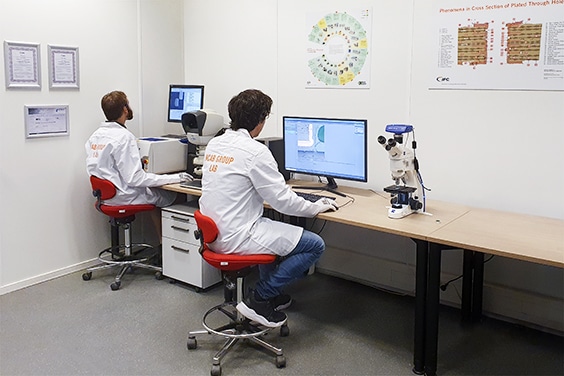
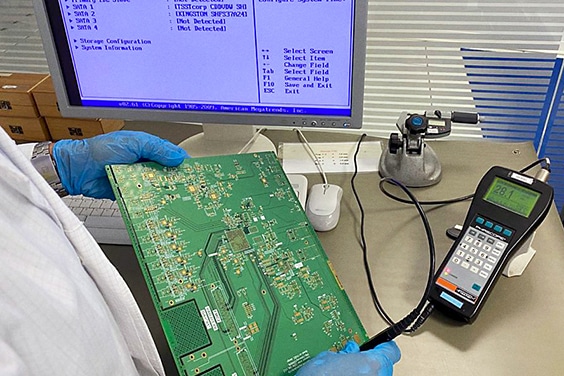
Watch our labs in 360° for best experience
Andy Dai (standing) and Star Ye, Lab Technicians at NCAB Factory Management working in the NCAB Group lab at the Chinese office.
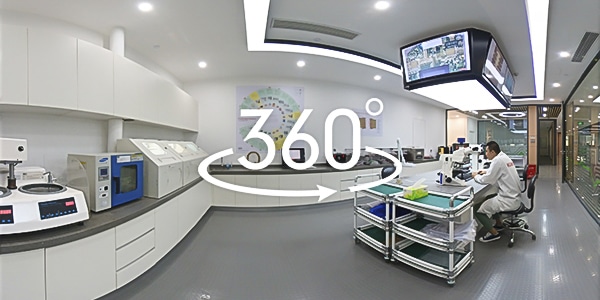
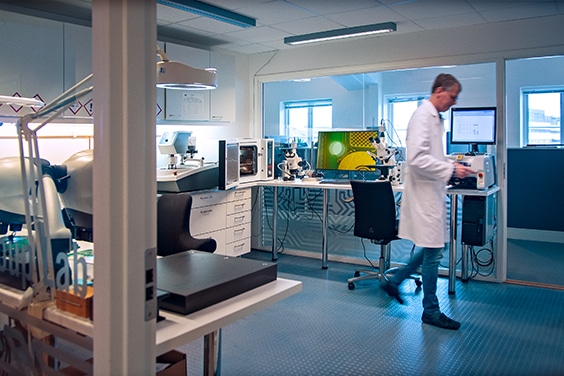
Regional labs
- NCAB Group Europe / Italy
- NCAB Group Europe / UK
- NCAB Group Europe / Netherlands
- NCAB Group Europe / Germany
- NCAB Group Nordic / Sweden
- NCAB Group USA / Chicago
Global lab
- NCAB Group Global / China
NCAB Group regularly undertakes the following activities:
- Full micro sectional analysis
- IPC class 3 process and acceptance verification
- Copper thickness checks on all layers and on hole wall
- Analysis and verification of build, including dielectric thicknesses
- Evaluation of BGA and SMD pad geometries along with track and gap measurements
- Solderability testing
- Thermal stress and delamination tests
- Solder-mask analysis including adhesion and thickness evaluation
- X-Ray fluorescence checks to measure the thickness of surface finishes such as ENIG, immersion Tin, etc.
- Generation of CpK data for critical features such as copper through hole, track and gap
- Fault finding and root causes analysis
The level of detail and analysis available from NCAB ́s internal qualification and release checks
can be seen in the template below.