Alimentati dall’elettricità anziché dai combustibili fossili, i veicoli elettrici (EV) stanno rivoluzionando e plasmando il nostro modo di viaggiare. L’impatto positivo che l’utilizzo di veicoli elettrici può avere sull’ambiente è vincolato alla diffusione di sistemi di ricarica efficienti. In questo articolo vi parleremo dei circuiti stampati per i sistemi di ricarica dei veicoli elettrici. Spiegheremo quali sono le tendenze, le considerazioni sulla progettazione e il valore aggiunto fornito da NCAB.
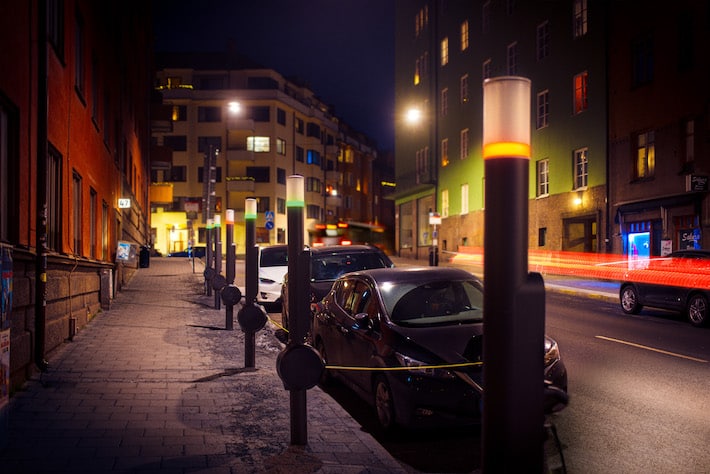
I circuiti stampati (PCB) sono componenti cruciali dei sistemi EVC e svolgono un ruolo fondamentale nel conferire all’infrastruttura di ricarica affidabilità, efficienza e sicurezza. Dalla gestione della distribuzione dell’energia al contributo all’infrastruttura del progetto, i PCB per la ricarica dei veicoli elettrici sono fondamentali per garantire capacità di ricarica affidabili e ad alta potenza. In questa guida non ci limiteremo a sottolineare il ruolo fondamentale dei circuiti stampati per le colonnine di ricarica elettrica, ma parleremo anche delle tendenze attuali, di come progettare i PCB per EVC, dei diversi tipi di EVC e del valore aggiunto che noi, come azienda, offriamo ai nostri clienti.
Tendenze attuali nell’industria dei circuiti stampati per veicoli elettrici
Tendenza alla miniaturizzazione degli EVC
In un settore in rapida crescita caratterizzato da enormi progressi tecnologici, le colonnine di ricarica elettrica non solo sono diventate più complesse, ma si sono anche modificate nelle dimensioni e nel design, diventando più compatte e leggere. Con l’evolversi degli EVC, anche noi produttori di pcb dobbiamo sviluppare e fare evolvere la nostra tecnologia e la progettazione.
Con la produzione di EVC sempre più complessi e di dimensioni ridotte, abbiamo dovuto trovare il modo di ottimizzare lo spazio limitato a disposizione. Ciò significa, quindi:
- Una maggiore densità e un maggior numero di strati nel circuito stampato: questo consente di disporre di un maggior numero di funzioni, necessarie per supportare lo sviluppo di un prodotto elettronico.
- Materiali più sottili (PP/CCL).
- Meno spazio per i connettori, ingombro totale.
- Microvias laser/vias interrati volti ad aumentare il numero di interconnessioni (HDI).
- Componenti di dimensioni inferiori.
In generale, con prodotti sempre più complessi che seguono la tendenza alla miniaturizzazione, anche noi dobbiamo seguire questa tendenza, il che significa chiedere di più alle nostre fabbriche.
Ricarica ad alta velocità
Un’altra tendenza evidente nel settore EVC riguarda la velocità di ricarica del veicolo. Con la crescente richiesta di tempi di ricarica più rapidi, anche la tecnologia dei PCB si sta evolvendo per supportare operazioni di ricarica ad alta potenza efficienti e affidabili.
