Elektrofahrzeuge, die mit Strom statt mit fossilen Brennstoffen angetrieben werden, revolutionieren und prägen unsere Art der Fortbewegung. Aber was nützen Elektrofahrzeuge und ihre geringeren Umweltauswirkungen, wenn man sie nicht aufladen kann? Erfahren Sie mehr über Leiterplatten für das Laden von Elektrofahrzeugen – die Trends, Designüberlegungen und den Mehrwert der NCAB.
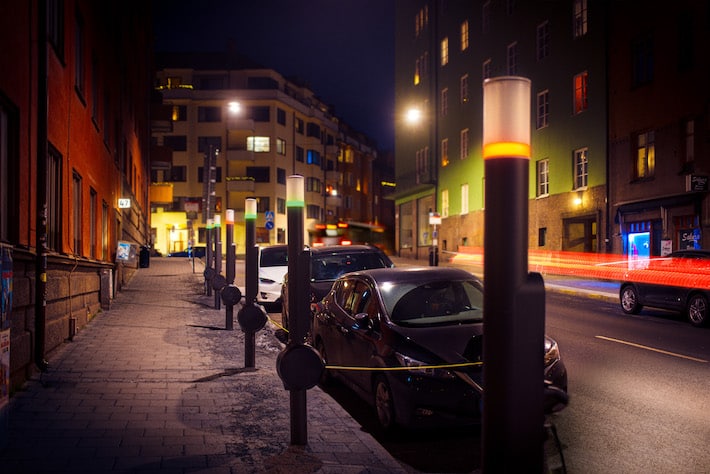
Leiterplatten (Printed Circuit Boards, PCBs) sind zentrale Komponenten in EVC-Systemen und spielen eine Schlüsselrolle bei der Gewährleistung der Zuverlässigkeit, Effizienz und Sicherheit der Ladeinfrastruktur. Von der Verwaltung der Stromverteilung bis hin zum Beitrag zur Designinfrastruktur sind Leiterplatten entscheidend für die Gewährleistung zuverlässiger und leistungsstarker Ladesysteme. In diesem Leitfaden werden wir nicht nur die zentrale Rolle von EVC-Leiterplatten hervorheben, sondern auch aktuelle Trends, das Design von Leiterplatten für EVC, die verschiedenen Arten von EVC und den Mehrwert, den wir als Unternehmen unseren Kunden bieten, beleuchten.
Aktuelle Trends in der Leiterplattenindustrie für Elektrofahrzeuge
Der Trend zur Miniaturisierung bei EVC, insbesondere bei Level-2-Ladegeräten
Mit einer schnell wachsenden Industrie und großen technologischen Entwicklungssprüngen sind EVCs nicht nur komplexer geworden, sondern auch ihre Größe und ihr Design haben sich verändert – sie sind nicht nur kompakter, sondern auch leichter geworden. Und da sich EVCs weiterentwickeln, müssen auch wir unsere Leiterplattentechnologie und -designs weiterentwickeln. Da immer komplexere und kleinere EVCs hergestellt werden, mussten wir Wege finden, den begrenzten Platz, der zur Verfügung steht, zu nutzen. Das wiederum bedeutet:
- Höhere Schaltungsdichte und mehr Lagen auf der Leiterplatte – dies erhöht die Funktionsdichte der Baugruppe und ist notwendig, um die Weiterentwicklung elektronischer Produkte zu ermöglichen.
- Dünnere Materialien (PP/CCL).
- Weniger Platz für Steckverbinder und 3D-Montage.
- PTH ist nicht ausreichend, so dass wir lasergebohrte Microvias und buried Vias benötigen, die kleiner sind und ausgesuchte Lagen untereinander verbinden, anstatt durch die gesamte Leiterplatte zu gehen. Dies wiederum erhöht die Anzahl der einzelnen Unterverbindungen.
- Kleinere Komponenten und kleinere Strukturen.
Angesichts immer komplexerer Produkte, die dem Trend zur Miniaturisierung folgen, müssen auch wir diesem Trend folgen, was höhere Anforderungen an die Fabriken bedeutet.
