Was ist bei der Entwicklung von Leiterplatten für extreme Umgebungen zu beachten? Erfahren Sie mehr über die Herausforderungen und wie die Leiterplatten für das Wärmemanagement, die Höhe, Stöße und Vibrationen angepasst werden müssen.
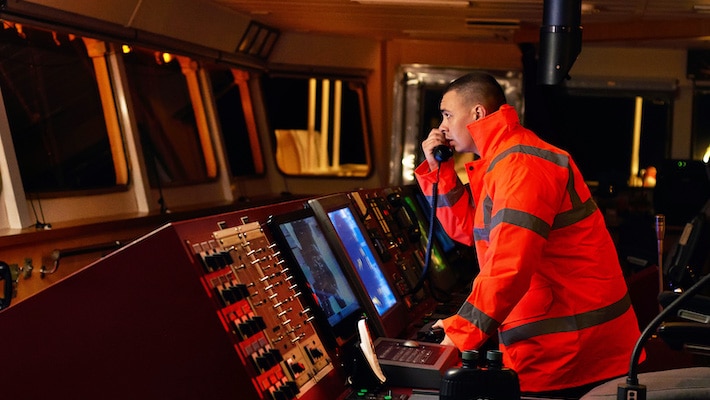
Im ersten Teil dieser Blogserie habe ich mehr über Anwendungsbereiche und die Herausforderungen für Leiterplatten in rauen und extremen Umgebungen gesprochen. Dieses Mal möchte ich tiefer in die Überlegungen zum Leiterplattendesign für extreme Umgebungen eintauchen. Das Design einer Leiterplatte für eine nicht-anspruchsvolle Umgebung kann an sich schon eine gewaltige Aufgabe sein. Es müssen viele Aspekte berücksichtigt werden, die sich wiederum gegenseitig beeinflussen oder voneinander abhängig sein können. Wenn ich über einige der besonderen Herausforderungen nachdenke, die extreme Umgebungen mit sich bringen, bin ich erstaunt über die Robustheit der verfügbaren Technologie. Die negativen Auswirkungen von Höhe, Vibration, Stößen und Hitze machen unseren elektronischen Systemen zu schaffen, auf die wir uns alltäglich verlassen.
Höhenunterschiede – wie wirken sie sich auf die Leiterplatte aus?
Eine Herausforderung, die viele Leiterplattendesigner bewältigen müssen, sind die Auswirkungen der Luftdichte in Abhängigkeit von der Höhenlage. Ohne zu sehr ins Detail zu gehen, wird die Dichte der Atmosphäre mit zunehmender Höhe geringer. In der Atmosphäre gibt es einen Bereich zwischen der unteren Atmosphäre und dem Vakuum des Weltraums, in dem Elektrizität schon bei niedrigeren Spannungen einen Lichtbogen bilden kann. Dies bedeutet, dass die Durchschlagsspannung der Luft in der dünneren Atmosphäre geringer ist. Dadurch kann der Strom bei niedrigeren Spannungen als auf Meereshöhe einen Lichtbogen über Leiter schlagen. Erschwerend kommt hinzu, dass sich die Ladung an einem Punkt schneller aufbaut als auf einer runderen Fläche. Die sich aufbauenden Ladungen können potenziell als Lichtbogenpunkte wirken.
Es gibt einige Dinge, die wir tun können, um diese Gefahr zu minimieren. Zunächst sollten Sie IPC-2221, Abschnitt 6 studieren. Dieses Kapitel enthält die wichtigsten Informationen zur Berechnung des elektrischen Abstands, der für Ihr Design erforderlich ist. Eine weitere Möglichkeit, Lichtbögen zu vermeiden, ist die Abrundung der Ecken in unserem Design. Damit meine ich die Beseitigung der neunzig Grad Innen- und Außenecken an Versorgungslagen, an SMD-Pads und an den Knickstellen von Leiterbahnen. Außerdem sollte man auf die Stiftleisten achten. Da diese Bereiche der Leiterplatte oft mit unterschiedlichen Spannungspegeln verbunden sind, besteht an diesen Stellen auch ein höheres Risiko für Lichtbögen. Manchmal haben wir ungenutzte Stifte auf dem Steckverbinder, die uns einen noch größeren Abstand ermöglichen, wenn wir nur jeden zweiten Stift verwenden.
Was kann passieren, wenn die Leiterplatte extremen Stößen und Vibrationen ausgesetzt ist?
