The aerospace industry imposes strict standards on its suppliers. The reasons why are not mysterious. No other sector deals with higher stakes and has such potential for both wild successes and horrifying disasters. The necessary equipment for aerospace endeavors requires extraordinary sophistication and reliability, which also includes the reliability of the aerospace PCBs.
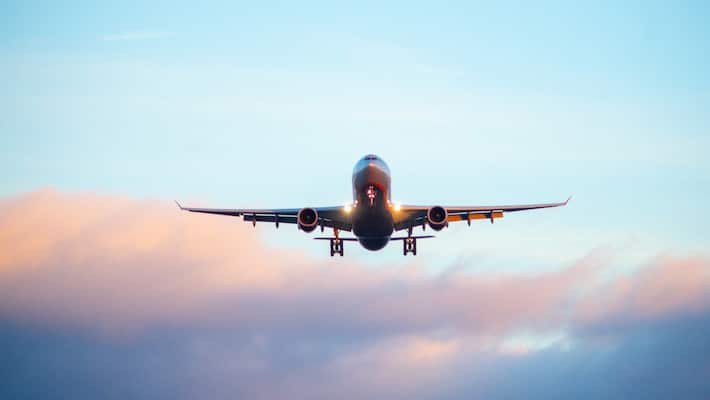
The printed circuit board (PCB) design and performance, a key to all aerospace systems, must be impeccable. To ensure the necessary quality, suppliers for aerospace efforts must meet AS9100 standards, which impose additional measures to the ISO9000 international requirements for quality systems. It provides a deep extra layer of protection for everyone involved.
What Is AS9100?
AS9100 was established in 1999 by the Society of Automotive Engineers and the European Association of Aerospace Industries. It included the ISO9000 standards and added increased audits other quality and safety requirements tailored for the aerospace industry. These requirements include:
- Operations Risk Management
- Product Safety
- Special Requirements
- Critical Items
- Configuration Management
- On Time Delivery
- Counterfeit Parts
- Expanded Requirements for Production and Sub suppliers
The major aerospace corporations insist that their suppliers comply with or achieve certification for AS9100 standards. This way, they ensure quality products and protect both those involved in flight and their companies’ reputations for excellence.
How Does AS9100 Impact the Supply Chain?
In addition to ensuring quality and safety, AS9100 improves efficiency, benefitting companies up and down the supply chain. These standards increase efficiency by ensuring regulation compliance, quality assurance, and risk mitigation. Products are able to smoothly go from manufacturers to suppliers, to warehouses, to transport, since every step works to maintain high standards.
Companies that meet the AS9100 standards and are certified have a competitive advantage in the industry since many companies will only work with suppliers that are certified. AS9100 helps maintain the integrity of the supply chain by eliminating poor-quality materials, inefficient practices, and substandard suppliers.
How Does AS9100 Affect the Production of the PCB?
AS9100 makes PCB production more demanding. The standards are higher, requiring more impeccable planning, constant monitoring, and intense quality-control measures. No level of contamination or configuration problems can be tolerated. PCB production for the aerospace community is a more time-intensive and expensive proposition for manufacturers and suppliers. PCB design must be sophisticated and meet every industry regulation. Companies that excel in this production must maintain highly proficient workers and advanced equipment. As a result of increased process and product control comes a strict reporting requirement regulated in Aerospace First Article Inspection Requirement AS9102 invoked by AS9102 7.5.1.1 Production Process Verification. This report shall provide objective evidence that all engineering design and specification requirements are understood, accounted for, verified and documented. A new report is required if there is a lapse in production for more than 2 years, any design change or any significant change in the manufacturing methods. In addition, any subassemblies shall be documented the same way.
What Are the General Requirements for Producing PCBs for Civil Aerospace?
In most cases, civil aerospace PCBs must meet standards for IPC Class 3 and ISO/AS9100. PCB designers and manufacturers must meet other standards as well, specifically, IPC 6012ES, an amendment that sets performance and certification requirements for aerospace rigid printed circuit boards. In addition, AS/EN9100 gives guidelines for quality and risk management for aerospace PCBs that are far more stringent than ISO9000 standards.
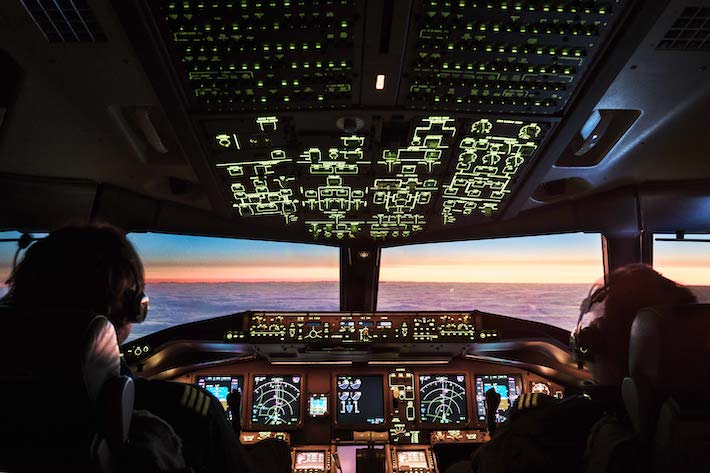
When producing PCBs for civil aerospace applications, there are certain requirements and standards set forth by regulatory agencies to ensure safety and reliability. The two primary regulatory agencies that oversee aerospace in different regions are the Federal Aviation Administration (FAA) in the United States and the European Union Aviation Safety Agency (EASA) in Europe. Each of these local authorities are members of the International Civil Aviation Organization (ICAO). Funded by the United Nations (UN), ICAO’s mission is, “To serve as the global forum of States for international civil aviation.” ICAO develops policies and standards, undertakes compliance audits including local authority regulatory bodies, performs studies and analyses, provides assistance and builds aviation capacity through many other activities and the cooperation of its Member States and stakeholders. The State has jurisdiction for Aircrafts, including manufacture of parts.