Schnellladen
Ein weiterer auffälliger Trend bei EVC betrifft die Geschwindigkeit, mit der das Fahrzeug geladen wird. Mit der steigenden Nachfrage nach kürzeren Ladezeiten entwickelt sich auch die Leiterplattentechnologie weiter, um effiziente und zuverlässige Hochleistungsladevorgänge zu unterstützen.
Leiterplatten, die in Schnellladesystemen eingesetzt werden, müssen höhere Ströme und Spannungen verarbeiten können. Dazu gehört neben anderen Faktoren auch die Auswahl bestimmter Materialien und der Einsatz von viel Kupfer, um sowohl den Strom zu leiten als auch überschüssige Wärme abzuführen.
Das Design der Schnellladesystemen-Leiterplatte ist ein weiterer Faktor, der in Betracht gezogen werden sollte. So muss beispielsweise sichergestellt werden, dass die Leiterbreite und der Isolationsabstand richtig gewählt werden.
Integration von erneuerbaren Energien
Im Sinne der Nachhaltigkeit und der Verringerung des CO2-Fußabdrucks von Elektrofahrzeugen ist die Integration des EVC-Systems mit erneuerbaren Energiequellen wie Sonnenkollektoren, Windenergie und dem Stromnetz ein weiterer Trend im Bereich EVC. So können Sie beispielsweise Sonnenkollektoren auf Ihrem eigenen Grundstück installieren, um Energie in einer Batterie zu speichern, die später bei hohen Strompreisen genutzt werden kann.
Verbesserte benutzerfreundliche Schnittstellen
Ein bedeutender technologischer Fortschritt im Bereich der Elektromobilität ist die Integration von benutzerfreundlichen Schnittstellen, die das Ladeerlebnis verbessern sollen. Diese Schnittstellen umfassen Funktionen wie Touchscreens, mobile Apps, RFID-Kartenleser und intuitive Bedienelemente, die den Komfort und das Gesamterlebnis während des Ladevorgangs verbessern sollen.
Wichtige Faktoren, die bei der Entwicklung und Herstellung einer Leiterplatte für Ladegeräte für Elektrofahrzeuge zu berücksichtigen sind
Durch die Zusammenarbeit mit unseren Technikern und unseren Fabriken erzielen wir positive Auswirkungen in den folgenden Bereichen:
Leiterplattendesign
Das Laden von Elektrofahrzeugen ist ein Anwendungsgebiet, welches das Design von Hochleistungsschaltkreisen erfordert.
Hochleistungsschaltungen zeichnen sich dadurch aus, dass sie im Vergleich zu Standardschaltungen wesentlich höheren Spannungs- oder Stromwerten standhalten müssen. Die Entwickler tragen die Verantwortung dafür, dass die Schaltung innerhalb der entsprechenden Spannungs- und Stromparameter funktioniert und gleichzeitig angemessene Kühlungs- und Sicherheitsmaßnahmen berücksichtigt werden.
Bei Hochleistungs-Leiterplatten wird in der Regel einer der folgenden beiden Designansätze verfolgt: Layoutdesign oder Referenzdesign. Das Layoutdesign beschreibt die Anordnung der Komponenten auf der Leiterplatte, während Referenzdesigns in der Regel unter Berücksichtigung bestimmter Layouts erstellt werden. Das Layout der Leiterplatte muss sorgfältig ausgearbeitet werden, um Hochleistungskomponenten effektiv unterzubringen und die Entstehung von Störungen zu minimieren.
Ein weiterer wichtiger Punkt ist die Anordnung der Komponenten. Die Verwendung von Hochleistungskomponenten erfordert bestimmte Designmethoden, um den Wärmewiderstand der Leiterplatte zu minimieren.
