Qui di seguito abbiamo elencato alcune delle domande che riceviamo con maggiore frequenza e aspetti che sono argomenti di discussione comune per la progettazione del circuito stampato.
HDI
Cos’è un foro microvia?
Secondo la nuova definizione dell’IPC-T-50M un microvia è una struttura cieca con un rapporto d’aspetto massimo di 1:1 la quale si connette ad una piazzola con una profondità totale non superiore a 0,25 millimetri, misurati dalla superficie esterna.
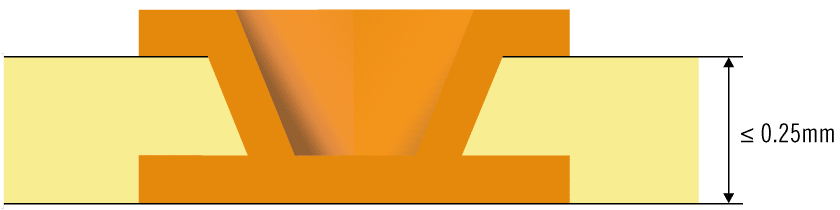
Cos’è un foro cieco?
È un foro che collega uno strato esterno con un solo strato interno, ma non attraversa l’intero PCB. Questi fori possono essere eseguiti meccanicamente od utilizzando la tecnologia laser. La figura al punto 1 mostra un foro cieco praticato con tecnologia al laser.
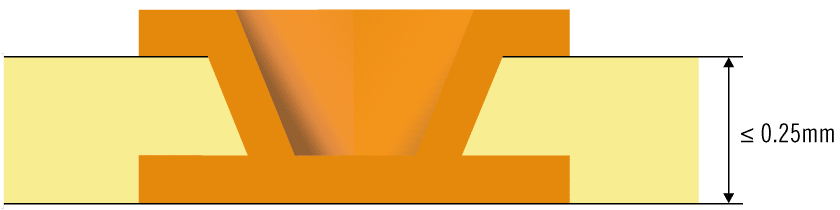
Cos’è un foro interrato?
Si tratta di un foro che collega uno o più strati interni. Solitamente viene praticato meccanicamente.
Cos’è un PCB HDI?
L’IPC-2226 definisce l’HDI come un circuito stampato con una maggiore densità di connessioni per unità di superficie rispetto ai circuiti stampati (PCB) convenzionali. Essi presentano piste e isolamenti più sottili ≤ 100 µm / 0,10 mm, vias più piccoli (<150 µm) e piazzole più piccole 20 pad/cm2) rispetto a quelli utilizzati nella tecnologia PCB convenzionale.
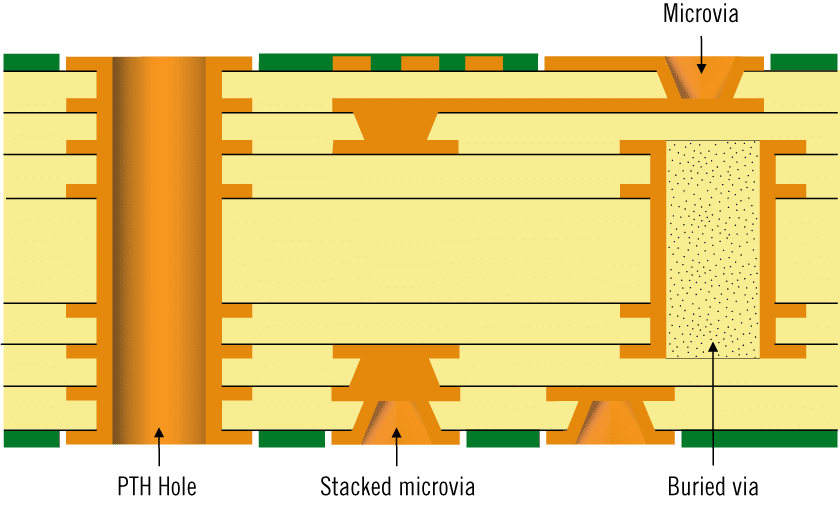
Che cos’è il PCB Ultra HDI?
