Alimentés par l’électricité et non par des énergies fossiles, les véhicules électriques sont en train de révolutionner et de façonner notre mode de transport. Mais à quoi servent-ils si nous ne sommes pas en mesure de les recharger ? Découvrez nos circuits imprimés pour la recharge de véhicules électriques (EV Charger) – les tendances, les conseils en matière de conception et la valeur ajoutée de NCAB.
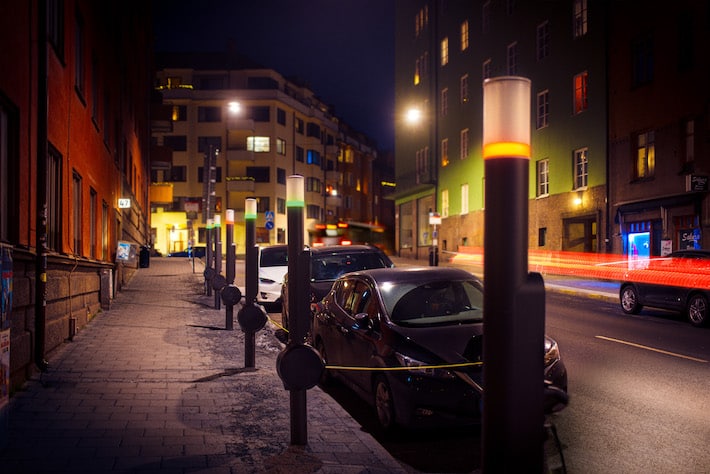
Les circuits imprimés (PCB) font partie des composants cruciaux des systèmes EV Charger jouant un rôle essentiel pour garantir la fiabilité, l’efficacité et la sécurité de la borne de recharge. Qu’il s’agisse de gérer la distribution de l’énergie ou de contribuer à la conception de l’infrastructure, ils sont essentiels pour garantir des capacités de charge fiables et de haute puissance. Dans ce guide, nous allons aborder les tendances actuelles, la conception des PCB destinés aux systèmes de charge électrique, les différents systèmes de charge électrique et la valeur ajoutée que nous apportons à nos clients en tant qu’entreprise.
Tendances actuelles dans l’industrie des circuits imprimés pour véhicules électriques
La tendance à la miniaturisation des EV Charger, en particulier des chargeurs de niveau 2
Avec une industrie en plein essor et des avancées technologiques considérables, les chargeurs de véhicules électriques sont non seulement devenus plus complexes, mais leur taille et leur conception ont également évolué – ils sont devenus plus compacts, mais aussi plus légers. Et comme les EV Charger évoluent, nous devons également développer et faire évoluer notre technologie ainsi que nos conceptions de circuits imprimés.
Cela se traduit par :
- Une densité plus élevée et un plus grand nombre de couches dans le circuit imprimé – cela fournit plus de conducteurs pour la fonction et est nécessaire pour aider au design des produits électroniques.
- Des matériaux plus fins (PP/CCL).
- Moins d’espace pour les connecteurs et les intégrations 3D.
- Des trous métallisés insuffisants. Nous avons besoin de microvia percés au laser et de via enterrés, plus petits, et qui connectent des couches sélectionnées au lieu de traverser l’ensemble du PCB. Cela permet d’augmenter le nombre d’interconnexions.
- Des composants plus petits.
Globalement, nous devons suivre la tendance à la miniaturisation, avec des produits de plus en plus complexes, impliquant des exigences accrues pour les usines.
Chargement rapide
Une autre tendance notable de l’EV Charger concerne la vitesse à laquelle le véhicule est rechargé. Avec la demande croissante de temps de charge plus rapides, la technologie des circuits imprimés évolue également pour permettre des opérations de charge à haute puissance efficaces et fiables.
Les circuits imprimés utilisés dans les systèmes de charge à grande vitesse doivent supporter des courants et des tensions plus élevés. Par exemple, il faut s’assurer que la largeur des conducteurs et les distances d’isolement sont correctement dimensionnées. Cela implique, entre autres considérations, l’utilisation de certains matériaux et d’une grande quantité de cuivre pour conduire le courant et dissiper l’excès de chaleur.
