Les produits électroniques modernes doivent offrir des fonctionnalités toujours plus avancées, tandis que leur taille est de plus en plus réduite. Cela impose des exigences accrues en matière de conception de circuits imprimés et de processus de fabrication.
Deux facteurs clés contribuent au succès de la production de PCB HDI : d’abord, faire les bons choix dès la conception, puis choisir avec soin l’usine capable de répondre aux exigences techniques spécifiques du projet.
Plus petit et plus complexe
Qu’il s’agisse d’électronique grand public, d’informatique, d’automobile ou de technologie médicale, la tendance générale est à la miniaturisation. Il ne s’agit pas seulement d’une réduction de la taille du produit fini, mais aussi de la taille des composants eux-mêmes, ce qui nécessite des assemblages plus denses et des fonctionnalités plus compactes.
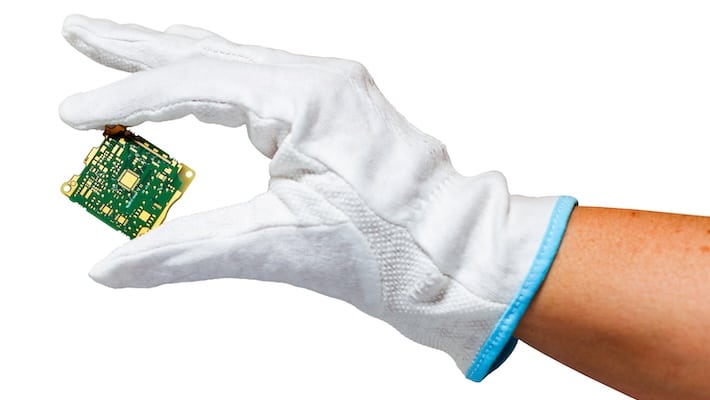
Ces produits électroniques plus sophistiqués ont favorisé la généralisation des circuits imprimés plus complexes. Ces spécificités requièrent des solutions d’interconnexion haute densité (HDI) comportant un plus grand nombre de couches et davantage de connexions, en surface comme à l’intérieur du circuit imprimé, avec des pistes plus fines et des isolements plus étroits. Ceci conduit à une conception basée sur des microvias plus petits, percés au laser (blind via), car les vias traversants classiques ne s’intègrent tout simplement pas dans l’espace disponible. Par conséquent, les fabricants produisent de plus en plus de cartes avec micro vias, intégrant également des vias enterrés. Ceci augmente le nombre d’interconnexions au sein de la carte et libère un espace précieux sur la couche externe pour l’installation de composants supplémentaires.
Le nombre accru de couches, associé à la technologie micro via, nécessite également l’utilisation de pré-imprégnés et de cores plus fins que dans les cartes fabriquées de manière conventionnelle, ce qui entraîne également des exigences accrues pour les usines.
Plus d’étapes de production
La miniaturisation généralisée impose des exigences bien plus élevées aux équipements de production des usines de PCB. De nombreuses étapes de production des cartes HDI sont similaires à celles des circuits multicouches. Cependant, la production HDI requiert des équipements beaucoup plus sophistiqués pour obtenir les géométries requises.
L’intégration de plusieurs couches de vias et/ou de micro vias enterrés dans les cartes nécessite non seulement plusieurs étapes supplémentaires, mais aussi plusieurs répétitions, ce qui augmente la complexité et le risque d’erreur. Les géométries des cartes HDI sont toutes beaucoup plus petites, ce qui nécessite des équipements dédiés et de meilleure qualité, conçus pour une fabrication de haute technologie. De nombreuses usines sont équipées de perceuses laser, et un nombre croissant entre elles possèdent les équipements de métallisation et l’expérience nécessaires pour fabriquer des cartes HDI fiables et de qualité. Nous consacrons beaucoup de temps et d’efforts à la qualification et à la vérification d’une usine avant de lui accorder notre autorisation pour la fabrication de cartes HDI pour nos clients.
La première étape pour la création de micro vias est l’utilisation de perceuses laser de pointe capables de percer des micro vias borgnes de 100 μm ou moins. Les dernières générations de ces machines sont capables de percer des centaines de trous par seconde. Ensuite, le transfert est une opération tout aussi cruciale qui exige une précision extrême, inaccessible aux techniques photographiques traditionnelles. Les fabricants de cartes HDI utilisent des technologies d’imagerie directe par laser (LDI), qui reproduisent le motif directement sur le matériau photo-imageable. L’absence de film photo améliore la qualité, permettant ainsi un transfert des motifs bien plus précis, jusqu’à 50 μm.