I PCB utilizzati nei sistemi di ricarica ad alta velocità devono gestire correnti e tensioni più elevate. Ciò comporta, per esempio, attenzione alla scelta dei materiali e dello spessore di rame ai fini della conduzione di corrente e della dissipazione del calore in eccesso.
Un altro fattore da tenere in considerazione è la progettazione dei circuiti stampati per colonnine di ricarica ad alta velocità. Per esempio, è importante essere certi che la larghezza del conduttore e la distanza di isolamento siano posizionate correttamente.
Integrazione con interfacce di facile utilizzo
Un notevole progresso tecnologico nell’ambito dei veicoli elettrici è l’integrazione di interfacce user-friendly volte a migliorare l’esperienza di ricarica. Queste interfacce comprendono funzioni come touchscreen, applicazioni mobili, lettori di schede RFID e controlli intuitivi, tutti progettati a favore dell’utente e migliorarne l’esperienza complessiva durante il processo di ricarica.
Cosa considerare per progettare un circuito stampato per colonnine di ricarica
Grazie alla collaborazione tra i nostri tecnici e le nostre fabbriche, possiamo avere un impatto positivo nei seguenti settori:
Design del circuito stampato
La ricarica dei veicoli elettrici richiede la progettazione di circuiti ad alta potenza.
I circuiti ad alta potenza sono caratterizzati da livelli di tensione o corrente significativamente maggiori rispetto a quelli utilizzati nei circuiti a bassa potenza. I progettisti hanno la responsabilità di garantire il funzionamento del circuito entro i parametri di tensione e corrente appropriati, incorporando anche misure di raffreddamento e sicurezza.
Quando si tratta di PCB ad alta potenza, in genere si segue uno dei due approcci seguenti: progettazione del layout o progettazione di riferimento. La progettazione del layout riguarda la disposizione dei componenti sul PCB, mentre i progetti di riferimento sono in genere creati tenendo conto di layout specifici. Il layout del circuito stampato deve essere realizzato meticolosamente per ospitare efficacemente i componenti ad alta potenza e ridurre al minimo la generazione di rumore.
Un altro fattore da considerare è il posizionamento dei componenti. Nel caso dell’alta potenza è possibile applicare alcune tecniche di posizionamento atte a ridurre la resistenza termica del circuito stampato.
Per ulteriori consigli sulla progettazione dei PCB, potete contattare il vostro ufficio locale o scaricare le nostre linee guida gratuite per la progettazione dei PCB.
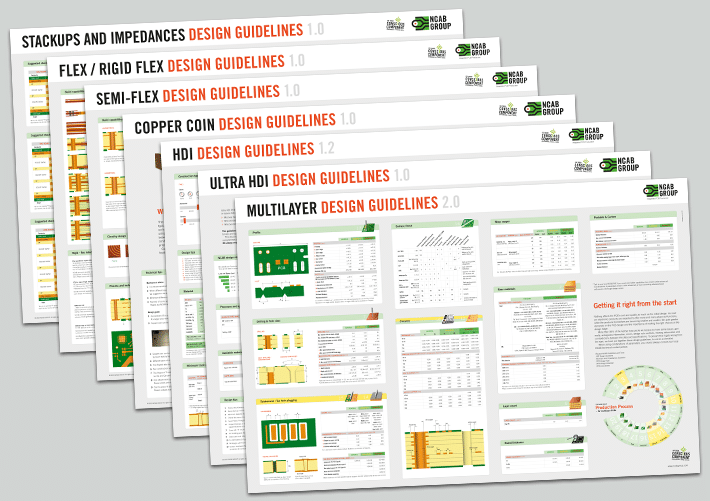
Regole di design per la progettazione di PCB
Per evitare di iniziare il lavoro con il piede sbagliato, abbiamo raccolto le nostre linee guida per la progettazione, da impiegare in una lista di controllo.
Spessore del Solder Mask
Il Solder Mask e il suo spessore sono un altro aspetto importante da considerare nella progettazione di EVC ad alta potenza.
