Leverage of scale
– providing efficiency
Producing reliable PCBs and securing a robust supply chain require global resources and expertise. With us, you will gain our full global strength from day one – secured capacity and capability, expertise, and a more sustainable way of doing business.
A resilient supply chain with carefully selected partner factories
We don´t own any factories, instead we have a network of partner factories in China, Taiwan, South Korea and Southeast Asia as well as in North America and Europe. This ensures flexibility, reduces geopolitical risk, and strengthens supply chain resilience.
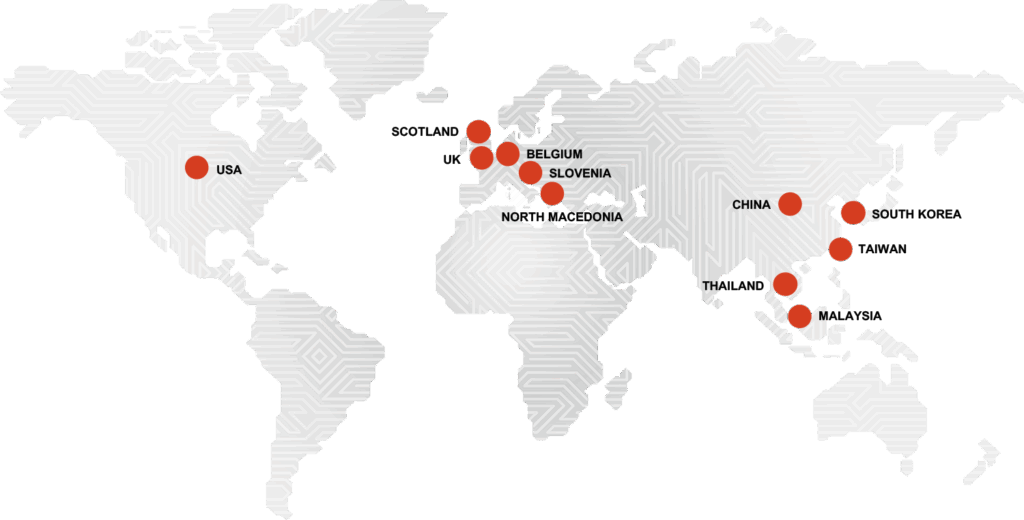
The factories we work with have undergone our comprehensive sourcing process and are approved based on the technologies and volumes they can reliably manufacture. We always have more than one factory for each technology and volume. This multi-sourcing capability ensures resilient production and flexible capacity to meet both general and specialized industry needs.
Considerable influence and priority
Our factory strategy is to enable partnership based on influence and priority. We achieve this by being a top 5 customer or contributing at least 15% of the factory’s revenue. This secures prioritization and enables us to implement both our own demands, such as our PCB specification, shorter lead times, and sustainability requirements – and those of our customers.
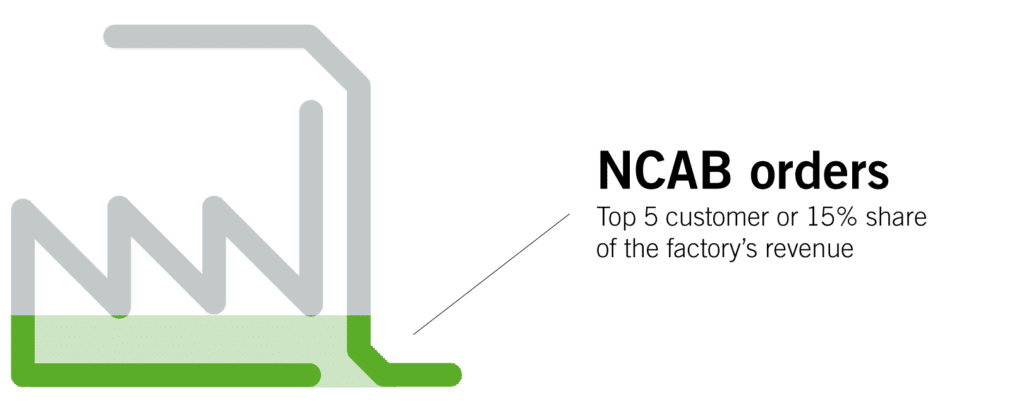
We have reserved capacity to ensure our customers’ orders are fulfilled, and if disruptions occur, the factory prioritizes and resolves our customers’ needs promptly. All transportation is managed by our main logistics suppliers, with whom we, as a group, have the leverage to ensure prioritization when needed. This secures on-time deliveries and enables a flexible logistics solution, even in turbulent times.
