Découvrez les défis que les concepteurs de circuits imprimés doivent relever pour parer à la gestion thermique, à l’altitude, aux chocs, ainsi qu’aux vibrations.
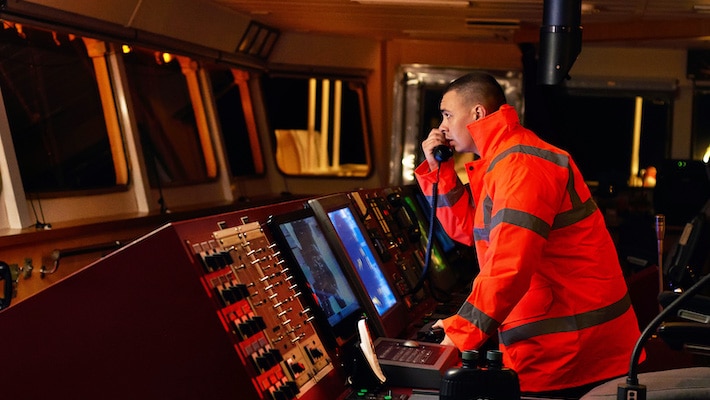
Dans la première partie de cet article, nous avons détaillé les applications et les défis auxquels les circuits imprimés sont confrontés dans les environnements extrêmes. Concevoir un circuit imprimé pour un environnement exigeant peut être une tâche intimidante car il y a de nombreuses considérations à prendre en compte. Les environnements extrêmes nécessitent une technologie robuste. En effet, l’altitude, les vibrations, les chocs et la chaleur affectent les systèmes électroniques dont nous dépendons tous les jours.
Changement d’altitude – comment cela affecte-t-il le circuit imprimé ?
L’un des défis que doivent relever de nombreux concepteurs de circuits imprimés concerne les effets de la densité de l’air sur le changement d’altitude. Sans entrer dans les détails, la densité de l’atmosphère devient plus légère à mesure que l’altitude augmente. Il existe une zone dans l’atmosphère entre la basse atmosphère et le vide absolu où il est possible créer un arc électrique à des tensions plus faibles. En d’autres termes, la tension de claquage de l’air dans l’atmosphère plus légère est plus faible. Cela permet à l’électricité de traverser les conducteurs à des tensions plus faibles qu’au niveau de la mer. Pour aggraver les choses, les charges s’accumulent plus rapidement à un point qu’à une surface plus ronde. Les charges qui s’accumulent peuvent potentiellement servir de points d’arc.
Il y a certaines choses que nous pouvons faire pour atténuer ce problème. Tout d’abord, consulter la section 6 de l’IPC-2221. Cette partie de la spécification du concepteur contient les « bonnes pratiques » en ce qui concerne le calcul de l’isolement électrique nécessaire. Une autre façon d’atténuer les effets d’arc électrique est d’arrondir les angles c’est-à-dire éliminer les angles vifs. Les ingénieurs peuvent également se pencher sur les pins de connexion. Étant donné que ces zones de la carte sont souvent associées à différents niveaux de tension, le risque d’arc électrique est également plus élevé à ces endroits. Parfois, des pins inutilisés sur le connecteur permettent d’obtenir un dégagement encore plus important si nous utilisons tous les autres pins.
Que se passe-t-il lorsqu’un circuit imprimé subit un choc extrême et des vibrations ?
Certains environnements soumettent les circuits imprimés à des chocs et des vibrations extrêmes. Les chocs extrêmes soumettent les PCB à une force de mouvement de grande amplitude pendant une courte durée. En revanche, les vibrations extrêmes contraignent les circuits imprimés sur des périodes de mouvement plus longues et de moindre amplitude. À leur tour, les oscillations sollicitent les matériaux de la carte et les points de connexion. Les matériaux sont soumis à des contraintes à l’endroit où le pré-imprégné adhère au cuivre. La métallisation des trous sont des points de connexion internes qui pourraient se fissurer, entraînant au mieux un fonctionnement intermittent. Il existe de nombreuses petites choses à faire pour atténuer les chocs et les vibrations. L’essentiel est de trouver le minimum de masse à ajouter au système tout en maintenant la stabilité mécanique. Outre le staking et le potting, voici quelques considérations relatives à la conception des circuits imprimés.
Conception de circuits imprimés résistants aux chocs et aux vibrations
Nous pouvons ajouter plus de trous de fixation dans la carte. Plus de trous de fixation signifie plus de points fixes sur le châssis et plus de stabilité. Cela permettra également d’ajouter plus de dispositifs d’amortissement dans le système.
Un autre aspect du circuit imprimé que nous voulons aborder est l’empilage. Pour les cartes qui seront soumises à des chocs ou des vibrations extrêmes, il est essentiel de s’assurer que le pré-imprégné contient suffisamment de résine pour résister à ces types de contraintes. La résine pré-imprégnée est la colle qui maintient l’ensemble des couches entre elles. Lors de chocs ou de vibrations, la carte peut plier et provoquer des tensions sur les points de connexion. Afin d’atténuer autant que possible les contraintes, nous devrions envisager d’utiliser des pré-imprégnés contenant plus de 50 % de résine. En outre, l’ajout de plus de deux pre-pregs est un autre moyen d’augmenter la force d’adhérence. En effet, les exigences en matière d’intégrité des signaux ne permettent pas toujours de changer facilement de diélectrique. Que se passe-t-il si vous n’avez pas d’exigences en matière d’intégrité des signaux ? Si trois feuilles de pré-imprégné sont bonnes, alors quatre doivent être meilleures, n’est-ce pas ? À un certain moment, trop de pré-imprégné sera préjudiciable à la registration entre les couches. Il vaut mieux s’en tenir à trois feuilles maximum, à moins que votre fournisseur de circuits imprimés ne vous dise le contraire. Si vous voulez plus d’épaisseur, mais que vous ne pouvez pas ajouter plus de pré-imprégné, envisagez d’utiliser des cores non cuivrés dans l’empilage. Contrairement au pré-imprégné, un core non cuivré est déjà polymérisé et n’ajoute donc pas de résine au cycle de pressage. La registration entre les couches n’est donc pas sacrifiée.