Intégration des énergies renouvelables
Suivant la voie de la durabilité et de la réduction de l’empreinte carbone associée aux véhicules électriques, l’intégration du système EV Charger avec des sources d’énergie renouvelables telles que les panneaux solaires, l’énergie éolienne, ainsi que le réseau électrique, est une autre tendance. Par exemple, vous pouvez installer des panneaux solaires sur votre propriété pour stocker de l’énergie dans une batterie, qui pourra ensuite être utilisée au moment souhaité.
Interfaces conviviales améliorées
L’intégration d’interfaces conviviales visant à améliorer l’expérience de charge constitue une avancée technologique notable dans le domaine des véhicules électriques. Ces interfaces comprennent des caractéristiques telles que des écrans tactiles, des applications mobiles, des lecteurs de cartes RFID et des commandes intuitives, toutes conçues pour améliorer le confort de l’utilisateur et l’expérience globale pendant le processus de charge.
Facteurs clés à prendre en compte lors de la conception et de la production d’un PCB pour les chargeurs de véhicules électriques
En travaillant en collaboration avec nos techniciens et nos usines, nous pouvons avoir un impact positif dans les domaines suivants :
Conception du circuit imprimé
L’EV Charger est une application nécessitant la conception de circuits imprimés haute puissance.
Les circuits à haute puissance se caractérisent par des niveaux de tension ou de courant nettement plus élevés que ceux utilisés dans les circuits à faible puissance. Il incombe aux concepteurs de veiller à ce que le circuit fonctionne dans les limites des paramètres de tension et de courant appropriés, tout en intégrant des mesures de refroidissement et de sécurité adéquates.
Les conceptions sont généralement créées en tenant compte de dispositions spécifiques. Le design du circuit imprimé doit être soigneusement élaboré pour accueillir efficacement les composants haute puissance et minimiser la génération de bruit.
Une autre considération à prendre en compte est le placement des composants afin de réduire les problèmes thermiques sur le circuit imprimé.
Pour plus de conseils sur la conception des circuits imprimés, vous pouvez contacter votre interlocuteur local ou télécharger gratuitement nos règles de conception.
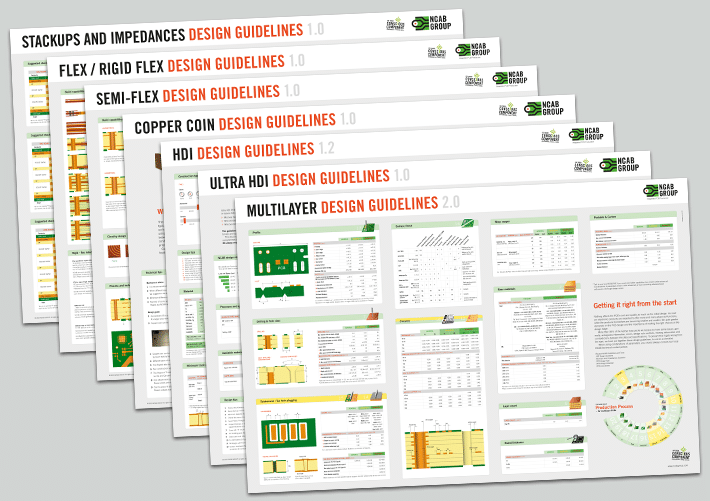
Règles de conception des PCB
Pour éviter de partir sur de mauvaises bases, nous avons mis au point des règles de conception, que nous utilisons comme liste de contrôle.
Épaisseur du vernis épargne
L’épaisseur du vernis épargne est un autre aspect important à prendre en compte dans la conception à haute puissance des EV Charger.
La présence importante de cuivre sur les couches externes peut conduire à l’utilisation d’un vernis épargne plus épais (afin de couvrir les isolements entre les pistes). L’usine peut également appliquer un double dépôt de vernis épargne.