Responsibility for design to volume on a wide product range
Thanks to our size, we offer both a wide product range – our PCB portfolio includes everything from 2-layer boards to highly advanced HDI and flex boards – and a broad range of services.
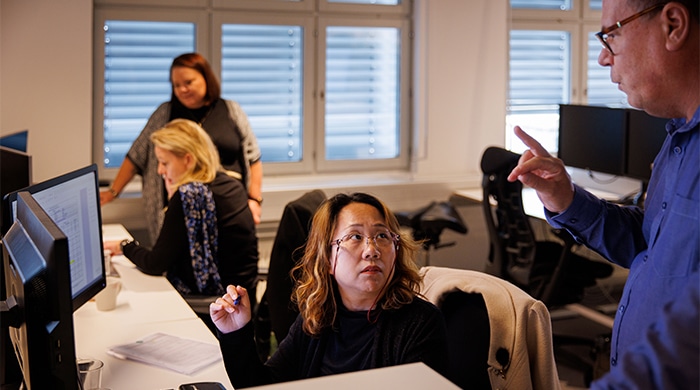
We take full responsibility for supporting our customers throughout every stage of PCB development, from design support (DFM) and early prototypes to series production, helping to avoid time-consuming mistakes. We also ensure compliance with the various regulations across the industries we serve.
Driving sustainable change throughout our value chain
Sustainability is part of our mission and permeates everything we do. It is an important factor in how we select partner factories, PCB materials and design solutions, and it sets the standard for how we act and make everyday decisions.
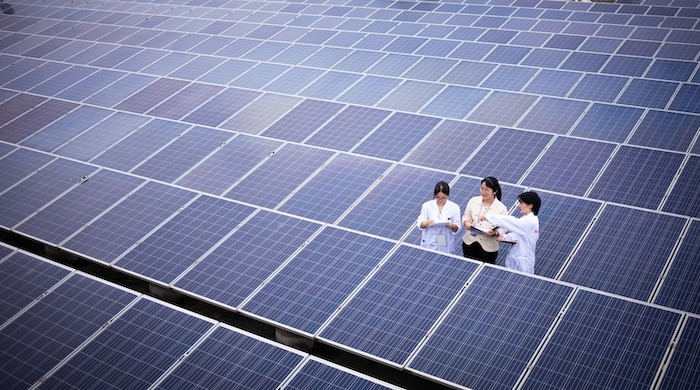
Together with our suppliers and customers, we want to create a more sustainable industry with growth and profitability for all. We believe that strong relationships and transparency are key to achieving this, and we work actively to reduce our climate impact and act on other environmental, social, and governance matters.
A PCB knowledge center for our customers
We continuously educate ourselves to stay up to date with developments in the industry, and we aim to share our PCB expertise with our customers in several ways.
Our Technical Council oversees all technical aspects of PCB design, manufacturing, and innovation. They are actively involved in IPC, providing our customers with proactive technical knowledge and R&D on emerging technologies, new materials, sustainability, and market trends. We have a PCB Learning Hub with technology videos, design tools, webinars, seminars, and white papers that deliver training and education for our customers – providing deeper insight into technical challenges and solutions for producing reliable PCBs.
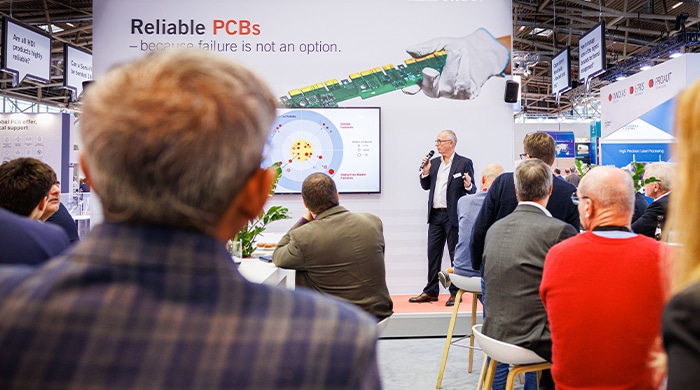
Our industry sector specialists have a deep knowledge of application demands, delivering tailored solutions that meet industry-specific standards, compliance requirements and regulations. In our seven NCAB Group’s labs we can evaluate and support a comprehensive first article inspection process to assure that the products we are receiving are as ordered. We can carry out root cause analysis of both assembled or bare boards if required, this allows us to quickly grasp any issue and feedback to the factories.
