PCB design – what you need to know
Nothing affects the PCB’s total cost and reliability as much as the initial design, but what are important to think about when designing a reliable PCB? In this page we have collected everything you need to know about printed circuit board design – including our design guidelines, design tips, things to think of when designing PCBs for industries that demands specific requirements and regulations, how to design for a cost efficient – and more sustainable – PCB and more.
Don’t hesitate to contact your local PCB technician for support – we are always happy to help!
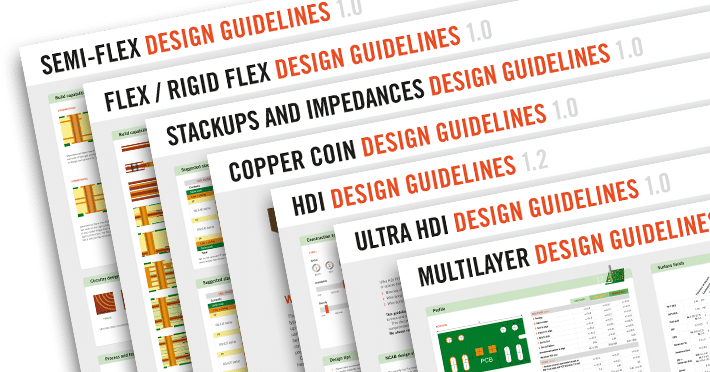
Design tips for PCB
Multilayer PCB
A Multilayer PCB is made with three or more conductive copper layers. The conductive foil appears to be various layers of a multi-sided circuit board. The different inner layers are processed in pairs (on a core) and then bonded together using prepreg as the insulating layer. The layers are then placed in such a way that both sides of the PCB can be used to mount components with additional tracking/electrical connections on the inside of the board. Vias are used as a source of the electrical connections between the different layers of a multilayer PCB.
Read our design tips for Multilayer PCBs:
- If specifying the build, aim for a symmetrical stack-up in terms of dielectric spacing to reduce the risk of excessive bow & twist on the final board.
- Internal copper plane layers shall be placed symmetrical in the stack-up, to minimize bow & twist.
- Avoid using cores as outer layer as this increase cost.
- Use the same copper thickness on both sides of an inner layer core for smoother production.
- Aim for similar amount copper area on top and bottom side to avoid over / under plating by using copper filling in empty areas.
- Avoid tight hole tolerances when not needed.
- Allow the factory to remove non-functional pads for via holes if uncritical. Read IPC-2222B, 9.1.4 table 9-3 for better understanding.
- Use tear-drops in all layers, on all designs both for IPC class 2 and 3. This will help reliability and reduce the need of Engineering Questions.
- Use balanced spacing between important components to avoid uneven copper foil and inconsistent PCB heat dissipation, resulting in bow & twist.
- Utilize back drilling structures instead of sequential lamination to avoid unwanted via stubs. This will reduce pressing cycles / process time and also save cost.
- Utilize thin trace widths only locally such as routing inside BGA pattern and other dense footprints.
- Always prioritize trace separation before trace width, to make room for etch compensation in the factory.
The above text is an extract from our design guideline about Multilayer PCB, if you want access to the whole design guideline, download it below.
HDI PCB
IPC-2226 defines HDI as a PCB with a higher wiring density per unit area than conventional circuit boards. Get some design tips below.
- Aspect ratio recommended as 0,8:1 for laser drilled microvia (L1-L2), advanced is 1:1.
- For better reliability, we recommend that microvia should be 100um when copper filling.
- If possible entry and capture pads should be 200um greater than the microvia size.
- Epoxy plugged via holes should be the same size if possible. Certainly no more than 0,15mm variation in size.
- Always copper fill microvia in SMD pad. It is more costly, but it will provide a better and more reliable option.
- Best practice is to stagger, rather than stack microvias on buried via holes as this relieves stress on the microvias.
- Where possible we recommend 400um between microvia holes, 300um at lowest to ensure no processing issues.
- Always plug through hole via in SMD pad according to IPC-4761 type VII.
- Skip via structures are not preferred, staggered structures are recommended.
- Always resin fill skip via holes.
- Aspect ratio recommended as 0,67:1 for skip microvia (L1-L3), advanced is 0,8:1.
The above text is an extract from our design guideline about HDI PCB, if you want access to the whole design guideline, download it below.
Flex / Rigid-Flex PCBs
The demand for flexible PCBs is increasing in all business segments with especially strong demands from medical, defense and industrial markets. Get the design right with our design tips below.
- Adhesiveless polyimide systems should be used due to increased reliability and lower z –axis CTE expansion compared to adhesive systems (acrylic = 2,5 x PI in terms of z-axis CTE).
- For dynamic applications keep layer count as low as possible.
- Static / flex to install applications can support higher layers in the flex construction (XX max).
- Semi-flex can be used for flex to install applications – multiple flexing increases risk of cracks in FR4 / copper.
- For dynamic use materials (FPC + coverlay) with similar properties.
- Use IPC-2223 to calculate accurate flex length for minimum bend radius. Incorrect length causes problems.