L’épaisseur du vernis épargne est importante et le concepteur doit également vérifier la fiche technique du vernis épargne utilisé (par exemple : la rigidité diélectrique, la résistance de surface). Les recommandations de l’IPC pour le vernis épargne sont incluses dans la norme IPC-SM-840. Par défaut, l’IPC suggère d’utiliser la classe T pour les circuits de performance 2 et la classe H pour les circuits de performance 3. Le vernis épargne ne doit pas être considéré comme le seul isolant. En outre, le concepteur doit également envisager un revêtement conforme.
Epaisseur de cuivre
Les masses de cuivre (Cu) font référence à l’épaisseur ou à la quantité de cuivre utilisée pour les pistes de puissance sur un circuit imprimé. Dans les chargeurs de véhicules électriques, les épaisseurs de cuivre jouent un rôle crucial pour un transfert efficace et fiable de l’énergie.
Le cuivre est un très bon conducteur de chaleur (385 W/mK) et non seulement une épaisseur de cuivre plus importante offre une plus grande capacité de transport de courant, mais elle permet également de dissiper plus de chaleur.
Cependant, il ne faut pas seulement penser à l’épaisseur de cuivre sur la surface. Bien sûr, un dépôt plus épais est essentiel pour la gestion thermique, mais nous devons tenir compte de la largeur de la piste, car cela permet d’augmenter la section transversale, et donc la quantité de chaleur qui peut être dissipée par le conducteur.
Le cuivre épais limite également la possibilité d’avoir des éléments plus fins sur le circuit. Il existe toutefois une solution si la conception nécessite de petits composants.
Largeur et épaisseur des pistes
L’épaisseur des pistes de cuivre est déterminée par la puissance qui leur sera appliquée. Plus la puissance est élevée, plus la piste doit être large.
Les concepteurs doivent tenir compte de l’épaisseur du feuillard de cuivre et respecter la largeur de piste et l’isolement minimaux en fonction de l’épaisseur de cuivre choisie (il est important de vérifier si les pistes seront conçues sur des couches internes ou externes). Plus l’épaisseur de cuivre est importante, plus la piste doit être large.
Par exemple, si vous voulez utiliser du 3oz/105µm en épaisseur de cuivre (couches externes), la largeur de piste devra être >350µm sur la couche externe.
Le saviez-vous ?
La taille et le nombre de couche du circuit imprimé peuvent avoir un impact majeur sur le développement durable. Si nous réduisons la taille du circuit imprimé, alors nous pouvons également minimiser la quantité de matériaux utilisés, ce qui se traduit par une réduction des déchets et de l’impact sur l’environnement.
Propriétés des matériaux
Pour pouvoir réduire la distance d’isolement entre les pistes / les zones de cuivre, on peut envisager d’utiliser un matériau ayant de meilleures propriétés CTI (Comparative Tracking Index).
Les matériaux standards FR4.0 et FR4.1 sont normalement conformes à l’API 3 (voir le tableau ci-dessous). Il est possible d’utiliser des matériaux de meilleure qualité, capables de répondre à la fois à l’API 1 et à l’API 0. Des facteurs tels que la disponibilité, le délai de livraison et les homologations UL doivent être pris en compte. Veuillez contacter votre technicien NCAB pour de plus amples informations.
Tracking Index (V) | PLC |
---|---|
600 and Greater | 0 |
400 through 599 | 1 |
250 through 399 | 2 |
175 through 249 | 3 |
100 through 174 | 4 |
< 100 | 5 |
Les matériaux ayant une température maximale de fonctionnement (MOT) élevée peuvent également être envisagés si la température à l’intérieur du boîtier, ou à la surface des cartes, est élevée. Les circuits imprimés fabriqués en FR4.0 et FR4.1 peuvent être approuvés UL avec une MOT maximale de 130°C, mais les cartes fabriquées en FR15.0 et FR15.1 peuvent être approuvées pour une température minimale de 150°C.