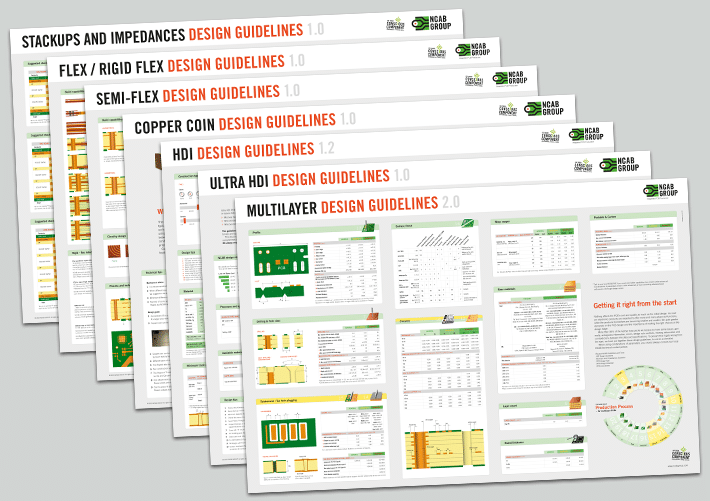
Design Rules für Leiterplatten
Um Fehler im PCB-Design von Anfang an zu vermeiden, haben wir unsere Design Rules in Form einer Checkliste zusammengestellt.
Lötstoppmaskendicke
Die Lötstoppmaske und ihre Dicke sind ein weiterer wichtiger Aspekt, der bei der Entwicklung von EVCs mit hoher Leistungsabgabe zu berücksichtigen sind. Eine hohe Kupferstärke auf den Außenlagen kann dazu führen, dass eine höhere Lötstoppmaskenstärke erforderlich ist (um die „Lücken” zwischen den Leiterbahnen zu schließen). Die Fabrik könnte eine Doppelschicht der Lötstoppmaske auftragen.
Die Dicke der Lötstoppmaske ist wichtig, und der Entwickler sollte auch das Datenblatt der verwendeten Lötstoppmaske prüfen (z. B. die Durchschlagfestigkeit, den Oberflächenwiderstand). Die IPC-Empfehlungen für Lötmasken sind in der IPC-SM-840 enthalten. Standardmäßig empfiehlt die IPC die Verwendung von Klasse T für Schaltungen der Leistungsklasse 2 und Klasse H für Schaltungen der Leistungsklasse 3. Die Lötstoppmaske sollte nicht als „einzige Isolierung“ betrachtet werden. Ferner sollte der Entwickler auch eine Schutzlackierung in Betracht ziehen.
Hochleistungskupferstärken – niedrigere Kupferstärken
Mit Hochleistungskupferstärken wird die Dicke oder Menge des Kupfers bezeichnet, das für Leiterbahnen auf einer Leiterplatte verwendet wird. In Ladevorrichtungen für Elektrofahrzeuge spielen Hochleistungskupferstärken eine entscheidende Rolle für eine effiziente und zuverlässige Stromübertragung.
Kupfer ist ein sehr guter Wärmeleiter (385 W/mK). Eine größere Kupferdicke bietet folglich nicht nur eine höhere Strombelastbarkeit, sondern ermöglicht auch eine bessere Wärmeableitung.
Wir müssen jedoch nicht nur an die Dicke der Kupferschicht auf der Oberfläche denken. Natürlich ist eine dickere Schicht der Schlüssel zum Thermomanagement, aber wir müssen auch die Breite der Leiterbahn oder des Kupferstruktur berücksichtigen, da dies zu einer Vergrößerung der Querschnittsfläche führt und somit die Wärmemenge erhöht, die über die Kupferleiter abgeleitet werden kann.
Dickeres Kupfer schränkt die Möglichkeit ein, feinere Merkmale in den Schaltungen zu verwenden. Es gibt jedoch eine Lösung, wenn das Design kleine Strukturen oder Elemente erfordert.
Leiterbahnbreite- und dicke
Die Dicke der Leiterbahnen hängt von der Leistung ab, die an sie angelegt wird. Je höher die Leistung, desto dicker müssen die Leiterbahnen sein.