For basic guides to achieve approximation
1L flex = 3 – 6 x FPC thickness
2L flex = 7 – 10 x FPC thickness
Dynamic = 20 – 40 x FPC thickness
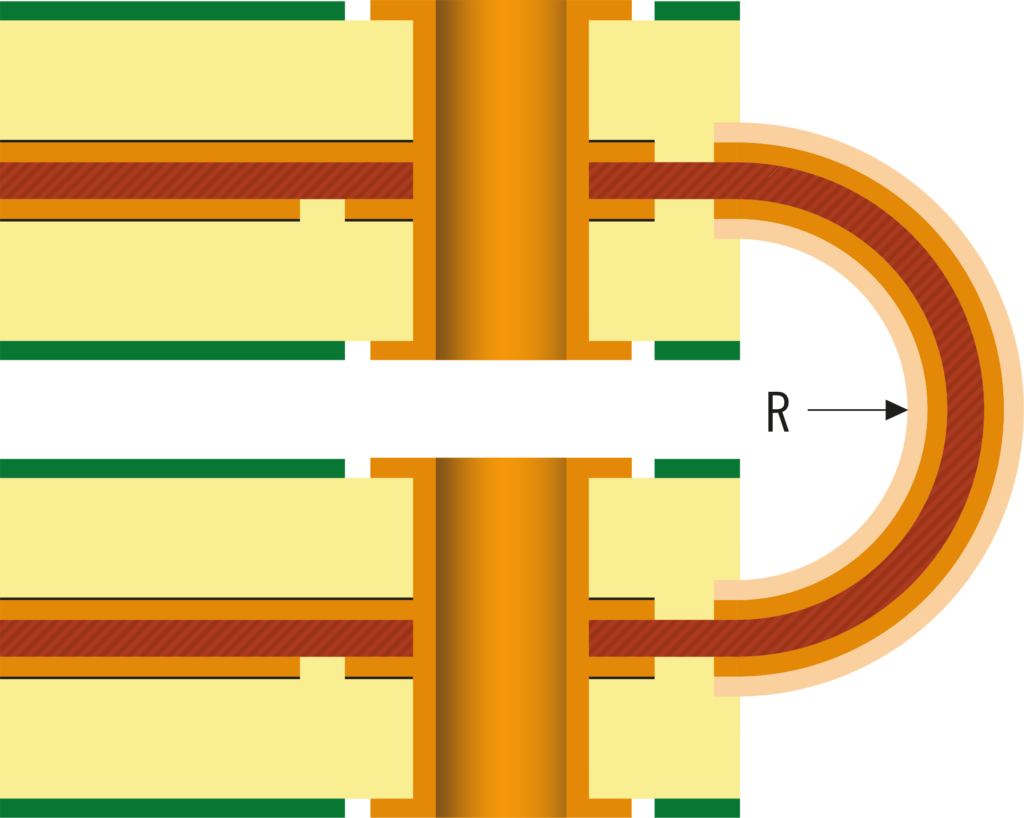
- NO sharp edges or corners on flex outline / circuitry.
- Solid copper fill on back of gold finger, if stiffeners cannot be added.
- Always keep stiffeners the same thickness.
- Always design pads larger than coverlay.
- No overlay of tracks for dynamic applications
– they should be offset when comparing L1 to L2.
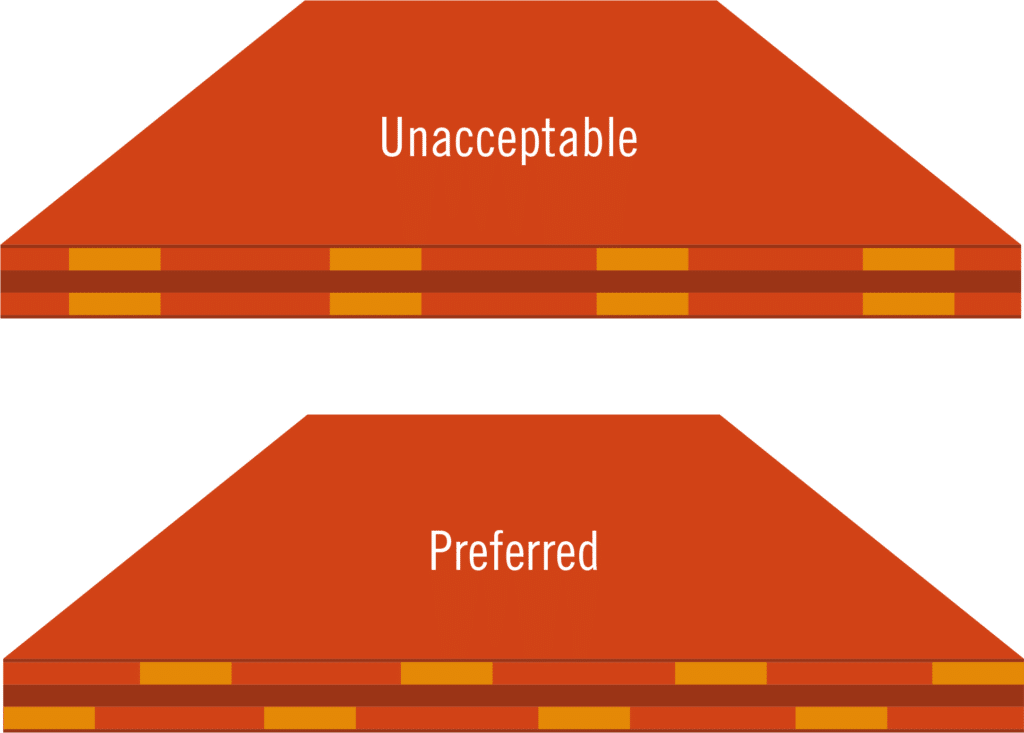
- As per IPC it is allowed for 300um adhesive squeeze out from the edge of the coverlay, so ensure features have sufficient spacing / distance from the termination of coverlay.
- Think in flexible terms – that straight flat flex can flex to fit.
- Outline considerations for robust flexing.

- Large radius in corners (>1.5mm, large = better)
- Tangent / same position corners on same feature
- Recessed slot
- Hole at slit termination to stop tearing (>1.5mm)
- Extra copper to strengthen corner
- Drilled hole at corner (>1.5mm)
The above text is an extract from our design guideline about Flex / Rigid-Flex PCBs. Follow the link below to get access to the whole design guideline!
Semi-Flex PCB
Semi-flex is effectively a ‘standard’ multilayer PCB, built using specific types of FR4 that has been depth to a specific tolerance so that the resulting thinner area provides a flexible / bending section of the traditionally rigid FR4. See our design tips below.
- Semi-Flex can be used for ‘Flex-To-Install’ static applications, or applications that have a VERY limited or controlled number of bends. ‘Dynamic Flex’ usage or multiple flexing increases risk of cracks in FR4/copper.
- For dynamic use materials ( FPC+ coverlay) with similar properties.
- Estimation of minimum bend length (marked ’G’ in below figures as shown under Process and technology capabilities). Many factors can play into a semi-flex circuit’s ability to withstand the bends required by the application. Some of these factors include, but are not limited to
a) Base material type and its flexibility
b) Bend area thickness
c) Bend radius
d) Copper type(RA, ED, etc.), thickness and elongation
e) Static applications requires specific bending angle & bending cycles
f) Conductive layers in bend area and stress concentration features.
Since no formula or calculation can possibly predict every possible construction and usage, it is recommended that the circuit design follow below formula to estimate the basic bend length, which is given by:
G= (πR (A2) ÷180) + 4mm
where:
G=minimum bend length
R=basic inner bend radius
A2=the bending angle, in degrees.