Gestion thermique
Les composants et l’augmentation de la demande d’énergie étant les deux principales causes de chaleur, la gestion thermique est essentielle à la fiabilité des chargeurs de véhicules électriques, car une température excessive peut entraîner des défaillances.
La gestion thermique concerne les méthodes employées pour transférer l’excès de chaleur d’un endroit à un autre. Dans le cas des chargeurs de véhicules électriques, l´objectif est de transférer l’excès de chaleur loin du composant, en dissipant la chaleur dans/ou à travers le circuit imprimé, d’un côté à l’autre.
Il existe plusieurs solutions à ce problème, l’une d’entre elles étant l’agencement :
- Placer les composants générateurs de chaleur loin du bord de la carte pour aider à dissiper la chaleur de manière uniforme.
- Ne pas regrouper les composants générateurs de chaleur, mais les répartir.
- Éloigner les composants générateurs de chaleur des composants plus petits et plus sensibles.
- Envisager l’installation de dissipateurs de chaleur dès le début du processus.
- Optimiser la circulation de l’air dans l’enceinte de l’unité assemblée.
- Prévoir des pistes plus larges pour évacuer la chaleur et utiliser des feuillards de cuivre épais sur les couches internes. Toutefois, il faut garder à l’esprit qu’avec des épaisseurs de cuivre élevées, l’espace peut être un problème.
Chargeurs à courant alternatif (CA) et chargeurs à courant continu (CC) – deux types de systèmes de recharge pour véhicules électriques
Les chargeurs AC (courant alternatif) et DC (courant continu) sont deux types de systèmes de charge utilisés pour les véhicules électriques.
Quelles sont les différences entre une charge en courant alternatif et une charge en courant continu ?
- La charge en courant alternatif (CA) et la charge en courant continu (CC) se distinguent par l’emplacement de la conversion du courant. Contrairement aux chargeurs à courant alternatif, qui convertissent le courant alternatif à l’intérieur du véhicule à l’aide du chargeur embarqué, les chargeurs à courant continu intègrent le convertisseur dans l’unité de charge. Par conséquent, les chargeurs à courant continu peuvent alimenter directement la batterie de la voiture sans dépendre du chargeur embarqué pour la conversion.
- Les chargeurs à courant alternatif sont spécifiquement conçus pour fonctionner avec du courant alternatif, le type d’électricité généralement fourni par les réseaux électriques. En revanche, les chargeurs à courant continu sont conçus pour fonctionner avec du courant continu, qui est généralement stocké dans des batteries ou généré par des panneaux solaires.
- Les chargeurs à courant alternatif se trouvent généralement dans divers endroits tels que les maisons, les lieux de travail, les parkings et les bornes de recharge publiques. Les chargeurs à courant continu, quant à eux, se trouvent généralement dans les zones de recharge publiques situées le long des autoroutes, des grands axes et des zones urbaines, et sont destinés aux déplacements longue distance et aux recharges rapides.
- Le courant continu est utilisé pour la charge rapide, tandis que les chargeurs à courant alternatif offrent des niveaux de puissance inférieurs, ce qui allonge les temps de charge.
- Les chargeurs à courant alternatif offrent généralement des puissances de charge allant de 3,7 kW à 22 kW, en fonction du chargeur spécifique et de la capacité du chargeur embarqué du véhicule électrique. Les chargeurs à courant continu peuvent fournir des puissances de charge élevées allant de 50 kW à plusieurs centaines de kilowatts, permettant une charge rapide et réduisant le temps nécessaire pour recharger la batterie d’un véhicule électrique.