L’elevato spessore di rame presente sugli strati esterni può comportare una maggiore deposizione di solder mask (per coprire il gap tra le piste). La fabbrica potrebbe applicare un doppio deposito di solder mask. Lo spessore del solder mask è un aspetto importante e il progettista dovrebbe valutare la scheda tecnica del materiale utilizzato (per esempio, la rigidità dielettrica e la resistenza superficiale). Le raccomandazioni IPC per il solder mask sono incluse nell’IPC-SM-840. Per impostazione predefinita, l’IPC suggerisce di utilizzare la Classe T per i circuiti di classe 2 e la Classe H per i circuiti di classe 3. Il solder mask non deve essere considerato come un “unico isolante”. Il progettista dovrebbe inoltre valutare l’impiego di un “conformal coating”.
Spessore di rame di potenza – spessori di rame inferiori
Con “Power Copper” si intende lo spessore di rame utilizzato per le tracce di alimentazione su un PCB. Nei sistemi di ricarica per veicoli elettrici, questi spessori svolgono un ruolo cruciale nel consentire una trasmissione di potenza efficiente e affidabile.
Il rame è un ottimo conduttore di calore (385 W/mK) e uno spessore maggiore di rame offre non solo una maggiore capacità di trasporto della corrente, ma permette anche di dissipare più calore.
Tuttavia, non dobbiamo pensare solo allo spessore del rame sulla superficie. Naturalmente, un deposito più spesso è fondamentale per la gestione termica, ma dobbiamo considerare anche la larghezza della traccia o dell’elemento poiché da questo parametro dipende la sezione trasversale e un suo aumento permetterà di incrementare così la quantità di calore che può essere dissipata attraverso la traccia di rame.
Di contro, il rame più spesso limita la possibilità di realizzare caratteristiche più fini sul circuito. Tuttavia, esiste una soluzione se il progetto richiede caratteristiche o componenti di piccole dimensioni.
Larghezza e spessore della traccia
Lo spessore delle tracce di rame è determinato dalla potenza che vi sarà applicata. Più alta è la potenza, più spessa deve essere la traccia.
I progettisti devono considerare lo spessore del rame e seguire la traccia e il gap minimi in base quello selezionato (tenendo presente che sussistono vincoli differenti per layer interni e layer esterni). Maggiore è lo spessore del rame necessario, maggiore è la larghezza della traccia da seguire. Per esempio, se per i layer esterni si vuole utilizzare uno spessore di rame di 3 oz (105µm), la larghezza minima della traccia dovrà essere 350µm, come da norma.
Sapevi che?
Le dimensioni e il numero di strati del PCB possono avere un forte impatto sulla sostenibilità? Se riusciamo a ridurre le dimensioni del PCB, possiamo anche minimizzare la quantità di materiali utilizzati, con conseguente riduzione dei rifiuti e dell’impatto ambientale.
Proprietà dei Laminati
Per ridurre la distanza di isolamento tra le tracce/aree di rame, si può prendere in considerazione un materiale con migliori proprietà CTI (Comparative Tracking Index).
Gli standard FR4.0 e FR4.1 soddisfano normalmente il PLC 3 (vedere la tabella seguente). È possibile utilizzare materiali migliori in grado di soddisfare il PLC 1 fino ad arrivare al PLC 0. È necessario tenere conto di fattori quali la disponibilità, i tempi di consegna e le approvazioni UL. Per informazioni più complete, contattare il tecnico NCAB locale.
Tracking Index (V) | PLC |
---|---|
600 e Greater | 0 |
400 a 599 | 1 |
250 a 399 | 2 |
175 a 249 | 3 |
100 a 174 | 4 |
< 100 | 5 |
In caso di temperatura elevata all’interno del dispositivo o sulla superficie delle schede, si possono prendere in considerazione anche materiali con una temperatura operativa massima (MOT) elevata. I circuiti stampati realizzati in FR4.0 e FR4.1 possono essere approvati da UL con una temperatura massima di 130°C, ma i circuiti stampati in FR15.0 e FR15.1 possono essere approvati con un minimo di 150°C.