Die Entwickler sollten die Dicke der Kupferfolie berücksichtigen und die Mindestbreite der Leiterbahn und den Mindestabstand entsprechend der gewählten Kupferdicke einhalten (es ist wichtig zu prüfen, ob die Leiterbahnen auf inneren oder äußeren Lagen verlaufen sollen). Je dicker die benötigte Kupferstärke ist, desto dickere Leiterbahnen werden verwendet. Wenn Sie z.B. 3 oz = 105 µm Kupferdicke (Außenlage) verwenden wollen, muss die Mindestbreite der Leiterbahnen auf den Außenlagen im Regelfall ≥ 350µm sein.
Wussten Sie schon?
Die Größe und Lagenzahl einer Leiterplatte können einen großen Einfluss auf die Nachhaltigkeit haben. Wenn wir Leiterplattengröße reduzieren können, können wir auch die Menge der verwendeten Materialien verringern, was zu weniger Abfall und Umweltbelastung führt.
Materialeigenschaften
Um den Isolationsabstand zwischen Kupferbahnen/Kupferbereichen zu verringern, kann Material mit besseren CTI-Eigenschaften (Comparative Tracking Index) in Betracht gezogen werden.
Standard FR4.0 & FR4.1 erfüllen normalerweise PLC 3 (siehe Tabelle unten). Es können auch bessere Materialien verwendet werden, die sowohl PLC 1 als auch PLC 0 erfüllen. Dabei müssen Faktoren wie Verfügbarkeit, Vorlaufzeit und UL-Zulassungen berücksichtigt werden. Bitte wenden Sie sich an Ihren NCAB-Techniker vor Ort, um weitere Informationen zu erhalten.
Tracking Index (V) | PLC |
---|---|
≥ 600 | 0 |
400 bis 599 | 1 |
250 bis 399 | 2 |
175 bis 249 | 3 |
100 bis 174 | 4 |
< 100 | 5 |
Materialien mit einer hohen maximalen Betriebstemperatur (MOT) können ebenfalls in Betracht gezogen werden, wenn die Temperatur im Inneren des Gehäuses oder auf der Oberfläche der Leiterplatte hoch ist. Leiterplatten aus FR4.0 und FR4.1 können von UL mit einer maximalen Betriebstemperatur von 130°C zugelassen werden, Leiterplatten aus FR15.0 und FR15.1 können jedoch bis mindestens 150°C zugelassen werden.
Thermomanagement
Da die Bauteile und der erhöhte Strombedarf zwei Hauptursachen für die Wärmeentwicklung sind, ist das Wärmemanagement für die zuverlässige Konstruktion von Ladestationen von entscheidender Bedeutung, da übermäßige Temperaturen zu Ausfällen führen können.
Das Thermomanagement bezieht sich auf die Methoden, die eingesetzt werden, um überschüssige Wärme von einem Ort zum anderen zu übertragen. Im Fall von EVCs und der Leiterplatte liegt unser Schwerpunkt darauf, die überschüssige Wärme von der Komponente wegzuleiten, indem die Wärme entweder in oder durch die Leiterplatte von einer Seite zur anderen abgeleitet wird.
Hierfür gibt es mehrere Ansätze, einer davon ist das Layout:
- Platzieren Sie wärmeentwickelnde Bauteile nicht am Rand der Platine, um die Wärme gleichmäßig zu verteilen.
- Gruppieren Sie wärmeentwickelnde Bauteile nicht zusammen, sondern verteilen Sie sie.
- Halten Sie wärmeentwickelnde Bauteile von kleineren, empfindlicheren Bauteilen fern.
- Ziehen Sie Kühlkörper schon früh im Designprozess in Betracht.
- Optimieren Sie den Luftstrom im Gehäuse der Baugruppe.
- Sorgen Sie für breite Leiterbahnen, um die Wärme abzuführen, und verwenden Sie dicke Kupferfolien auf den Innenlagen. Bedenken Sie jedoch, dass bei hohen Kupferstärken Platz ein Problem werden kann.
AC-Ladegeräte und DC-Ladegeräte – zwei Arten von EV-Ladesystemen
AC- (Wechselstrom) und DC- (Gleichstrom) Ladegeräte sind zwei Arten von Ladesystemen, die für Elektrofahrzeuge verwendet werden.
