– trends, challenges and expert insights for optimal design and production
Medical Printed Circuit Boards (PCBs) are the key component of modern-day medical devices. A PCB is an electrical interconnect, allowing power and data signals to be easily transferred within a device. Medical PCBs build on this concept by adding a human interconnect, meaning the physical form factor must meet stringent requirements such as small size, low weight, high reliability, and safety while also providing functionality that meets the needs of the intended user base. As a result, the demand for high quality and reliable medical PCBs has increased exponentially over time.
For anyone constructing a medical PCB, there are certain essentials you should know. In this guide, we’ll cover how to design medical PCBs, the latest medical PCB trends in this rapidly evolving market, and also show how we can help find the optimal solution for specific needs.
Current Trends in the Medical PCB Industry
As the demand for innovative, energy-efficient and smaller, less invasive medical devices surges, so does the need for specialized PCBs. Consequently, today’s medical PCB industry is evolving to accommodate these trends by utilizing HDI technology which allows these smaller but denser boards to signal high speed connectivity. To satisfy increasingly strict design criteria, many manufacturers are now utilizing non-traditional form factors. This may require flex, rigid flex or semi-flex constructions that enable three-dimensional configuration choices. Combined with these advanced technologies are demands for features like low power consumption and high-speed signal transmission making medical PCBs one of the more difficult applications for the PCB supplier. Such solutions can be pricier but guarantee reliable performance even in the most arduous of conditions.
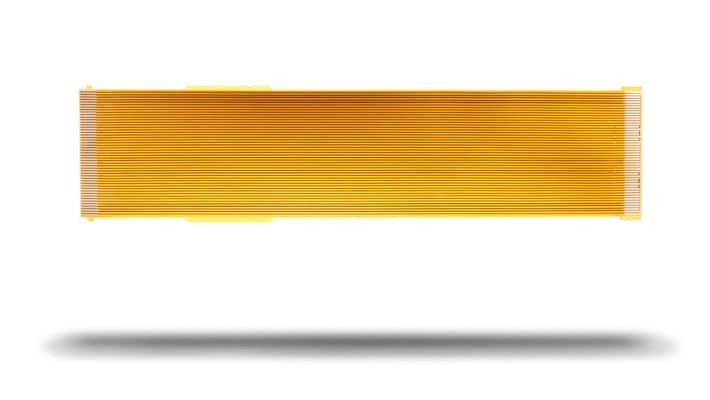
In order to promote reliable communication between these systems, the medical PCB industry has adopted the Internet of Things (IoT). Utilizing multiple data signals for optimum signal strength and increased efficacy is just one advantage of this technology. Moreover, it facilitates a stronger link between different pieces within a device or system, allowing you to maximize its potential. Medical electronics are always evolving which puts a dynamic demand on the bare PCBs. As devices are getting smaller, denser, and more intelligent, board manufacturers are working hard to create smaller and more complex boards that are equipped with sophisticated features yet still offer reliable performance. This trend is expected to remain for the coming years as medical technology continues to grow.
Challenges for the Medical Industry and Medical PCBs
The medical industry is highly regulated and requires adherence to stringent standards to ensure that medical devices produced are safe and effective. Patient safety is a paramount concern in this application and as such a large demand for safety, consistency and reliability is placed on the PCB.
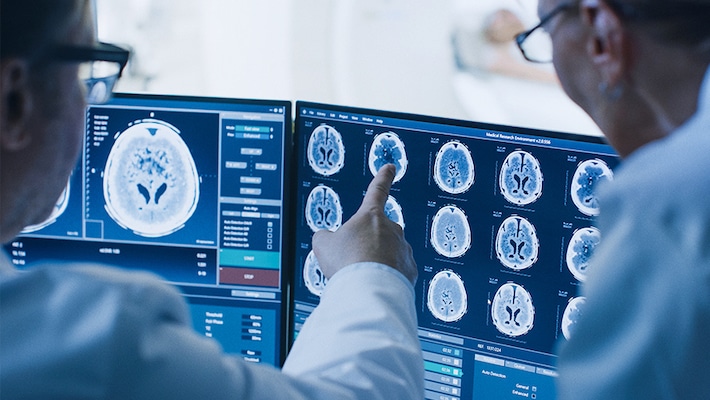
This presents a variety of challenges, particularly when it comes to the PCB supplier. In order to meet these regulations and demands, manufacturers must consider factors such as method validation, facility approval, part limitations and high production costs.