While both the EASA and FAA share a common goal of ensuring aviation safety, there can be some differences in their requirements and processes for aerospace PCBs:
Certification Process:
- FAA: The FAA uses a certification process based on FAR (Federal Aviation Regulations) Part 21. The FAA may require specific documentation, testing, and compliance with additional standards.
- EASA: EASA follows the European Union Aviation Safety Regulations (EASA Part 21, Subpart G; Production Organisation Approval (POA)). For example, NCAB holds a certified POA Auditor on behalf of SAAB, which means we at NCAB Group is certified to audit and qualify PCB factories for EASA on behalf of SAAB. Only Certified factories can deliver to the EASA program. Similar to the FAA, EASA may require compliance with additional standards. EASA rules under Part 21, Subpart G also covers quality system requirements. There are no strict rules for PCB design or a direction to use a specific PCB standard, but in most cases, standards must meet those for IPC Class 3 or IPC-6012ES, an addendum that sets performance requirements for aerospace rigid printed circuit boards. The exact specification is of course decided by the organization that designs and owns the product.
Environmental Testing:
- Both agencies require environmental testing to ensure that PCBs can withstand the harsh conditions of aerospace environments, including temperature extremes, humidity, vibration, and electromagnetic interference. However, the specific test procedures and criteria may vary.
Safety and Reliability:
- Both agencies prioritize safety and reliability, but they may have different approaches to assessing and ensuring these qualities in PCBs. Compliance with specific safety standards and the demonstration of reliability through testing are typically required.
Supplier Qualification:
- Suppliers and manufacturers of aerospace PCBs may need to meet additional quality and traceability requirements, such as AS9100 certification for the aerospace industry.
Documentation:
- Both the FAA and EASA emphasize comprehensive documentation to demonstrate compliance with their regulations. Documentation may include design specifications, test reports, quality control records, and traceability of components.
International Cooperation:
- EASA and FAA often work together to harmonize standards and certification processes, especially for products and components intended for use in both regions. This helps streamline the certification process for manufacturers.
Regional Differences:
- Keep in mind that FAA regulations primarily apply to products intended for use in the United States, while EASA regulations apply to products for use in the European Union. If your PCBs will be used internationally, you may need to adhere to both sets of regulations.
It’s crucial for manufacturers and suppliers in the aerospace industry to stay updated on the latest requirements from both the FAA and EASA, as these regulations can change over time. Additionally, working with experienced aerospace engineering and compliance professionals is essential to navigate the complex certification processes and ensure that PCBs meet all necessary requirements for safe and reliable operation in aircraft.
Design and Requirements: PCBs for Aerospace
- We recommend your supplier has their own set of PCB specifications. For example, in our PCB Specification, we address a number of IPC AABUS (As Agreed Upon Between User and Supplier) rules and requirements that shall be agreed between buyer and supplier. We cover various requirements typically forgotten by the designer, and in some cases, we exceed IPC class 2 requirements to ensure high reliability at best possible price.
- Select high-quality materials. This step is essential to creating the reliability and durability needed in aerospace PCBs.
- Conformal coating of the assembled PCB is often present in aerospace processes. Conformal coatings are used to protect electronic components from the environmental factors they are exposed to. Successful conformal coating will prevent the board from corroding. The use of conformal coatings requires excellent adhesion to the soldermask. We have tested and certified a number of soldermask and conformal coating combinations that will secure sufficient adhesion.
With the local and global regulatory bodies as well as guidelines from federal and international guidelines, there is an immense amount of requirements and regulations when designing and sourcing PCBs for aerospace. We always recommend working with a trusted PCB supplier from the start of the design phase to stay abreast of necessary requirements and design support based on practical experience, but this is particularly crucial with aerospace applications.
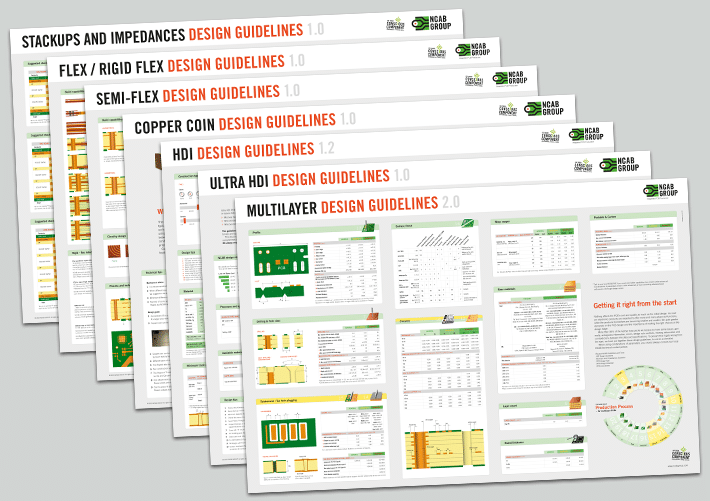
PCB design guidelines
Get it right from the start with our PCB design guidelines. To prevent getting it wrong from the start, we have put together our design guidelines, to use as a checklist.