Gestione termica
Poiché i componenti e l’aumento di potenza sono le cause principali del calore, la gestione termica è fondamentale per una progettazione affidabile dei sistemi di ricarica per veicoli elettrici, in quanto una temperatura eccessiva può contribuire a provocare guasti.
La gestione termica si riferisce ai metodi impiegati per trasferire il calore in eccesso nella misura desiderata dall’applicazione. Nel caso dei EVC e del PCB, l’obiettivo è quello di trasferire il calore in eccesso lontano dal componente, dissipando il calore all’interno del PCB o verso il lato opposto.
Sono possibili alcune soluzioni a questo problema, una delle quali è il layout:
- Posizionare i componenti che generano calore lontano dal bordo della scheda per contribuire a dissipare il calore in modo uniforme.
- Non raggruppare i componenti che generano calore, ma distribuirli nella scheda.
- Tenere i componenti che generano calore lontano dai componenti più piccoli e sensibili.
- Considerare i dissipatori di calore nelle prime fasi del processo.
- Ottimizzare il flusso d’aria dell’unità assemblata.
- Prevedere tracce più larghe per allontanare il calore e utilizzare fogli di rame più spessi sugli strati interni. Tenete presente, tuttavia, che con spessori di rame più alti il dimensionamento delle tracce può risultare problematico.
Sistemi AC & DC – due tipi di sistemi di ricarica per veicoli elettrici
I sistemi di ricarica AC (corrente alternata) e DC (corrente continua) sono due tipi di sistemi di ricarica utilizzati per i veicoli elettrici.
Quali sono le differenze tra una colonnina in AC e una in DC?
- I due sistemi di ricarica AC e DC si distinguono per il metodo di conversione dell’energia. A differenza dei sistemi AC, che convertono l’alimentazione all’interno del veicolo utilizzando il dispositivo di conversione di bordo, i sistemi di ricarica DC hanno il convertitore integrato nell’unità di ricarica. Di conseguenza, i sistemi di ricarica in DC possono fornire energia direttamente alla batteria dell’auto senza dover ricorrere al carica batterie di bordo per la conversione.
- I sistemi di ricarica AC sono progettati specificamente per funzionare con la corrente alternata, il tipo di elettricità tipicamente fornita dalle reti elettriche. I sistemi di ricarica in DC, invece, sono progettati per funzionare con la corrente continua, comunemente immagazzinata nelle batterie o generata dai pannelli solari.
- I sistemi di ricarica in AC si trovano comunemente in vari luoghi, come case, luoghi di lavoro, parcheggi e stazioni di ricarica pubbliche. I sistemi di ricarica in DC, invece, si trovano tipicamente nelle stazioni di ricarica pubbliche lungo le autostrade, le strade principali e le aree urbane, per i viaggi a lunga distanza e per le ricariche rapide.
- La carica in DC viene utilizzata per la ricarica rapida, mentre i sistemi di ricarica in AC offrono livelli di potenza più bassi che comportano tempi di ricarica più lunghi.
- I sistemi di ricarica in AC offrono in genere potenze di ricarica che vanno da 3,7 kW a 22 kW, a seconda del modello specifico e della capacità del caricatore di bordo del veicolo elettrico. I sistemi di ricarica DC possono fornire velocità di ricarica ad alta potenza, da 50 kW a diverse centinaia di kilowatt, consentendo una ricarica rapida e riducendo il tempo necessario per ricaricare la batteria di un veicolo elettrico.
