Woher kommen die Kosten? Nun, 80-90% aller Kosten werden in einer sehr frühen Phase der Kette in das Projekt eingebaut – bevor die Lieferanten (EMS-Unternehmen, LeiterplattenLieferanten usw.) das Design in Sichtweite haben.
Wir empfehlen Ihnen immer Ihre Lieferanten bereits in der frühen Entwurfsphase einzubeziehen. Um das Thema Kostentreiber anzugehen, haben wir dieses in zwei Kategorien unterteilt. In „harte“ und „weiche“ Kostentreiber der Leiterplattenproduktion. Heute werden wir über die harten Kostentreiber diskutieren und die weichen Kostentreiber zu einem späteren Zeitpunkt behandeln.
Es gibt grundlegende Faktoren, wie die Größe der Leiterplatte – wir alle wissen, je größer die Leiterplatte, desto mehr Material wird benötigt. Damit steigen die Kosten. Wenn wir eine 2-Lagen-Platte mit einer Abmessung von 2cmx2cm“ als unsere „Basis“ betrachten, wird eine Erhöhung der Abmessungen auf 4cmx4cm“ die anfänglichen Materialkosten vervierfachen. Eine steigende Lagenzahl wirkt sich auch auf die Basismaterialkosten aus, da der Materialbedarf nicht nur ein Faktor auf der X- und Y-Achse ist, sondern auch auf der Z-Achse. Jeder Kern, der dem Lagenaufbau hinzugefügt wird, erfordert zusätzliches Material, zuzüglich der Kosten für die Verarbeitung dieses Materials. Verarbeitungsprozesse wie Drucken und Ätzen, die AOI-Inspektion, die chemische Reinigung und der Oxidationsprozess sind hier zu nennen. Eine Erhöhung der Anzahl der Lagenzahl erhöht damit automatisch die Kosten des Endprodukts.
Das von Ihnen gewählte Basismaterial wirkt sich ebenfalls auf die Kosten aus. Grundsätzlich wird jede Anforderung, die über den Standard FR-4 hinausgeht, zusätzliche Kosten verursachen. Die Anforderung ein sehr spezifisches Material zu verwenden wird zusätzliche Kosten verursachen und kann weiterhin zu Problemen mit der Verfügbarkeit führen. Wir empfehlen Ihnen, IPC4101/XXX als Standardanforderung zu verwenden. Wenn Sie ein bestimmtes Material spezifizieren, empfehlen wir Ihnen die Option „oder gleichwertig“ zu ergänzen – dies eröffnet den Fabriken einige Optionen alternative Materialien zu verwenden bei gleichzeitiger Erfüllung Ihrer Anforderungen.
Die Kupferdicke diskutieren?
Die Komplexität des Aufbaus kann eine weitere Ursache für zusätzliche Kosten sein. Wenn Sie eine Standard-Multilayer-Leiterplatte nehmen und dieser Sacklöcher, vergrabene Durchkontaktierungen oder eine Kombination aus beidem hinzufügen, verursacht dies zusätzliche Kosten. Um die vergrabenen Durchkontaktierungen herzustellen muss die Leiterplatte geklebt, gebohrt, mit Kupfer plattiert und dann für den nächsten Bohr- und Plattenzyklus erneut geklebt werden. Mit jedem Zyklus den die Leiterplatte dabei durchlaufen muss, steigen die Kosten für die Herstellung.
Ein weiterer sehr wichtiger Faktor, den es zu berücksichtigen gilt, ist die Anordnung der Leiterplatte(n) im Liefernutzen. Die Art und Weise wie Sie Leiterplatte(n) im Liefernutzen platzieren, wirkt sich auf den Materialverbrauch aus. Einige Designer lassen viel Platz zwischen den Leiterpatten und große Stege. Wenn dieser Platz nicht benötigt wird, erhöht dieser nur den Umfang des Liefernutzens und damit die Kosten. Verringert man den Abstand zwischen den Leiterplatten und die Größe der Stege, dann verringert man den Materialverbrauch und generiert tatsächliche Kosteneinsparungen. Wenn das Design quadratisch oder rechteckig ist, bietet die Anordnung der Leiterplatten mit V-Kerbe und Abstand „0“ im Liefernutzen die ultimative Einsparung. Die Verwendung eines Liefernutzenrands auf zwei anstatt auf vier Seiten erhöht diese Einsparungen.