- Method Validation: The process used to manufacture medical PCBs must be validated for accuracy and safety. This includes validating the temperature, humidity, and pressure of the manufacturing environment, ensuring proper parameters are met during each step of the production process, and subjecting final assemblies to various tests. Manufacturers must document their processes thoroughly in order to pass regulatory inspections.
- Facility Approval: Medical device manufacturers must also obtain approval from regulatory bodies before producing any products for sale. This includes ensuring that all equipment is properly maintained and calibrated, they have an adequate quality control plan in place, and provide evidence of conformance with applicable standards. As part of this approval process, facilities must also be periodically inspected to ensure they are still in compliance.
- Part Limitations: Inherent limitations exist when it comes to medical PCBs due to their size and complexity. For example, parts may need to be extremely small or densely packed together, which can create difficulties in terms of reliability and fabrication. Additionally, certain materials used such as copper and silver may not be suitable for use in some applications due to their cost or reactivity with other materials. On top of all this, manufacturers must also consider the impact of electromagnetic interference (EMI) on the performance of their products.
- High Production Costs: Producing medical PCBs is an expensive endeavor as manufacturers must purchase high-end equipment and material, follow specific processes, and comply with a variety of regulations. Due to the complexity of medical PCBs and their need for high levels of accuracy, manufacturers must dedicate more resources to quality control measures such as testing and inspection.
Key Factors to Consider When Designing and Producing a Medical PCB
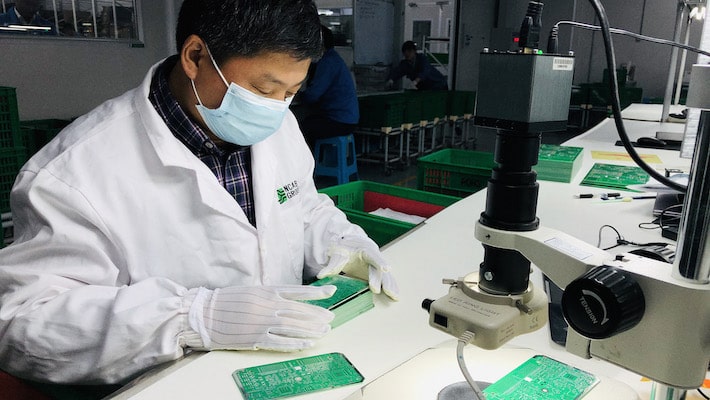
When designing medical PCBs, there are several key factors to consider to ensure it is safe. In addition, manufacturing medical PCBs requires careful attention to detail and strict adherence to quality standards to ensure that the resulting devices are reliable and effective. Here are some critical considerations when designing manufacturing medical PCBs:
- Signal integrity is also important for medical PCBs, as electrical signals must remain clear from noise and interference while traveling along the traces. It is essential to ensure that the PCB layout and routing selection follow best practices to minimize any unwanted noise on traces.
- EMI/EMC compliance must be taken into account, as electrical interference can affect not only the operation of the device but also other nearby devices or systems.
- Power consumption is also a key factor to consider when designing a medical PCB, as some devices may require very low power levels for portability or battery operation. It is essential to ensure that the board layout does not impede any power efficiency gains, and that all materials chosen minimize energy needs without compromising performance.
- DfM design for manufacturability must be considered, as medical boards need to meet strict standards for precision and quality typically part of an IPC 6012 Class 3 build. DfM is critical to ensuring the design and the supplier are compatible at the most stringent aspects of the design.
- High reliability is of primary importance for medical PCBs, as failure of a medical device could potentially put lives at risk. Parts should be selected that can withstand the intended operating environment, including temperature fluctuations and humidity levels, to minimize premature degradation or failure.
- Quality Control is critical for medical PCBs to ensure that they meet the required standards and specifications. The manufacturing process must be closely monitored and controlled to ensure that the PCBs are manufactured to the required tolerances, dimensions, and electrical properties.
- Traceability — medical device manufacturers must be able to trace every component of the device, including the PCB, from the supplier to the finished product. This requires strict adherence to traceability protocols, including component tracking, lot tracking, and serial number assignment. Medical device manufacturers must also maintain comprehensive documentation and records of the manufacturing process, including material traceability, testing results, and validation reports.