- Généralement, le courant continu utilise une tension plus élevée – Les chargeurs de courant continu adoptent de plus en plus des niveaux de tension plus élevés pour permettre une charge plus rapide. L’utilisation de tensions plus élevées, telles que 400V, 800V ou plus, réduit le temps de charge en permettant à des courants plus élevés de circuler dans la batterie du véhicule électrique. Une tension de charge plus élevée permet également de réduire les pertes et d’améliorer l’efficacité du transfert d’énergie. Il convient de noter ici que de nouvelles études ont montré que les tensions élevées dans un circuit imprimé peuvent causer de graves dommages au fil du temps ; c’est le cas lorsque le PCB lui-même comporte des pistes dont la tension est supérieure à 500V. Dans le cadre de la recharge des véhicules électriques, la performance des courants forts et des tensions élevées est importante pour la conception de l’alimentation. Il est donc important de s’assurer que le design respecte les exigences de sécurité, telles que :
- Espacement entre les via (environ 5 mm)
- Isolement cuivre à cuivre / piste à piste.
Recommandations :- 48V = 1 – 1.5mm
- 110V = 3mm
- 220V = 6 – 8mm
- 480V = 16mm
- Cuivre en bord de carte (environ 5 mm)
- Une autre différence entre les deux est le coût, les chargeurs à courant alternatif étant généralement moins chers que les chargeurs à courant continu.
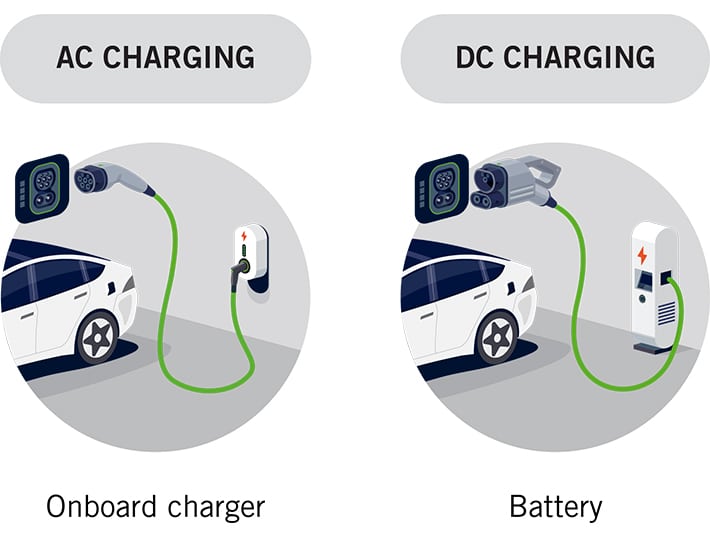
Normes auxquelles les circuits imprimés EV Charger doivent satisfaire
La norme pour les connecteurs ou les prises de recharge des véhicules électriques, varie selon les endroits et les modèles de véhicules. Bien qu’il n’y ait pas d’accord sur une technologie de prise universelle, un grand nombre de constructeurs automobiles mondiaux soutiennent le système de charge combiné (CCS) en Amérique du Nord et en Europe.
Malgré l’existence de normes différentes, il existe un consensus croissant dans divers pays pour promouvoir l’adoption de normes harmonisées pour les véhicules électriques dans le monde entier. En outre, il existe des normes et des réglementations mondiales importantes pour les véhicules électriques telles que la norme CEI 61851 qui couvre les modes de charge, les connecteurs et la sécurité électrique. Une autre norme est l’ISO 15118 qui se concentre sur la communication entre les véhicules électriques et la borne de recharge. Il est essentiel de reconnaître que les réglementations et normes spécifiques peuvent varier d’un pays ou d’une région à l’autre.
Quelle valeur ajoutée NCAB peut-il apporter ?
Contrôle de la qualité et assistance technique – Notre objectif est de contrôler la qualité tout au long du processus de fabrication des circuits imprimés. La conception initiale d’un PCB a une incidence considérable sur son coût total et sa fiabilité. Tous les bureaux NCAB comptent des spécialistes qui travaillent avec vous pour comprendre vos exigences et celles du produit. Nos équipes de support à la conception peuvent vous conseiller. Elles ont pour but de vous aider à obtenir la meilleure conception possible pour une production rentable de vos circuits imprimés, des prototypes à la production en série. Notre équipe de gestion des usines travaille sur place, dans nos usines. Nos ingénieurs qualité sont directement responsables des performances ainsi que des relations avec elles pour obtenir des améliorations.