Die Leiterbahnbreite und der -Abstand wirken sich auch auf den Preis aus. Die Fabriken haben in Bezug auf die schmalste Leiterbahnbreite und den schmalsten Leiterbahnabstand unterschiedliche technische Fähigkeiten. Diese Fähigkeiten wirken sich darauf aus, wie schmal eine Leiterbahn bzw. wie schmal der Abstand dazwischen für eine Fabrik minimal sein darf. Faustregel: „Je schmaler die Leiterbahn und je schmaler der Abstand, desto schwieriger ist es sie zu produzieren (desto größer das Ausfallrisiko, die Ausschussrate)“. Diese Schwierigkeit wird zusätzlich erhöht, wenn das Design lange Leiterbahnen enthält oder die Leiterbahnen in Schleifen verlaufen. Mit der Länge der Leiterbahn erhöht sich die Wahrscheinlichkeit eines Fertigungsfehlers. Um schmale Leiterbahnen und – Abstände herstellen zu können, benötigen die Fabriken hochwertigste Fertigungstechnik und auch spezielles, technisches Know-How. Beides führt letztlich zu einer Kostensteigerung
Die Anzahl und die Größe der Bohrungsdurchmesser sind ein weiterer Kostentreiber. Sehr kleine Bohrungsdurchmesser oder eine große Anzahl von Bohrungen führen zu einer teureren Leiterplatte. Bohrer mit kleinen Bohrdurchmessern haben schmalere Spannutzen, welche die Anzahl der Platten, die in einem Bohrzyklus gebohrt werden können, begrenzen. Die kleinere Nutzenlänge kleinerer Bohrerdurchmesser begrenzt den Leiterplattenhersteller in der Anzahl der Produktionsplatten, die in einem Stapel gebohrt werden können. Eine Reduzierung der Stapelhöhe führt automatisch zu einer Erhöhung der Arbeitskosten, da damit die Anzahl der Zyklen auf der CNC-Bohrmaschine steigt. Das Verhältnis des Bohrdurchmessers zur Dicke der Leiterpatte (auch Aspekt-Ratio genannt) muss ebenfalls berücksichtig werden. Kleine Bohrdurchmesser in dicken Leiterplatten sind damit ein Kostenfaktor. Der kleinste Bohrdurchmesser und das Verhältnis zur Leiterplatte (Aspekt-Ratio) kann die Anzahl der Fabriken, die Ihr Design herstellen können, zusätzlich einschränken.
Der letzte Prozessschritt bei den harten Kostentreibern, mit dem wir uns befassen müssen ist die Lötoberfläche. Oberflächen wie Hartgold, Dickgold, Spezialoberflächen wie ENEPIG erhöhen die Kosten. Wir alle wissen, dass Edelmetalle kostspielig sind. Diese als Lötoberfläche zu spezifizieren wird zweifellos zusätzliche Kosten verursachen. Wenn es um harte Kostentreiber geht, sollten Sie nur das spezifizieren, was Sie tatsächlich benötigen. Fragen Sie nicht nach einer Lötoberfläche, die nicht benötigt wird oder nach Materialien, die nicht notwendig sind. Alle Entscheidungen, die Sie in der Entwurfsphase treffen, wirken sich auf den Endpreis der Leiterplatte aus. Wir empfehlen Ihnen Ihren Leiterplattenlieferanten so früh wie möglich in das Design einzubeziehen. Wie Sie sehen, müssen viele Entscheidungen getroffen werden – werden diese nicht zum richtigen Zeitpunkt getroffen, sondern erst wenn der Hersteller mit dem Design konfrontiert wird, kann es bereits zu spät sein, um Optimierungen vorzunehmen. Weiterhin werden Optimierungen in dieser Phase negativen Einfluss auf Ihren Produktionszyklus haben.
What drives the cost of a circuit board?
And how do those factors in turn impact the sustainability? To avoid large cost drivers we have developed a tool that can support you.
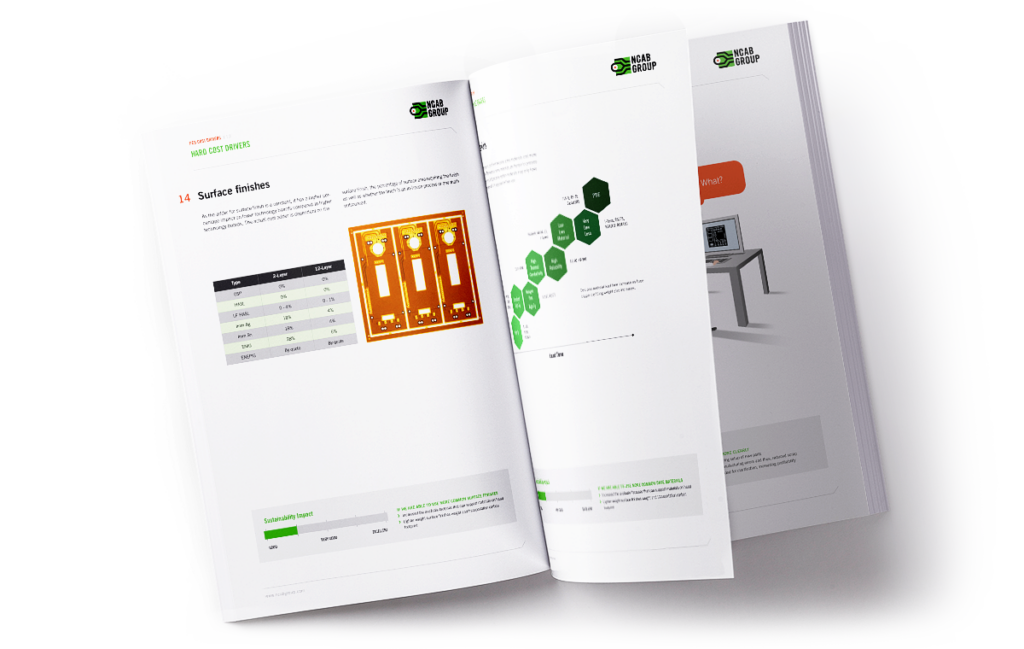