Per essere definito Ultra HDI, il circuito stampato deve avere:
- Larghezza dei conduttori e distanza di isolamento inferiore a 50 µm
- Spessore del dielettrico inferiore a 50 µm
- Diametro della microvia inferiore a 75 µm
- Caratteristiche del prodotto che superano lo standard esistente IPC 2226 livello C
Per saperne di più su Ultra HDI, guardate questo video.
Esistono diversi tipi di caratteristiche HDI?
Il grafico seguente mostra le principali strutture – tipo I, tipo II e tipo III come definito dall’IPC-2226.
Tipo I. Definisce un singolo strato di microvia su uno o entrambi i lati del nucleo. Utilizza microvia placcati e PTH per l’interconnessione, adottando fori ciechi, ma non fori interrati.
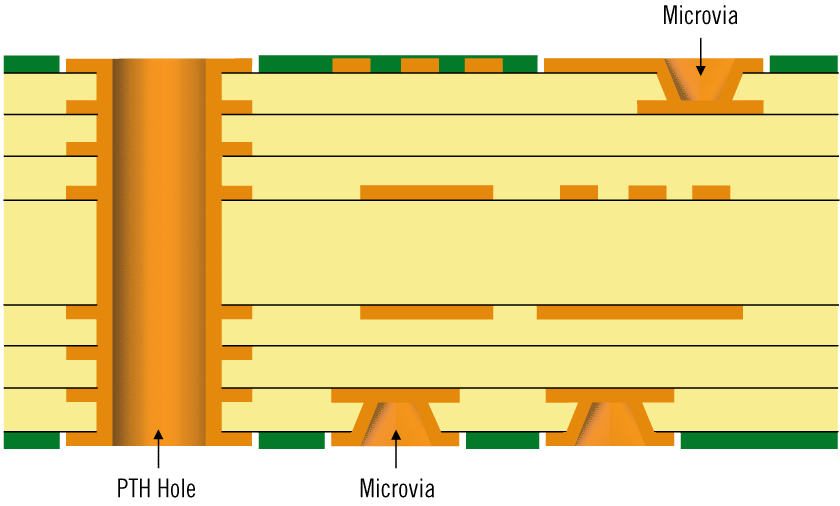
Tipo II. Definisce un singolo strato di microvia su uno od entrambi i lati del nucleo. Utilizza microvia placcati e PTH per l’interconnessione. Adotta fori ciechi e interrati.
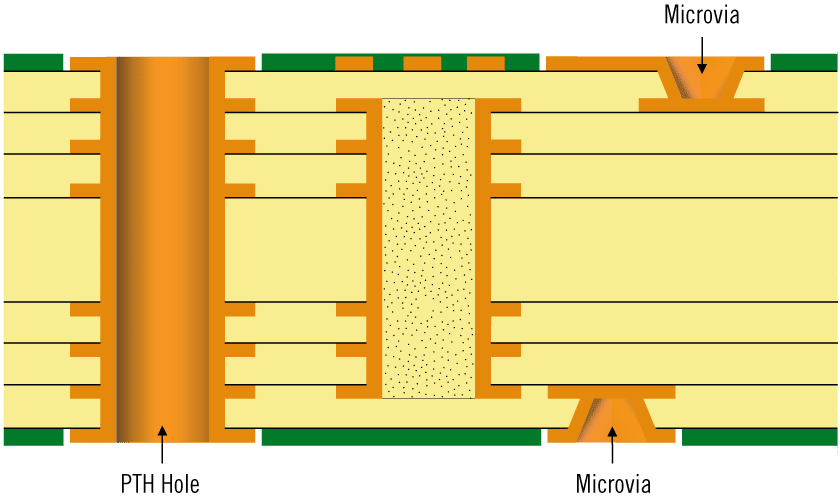
Tipo III. Definisce almeno due strati di microvia su uno od entrambi i lati del nucleo. Utilizza microvia placcati e PTH per l’interconnessione. Adotta fori ciechi e interrati.