Digitalization supporting integration, efficiency and data protection
We implement stringent security protocols to safeguard intellectual property (IP) and maintain confidentiality throughout the supply chain. For more sensitive projects such as those in the defense sector, an additional layer of information security is applied.
Our customers can reduce manual effort, minimize errors, and enhance operational efficiency with our EDI solutions. This enables seamless digital data exchange ensuring real-time collaboration and accuracy in business transactions.
Customer presence
– providing a lean process
Reliable PCBs are built through partnership, and being close to our customers is key – geographically, legally and through expertise. Our local presence allows us to act fast, meet specific market demands, and ensure compliance.
Local commercial responsibility with global reach
NCAB is a global, full-service PCB supplier with a decentralized set up. We serve customers in 45 countries and have local companies in 19 of them. The knowledge and experience gathered worldwide are made available locally.
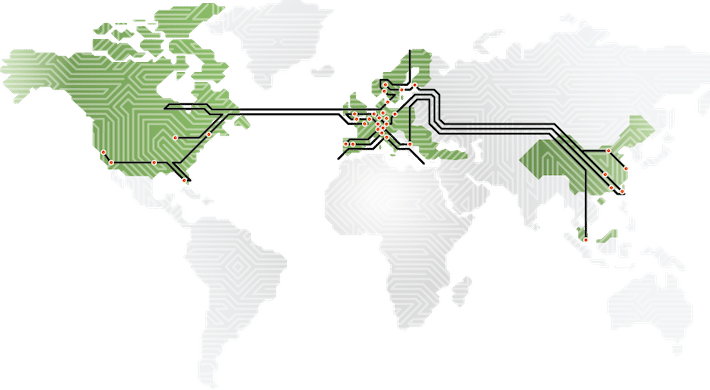
Our local companies take full commercial responsibility, ensuring that terms and conditions comply with local legislation – including claims handling, VAT, customs, and adherence to industry standards such as RoHS, REACH and UL. This means you get less administration and a mitigated commercial risk.
Efficient technical and design support
We know that nothing affects the PCB’s total cost and reliability as much as the initial design of the PCB. This is why all our local offices include dedicated specialists who work with you to understand your requirements.
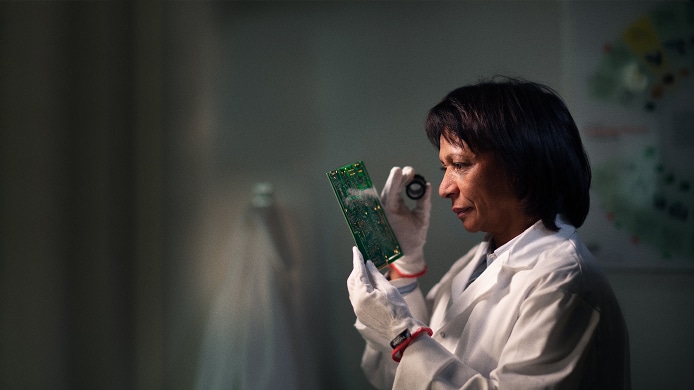
We examine the manufacturability of customer supplied data and work with the customer as part of our EQ management approach, to secure that the PCBs can be produced with the best yield, building in quality and sustainability from the very start.
This ensures an easy transition from prototype to series production.
We do Design Rule Checks (DRC), Design for Manufacturing (DFM) reviews, and verify build-ups and impedance calculations. We also collaborate in three-party setups with EMS companies and the product owner to ensure a reliable result. Our local technicians are backed by our global team, including Factory Management, a technical council, and industry experts, who review a vast number of new designs each year. This support ensures the entire team stays knowledgeable and up to date.