In manchen Umgebungen sind Leiterplatten extremen Schock- und Vibrationsbelastungen ausgesetzt. Extreme Schocks sind Ereignisse, bei denen die Leiterplatten für kurze Zeit einer hohen Amplitude von Bewegungskräften ausgesetzt sind. Bei extremen Erschütterungen sind die Leiterplatten hingegen längerer Bewegung mit geringerer Amplitude ausgesetzt. Die Bewegungskraft führt dazu, dass die Leiterplatte um den Massenschwerpunkt schwingt. Die Schwingungen belasten wiederum die Leiterplattenmaterialien und Verbindungsstellen. Die Materialien werden an der Stelle belastet, an der sich das Prepreg mit dem Kupfer verbindet. Zuddem könnte die Lochmetallisierung reißen, was schlimmstenfalls einen Ausfall des Systems zur Folge hätte. Es gibt viele kleine Dinge, die wir tun können, um Stöße und Vibrationen zu mindern. Der Schlüssel liegt darin, ein Minimum an Masse in das System einzubringen und gleichzeitig die mechanische Stabilität zu erhalten. Neben Absteifungen und Vergussmassen sind im Folgenden einige Überlegungen zum Leiterplattendesign aufgeführt.
PCB-Design für Schock- und Vibrationsfestigkeit
Wir können mehr Befestigungslöcher in die Platine einbauen. Mehr Befestigungslöcher bedeuten mehr Befestigungspunkte am Gehäuse und mehr Stabilität. Dadurch können auch mehr Dämpfungsvorrichtungen in das System integriert werden.
Ein weiterer Aspekt der Leiterplatte, mit dem wir uns befassen wollen, ist der Stackup. Im Unterricht hatte ich praktische Aufgaben wie das Entwerfen einer Platine und eines Stackups für eine Satellitenanwendung. Das war meine Lieblingsaufgabe. Bei Leiterplatten, die extremen Schock- oder Vibrationsbelastungen ausgesetzt sind, muss sichergestellt werden, dass der Harzgehalt des Pre-Pregs ausreicht, um diesen Belastungen standzuhalten. Das Pre-Preg-Harz ist der Klebstoff, der die Leiterplatte zusammenhält. Bei Stößen und Vibrationen kann sich die Leiterplatte verbiegen und die Verbindungspunkte belasten. Um die Belastung so weit wie möglich zu verringern, sollten wir die Verwendung von Pre-Pregs mit einem Harzgehalt von über 50 % in Betracht ziehen. Darüber hinaus ist das Hinzufügen von mehr als zwei Lagen Pre-Preg eine weitere Möglichkeit, die Festigkeit der Verbindung zu erhöhen. Ich spreche hier von einer Überlegung, weil die Anforderungen an die Signalintegrität nicht immer einen einfachen Wechsel der Dielektrika erlauben. Was ist, wenn Sie keine Anforderungen an die Signalintegrität haben? Wenn drei Lagen Pre-Preg gut sind, dann müssen vier besser sein, oder? Das mag sein. Ab einem bestimmten Punkt wirkt sich zu viel Pre-Preg nachteilig auf die Registrierung von Schicht zu Schicht aus. Ich würde versuchen, bei maximal drei Lagen zu bleiben, es sei denn, Ihr Leiterplattenlieferant sagt etwas anderes. Wenn Sie mehr Dicke wünschen, aber nicht noch mehr Pre-Preg hinzufügen können, sollten Sie die Verwendung von unkaschierten Kernen im Stackup in Betracht ziehen. Im Gegensatz zum Pre-Preg ist ein unkaschierter Kern bereits ausgehärtet, so dass er dem Presszyklus kein Harz hinzufügt. Dadurch wird die Registrierung von Schicht zu Schicht nicht beeinträchtigt.
Abschließend möchte ich noch auf die internen Verbindungspunkte eingehen. Wenn die Leiterplatte schwingt, schwingen auch die Bohrlöcher. Dadurch wird die Metallisierung in den Löchern belastet. Wenn die Metallisierung belastet wird, kann sie brechen. Einige Leiterplatten können wieder funktionieren, nachdem sie auf Betriebstemperatur gebracht wurden, bei anderen kann es zu einem katastrophalen Ausfall kommen. In jedem Fall ist es nicht immer möglich, die Leiterplatte vor Ort zu reparieren. Eine zusätzliche Metallisierung der Löcher ist nur eine weitere Überlegung, um eine robuste Leiterplatte zu erhalten und ist nicht für jede Anwendung geeignet.
Wärmemanagement in Leiterplatten
Das Wärmemanagement ist die letzte Herausforderung, die ich erörtern möchte. Für eine einfache Leiterplatte ist eine passive Kühlung, z. B. durch Konvektion, eine angemessene Lösung für das Wärmemanagement. Andere Leiterplatten können zur Wärmeübertragung mit dem Gehäuse verbunden sein, und einige können durch andere Geräte gekühlt werden. Leiterplatten, die in extremen Umgebungen arbeiten, können nicht immer mit diesen Methoden gekühlt werden. Wir können die Leiterplatte jedoch so gestalten, dass sie über aktive Kühlungslösungen verfügt.