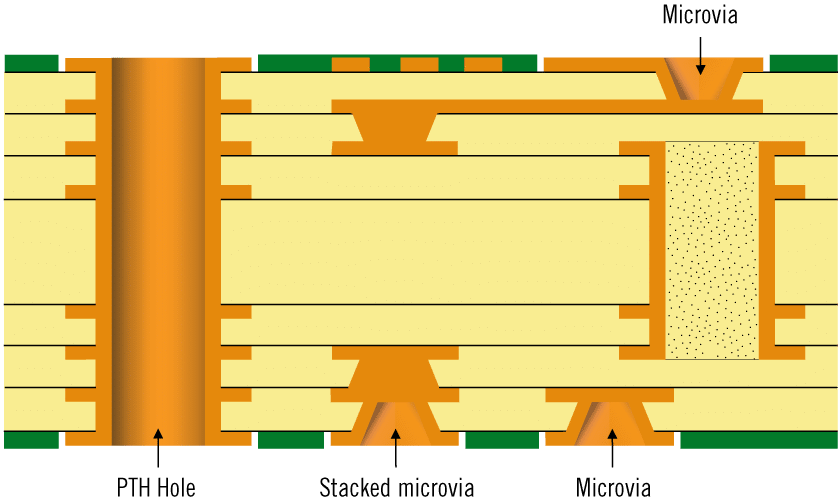
Terminologia di costruzione per definire la complessità strutturale dell’HDI:
- 1+n+1 = singolo strato di microvia (come da esempi del tipo I e tipo II riportati sopra)
- 2+n+2 = 2 strati di microvia (come da esempio del tipo III riportato sopra)
- 3+n+3 = 3 strati di microvia
REGOLE DI PROGETTO
Quali sono le strutture disponibili per circuiti stampati flessibili e rigido flessibili ?
Sono disponibili numerose e differenti strutture. Le più comuni sono definite di seguito:
Flessibile mono faccia (ipc-6013 tipo 1) laminato di base poliammide senza adesivo con Coverlay (poliammide + adesivo) con o senza irrigiditore

Flessibile doppia faccia (IPC-6013 tipo 2) laminato di base poliammide senza adesivo a fori passanti metallizzati, con Coverlay (poliammide + adesivo) con o senza irrigiditore

Multistrato flessibile (IPC-6013 tipo 3) laminato di base poliammide senza adesivo a fori passanti metallizzati, con Coverlay (poliammide + adesivo) con o senza irrigiditore, max 4 strati
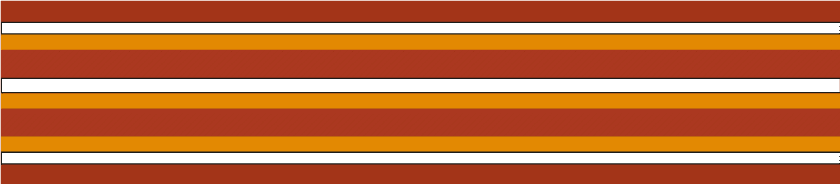
Multistrato rigido flessibile (IPC-6013 tipo 4) costruzione tradizionale con laminato di base senza adesivo, con tre o piu strati a fori passanti metallizzati, capability 22 strati, di cui 10 strati flessibili
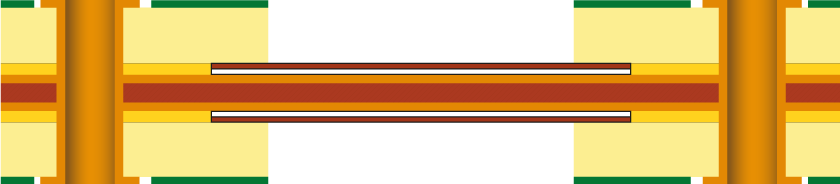
Costruzione flessibile asimmetrica, in cui il layer flessibile è situato sullo strato esterno della costruzione rigida. Contiene tre o più strati con fori passanti metallizzati.