Prérequis : Équipement adéquat et salles blanches
Pour garantir le meilleur résultat possible lors du processus de transfert d’images, il est essentiel que celui-ci soit réalisé dans des salles blanches spéciales, dont la température et l’humidité sont soigneusement contrôlées. Les salles blanches utilisées pour ces processus sont conformes à la norme fédérale américaine 209E Classe 10000. Cette classe, qui constitue la norme industrielle depuis de nombreuses années, stipule que la concentration de particules en suspension dans l’air ≥ 0,5 μm (l’épaisseur d’un cheveu humain est généralement de 20 à 50 μm) ne doit pas dépasser 10 000 particules par pied cube.
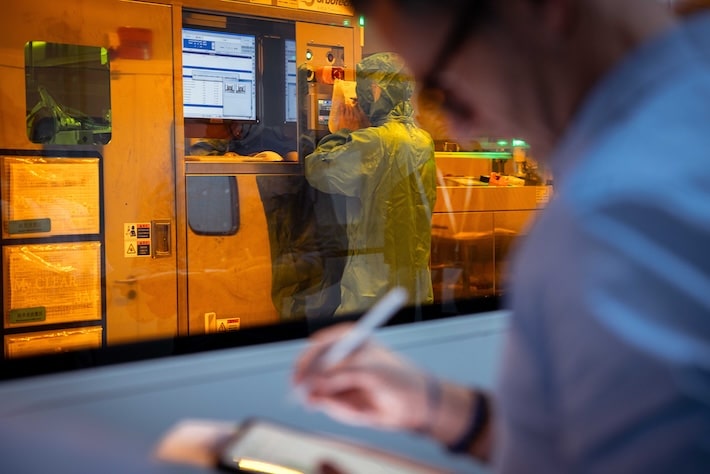
Aujourd’hui, les meilleures usines disposent de salles blanches conformes aux exigences de la classe 1000. Pour illustrer ce concept, l’air de notre environnement quotidien contient un million de particules de même taille par mètre cube. Cependant, les salles blanches de bonne qualité sont coûteuses, tant à l’achat qu’à l’entretien.
La production de cartes HDI nécessite également un type de ligne de métallisation différent. Pour les cartes non HDI, on peut généralement se contenter de lignes de métallisation classiques, avec des panneaux maintenus verticalement et utilisant une agitation mécanique et pneumatique, permettant aux produits chimiques de faciliter le dépôt de cuivre sur les surfaces et dans les trous. Cependant, cette méthode n’est pas vraiment adaptée aux cartes HDI dont des vias borgnes peuvent mesurer 100 μm de diamètre ou moins. C’est pourquoi la plupart des usines utilisent à la fois des lignes de métallisation horizontales et verticales continues (VCP). Ces méthodes consistent à pulvériser les produits chimiques à haute pression sur la surface, ce qui garantit une métallisation correcte des micro vias.
Le positionnement correct du vernis épargne par rapport au motif représente un défi majeur, car les composants extrêmes, comme les composants CMS circuits 01005 et μBGA avec des pas de 400 μm ou plus fins, doivent assurer une registration jusqu’à 37 μm, voire 25 μm dans les cas extrêmes. Pour y parvenir, des unités d’exposition CCD sont nécessaires. Les fabricants de circuits imprimés ont désormais la possibilité d’utiliser des unités LDI spéciales pour exposer le vernis épargne. Ils ont en effet développé des encres spéciales pour les conceptions HDI nécessitant une énergie de polymérisation plus faible.
Regarder « sous le capot »
Nous devons examiner minutieusement tous les aspects des processus et équipements de production d’une usine pour déterminer si elle répond aux exigences de la fabrication HDI. C’est comme inspecter sous le capot d’une voiture avant de l’acheter. Si une usine affirme être équipée de perceuses laser et donc capable de produire des PCB HDI fiables, c’est comme dire qu’il suffit de se procurer un marteau et un burin pour devenir le nouveau Michel-Ange ! Nous savons que l’équipement de perçage laser n’est pas la clé de voûte de la production HDI ; il est tout aussi important de disposer du bon équipement de métallisation et de la bonne chimie, ainsi que de savoir gérer, contrôler et vérifier l’intégralité du processus de métallisation. Nous examinons également les produits chimiques et les méthodes utilisés, ainsi que les équipements et procédures de transfert d’image, tout en comprenant les chiffres qui sous-tendent l’expérience réelle des usines dans ce domaine et leurs performances, deux facteurs cruciaux.