Attention également aux points de connexion internes. Lorsque le circuit imprimé oscille, la métallisation des trous oscille également. Lorsque le métal est soumis à des contraintes, il peut se fissurer. Certains circuits imprimés peuvent fonctionner à nouveau après avoir été ramenés à leur température de fonctionnement, tandis que d’autres peuvent subir une défaillance catastrophique. Dans tous les cas, il n’est pas toujours possible de récupérer le circuit imprimé en question. L’ajout d’une métallisation supplémentaire dans les trous n’est qu’un élément de plus à prendre en compte pour obtenir un circuit imprimé robuste. Cela ne fonctionnera pas pour toutes les applications.
Gestion thermique et circuits imprimés
Dans un circuit imprimé d’application non critique, le refroidissement passif tel que la convection, sera une solution de gestion thermique adéquate. D’autres PCB peuvent être fixés au châssis pour le transfert de chaleur, et certains peuvent être refroidis par d’autres dispositifs. Les circuits imprimés qui fonctionnent dans des environnements extrêmes ne peuvent pas toujours être refroidis par ces méthodes. Nous pouvons concevoir le circuit imprimé de manière à ce qu’il soit doté de solutions de refroidissement actives.
Un moyen simple d’atténuer la chaleur est d’augmenter l’épaisseur de cuivre du circuit imprimé. En clair, un cuivre plus épais dissipe mieux la chaleur. Par prudence, assurez-vous que les isolements électriques dans les données du PCB permettent de fabriquer le circuit imprimé avec du cuivre plus épais. Votre fournisseur de circuits imprimés connaîtra avec certitude les isolements dont vous aurez besoin, c’est pourquoi il est toujours une bonne source pour ce type d’information.

Si l’augmentation de l’épaisseur du cuivre ne suffit pas à résoudre les problèmes de gestion thermique, il est possible d’ajouter des copper coins. La façon la plus simple de décrire cette technologie est de dire qu’elle revient à intégrer un dissipateur thermique discret dans le circuit imprimé. Elle est placée directement sous le composant, de sorte qu’elle est en contact avec ce dernier. Dans certains cas, la pièce peut être connectée électriquement au composant. L’avantage ici est un meilleur transfert de chaleur plutôt qu’une simple augmentation de l’épaisseur de cuivre. Le principal inconvénient est que le nombre de copper coins est limité. Ce nombre varie d’un fabricant à l’autre, mais il convient de garder à l’esprit un point important, quel que soit le fabricant : chaque fois qu’une pièce est insérée dans un circuit imprimé, un point faible est créé. Or, un trop grand nombre de points faibles peut entraîner des déformations et des conséquences inattendues. Prenons l’exemple d’un environnement soumis à des chocs et à des vibrations, avec de nombreux copper coins dans une même conception.
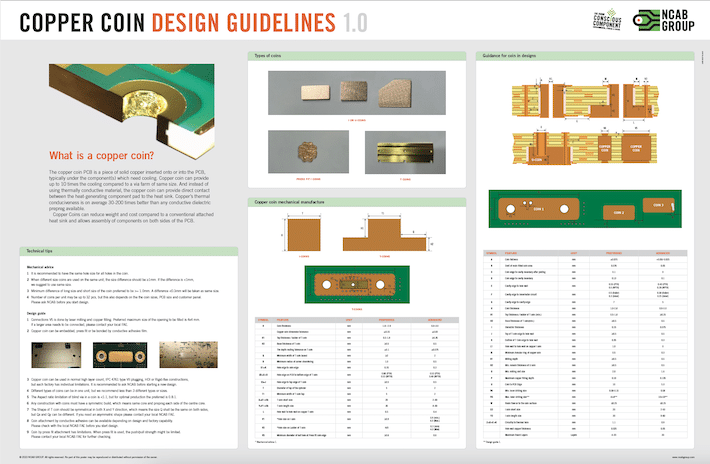
Plutôt que de concevoir des PCB avec trop de copper coins, il faut envisager la construction d’un core métallique. Les cores métalliques peuvent être pressés dans l’empilage ou sur une couche, afin de fournir la meilleure capacité de dissipation thermique. Lors de la planification des cores métalliques, les épaisseurs diélectriques doivent être soigneusement prises en compte. Nous voulons utiliser le diélectrique le plus fin possible entre la couche du composant et le core métallique. En effet, les diélectriques plus fins ont une moindre résistance à la chaleur.
Les environnements extrêmes soumettent les PCB à de nombreux risques dont nous devons tenir compte, tandis que d’autres défis vont s’amplifier. Nous espérons que cet article vous aidera à concevoir un circuit imprimé plus robuste. Le meilleur conseil que nous puissions vous donner est de toujours travailler avec votre fournisseur de circuits imprimés et ce, le plus tôt possible dans la phase de conception. Il connaît à la fois les exigences de conception et les capacités de fabrication pour vous aider à concevoir le circuit imprimé de la manière la plus efficace et la plus durable possible.