Meeting national compliance demands across industry sectors
For specific industry sectors, everyone in the entire PCB supply chain must follow industry-specific rules, laws, and regulations to be permitted to handle offers, orders and deliveries.
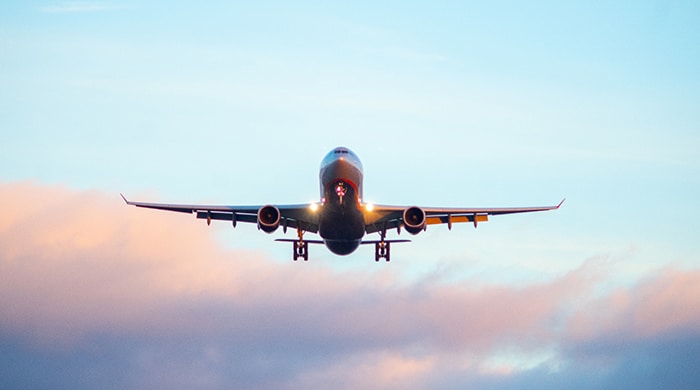
We have the size, organization, processes, systems, and expertise to manage our factories and all stakeholders in the supply chain, ensuring compliance with the specific standards of each industry. This includes requirements from both national and international laws and regulations, as well as adaptation to geopolitical challenges. Some of the stricter standards we meet are ITAR, EAR, FAR/DFAR(s), AS9100, EN9100, NADCAP. Our solution to handle sensitive data for defense projects is built to meet the standards for NIST800-171 (cyber security).
Dynamic logistic solutions
We offer warehousing solutions for suitable projects, either through buffer stock at our premises (own or third-party warehouses) or consignment at our customers’ premises. These solutions help mitigate freight risks, support vendor-managed inventory, add flexibility, and reduce lead times and emissions.
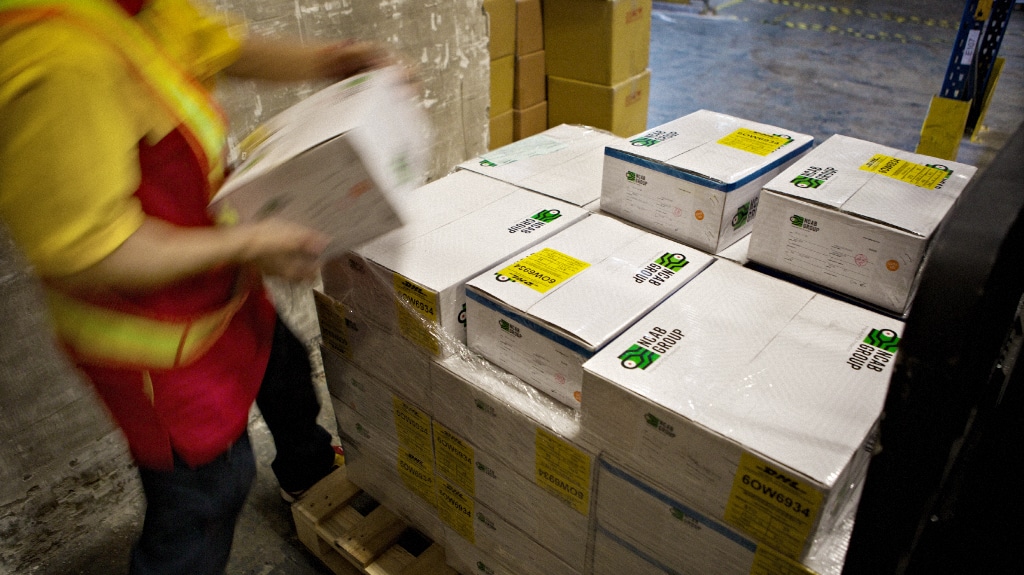
All transportation is handled by our Logistic management team utilizing the main logistics suppliers, with whom we, as a group, have leverage to ensure prioritization when necessary, securing on-time deliveries. Utilizing both sea and air (standard or express) options allows for cargo consolidation, enabling us to dynamically use all available routes. This provides flexibility in terms of lead time, cost efficiency, and emission reduction.