4mm is from experimental empirical value for safety compensation.
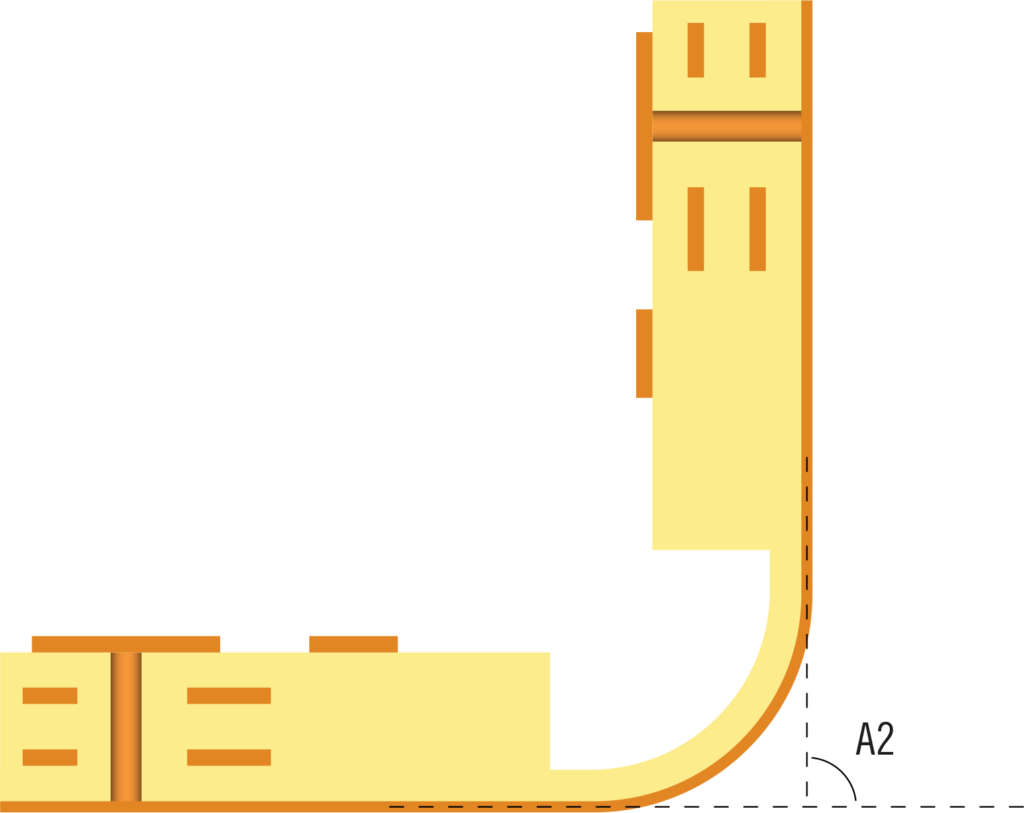
Detailed calculations about bend radius should refer to the basic empirical formulas which can be seen as below
MINIMUM BEND RADIUS (R) FOR ≤ 90 DEGREE BENDING | ||
---|---|---|
CONDUCTIVE LAYERS IN THE BEND AREA | STANDARD | ADVANCED |
1 layer | ≥ 5 mm | ≥ 3 mm |
2 layer | ≥ 7 mm | ≥ 5 mm |
It is preferable that a semi-flex PCB be allowed to follow its own natural bend. Bends greater than 90°and containing a small bend radius should be avoided.

- For 180 degree bending:
For improved strength and reliability, a 2 x 90 degree bending (Fig 1) is suggested to be used instead of 180 degree bending.
For 180 degree bending, radius >=5mm is recommended.
It is recommended to use a thin FR4 core 0.075-0.1mm (Fig. 2), this will give more flexibility for bending. Due to the use of de-capping process, the remaining surface will be smoother and better thickness tolerance. Only 1L copper is recommended.
During the bending operation, it is suggested to use a support tool (bending die) (Fig. 3). Make sure this mandrel fully supports the semi-flex area during the bend.
For reliability and avoid fractures in the material under bending, we recommend copper fill in the bending area. Add dummy copper where needed, in cooperation with NCAB FAE.
Bending in Warp direction of the glass fiber will improve bending performance. So to design all bending zones in same direction is recommended. - Maximum bending cycles
Although SemiFlex is a bend to install technology, repeated bend cycles may be possible. Maximum number of bend cycles must be discussed with your local NCAB FAE. The required bend cycles shall be clearly written in the procurement documentation. - Selection of Flexible Soldermask or Coverlay
Generally, flexible soldermask is recommended for coating outer layer copper feature only in bend area when less than 10 bending cycles and where bending strength is not high. If bending application requires more than 10 bending cycles and high flexural strength, it is recommended that using Coverlay. - The bending area should be facing outwards. Facing inwards would greatly increase the mechanical stress that may weaken the structural integrity of the PCB. The copper layer shall be on the outer layer / outside in the bend area. See Fig 1-3 above.
- If the bend area contains only a single conductive / copper layer, then It is recommended to add copper fill in the bending area to even out the copper distribution in the bending area. This will distribute the forces and minimize the risk of cracks. An example can be seen in the graphic below where the yellow colour represents added copper. If the design contains more than one conductive / copper layer in the bend area, then it is recommended to contact your local NCAB FAE to discuss the design.