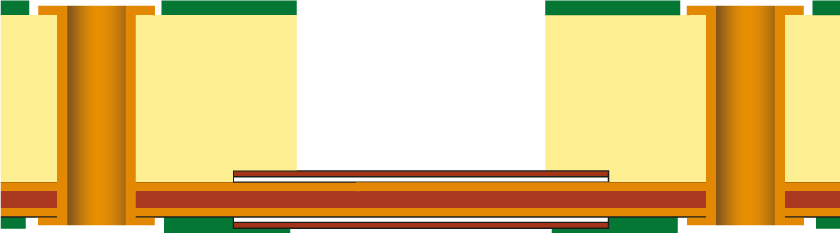
Multistrato rigido flessibile, struttura sulla zona rigida con fori interrati / ciechi (microvia). È possibile 2 strati di microvia. La costruzione può anche comprendere due strutture rigide quale parte di una conformazione omogenea. La capacità è struttura HDI 2+n+2.
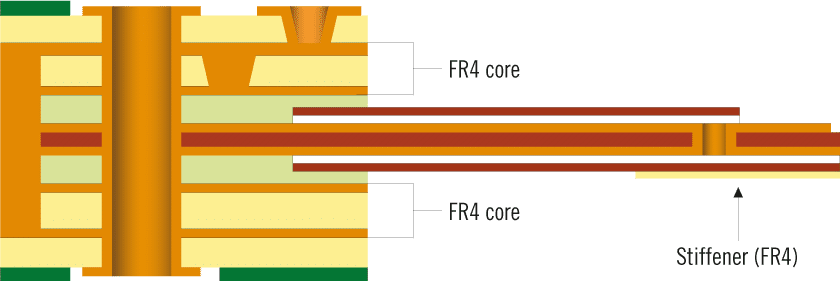
Struttura complessa a coppie separate, con spazi tra gli strati flessibili del circuito stampato, per consentire migliore flessibilità. Gli strati flessibili possono essere di differenti lunghezze nelle costruzioni complesse, questo per ridurre al minimo la compressione degli strati flessibili interni entro il loro raggio di curvatura.
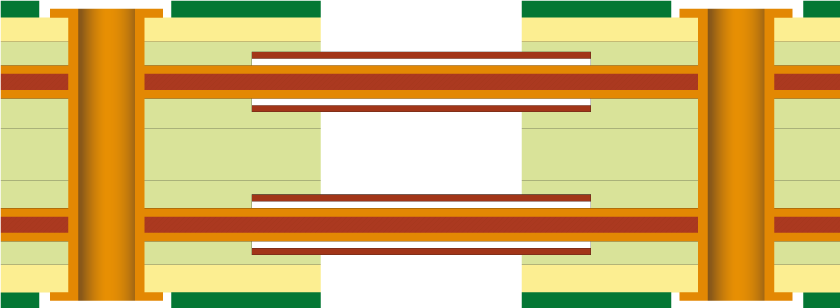
Come si calcola la giusta lunghezza della parte flessibile di una struttura rigido flessibile per consentire il raggio di curvatura minimo?
Raccomandazioni dettagliate sono disponibili sulle IPC-2223, sezioni 5.2.3.3 riguardo al raggio di curvatura sia statico che dinamico, e devono essere utilizzate per la verifica finale del progetto. Tuttavia, di seguito sono riportate alcune linee guida basate sullo spessore del materiale flessibile:

FLEX TYPE | MINIMUM BEND RADIUS |
---|---|
Single sided flex | 3 – 6 x circuit thickness |
Double sided flex | 7 – 10 x circuit thickness |
Multilayer flex | 10 – 15 x circuit thickness |
Dynamic application | 20 – 40 x circuit thickness |
Qual è la differenza tra semi-flessibile e rigido flessibile?
Il circuito stampato semi-flessibile è in effetti un PCB multistrato “standard”, costruito utilizzando specifici tipi di laminati FR4, nelle zone flessibili viene lavorato meccanicamente a profondità controllata con una specifica tolleranza in modo che l’area risultante offra una sezione flessibile e un buon raggio di curvatura. Il circuito stampato semi-flessibile è adatto ad applicazioni statiche, o con numero di curvature molto limitato.