Efficient complaint management
When unforeseen problems arise, our top priority is to keep your supply chain running without the risk of further defects. At the same time, we kick-start our root cause analysis, conducted either in one of our laboratories or within the production process to identify the issue and implement both corrective and preventive actions to eliminate the risk of recurrence.
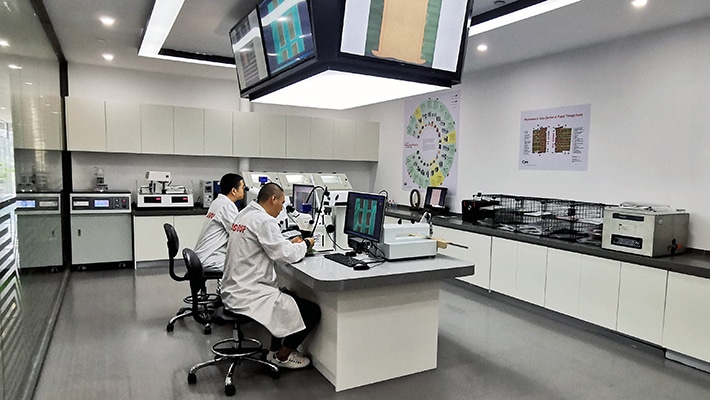
Being on-site allows us to maintain continuous communication, ensuring all parties are aware of the progress being made to resolve the problem and provide updates on recovery activities. This is all documented and reported using an NCAB 8D corrective action report. These actions are then verified on-site during the next factory meeting.
Factory presence
– providing maximum performance
To ensure long-term quality and flexibility, we don’t own any factories. Instead, we select the best-performing manufacturers globally that we want to work with. This demands a deep knowledge of each factory and a strong on-site presence to secure that our production standards are met.
Systematically sourced factories
