I’ve noticed that our clients are understanding more and more that PCBs are the key component, but still have challenges communicating to their PCB suppliers what they want to build. When we receive Gerber files for an order there are times we cringe because we’re missing pieces of information necessary to make sure the PCB is made with zero defects. As we are in some trying and interesting times, the key component is still a relevant piece to consider. Here are some key factors I wish customers would consider before they send their files.
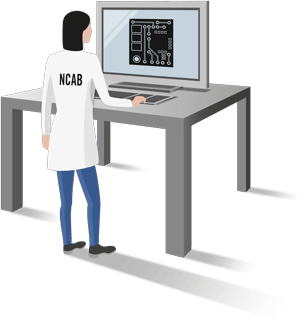
Update documentation to match the Gerber data
One of the first things I wish customers would recognize is the need to update their documentation to match the Gerber data. As a PCB designer finishes routing their last trace they’re eager to send off the board that they overlook including the finishing touches. We call these finishing touches the fabrication notes, or fab notes, and they’re often omitted. Have you checked if the revision is updated? Is a part number included to help differentiate? If you have generic notes for each board, do they apply to this one? While these checks won’t necessarily hold up a factory, it is a possibility. And don’t we want to be as precise as possible when designing such a complex product? All these factors can have an impact on the overall quality.
« If you have a drill table (in addition to a NC Drill file), make sure to update this so it matches the Gerber data. Your design software will update this with a click of a button, and that small action will reduce confusion and additional questions. »
The fabrication notes are also important for details like the drill table, board stackup, and dimensions. If these don’t match the Gerber files or are inconsistent, the factory will hold the board until the questions are resolved. This could waste hours or even days of time when a simple update can avoid this problem completely. If you have a drill table (in addition to a NC Drill file), make sure to update this so it matches the Gerber data. Your design software will update this with a click of a button, and that small action will reduce confusion and additional questions. The same goes with the board stackup file if it’s embedded into a Gerber file. The added benefit of this is when you export the Gerber as a PDF, you can easily refer to the fab notes to understand how many layers and holes your design has.
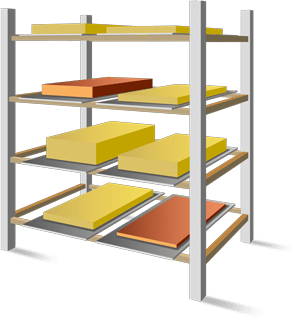
What are the materials needed to build the specific PCB?
Another thing I wish our customers would consider is the materials needed to build the specific PCB. While most boards default to FR4 material, we deal with some that have a specific material callout. This is great for understanding the customer application, but the drawback is when those materials are uncommon, it will cause increased lead times to obtain the material, or a factory will refuse to build the board altogether. This is more common with companies that have many years of experience in designing and/or building PCBs, but we also see it with engineers that are designing their first high-speed or high-Tg board. Keep in mind that the PCB manufacturing process is mostly chemical. There are so many steps that require proper chemical balances and new laminate materials create uncertainties. If possible, indicate whether or not equivalents are acceptable. I also recommend specifying material per IPC specifications, i.e. IPC 4101-126. If a factory recommends another material and they have experience with it, you can ask for the board stackup or impedance calculations to make sure both the designer and factory feel comfortable with proposed changes.
Updated design rules
A final thing I wish customers would do is update their design rules. These design rules assure the size of features like component pads, vias and traces. They also help with spacing between different features across the entire PCB.We’re always pushed to make things smaller and closer together, but you could be setting yourself up for failure if you’re not working with a suitable factory from the beginning. In order to design a board that is easily manufactured, ask for the factory’s design rules. That way the factory will know they can build a board with those specs under most conditions. Creating a quality PCB on time with zero defects is a team effort. While there are standard specifications, there are almost always exceptions as well.
Although a PCB is technical and precise, it is also a piece of art. Each one is unique and has variations to the rules. Helping your PCB supplier will save time that’s wasted clarifying information and asking additional questions. The actions I’ve mentioned should be implemented into your normal routine before releasing a board in order to obtain the best quality, on time and at the lowest total cost.
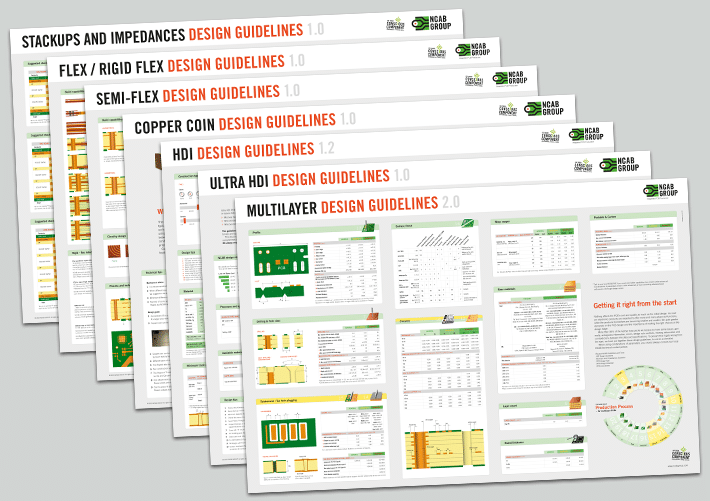
PCB design guidelines
Get it right from the start with our PCB design guidelines. To prevent getting it wrong from the start, we have put together our design guidelines, to use as a checklist.