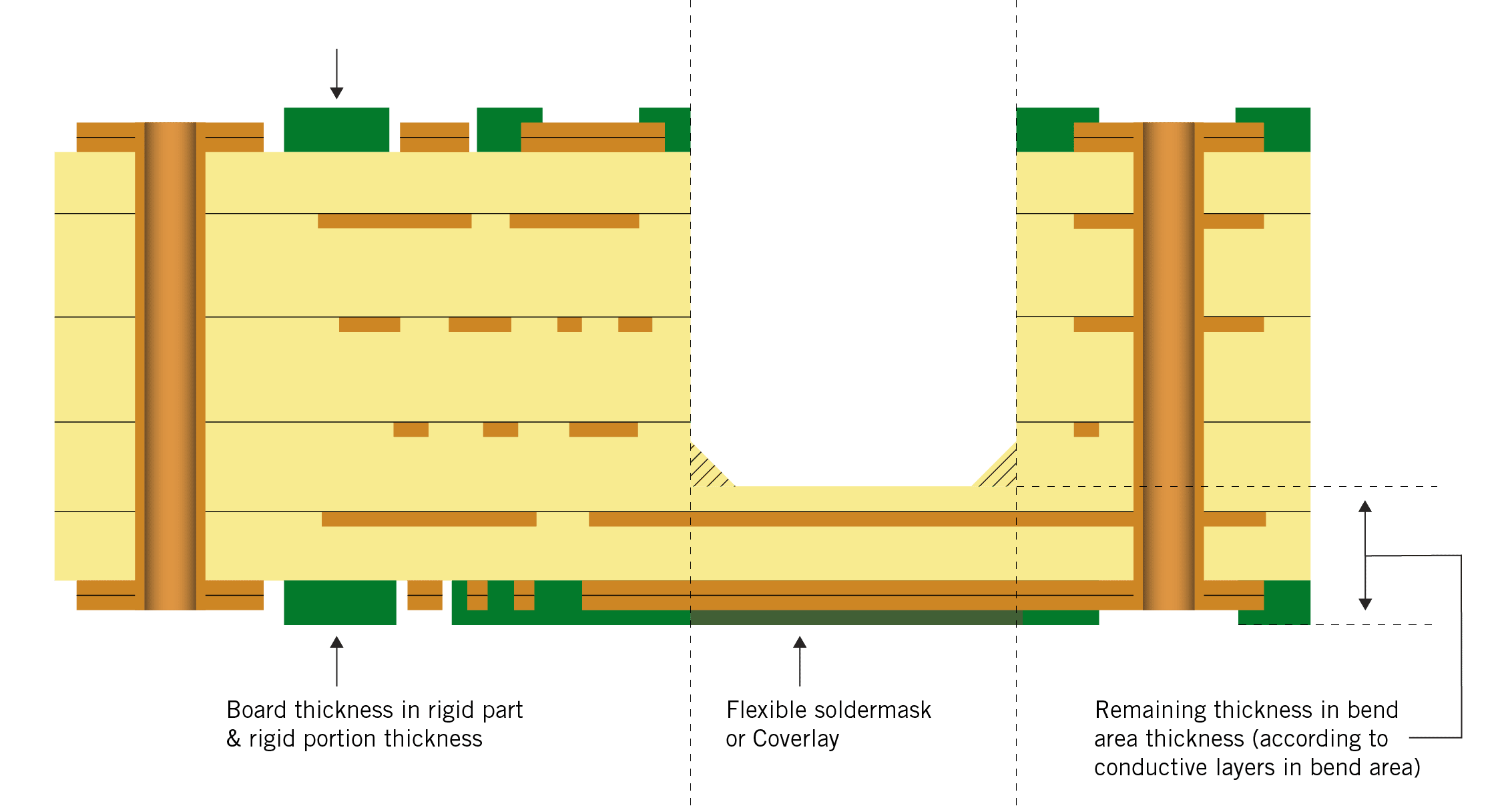
Qual è la differenza tra strutture flessibili con adesivi e senza adesivo?