Was sind die Unterschiede zwischen einer Wechselstrom- und einer Gleichstromladung?
- Wechselstrom-Ladegeräte und Gleichstrom-Ladegeräte unterscheiden sich durch den Ort der Stromumwandlung. Im Gegensatz zu Wechselstrom-Ladegeräten, bei denen die Umwandlung des Wechselstroms im Fahrzeug über das bordeigene Ladegerät erfolgt, ist bei Gleichstrom-Ladegeräten der Wandler in die Ladestation integriert. Folglich können Gleichstrom-Ladegeräte den Strom direkt in die Fahrzeugbatterie einspeisen, ohne dass die Umwandlung über das Bordladegerät erfolgen muss.
- AC-Ladegeräte sind speziell für den Betrieb mit Wechselstrom ausgelegt, der Art von Elektrizität, die normalerweise von Stromnetzen bereitgestellt wird. Im Gegensatz dazu sind DC-Ladegeräte für den Betrieb mit Gleichstrom ausgelegt, der in der Regel in Batterien gespeichert oder von Photovoltaikanlagen erzeugt wird.
- Wechselstrom-Ladegeräte sind in der Regel an verschiedenen Orten wie Wohnungen, Arbeitsplätzen, Parkplätzen und öffentlichen Ladestationen zu finden. Gleichstrom-Ladegeräte sind in der Regel an öffentlichen Ladestationen, entlang von Autobahnen, Hauptverkehrsstraßen und in städtischen Gebieten zu finden und eignen sich für Langstreckenfahrten und zum schnellen Aufladen.
- Gleichstrom-Ladegeräte werden für Schnellladungen verwendet, während Wechselstrom-Ladegeräte eine geringere Leistung bieten, was wiederum zu längeren Ladezeiten führt.
- Wechselstrom-Ladegeräte bieten in der Regel Ladeleistungen zwischen 3,7 kW und 22 kW, je nach Ladegerät und der Ladekapazität des Fahrzeugs. Gleichstrom-Ladegeräte bieten hohe Ladeleistungen von 50 kW bis zu mehreren hundert Kilowatt, was ein schnelles Aufladen ermöglicht und die für das Aufladen der Batterie eines E-Fahrzeugs erforderliche Zeit verkürzt.
- DC-Ladegeräte verwenden in der Regel höhere Spannungen. Die Verwendung höherer Spannungen, wie 400 V, 800 V oder höher, verkürzt die Ladezeit, da höhere Ströme in die Batterie des Fahrzeugs fließen können. Das Laden mit höherer Spannung führt auch zu geringeren Verlusten und einer effizienteren Energieübertragung.
- An dieser Stelle sei darauf hingewiesen, dass neue Untersuchungen gezeigt haben, dass hohe Spannungen in einer Leiterplatte im Laufe der Zeit schwere Schäden verursachen können; dies ist der Fall, wenn die Leiterplatte selbst Leiterbahnen mit Spannungen von über 500 V aufweist.
- Beim Laden von Elektrofahrzeugen ist die Belastbarkeit mit großen Strömen und hohen Spannungen wichtig für das Leistungsdesign. Daher muss sichergestellt werden, dass das Design den Sicherheitsanforderungen entspricht, wie z.B.:
- Abstand von Via zu Via (ca. 5 mm)
- Kupfer zu Kupfer / Leiterbahn zu Leiterbahn-Abstand. Empfehlungen:
- 48 V = 1 – 1,5 mm
- 110 V = 3 mm
- 220 V = 6 – 8 mm
- 480 V = 16 mm
- Abstand zwischen Kupfer und Rand (ca. 5 mm)
- Ein weiterer Unterschied zwischen den beiden ist der Preis: Wechselstrom-Ladegeräte sind in der Regel billiger als Gleichstrom-Ladegeräte.