- In generale, i sistemi di ricarica in DC utilizzano tensioni più elevate – I sistemi di ricarica in DC adottano sempre più spesso livelli di tensione più elevati per consentire una ricarica più rapida. L’uso di tensioni più elevate, come 400V, 800V o superiori, riduce i tempi di ricarica consentendo il passaggio di correnti più elevate nella batteria del veicolo elettrico. La ricarica a tensione più elevata comporta anche una riduzione delle perdite e un trasferimento di energia più efficiente. Vale la pena notare che nuove indagini hanno dimostrato che le alte tensioni in un circuito stampato possono creare gravi danni nel tempo; questo accade quando il circuito stampato stesso presenta tracce con tensioni superiori a 500V. Nell’ambito della ricarica dei veicoli elettrici, le prestazioni di alte correnti e tensioni sono rilevanti per la progettazione della potenza. È quindi importante garantire che la progettazione segua i requisiti di sicurezza, quali:
- Spaziatura tra i vias circa 5 mm
- Spaziatura tra copper to copper/track to track. È raccomandato
- 48V = 1 – 1,5 mm
- 110V = 3 mm
- 220V = 6 – 8 mm
- 480V = 16mm
- Copper to edge (circa 5 mm)
- Un’altra differenza tra i due modelli è il costo: i sistemi di ricarica in AC sono generalmente più economici di quelli in DC.
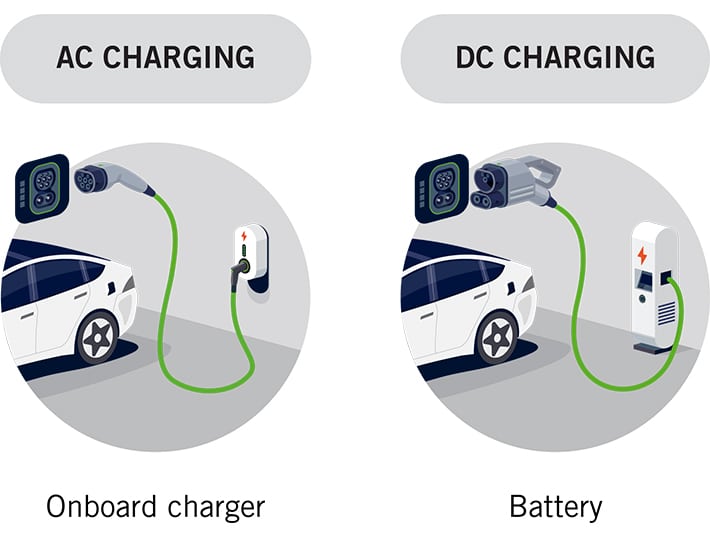
Standard che i PCB per EVC devono soddisfare
Lo standard per i connettori o le prese di ricarica dei veicoli elettrici varia a seconda delle regioni e dei modelli di veicoli. Sebbene non sia stata concordata una tecnologia universale per le prese, un numero significativo di case automobilistiche mondiali sostiene il sistema di ricarica combinato (CCS) in Nord America e in Europa.
Nonostante l’esistenza di standard diversi, c’è un crescente consenso in varie regioni per promuovere l’adozione di standard EV armonizzati a livello mondiale. Inoltre, esistono importanti norme e regolamenti globali per i veicoli elettrici, come la IEC 61851, che riguarda le modalità di ricarica, i connettori e la sicurezza elettrica. Un altro standard è l’ISO 15118, che si concentra sulla comunicazione tra veicoli elettrici e infrastrutture di ricarica. È essenziale ricordare che le normative e gli standard specifici possono variare a seconda dei Paesi e delle regioni.
Quale valore aggiunto fornisce NCAB per ?
Controllo qualità e supporto tecnico – Il nostro obiettivo è controllare la qualità durante l’intero processo di produzione dei PCB. La progettazione iniziale del PCB influisce molto sul costo totale e sull’affidabilità del circuito stampato, tutti gli uffici locali di NCAB includono specialisti dedicati che lavorano con voi per comprendere le vostre esigenze e quelle del prodotto. I nostri team di supporto alla progettazione sono in grado di fornire consulenze di valore sulle strategie di design. Il loro scopo è quello di aiutarvi a realizzare il miglior progetto possibile, per una produzione di PCB economicamente vantaggiosa, dai prototipi alla produzione in serie. Nelle fabbriche sono presenti i nostri team di gestione della produzione, che lavorano direttamente sulle linee. I nostri ingegneri della qualità sono direttamente responsabili delle prestazioni delle linee produttive, nonché della creazione di relazioni e della collaborazione proattiva con loro per ottenere miglioramenti.