I circuiti stampati che utilizzano laminati con adesivi si affidano all’adesivo per far aderire il rame al substrato. In quanto tale, questo adesivo insieme a coverlay totale, penetra nella struttura rigida e direttamente nel foro. Il maggiore coefficiente di espansione dell’adesivo aumenta il rischio di problemi dei fori passanti, come la criccature del rame depositato, e successivi malfunzionamenti dei fori di via in conseguenza all’espansione, mentre la presenza di questo materiale all’interno del foro stesso può provocare problemi nella formazione di rame della parete del foro, dovuti a scarso desmearing dell’adesivo.
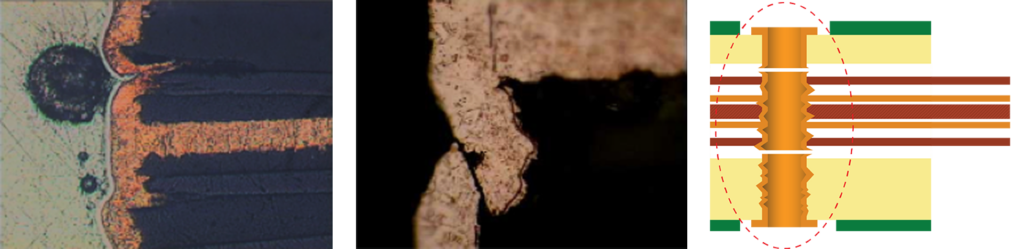
La soluzione per migliorare l’affidabilità del foro passante è stato il passaggio all’utilizzo di laminato senza adesivo tra il supporto e il copper foil (rame attaccato direttamente al supporto di base poliammide, in fase di laminazione) e limitare la sovrapposizione del coverlay nella parte rigida della scheda. Questo assicura una struttura a fori passanti molto più affidabile, senza adesivo che penetra nei fori. Si tratta dell’approccio di gran lunga più diffuso al flessibile rigido.
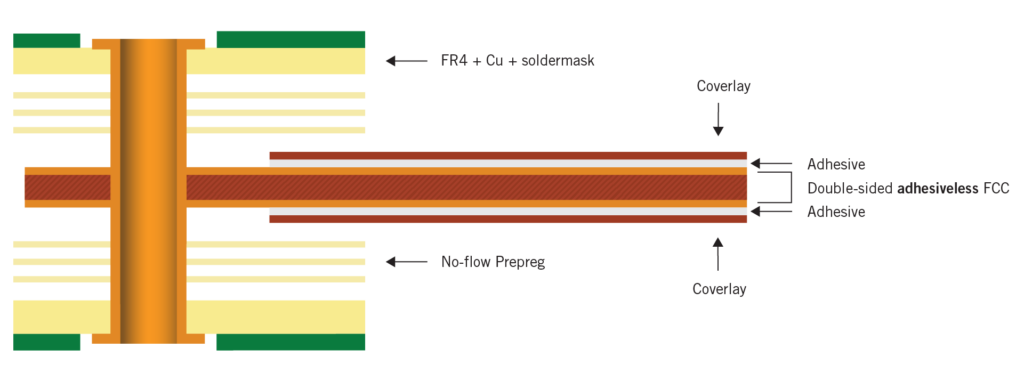
REGOLE DI PROGETTO
Qual è la dimensione minima del foro praticato sulla piazzola dello strato esterno/interno?