Le développement durable est un élément central de notre façon de penser et d’agir. Lorsque vous travaillez avec nous, nous mettons en évidence les différents aspects de votre circuit imprimé (de la conception à la livraison, en passant par la production) pouvant avoir un impact positif sur le développement durable.
Grâce à notre outil sur les PCB cost drivers, vous pouvez découvrir les différents facteurs qui déterminent le coût d’un circuit imprimé, ainsi leur impact direct sur la durabilité.
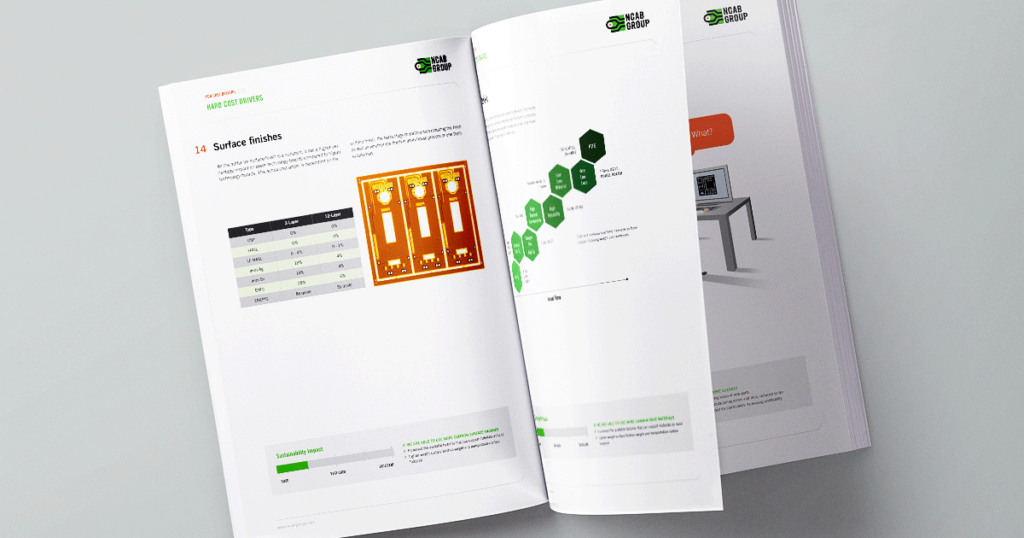
PCB cost drivers
Qu’est-ce-qui détermine le coût d’un circuit imprimé ?
Et comment ces facteurs influencent-ils à leur tour le développement durable ? Nous avons développé un outil afin de vous aider à anticiper et à déterminer les PCB cost drivers.
Support local – Grâce à notre présence mondiale et à notre vaste réseau de bureaux et de représentants locaux, nous assurons une communication claire et efficace. Nos équipes bien informées comprennent les exigences et les défis spécifiques de chaque marché, ce qui leur permet de fournir des solutions sur mesure et des conseils précieux tout au long du processus de fabrication des circuits imprimés.
Spécifications clés pour la fiabilité – Nous avons notre propre spécification PCB que nous utilisons pour tous les circuits imprimés que nous fournissons à nos clients. Plusieurs caractéristiques importantes sont propres à NCAB et/ou vont au-delà de la norme industrielle IPC Class 2. C’est l’un des facteurs qui nous permet de fournir un produit plus fiable que beaucoup de nos concurrents.
Alors que les véhicules électriques continuent de révolutionner le secteur des transports, l’importance de l’infrastructure de recharge devient primordiale. Les circuits imprimés jouent un rôle crucial en garantissant l’efficacité, la fiabilité et la sécurité des systèmes EV Charger.
En tant que fournisseur de circuits imprimés, nous devons également nous adapter et apprendre, afin de pouvoir fournir des solutions innovantes et de répondre aux demandes changeantes du marché.