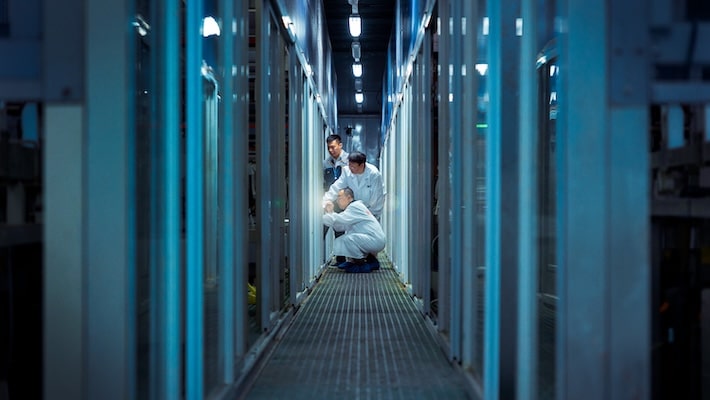
Notre stratégie consiste à maintenir et à développer un parc industriel de pointe et sécurisé. Nous insistons sur l’importance de la capacité de l’usine non seulement à fabriquer des circuits imprimés HDI, mais aussi à minimiser les erreurs de production. La production de cartes HDI avec 3 couches de micro vias de chaque côté et 4 couches de micro vias enterrées nécessite quatre opérations de lamination, 10 de perçage et de métallisation. Si le taux de défaillance est de 10 % à chaque passage en usine, le nombre de cartes mises au rebut dépasserait les volumes livrés. Dans ce cas, il est essentiel de s’interroger sur la qualité des pièces livrées. Sachant que les composants d’une carte peuvent coûter plus de 100 fois son prix, il est impératif de pouvoir compter sur sa qualité. Dans le cas contraire, la mise au rebut du produit pourrait s’avérer extrêmement coûteuse.
Obtenez le bon design dès le début
Un autre aspect à prendre en compte pour les circuits avancés est la conception elle-même. Les marges de manœuvre sont minimes concernant des facteurs tels que la largeur des pistes, les isolements entre les plages de composants, les exigences d’impédance, le diamètre des vias et leur relation avec les plages de capture et de cible. Tout cela représente un défi considérable lors de la phase de construction. Les règles de conception doivent être réalistes et adaptées à la production en série dès le départ.
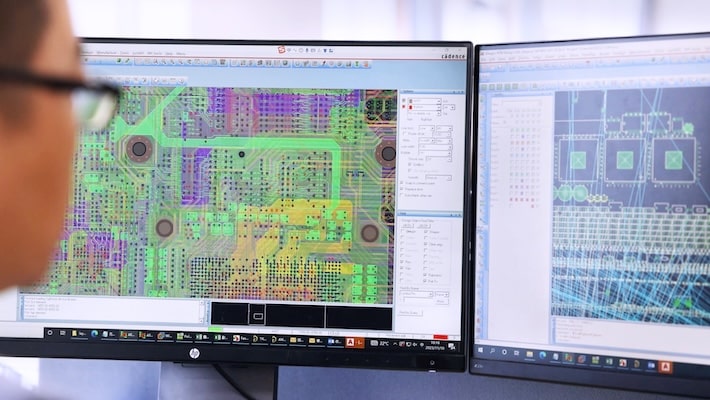
Il existe plusieurs pièges à éviter lorsqu’on se limite aux règles de conception des usines de prototypes : par exemple, rendre les cores des couches internes trop fins pour obtenir un bon couplage capacitif. Cela peut fonctionner dans une usine de prototypes, où l’on prend grand soin d’usiner manuellement ces cores fins. Cependant, cela peut entraîner des problèmes majeurs lors de la production en série, car les capacités peuvent varier. Dans ce cas, les cores les plus fins peuvent facilement se coincer pendant le traitement à cause de longues lignes de gravure orientées vers le volume, car ils sont trop fragiles. Nous recommandons donc d’utiliser un isolement diélectrique de 60 à 80 µm pour une couche de microvias, car en-dessous, cela peut poser problème. Notre expérience nous montre que cette règle de conception fonctionne bien dans toutes nos usines de haute technologie. Certaines usines avec lesquelles nous travaillons sont plus avancées et peuvent fabriquer des cores encore plus fins si nécessaire.