Questo aspetto varia da produttore a produttore, ma in generale si può affermare che la maggior parte dei produttori è in grado di praticarli come segue:
A = 0.15 mm
B = 0.20 mm
C = 0.30 mm
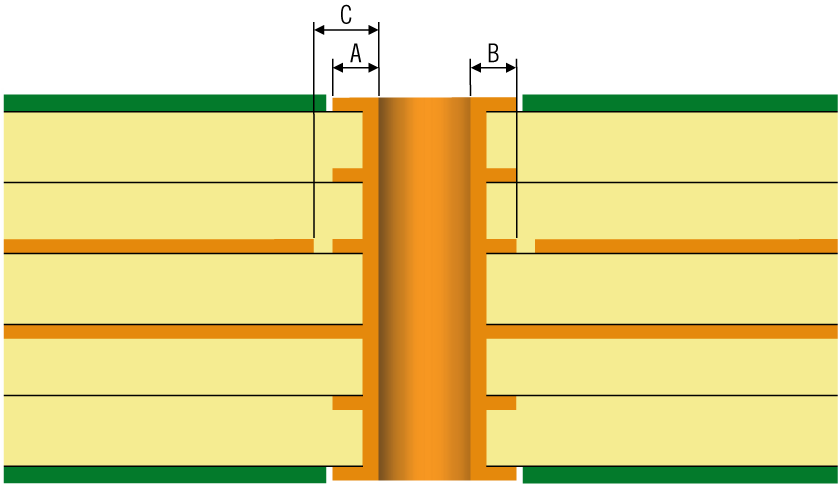
Quando ho l’esigenza di piste di spessore superiore a quelle standard, quali larghezze posso adottare?

In generale, quanto maggiore è lo spessore della base di rame, tanto più ampia dovrebbe essere la pista. Una regola empirica prevede che con rame base da da 18 micron, la pista non deve essere più stretta di 0,1 mm (4 mil) e con rame base da 105 micron la pista non deve essere più stretta di 0,25 mm (10 mil).
Quale spessore di rame finito possiamo aspettarci?
Vi è l’errata convinzione che a determinati pesi di rame corrispondano spessori esatti e che essi non si riducano durante la produzione di un PCB. Ad esempio 1 oz. = 35 um o ½ oz. = 18 um. In realtà l’IPC-6012 presenta in dettaglio lo spessore minimo accettabile delle lamine di rame e delle lamine dopo la placcatura in base alle tolleranze ammissibili, nonché le riduzioni della placcatura di rame durante la successiva lavorazione.
Qui di seguito mostriamo alcuni dei pesi di rame più diffusi e gli spessori finiti ammissibili.
Pertanto è fondamentale capire ciò di cui avete bisogno e specificarlo correttamente. In caso contrario sussiste il rischio di sovrastimare o sottostimare, il che può portare a costi eccessivi a seguito di un’errata progettazione del circuito stampato. Per maggiori informazioni vi invitiamo a consultare i nostri tecnici.
Spessore lamina dello strato interno dopo la lavorazione | |
Peso del rame di base | Minimo finito dopo la lavorazione |
1/2 oz. | 11.4 um |
1 oz. | 24.9um |
2 oz. | 55.7um |
Spessore conduttore esterno dopo placcatura e lavorazione | ||
Base copper weight | Minimo finito dopo la lavorazione Classe 2 | Minimo finito dopo la lavorazione Classe 3 |
1/2 oz. | 33.4um | 38.4um |
1 oz. | 47.9um | 52.9um |
2 oz. | 78.7um | 83.7um |
Le piazzole non funzionali devono essere rimosse o lasciate ?
In IPC-2222A punto 9.1.4 si stabilisce espressamente che il produttore non deve rimuoverle, ma molti stabilimenti chiedono di fare un’eccezione e di rimuoverle per ottenere una migliore resa nella produzione. Se non sono fondamentali per la funzione prevista, si consiglia di prendere in considerazione l’idea di consentirne la rimozione.
