PCBs used in harsh and extreme environments will be exposed to extreme temperature, humidity, vibration, shock, and other conditions that can affect its performance and reliability. To design this kind of PCBs, you need to have the right knowledge and tools. In two blog posts we will talk about what defines extreme environments and how to design PCBs for these environments.
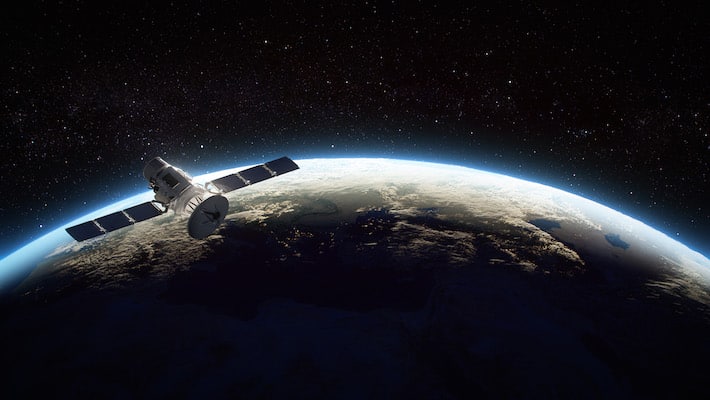
At the end of 2022 I completed IPC’s six-week IPC training certification, PCB Design for Military, Aerospace and Other Extreme Environments. This in-depth course provided me with the knowledge and tools to provide support to customers who are designing within these harsh and/or extreme environments. Whether it is for applications such as aerospace, military, or industrial, harsh environments can expose the PCB to extreme temperature, humidity, vibration, shock, and other conditions that can affect its performance and reliability.
I came away from this course with so much knowledge to share. In part one of this two-part series, I will first discuss the types of applications and product examples and the factors that result it being considered an extreme environment. Later in part-two, I will get more into tips and how to design for these environments with careful consideration of the operating conditions and selection of appropriate materials.
Applications and product examples
Aerospace
Inertial measurement unit (IMU) is an electronic device that is used to measure the orientation, velocity, and acceleration of an aircraft, spacecraft, or missile. They provide critical data for flight control and navigation, and are essential for maintaining safe and accurate flight operations in harsh aerospace environments.
Deep sea
Autonomous Underwater Vehicle (AUV) is a robotic vehicle that operate without a tether or remote control, using onboard sensors and navigation systems to navigate and perform tasks in deep sea environments. AUVs can be used for a variety of applications, such as underwater mapping, oceanography, and oil and gas exploration.
Down hole drilling
Measurement While Drilling (MWD) tools are electronic devices that are installed during drilling operations to measure various parameters, such as temperature, pressure, and wellbore trajectory. MWD tools transmit this data in real-time to the surface, allowing the driller to make decisions and adjust drilling parameters as needed.
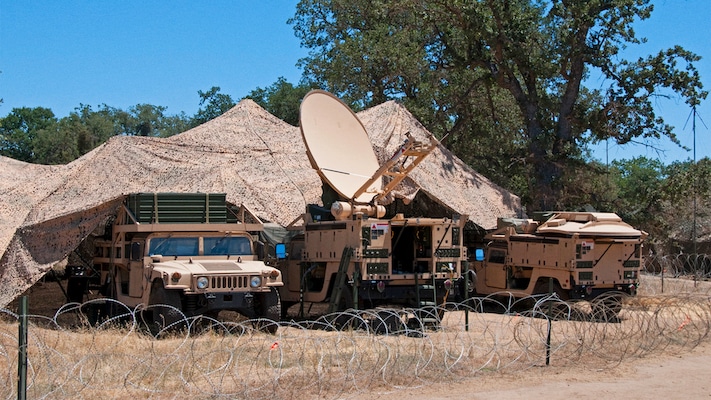
Defense
Ruggedized communication systems which are specialized electronic devices designed to withstand the extreme conditions of defense environments, such as extreme temperatures, humidity, shock, and vibration. They are built to operate reliably in harsh conditions and provide critical data and communication capabilities for defense personnel.
What the PCB can be subject to in these environments
There are various additional examples applications and countless products which are subject to environmental extremes. But now let’s take a look at the factors which the PCBs can be subject to in these environments.
Moisture and corrosion
Water and/or humidity can seep into the PCB and cause corrosion or oxidation, leading to deterioration of the PCB and its components over time. Specifically in underwater applications, the presence of saltwater can exacerbate this problem due to its corrosive properties.