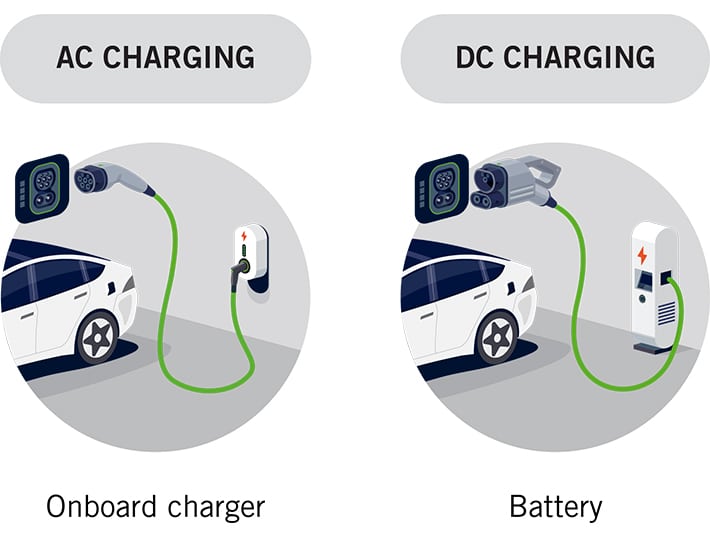
Standards, die EVC-Leiterplatten erfüllen müssen
Der Standard für Ladesteckvorrichtungen für Elektrofahrzeuge variiert je nach Region und Fahrzeugmodell. Obwohl man sich nicht auf eine universelle Steckertechnologie geeinigt hat, gibt es eine beträchtliche Anzahl globaler Automobilhersteller, die das Combined Charging System (CCS) in Nordamerika und Europa unterstützen.
Trotz der unterschiedlichen Standards gibt es einen wachsenden Konsens in verschiedenen Regionen, um die Umsetzung von harmonisierten EV-Standards weltweit zu fördern. Darüber hinaus gibt es bemerkenswerte globale Normen und Vorschriften für EVC, wie z. B. die IEC 61851, die sich mit Lademodi, Steckern und elektrischer Sicherheit befasst. Eine weitere Norm ist ISO 15118, die sich auf die Kommunikation zwischen Elektrofahrzeugen und der Ladeinfrastruktur konzentriert. Es ist wichtig zu wissen, dass die spezifischen Vorschriften und Normen in verschiedenen Ländern und Regionen unterschiedlich sein können.
Welchen Mehrwert können wir bei der NCAB bieten?
Qualitätskontrolle und technische Unterstützung – Unser Ziel ist es, die Qualität während des gesamten PCB-Prozesses zu kontrollieren. Das anfängliche Design der Leiterplatte hat einen großen Einfluss auf die Gesamtkosten und die Zuverlässigkeit der Leiterplatte. Alle lokalen NCAB-Niederlassungen verfügen über engagierte Spezialisten, die mit Ihnen zusammenarbeiten, um Ihre Anforderungen und die des Produkts zu verstehen. Unsere Design-Support-Teams können Sie bei wertsteigernden Initiativen beraten. Sie sollen Ihnen helfen, das bestmögliche Design oder Redesign für eine kosteneffiziente Leiterplattenproduktion von Prototypen bis hin zur Serienproduktion zu erreichen. In den Fabriken arbeiten unsere Factory Management Teams direkt vor Ort mit den Produktionsstätten zusammen. Unsere Qualitätsingenieure sind direkt für die Leistung der Fabriken verantwortlich, sie bauen Beziehungen auf und arbeiten proaktiv mit ihnen zusammen, um Verbesserungen zu erzielen.