Finding a PCB factory is not so difficult but finding a reliable one is. Our process for finding and quality-assuring the right partners has ensured that we always have factories that match customer requirements. Finding and developing the right ones requires a broad range of expertise. Our sourcing process described below shows how we approve our partner factories.
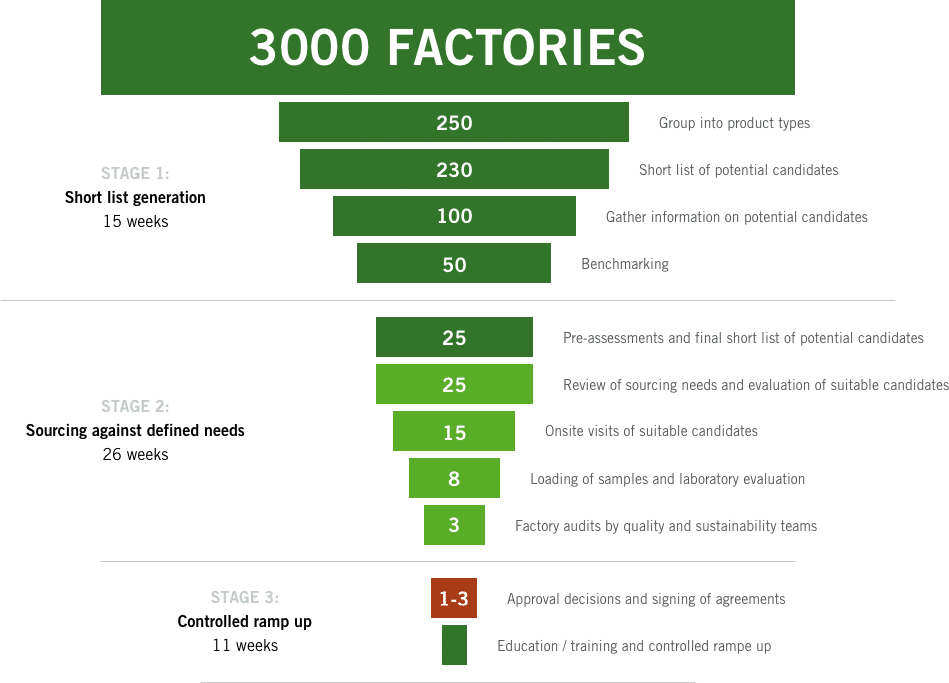
Use the factory for what it is good at
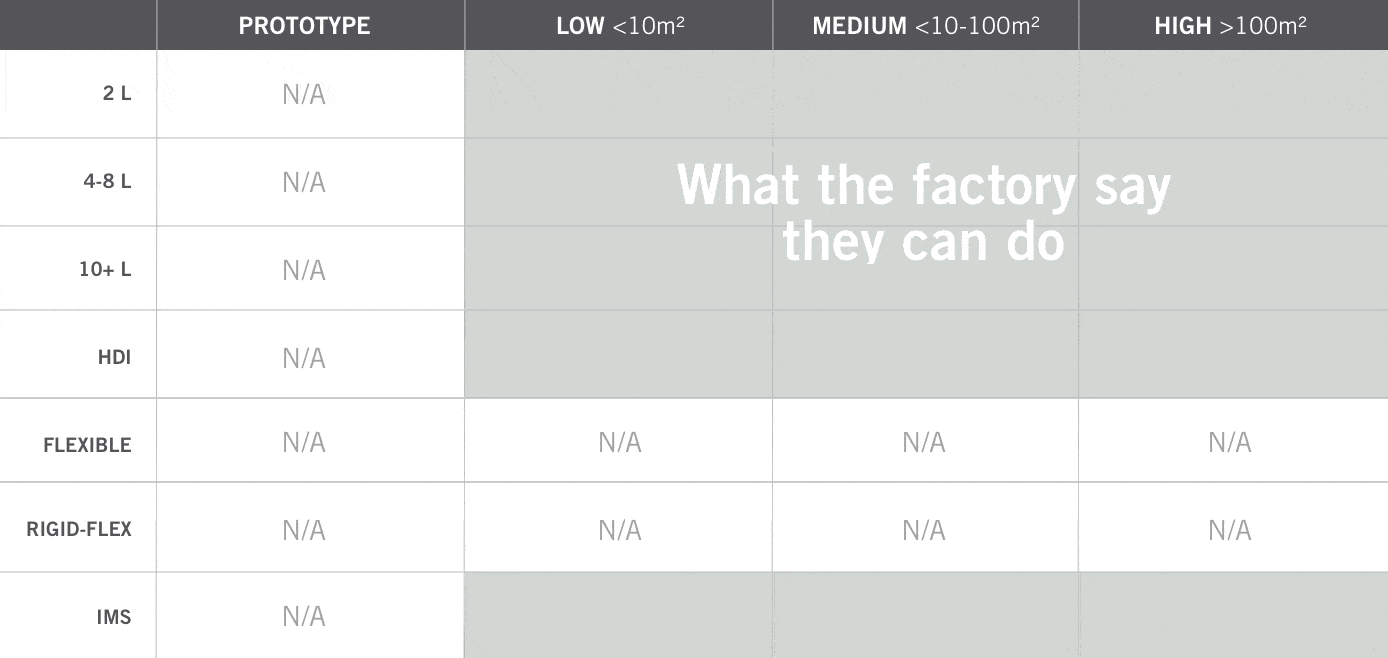
We source and approve factories based on the technologies, volumes, and industry sectors they can reliably support. The same approach is applied when developing existing factory partnerships. Projects are only placed in the most suitable factories—ensuring production meets our expectations for quality and delivery performance, which exceed industry averages.
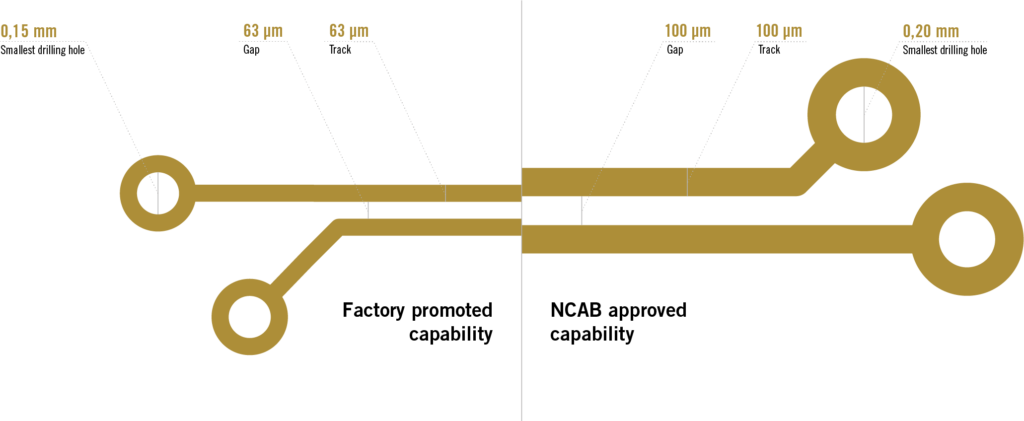
Production control throughout the whole process
Our own PCB specification, related acceptance criteria and quality control in our main factories ensure that the product delivers what it promises. Our PCB specification is a comprehensive document listing over 100 different requirements, all of which must be met while manufacturing PCBs for our customers. The specification either complements or goes beyond the established industry standard of IPC class 2.