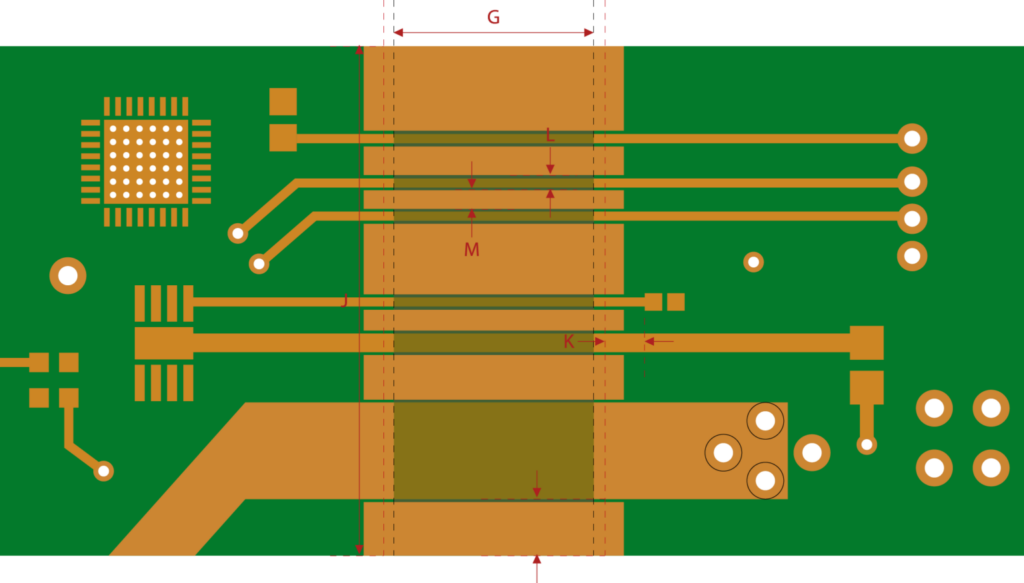
The above text is an extract from our design guideline about Semi-Flex PCB, to get access to the whole design guideline, follow the link below.
Ultra HDI PCB
Ultra HDI PCB is defined by IPC as a PCB with attributes beyond the existing IPC-2226 A producibility level C, where one or more layers have lines or spaces below 50 um. Below we give you some design tips.
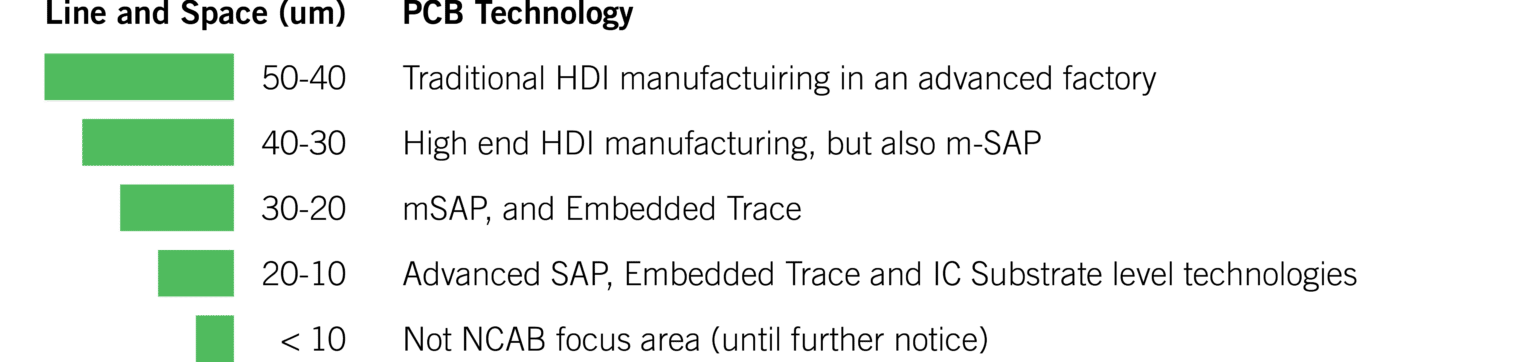
- Reduce track before space when smaller size is needed.
- Every stackup must be approved case by case, specially when coreless or odd layers are requested.
- Minimum dielectric thickness of core and prepreg can be 0.025mm (1mil).
- Overall thickness of the board can be 0.12-2.0mm, should be <=2.0mm.
- Avoid Plated Through Holes when start/stop layers are UHDI
- Copper thickness in UHDI layers will be thinner than the normal HDI layers. Exact start copper and final copper must be evaluated in each case. Normally, the minimum final copper thickness of conductors will be 8-30um.
- Cores with “X” micro-via drilling is available on request. Core thickness between 60-160mm with hole size<=80um.
- For bonding pads, the width will be measured on the top of the pad. Required minimum bonding pad area must be specified and agreed.
- Check with local office if the tolerance of pad size <=+/-10um needed. The advanced capability now is +/-5um.
- For SM flatness 5-7um, dry film solder mask will be used, but availability is limited to Substrate or Substrate Like PCB factories.
- All designs with Track/ gap less than 35 um must be evaluated case by case, and typically with limited layer count.
- Surface treatment ENIG, ENEPIG, OSP, Immersion Tin and soft gold plating is available. But for FCBGA, ENEPIG is recommended but less available. Immersion tin is recommended in some factories.
Stackups & Impedances
Below you will get some design tips for stackups and impedances.
Stackup
- Make sure the stackup is symmetric.
- Normally suggested stackups are a foil build. Special core build is possible (for example with Rogers), but not common.
- Standard thickness tolerance of +/-10% is for board >1mm. Standard thickness tolerance of +/-0,1mm is for 1mm board. Thickness tolerance for board ≤1mm shall be approved by NCAB.
- Minimum dielectric thickness will be 90μm according to IPC if FAB drawing doesn’t specify anything and there aren’t Micro vias.
- Keep in mind to use maximum 3 sheets of prepreg to bond layers together.
- The stackup used in production might be a bit different to the specified one, but an EQ will be send to confirm it. This happens due to the copper distribution, materials on stocks, etc.
- For thicker copper foils needs thicker dielectric between layers.
- Foil thickness value after processing is not the same as base foil.
- Differences in the % of resin for same prepreg type will have impact on different thickness of the prepreg.
- If you require microvias in your product, keep in mind Aspect ratio (recommended (0,8:1)and advanced (1:1) when you choose the right prepreg.
- If you require special materials, thickness tolerance or stackups, contact your local NCAB office.
Impedance
- Consider better type of material (medium, high or ultra-high speed) and flat glass style when signal speed is above 2 GHz and timing is critical.
- Ensure a reliable lamination process and avoid risk of resin starvation by letting factory selecting number of prepregs, prepreg styles and resin content in the stackup.
- Keep in mind primary drivers of impedance signal losses:
1 Line length (line losses are directly proportional to line length, shorter line less losses / longer line – greater losses)
2 Dielectric loss (can be reduced by appropriate material selection)
3a Copper loss (cross-section area – stackup design)
3b Copper loss due to surface roughness (can be reduced by material selection and/or stackup) - When request tighter impedance tolerance (below +/- 10%) discuss with your local NCAB contact window what is possible for your design.