Eine einfache Möglichkeit, die Wärmeableitung zu verbessern, besteht darin, die Kupferstärke der Leiterplatte zu erhöhen. Einfach ausgedrückt: Dickeres Kupfer leitet die Wärme besser ab. Vergewissern Sie sich jedoch, dass die Abstände in Ihren Leiterplattendaten die Herstellung der Leiterplatte mit dickerem Kupfer zulässt. Ihr Leiterplattenlieferant weiß mit Sicherheit, wie viel Isolationsabstand Sie benötigen, so dass er immer eine wertvolle Anlaufstelle für diese Art von Informationen ist.

Wenn eine einfache Erhöhung der Kupferdicke die Anforderungen an das Wärmemanagement nicht erfüllen kann, besteht die Möglichkeit, die Leiterplatte mit der Copper-Coin-Technologie zu versehen. Am einfachsten lässt sich diese Technologie so beschreiben, dass sie wie ein diskreter Kühlkörper in die Leiterplatte eingebaut wird. Er wird direkt unter dem Bauteil positioniert, so dass er in Kontakt mit dem Bauteil ist. In einigen Fällen kann der Coin auch elektrisch mit dem Bauteil verbunden werden. Der Vorteil liegt hier in der besseren Wärmeübertragung und nicht in der einfachen Erhöhung der Kupferdicke. Einer der Nachteile ist die Anzahl der Copper-Coins, die auf einer Platte platziert werden können. Diese Anzahl ist von Hersteller zu Hersteller unterschiedlich, aber unabhängig vom Hersteller sollte man bedenken, dass jedes Mal, wenn ein Coin in eine Leiterplatte eingesetzt wird, eine Schwachstelle im Leiterplattenmaterial entsteht. Zu viele Schwachstellen können zu Verzug und ungewollten Folgen führen. Stellen Sie sich eine Leiterplatte in einer Umgebung mit Schock- und Vibrationsereignissen, welche zudem mehrere Copper-Coins aufweist vor.
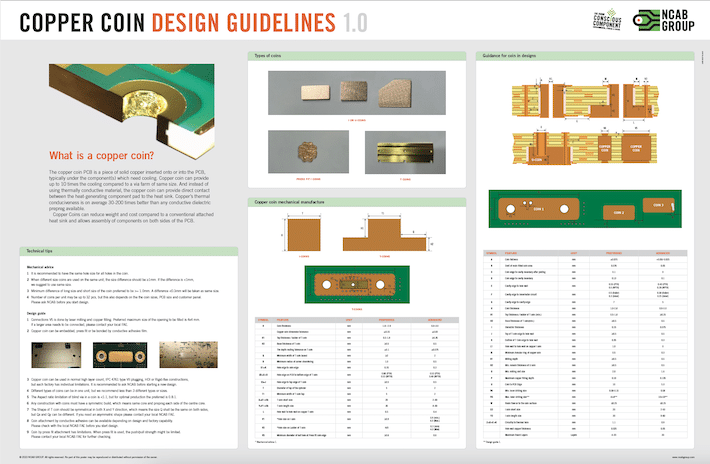
Anstatt die Leiterplatte mit zu vielen Copper-Coins zu gestalten, sollten Sie eine Metallkernkonstruktion in Betracht ziehen. Metallkerne können in den Stackup gepresst oder auf eine Lage gepresst werden, um eine optimale Wärmeableitung zu gewährleisten. Bei der Planung von Metallkernen sollten die dielektrischen Dicken sorgfältig berücksichtigt werden. Wir wollen ein möglichst dünnes Dielektrikum zwischen der Bauteilschicht und dem Metallkern verwenden. Dies liegt daran, dass dünnere Dielektrika eine geringere Wärmebeständigkeit aufweisen. Dieser Hinweis steht in direktem Widerspruch zu meiner Empfehlung, den Stackup so zu gestalten, dass er Stößen und Vibrationen standhält. Da die Leiterplatte immer komplexer wird, müssen wir jedes bewegliche Teil der „Maschine“ im Zusammenhang mit den anderen Komponenten betrachten.
Extreme Umgebungen setzen die Leiterplatten vielen neuen Gefahren aus, die wir berücksichtigen müssen, während andere Herausforderungen an Bedeutung zunehmen werden. Es ist schwierig, alles zu wissen, was man wissen kann, um die Effekte extremer Umwelteinflüsse auf unsere Leiterplatten zu mildern. Es bleibt zu hoffen, dass ein wenig hier und ein wenig dort dazu beiträgt, dass Sie eine robustere Leiterplatte entwerfen können. Der beste Rat, den ich Ihnen geben kann, ist, immer so früh wie möglich in der Designphase mit Ihrem Leiterplattenlieferanten zusammenzuarbeiten – er kennt sowohl die Designüberlegungen als auch die Fertigungsmöglichkeiten, um die Leiterplatte auf die effizienteste und nachhaltigste Weise zu entwerfen.