- Material Selection — the materials used in medical PCBs must be carefully selected to ensure that they are compatible with the device’s intended use, sterilization method, and regulatory requirements. The materials used must also be free from contaminants and impurities that could impact the device’s safety and efficacy. The type of material used in a medical PCB is also critical for safety and reliability. Materials should be carefully selected for their properties, durability and flame retardancy (as appropriate) and must be UL approved.
- Environmental Controls — the manufacturing environment must be carefully controlled to ensure that the PCBs are manufactured in a clean and controlled environment free from contaminants and particles that could impact their performance or safety.
- Testing and Validation: Medical PCBs must be tested and validated to ensure that they meet the required standards and specifications. This includes testing for electrical performance, environmental performance, and compatibility with the device’s other components.
Standards that Medical PCBs Must Meet
Medical PCBs (Printed Circuit Boards) are essential components in many medical devices and must meet strict standards in order to ensure the safety, quality, reliability, and security of these products. These standards regulate how a manufacturer designs and builds a medical device’s PCB assembly.
All medical PCBs must also meet UL certification standards in order for them to be used in medical device. These standards involve the testing of various electrical and mechanical parameters, such as temperature rise, dielectric strength, resistance to fire, etc. Meeting these standards ensures that the PCBs are safe for use in medical devices and will not cause any harm to patients or technicians.
The PCB fabricator may also have certification from ISO for the quality management system. ISO 13485 is a medical-specific quality management system in conjunction with ISO 9001 certification specifically geared towards medical device manufacturers that fabricators.
Key considerations from your PCB supplier
When building a medical product, your PCB supplier must understand the importance of delivering nothing but superior quality and reliability when it comes to PCBs. Knowledgeable engineers and technicians should incorporate a thorough methodology comprising designing, manufacturing, testing and documentation while producing your medical PCBs.
First, your supplier should undertake a comprehensive analysis of your PCB project parameters. They must ascertain that all parts are compatible with the chosen materials and that signal reliability is ensured for any high-speed designs. Moreover, factors in environmental conditions such as temperature extremes and humidity when selecting appropriate material for each layer during fabrication.
Once the design is endorsed, it’s time to kick off prototyping and testing. To ensure quality product, prototypes are often built in the same facility as production batches.
After prototyping, a pre-production batch is made, often times for end product certification. This batch typically does not allow changes from the initial batch and is required to be built in the same manner and facility as the final production.
And finally, after pre-production then volume production can begin. It is good practice for your supplier to implement quality checks during, and post-production, to ensure a high-quality finished product. A first article report detailing the quality of the build should be included with every batch as evidence of quality. At NCAB, we put quality and safety first. Our comprehensive approach ensures your product is designed, manufactured, and tested to the highest standards so you can have peace of mind that your medical device is compliant and reliable.
NCAB produce PCBs for several medical applications
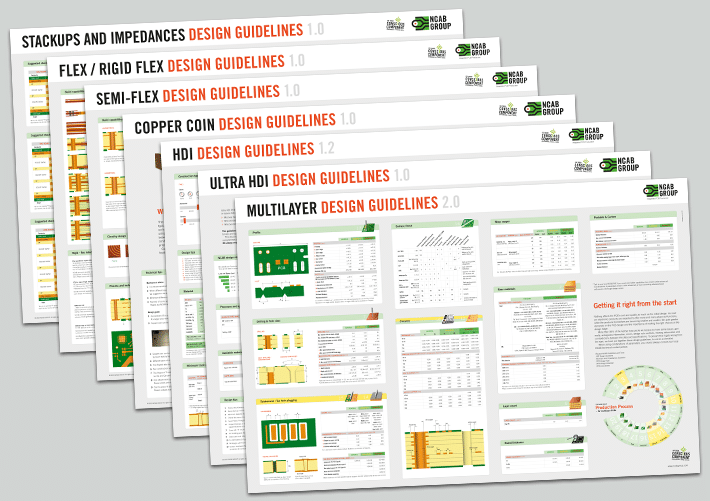
PCB design guidelines
Get it right from the start with our PCB design guidelines. To prevent getting it wrong from the start, we have put together our design guidelines, to use as a checklist.