- When designing rigid-flex boards, please note that separate calculations need to be done for the rigid and flex part for the same signal.
- Thickness and dielectric constant of solder mask will be adjusted by manufacturer depend of their solder mask properties / printing method.
- Differences in the % of resin for same prepreg type will have impact on impedance.
- If you required support for impedance calculations, contact your local NCAB office.
This is an extract from our design guideline about Stackups & Impedances.
Copper coin
The copper coin PCB is a piece of solid copper inserted onto or into the PCB, typically under components which need cooling. It can provide up to 10 times the cooling compared to a via farm of same size. See our design tips below.
Mechanical advice
- It is recommended to have the same hole size for all holes in the coin.
- When different size coins are used on the same unit, the size difference should be ≥1mm. If the difference is <1mm, we suggest to use same size.
- Minimum difference of long size and short size of the coin preferred to be >= 1.0mm. A difference <0.3mm will be taken as same size.
- Number of coins per unit may be up to 32 pcs, but this also depends on the the coin sizes, PCB size and customer panel. Please ask NCAB before you start design.
Design guide
- Connections V5 is done by laser milling and copper filling. Preferred maximum size of the opening to be filled is 4×4 mm. If a larger area needs to be connected, please contact your local FAE.
- Copper coin can be embedded, press fit or be bonded by conductive adhesive film.

- Copper coin can be used in normal high layer count, IPC 4761 type VII plugging, HDI or Rigid-flex constructions, but each factory has individual limitations. It is recommended to ask NCAB before starting a new design.
- Different types of coins can be in one unit, but we recommend less than 3 different types or sizes.
- The Aspect ratio limitation of blind via in a coin is <1:1, but for optimal production the preferred is 0.8:1.
- Any construction with coins must have a symmetric build, which means same core and prepreg each side of the centre core.
- The Shape of T coin should be symmetrical in both X and Y direction, which means the size Q shall be the same on both sides, but Qx and Qy can be different. If you need an asymmetric shape please contact your local NCAB FAE.
- Coin attachment by conductive adhesive can be available depending on design and factory capability. Please check with the local NCAB FAE before you start design.
- Coin by press fit attachment has limitations. When press fit is used, the push/pull strength might be limited. Please contact your local NCAB FAE for further checking.
This is an extract from our design guideline about Copper Coin.
Design for different industries and applications
Different industries and applications have different regulations and demands for the PCB design that are important to know of.
In a couple of blog posts, we have gathered some tips and information about how to design PCBs with specific demands and regulations.
PCB design for extreme environments
PCB design for EVC – Electrical vehicle charging
PCB design for aerospace
PCB design for railway
PCB design for medical application
PCB design for high-power applications
PCB design for extreme environments
What is important to consider regarding PCB design for extreme environments? Learn more about the challenges and how the PCBs needs to be adapted for thermal management, altitude and shock and vibration events.
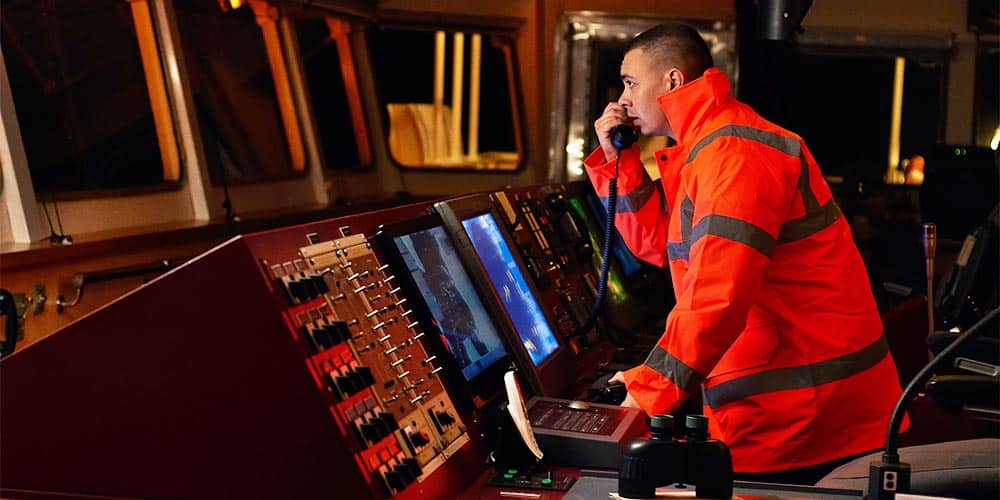
PCB design for handling shock and vibrations
We can design more mounting holes into the board. More mounting holes means more mounting points to the chassis and more stability. This will also allow the addition of more dampening devices to be mounted into the system.
Another aspect of the PCB we want to address is the stackup. For boards that will be subject to extreme shock or vibration events it is critical to ensure the pre-preg has enough resin content to withstand these types of events. The pre-preg resin is the glue that holds the board together. During shock and vibration events the PCB may flex and cause stress on the connection points. In order to mitigate as much stress as possible we should consider using pre-pregs with over 50% resin content. In addition, adding more than two sheets is another way to add more bonding strength. I say this as a consideration because signal integrity requirements do not always allow changing dielectrics easily.
What if you do not have a signal integrity requirement? If three sheets of pre-preg is good then four has to be better, right? It may. At a certain point too much pre-preg will be detrimental to the layer-to-layer registration. I would try to stay with three sheets max, unless your PCB vendor says otherwise. If you are after more thickness, but cannot add any more pre-preg, consider using unclad cores in the stackup. Unlike the pre-preg, an unclad core is already cured, so it does not add any resin to the press cycle. Thus, layer-to-layer registration is not sacrificed.
PCB design for EVC – Electrical vehicle charging
Driven by electricity instead of fossil fuels, electric vehicles (EVs) are revolutionising and shaping our mode of transportation. But what are electric vehicles and their reduced environmental impact if you’re not able to charge them? Learn about PCBs for electric vehicle charging – the trends, design considerations and NCAB´s added value.