Nachhaltigkeit – ist ein zentraler Bestandteil unserer Denk- und Handlungsweise. Wenn Sie mit uns zusammenarbeiten, beleuchten wir die verschiedenen Aspekte Ihrer Leiterplatte (vom Design über die Produktion bis hin zur Lieferung), die einen positiven Einfluss auf die Nachhaltigkeit haben können. In unserem PCB-Kostentreiber-Tool erfahren Sie mehr über die verschiedenen Faktoren, die die Kosten einer Leiterplatte beeinflussen, aber auch darüber, wie sich diese Faktoren wiederum auf die Nachhaltigkeit auswirken können…
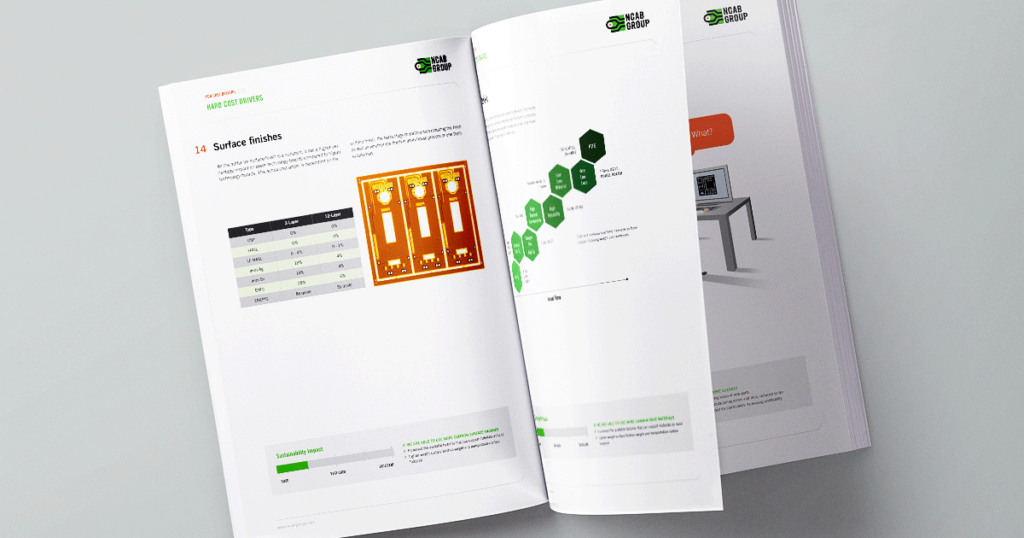
PCB-Kostentreiber
Was treibt die Kosten einer Leiterplatte in die Höhe?
Und wie wirken sich diese Faktoren wiederum auf die Nachhaltigkeit aus? Um große Kostentreiber zu vermeiden, haben wir ein Tool entwickelt, das Sie unterstützen kann.
Lokale Betreuung – Mit unserer globalen Präsenz und einem umfassenden Netz lokaler Büros und Repräsentanten bieten wir persönliche Unterstützung und Fachwissen in zahlreichen Regionen. Durch unseren lokalen Support stellen wir eine klare und effiziente Kommunikation sicher. Unsere sachkundigen Teams kennen die spezifischen Anforderungen und Herausforderungen der einzelnen Märkte und können so maßgeschneiderte Lösungen und wertvolle Hilfestellung während des gesamten Leiterplattenherstellungsprozesses bieten.
Wichtige Merkmale für die Zuverlässigkeit – Wir haben unsere eigene, maßgeschneiderte Leiterplattenspezifikation, die für alle Leiterplatten verwendet wird, die wir an unsere Kunden liefern. Mehrere wichtige spezifizierte Leiterplattenmerkmale sind einzigartig bei uns und/oder gehen über den Industriestandard IPC Klasse 2 hinaus. Dies ist einer der Faktoren, die es uns ermöglichen, ein zuverlässigeres Produkt als viele unserer Mitbewerber zu liefern.
Da Elektrofahrzeuge die Transportindustrie immer weiter revolutionieren, wird die Bedeutung der Ladeinfrastruktur für Elektrofahrzeuge immer größer. Leiterplatten spielen eine entscheidende Rolle bei der Gewährleistung der Effizienz, Zuverlässigkeit und Sicherheit von EVC-Systemen.
Da sich die EVC-Branche ständig weiterentwickelt, müssen auch wir uns anpassen und lernen, damit wir innovative Lösungen und umfassende Unterstützung anbieten können, um die sich entwickelnden Anforderungen des Marktes zu erfüllen.