We have Production Quality Engineers (PQEs) and Quality Control technicians (QCs) on site. Our PQEs are working proactively to achieve improvements and are responsible for the factories’ performance, as well as for building relationships. Our QCs confirm that the PCBs are manufactured and verified according to our specifications. Our dedicated teams are composed of selected factory employees – including production controllers, customer service representatives, pre-production engineers, and inspection teams. Each team member receives additional training from NCAB, focused on meeting both our own and our customers’ requirements. These teams are fully dedicated to handling, preparing, and controlling our orders.
Audits to ensure quality and sustainability
As part of our production control in the main factories, we carry out full quality audits every year that focus upon the production process and other related aspects. These audits take three days for three auditors and cover eight different areas.
In addition, in our main factories in China, we also conduct pre-production process audits that examine front-end processes and associated controls. These annual audits are supplemented by monthly process audits, where we focus our expertise on specific areas to ensure continuous improvement.
Our sustainability audits aim to improve working conditions and environmental performance. A full audit at a factory normally takes two days with two auditors, and the follow-up audit takes one day. All our main factories in China undergo the auditing process every other year.
Stable, high-level performance
To give our customers a competitive advantage, enabling them to operate efficiently and allocate resources toward growth rather than addressing challenges in the PCB supply chain, we operate with high-performing KPIs.
Our main KPIs
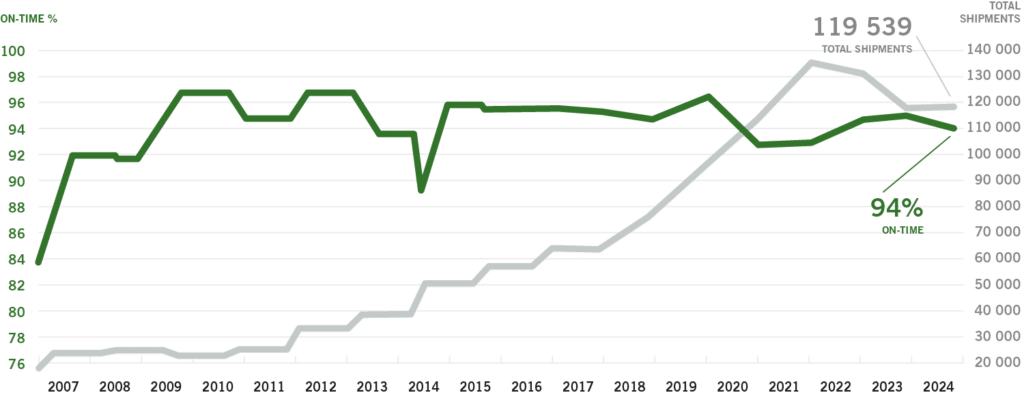
On-time deliveries – delivery precision is measured by the percentage of orders delivered in full, on time, or early to the customer’s site. Through forecasts and buffer stocks, 100% delivery accuracy can be achieved.

PCBs with zero defects – quality performance is measured based upon the number of customers claims against order line delivered.

Customer satisfaction Index – reflects how our customers view NCAB Group based on a number of quality criteria. The result is used to identify improvement areas to increase customer satisfaction.
Environment – Reduce our Greenhouse Gas emission intensity with 50% by 2030 (Scope 1-3). Baseline year 2021 (28.7 tCO2/MSEK).