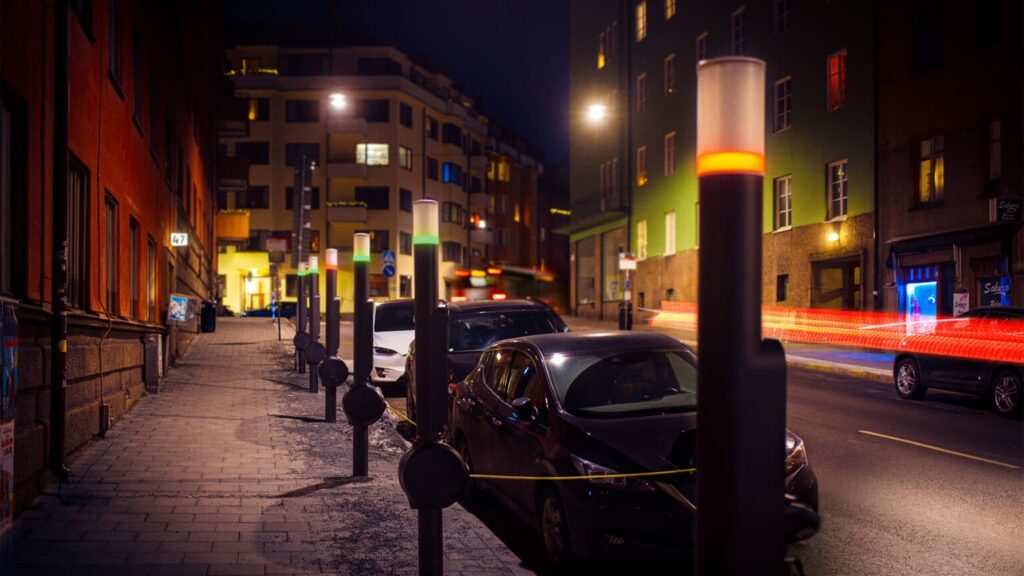
Key factors to consider when designing and producing a PCB for electric vehicle chargers
EV charging is an application and end-product which requires high-power circuit design.
High-power circuits are characterized by their significantly greater voltage or current levels compared to those utilized in low-power circuits. Designers bear the responsibility of ensuring the circuit functions within the appropriate voltage and current parameters, while also incorporating adequate cooling and safety measures.
When it comes to high-power PCBs, they typically follow one of two design approaches: layout design or reference design. Layout design pertains to the arrangement of components on the PCB, while reference designs are typically created with specific layouts in consideration. The PCB layout must be meticulously crafted to accommodate high-power components effectively and minimize the generation of noise.
Another consideration to consider is component placement. The high-power component placement is a design technique that is used to reduce the thermal resistance of the PCB. This technique is used when there are high-power components on the PCB.
PCB design for aerospace
The PCB design and performance, a key to all aerospace systems, must be impeccable. To ensure the necessary quality, suppliers for aerospace efforts must meet AS9100 standards, which impose additional measures to the ISO9000 international requirements for quality systems. It provides a deep extra layer of protection for everyone involved.
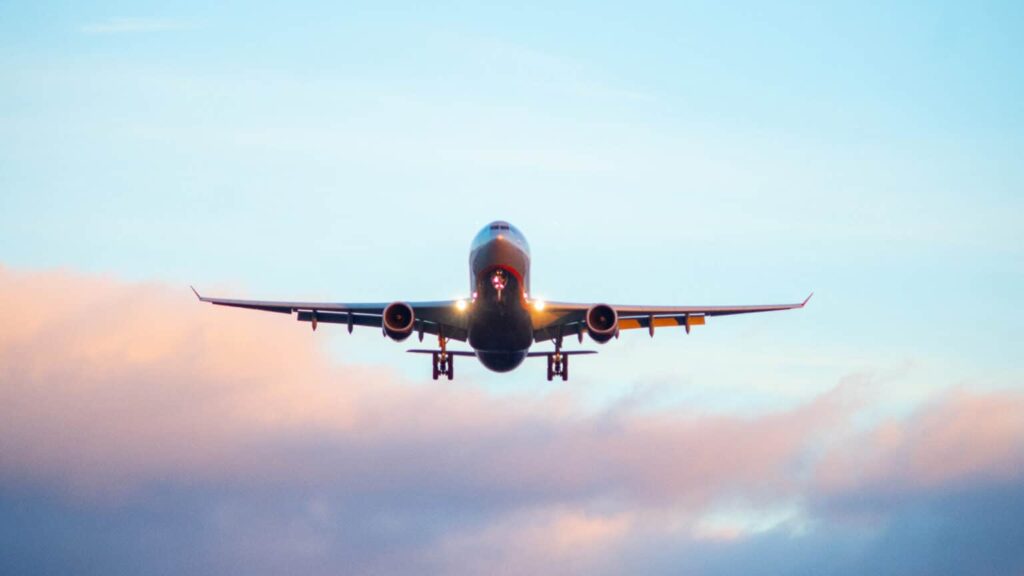
Design and Requirements: PCBs for Aerospace
We recommend your supplier has their own set of PCB specifications. For example, in our PCB Specification, we address a number of IPC AABUS (As Agreed Upon Between User and Supplier) rules and requirements that shall be agreed between buyer and supplier. We cover various requirements typically forgotten by the designer, and in some cases, we exceed IPC class 2 requirements to ensure high reliability at best possible price.
Select high-quality materials. This step is essential to creating the reliability and durability needed in aerospace PCBs.
Conformal coating of the assembled PCB is often present in aerospace processes. Conformal coatings are used to protect electronic components from the environmental factors they are exposed to. Successful conformal coating will prevent the board from corroding. The use of conformal coatings requires excellent adhesion to the soldermask. We have tested and certified a number of soldermask and conformal coating combinations that will secure sufficient adhesion.
With the local and global regulatory bodies as well as guidelines from federal and international guidelines, there is an immense amount of requirements and regulations when designing and sourcing PCBs for aerospace. We always recommend working with a trusted PCB supplier from the start of the design phase to stay abreast of necessary requirements and design support based on practical experience, but this is particularly crucial with aerospace applications.
PCB design for railway
In general, when a PCB designer faces the challenge of creating a printed circuit board for a railway application, the common regulation for the design of the railway application that one should refer to is UNE-EN 50124-1 – The European Standard. However, given the high reliability required for most railway applications, another fundamental standard is to be considered: IEC 61508 – An international standard published by the International Electrotechnical Commission.