Conception de circuits imprimés HDI rentable
Si l’espace sur la carte est suffisant et que le composant est disponible avec différents pas, nous recommandons également de choisir un composant avec un pas plus grand, car cela réduit la complexité du circuit et permet de réaliser des économies. Des composants plus petits peuvent être moins chers à l’achat ou plus facilement disponibles, mais cette approche peut rendre la carte inutilement coûteuse par rapport à son application finale.
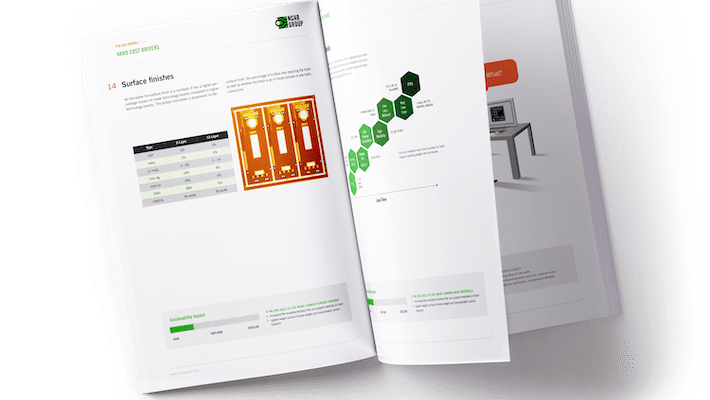
Opter pour des composants de petite taille augmente généralement la complexité des circuits, et donc le coût de la carte. C’est pourquoi le client doit collaborer avec son fournisseur de circuits imprimés pour déterminer si la conception nécessaire à ces composants est rentable : le coût réduit associé à l’achat de composants plus facilement disponibles, mais plus complexes, est-il compensé par un circuit imprimé potentiellement plus coûteux ? Par exemple, s’il est destiné à être utilisé dans des téléphones portables destinés au marché grand public ou à une production en petite série. On observe également une augmentation de l’utilisation de composants de type « boîtier sur boîtier » (PoP) dans l’industrie. Il est important de vérifier si l’assembleur maîtrise cette technologie et les coûts supplémentaires qu’elle peut entraîner. Bien sûr, des composants plus petits permettent de gagner de la place, ce qui peut permettre de produire une carte moins chère, à condition de ne pas la complexifier avec plusieurs niveaux de microvias ou l’ajout de structures enterrées, etc. Il est toujours nécessaire de peser le pour et le contre des problèmes de complexité dès la phase de conception.
Les fabricants de PCB doivent être impliqués dès le début pour aider les clients à trouver la solution idéale. Il est important de comprendre qu’il existe de réelles différences entre la production de prototypes et la production en série. Se concentrer sur les mauvais éléments dès le départ pourrait compromettre l’ensemble du projet si votre conception ne peut être appliquée à la production en série. Nous recommandons d’impliquer votre fournisseur de circuits imprimés dès le début afin de garantir une fabrication à un coût raisonnable, avec un niveau de complexité adapté à la conception et des rendements fiables. Contactez-nous pour discuter de vos projets ; nous serons ravis de vous aider.
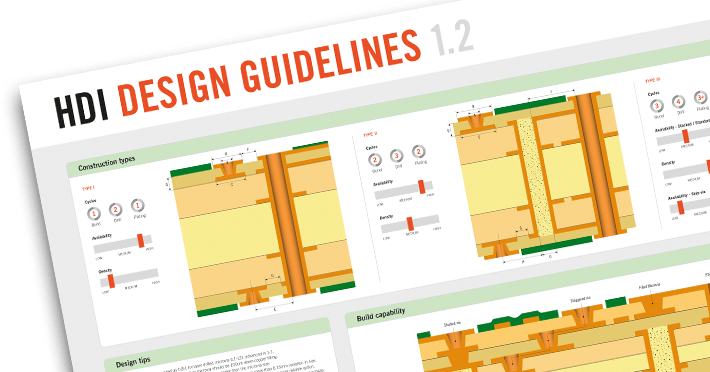
Téléchargez nos règles de conception pour les PCB HDI
Pour éviter de partir sur de mauvaises bases, nous avons mis au point nos règles de conception afin de vous aider à concevoir votre circuit imprimé.