Pressure
High pressure is widely found in these applications (e.g., deep sea, space). Depending on the depth and type of application, PCBs may be subjected to high pressure, which can affect the mechanical integrity of the PCB. In the vacuum of space PCBs experience many different problems due to the lack of atmosphere pressure.
Temperature
Here we’re not just concerned with high heat or below freezing temperatures. The variation of temperature in the ocean, or more impactfully, a satellite in space can vary greatly depending on its location and orientation relative to the sun. If a satellite is in direct sunlight, it can be subjected to extreme temperatures due to the intense heat from the sun. The temperature can rise to as high as 200°C (392°F) or more on the sun-facing side, while the shaded side can be as cold as -200°C (-328°F) or lower.
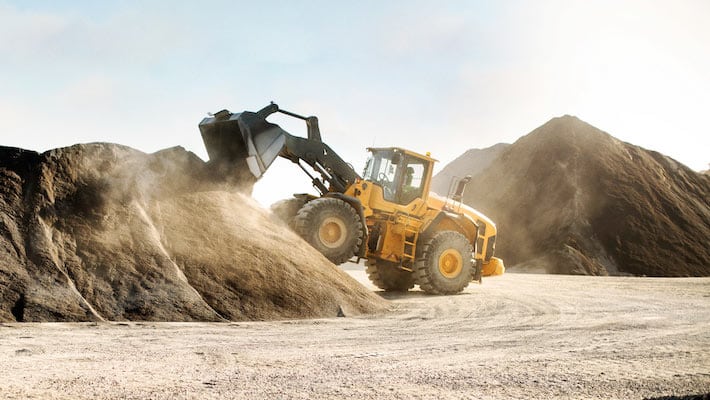
Vibration and shock
These applications may also subject the PCB to significant vibration or shock, which can cause damage to the PCB and its components. This could be high winds, or for example when I was in the US Airforce I would sit and watch F-16s take off on the runway. The speed and force at which they accelerate is incredibly powerful. A PCB needs to withstand that drastic and rapid acceleration.
EMI/RFI interference
Many of these environments can also subject the PCB to electromagnetic interference (EMI) or radio-frequency interference (RFI), which can affect the performance of the PCB and its components.
Other environmental hazards
Applications can also expose PCBs to a range of environmental hazards, such as wind, sand, dust, and debris. These environmental hazards can enter the PCB and cause damage or affect the performance of the PCB.
Reliable PCBs is necessary in extreme environments
Finally, let’s discuss perhaps the most important aspect in these applications. They need to be reliable. There is no compromise here. This is not my toaster that where I can go buy another or live without it if it’s defective or stops working. There cannot be any downtime. Did you know, it costs approximately $10,000 to put one pound of mass in space? We must design PCBs to ensure the safety and functionality of mission-critical electronic systems. The failure of even a single PCB can have significant consequences, ranging from equipment malfunction to loss of life, property, or mission-critical information. Therefore, PCB designers and suppliers must take extreme care to ensure that their products meet the high reliability standards required for these applications, which I will discuss more in part-two of this series.
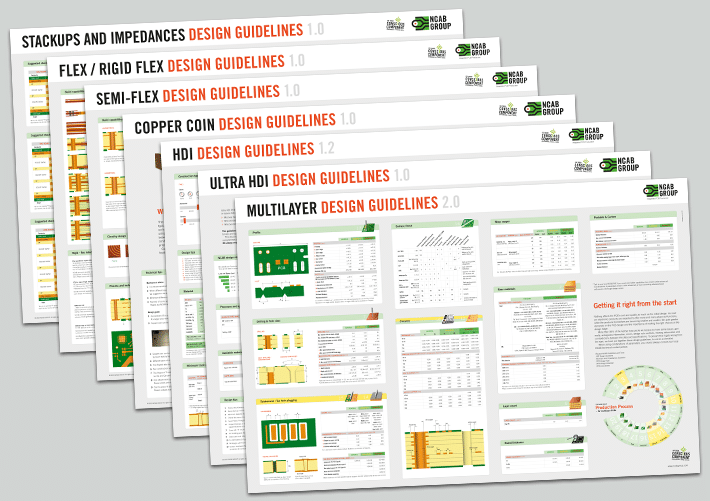
PCB design guidelines
Get it right from the start with our PCB design guidelines. To prevent getting it wrong from the start, we have put together our design guidelines, to use as a checklist.