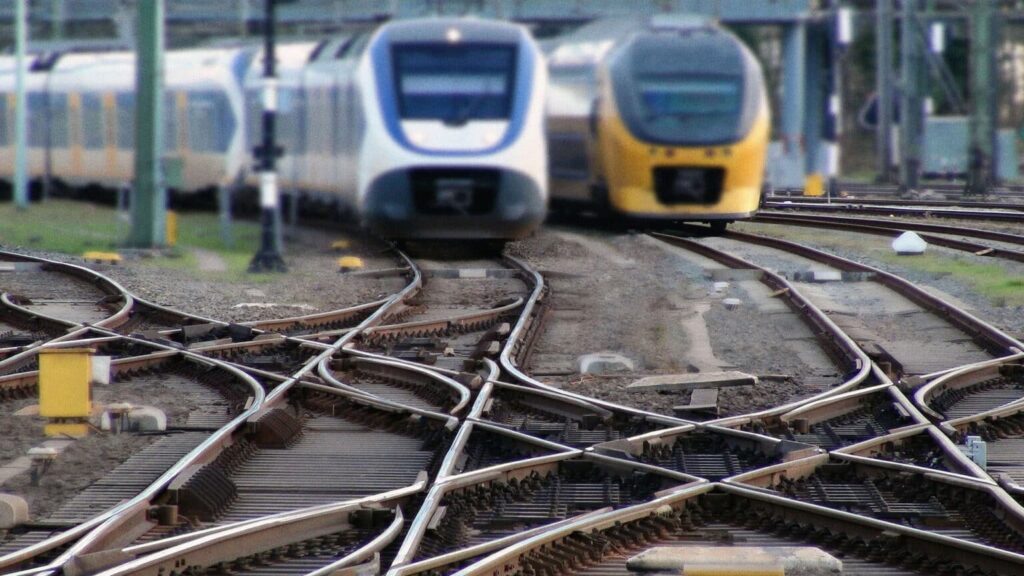
IEC 61508 Regulations
IEC 61508 provides functional safety standards for the lifecycle of electrical, electronic, or programmable electronic (E/E/PE) systems. Two of those standards being:
- Specific architecture requirements to comply with SIL (Safety Integrity Level)
- Methodology for obtaining FCC (Federal Communications Commission) compliance. They do not consider the concept of Fail Safe.
There are three fundamental principles in IEC 61508:
- Zero risk “can never be achieved.”
- Non-tolerable risks must be reduced.
- Security management must be considered from the beginning.
This regulation is, in turn, the basis for other standards that apply to the railway sector, such as CENELEC.
PCB design for medical application

Key factors to consider when designing and producing a medical PCB
When designing medical PCBs, there are several key factors to consider to ensure it is safe. In addition, manufacturing medical PCBs requires careful attention to detail and strict adherence to quality standards to ensure that the resulting devices are reliable and effective. Here are some critical considerations when designing manufacturing medical PCBs:
- Signal integrity is also important for medical PCBs, as electrical signals must remain clear from noise and interference while traveling along the traces. It is essential to ensure that the PCB layout and routing selection follow best practices to minimize any unwanted noise on traces.
- EMI/EMC compliance must be taken into account, as electrical interference can affect not only the operation of the device but also other nearby devices or systems.
- Power consumption is also a key factor to consider when designing a medical PCB, as some devices may require very low power levels for portability or battery operation. It is essential to ensure that the board layout does not impede any power efficiency gains, and that all materials chosen minimize energy needs without compromising performance.
- DfM design for manufacturability must be considered, as medical boards need to meet strict standards for precision and quality typically part of an IPC 6012 Class 3 build. DfM is critical to ensuring the design and the supplier are compatible at the most stringent aspects of the design.
- High reliability is of primary importance for medical PCBs, as failure of a medical device could potentially put lives at risk. Parts should be selected that can withstand the intended operating environment, including temperature fluctuations and humidity levels, to minimize premature degradation or failure.
- Quality Control is critical for medical PCBs to ensure that they meet the required standards and specifications. The manufacturing process must be closely monitored and controlled to ensure that the PCBs are manufactured to the required tolerances, dimensions, and electrical properties.
- Traceability — medical device manufacturers must be able to trace every component of the device, including the PCB, from the supplier to the finished product. This requires strict adherence to traceability protocols, including component tracking, lot tracking, and serial number assignment. Medical device manufacturers must also maintain comprehensive documentation and records of the manufacturing process, including material traceability, testing results, and validation reports.
- Material Selection — the materials used in medical PCBs must be carefully selected to ensure that they are compatible with the device’s intended use, sterilization method, and regulatory requirements. The materials used must also be free from contaminants and impurities that could impact the device’s safety and efficacy. The type of material used in a medical PCB is also critical for safety and reliability. Materials should be carefully selected for their properties, durability and flame retardancy (as appropriate) and must be UL approved.
- Environmental Controls — the manufacturing environment must be carefully controlled to ensure that the PCBs are manufactured in a clean and controlled environment free from contaminants and particles that could impact their performance or safety.
- Testing and Validation: Medical PCBs must be tested and validated to ensure that they meet the required standards and specifications. This includes testing for electrical performance, environmental performance, and compatibility with the device’s other components.
PCB design for High-power applications
Electronic devices are becoming more and more complex as the years go by. This means that the PCBs must be designed with precision and care to ensure that the end product is successful. The most important thing to remember is that high-power circuits are not just a single component but a system. The system has to be designed with consideration for all its components, including the circuit board, electronic devices, thermal management, and power supply.