La sostenibilità ha un ruolo chiave nel nostro modo di pensare e di agire. Quando lavorate con noi, mettiamo in luce i vari aspetti da considerare nel circuito stampato (dal design, alla produzione alla consegna) che possono avere un impatto positivo in termini di sostenibilità. Il nostro strumento per valutare i fattori di costo di un pcb vi permetterà di conoscere i diversi elementi che contribuiscono al costo finale di un circuito stampato, evidenziando anche come è possibile lavorare sull’impatto dei pcb sulla sostenibilità.
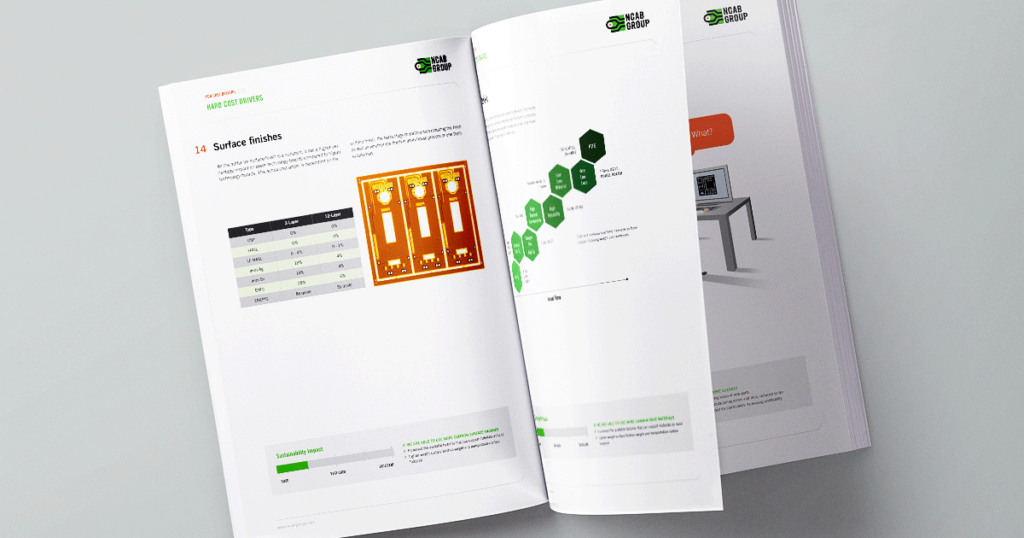
Strumenti di progettazione – per PCB affidabili
Quali fattori determinano il costo di un circuito stampato?
Che impatto hanno questi fattori sulla sostenibilità? Abbiamo sviluppato uno strumento per aiutarti a ridurre i costi nella produzione di PCB.
Supporto locale – Con una presenza globale e una vasta rete di uffici e rappresentanti locali, offriamo assistenza e competenze personalizzate in varie regioni. Grazie al nostro supporto locale, garantiamo una comunicazione chiara ed efficiente. I nostri team di esperti conoscono i requisiti e le sfide specifiche di ciascun mercato, sono in grado di fornire soluzioni su misura e indicazioni preziose durante l’intero processo di produzione dei circuiti stampati.
Le principali specifiche per l’affidabilità – Abbiamo una nostra specifica che viene utilizzata per tutti i PCB che forniamo ai clienti. Alcune caratteristiche di questa specifica, sono uniche di NCAB e/o vanno oltre lo standard IPC Classe 2. Questo è uno dei fattori che ci permette di fornire prodotti più affidabili rispetto a molti concorrenti.
Poiché i veicoli elettrici continuano a rivoluzionare il settore dei trasporti, l’importanza dell’infrastruttura di ricarica dei veicoli elettrici diventa fondamentale. I PCB svolgono un ruolo cruciale nel garantire l’efficienza, l’affidabilità e la sicurezza dei sistemi EVC.
Poiché il settore delle colonnine di ricarica elettrica continua ad evolversi, anche noi dobbiamo adattarci e imparare, in modo da poter fornire soluzioni innovative e un’assistenza completa per soddisfare la continua evoluzione del mercato.