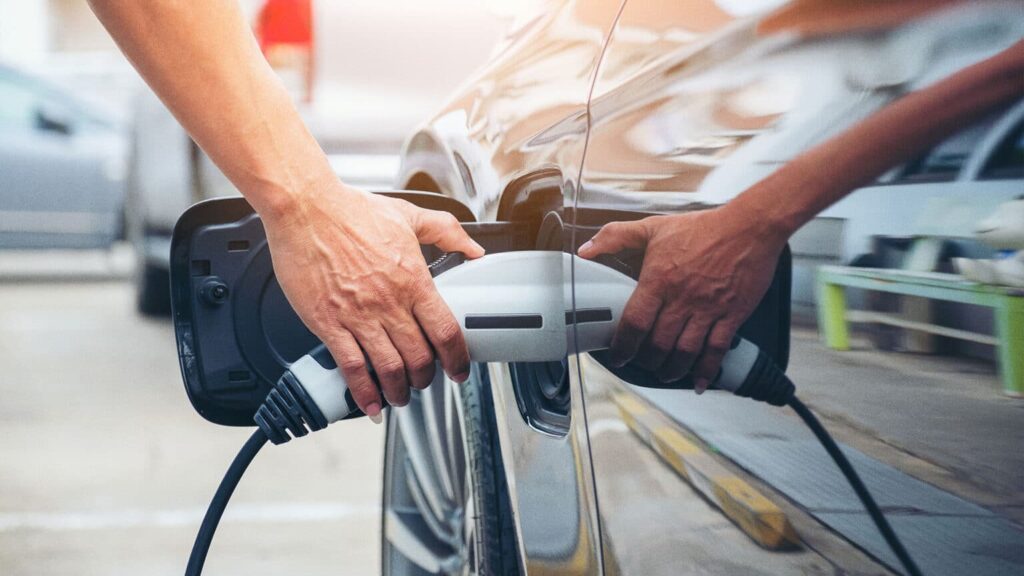
High-Power Considerations for Design
High-power applications are those that require a lot of power to operate. This is usually because they are used in devices that need to be able to run for a long time without being plugged in.
High-power circuits are defined as having a voltage or current of an order of magnitude higher than that used in a low-power circuit. Designers must ensure that the circuit operates at the proper voltage and current and has enough cooling and safety provisions. The following are aspects that need to be considered in the high-power design.
PCB design tools – for reliable printed circuit boards
Nothing affects the PCB’s total cost and reliability as much as the initial design. That is why we have put together our PCB design tools for engineers, designers and anyone else involved in the PCB design or production process. Our current PCB design tools are PCB design guidelines, PCB design tips, PCB design checklist and PCB cost drivers.
To help you get it right from the start and make reliable PCBs!
PCB design guidelines
In today’s world, electronic products are expected to deliver increasingly advanced features while becoming smaller in size. This places greater demands on the PCB layout and design, making it more crucial than ever to make informed choices during the design stage. To ensure a successful start, we have compiled our PCB design guidelines, which serve as a comprehensive checklist.
We have design guidelines for
- Multilayer PCB
- Flex / Rigid-Flex PCBs
- Stackups and Impedances
- Copper coin
- HDI PCB
- Ultra HDI PCB
- Semi-Flex PCB
To see all our design recommendations for the different PCB technologies, download the PCB design guidelines.
Our design tips to avoid the most common design mistakes
There are many reasons for mistakes. Whether it’s a default in your CAD program which was missed because of a variance, all the way to complex designs which require the implementation of very specific rules. We have created a tool for engineers, designers and anyone else involved in the PCB design or production process, that identifies some common mistakes, the implications these may have on the finished PCB and how to avoid them. The ultimate goal of this design tips tool is to provide support in producing reliable PCBs.
These are the 13 most common PCB design mistakes
- Annular ring issues
- Plated Through Hole (PTH) to Copper
- Non-plated Through Hole (NPTH) / NPTH slots to copper
- Holes located on edge of surface mount device (SMD) pad, or very close to SMD
- Trace width and isolation spacing doesn’t work with the selected base copper foil thickness
- Stubs (unterminated traces) on copper layer
- Slivers and same net spacing in copper layers
- Copper to edge – distance between copper features and profile
- Improper SMD/BGA pads design
- Soldermask is oversized / lack of oversize in the same design
- Soldermask bridge / web to small
- Coverage of soldermask
- Legend print problems
To read more about the different mistakes and learn how to avoid them – download our PCB design tips tool for free.
PCB design checklist – before your start to produce
Is your solder mask larger than the component pad? Have you considered any possible mechanical assembly problems using a 3D model of the assembly? To help you with this, we created the PCB design checklist. This checklist can aid you in your own design work. Alongside our PCB design guidelines, this will provide a total solution to further help you get it right from the start.
As always, you can reach out to NCAB’s technical team if there are any questions on this, or anything having to do with your PCB design.
PCB design checklist
- Placement Check
- Test Pin
- Component Packaging
- Mechanical Check
- Technical Check
- Constraint Rules
- Routing Check
- Timing Design
- Power Design Check
- DRC Check
- Test Pin
- Silkscreen Check
- Gerber Review
Does the PCB design have any impact on the cost of the PCB?
There are a number of factors that affect the price of the printed circuit board – including size, batch quantity, choice of materials, layer count and specifications & tolerances. NCAB’s technical support team is always on hand to offer helpful advice on designs and ideas that can avoid unnecessary expense whilst at the same time ensuring that the design and the printed circuit board itself is perfectly suited to the end application.
We have found that the majority of the cost – 80-90% – is built into the product in the early stages of the design phase. We have also found that many of the PCB cost drivers directly impact all aspects in producing and delivering a more sustainable product.
To help you avoid large cost drivers, we have made a tool – PCB cost drivers tool – that you can download and get some tips and inspiration from.
We divided the circuit board cost drivers in two categories; “hard costs” and “soft costs“. The hard cost drivers are covering aspects that relate to the physical printed circuit board itself. Examples being copper weights and build complexity. In these cases the impacts on cost and sustainability are more tangible. The soft cost drivers are those elements that unless considered can lead to delays in engineering, lost time and mis-specified demands that only serve to either drive cost upwards or fail to identify what is needed to achieve the desired quality or long-term reliability – this is not sustainable PCB production in our eyes. In our Sustainability Impact meter you can see the possible effects for each cost driver.
Hard cost drivers
- PCB size
- Layer count
- Build / Complexity
- Via treatments
- Material / panel utilization
- Track and gap
- Hole (size & quantity)
- Additional drilled/routed features
- Hard gold / Thick gold
- Impedance
- Excessive tolerances
- Copper foil weights
- Soldermask, legend/silkscreen, carbon print
- Surface finishes
- Materials
Soft cost drivers
- Under specification
- Over specification
- Reliability
- Lead times
- Transportation costs
- Lack of knowledge, communication, willingness
Do you need support with your PCB design?
Getting it right at the design stage can make all the difference between a printed circuit board meeting expectations and failing to live up to the expectations of functionality or performance. This does not mean that the PCB is faulty – given that acceptance or rejection criteria cannot be established without standards on which to base those criteria. We see PCB design support not only as defining what we need, but also what we do with your design from receipt of data through to the finished product.