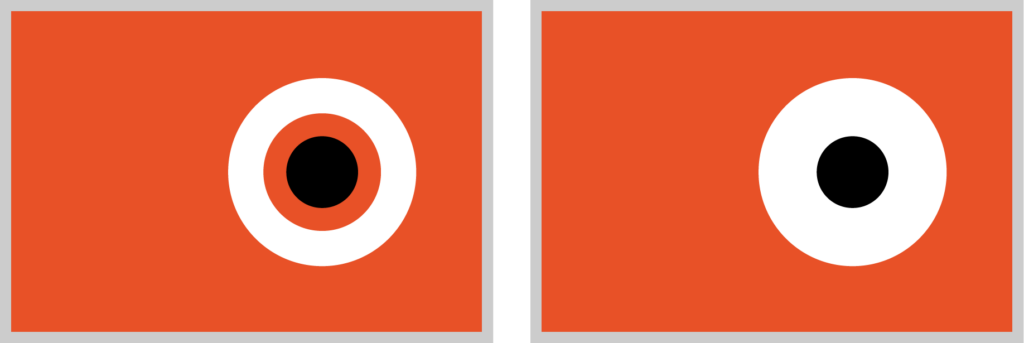
Cosa significa isolamento nella stessa net?
“Distanza nella stessa net” significa che la distanza tra rame e rame, all’interno della stessa net è troppo vicina per poter essere prodotta secondo i file Gerber. Poiché si tratta della stessa net, il DRC (Design Rule Check) del software CAD del cliente non rileva questo errore. È importante che il cliente imposti i limiti corretti quando inizia un nuovo progetto. La distanza minima tra rame e rame è normalmente impostata in modo corretto, ma si dimentica di impostare lo stesso valore all’interno della stessa net. Non è un problema grave, ma causa ritardi e domande tecniche inutili.
Perché è richiesta una distanza così grande dal bordo del foro al rame per i fori non placcati (NPTH)?
Quando si eseguono i fori nel circuito stampato, si desidera eseguire tutti i fori nello stesso set up per ottenere la migliore precisione di posizione dei fori. I fori non placcati devono poi essere protetti durante il processo di placcatura (altrimenti saranno anch’essi placcati). Per poter ottenere la protezione del NPTH è necessario uno spazio tra il bordo del foro e il rame. La distanza necessaria è legata allo spessore del rame. Per uno spessore di rame standard (rame di base 18µm), un buon valore è di 0,3 mm e sicuramente non inferiore a 0,2 mm.
TERMINOLOGIA
Cos’è l’“aspect ratio”?
Il rapporto tra il diametro del foro e la sua lunghezza. Quando un produttore afferma che la sua produzione ha un “rapporto” di 8:1, ciò significa, per esempio, che il diametro foro è di 0,20 mm in un PCB dello spessore di 1,60 mm.
Per strutture HDI, la proporzione adatta per microvia è normalmente 0,8:1, con 1:1 preferibile per la facilità di placcatura.
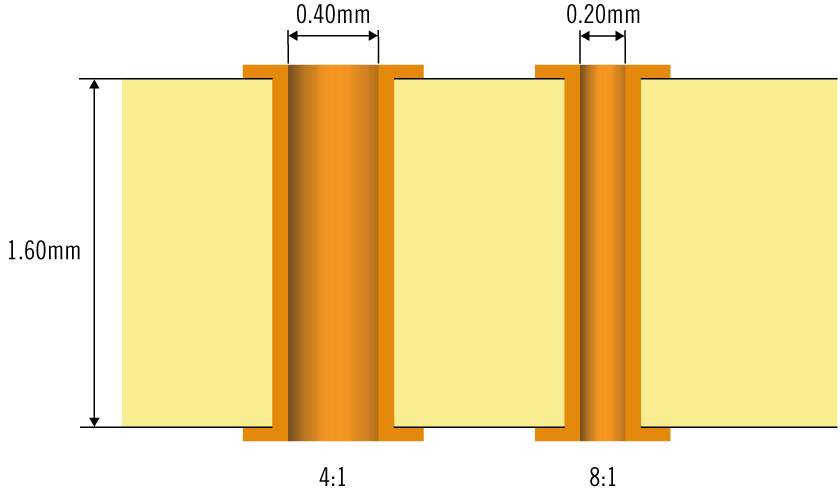
Cos’è la placcatura di rame?
La placcatura di rame è lo strato continuo di rame placcato che è depositato nella parete del foro e che si estende sulla superficie del PCB (o la superficie del nucleo dello strato interno se parte di una struttura HDI) per un minimo di 25 um.
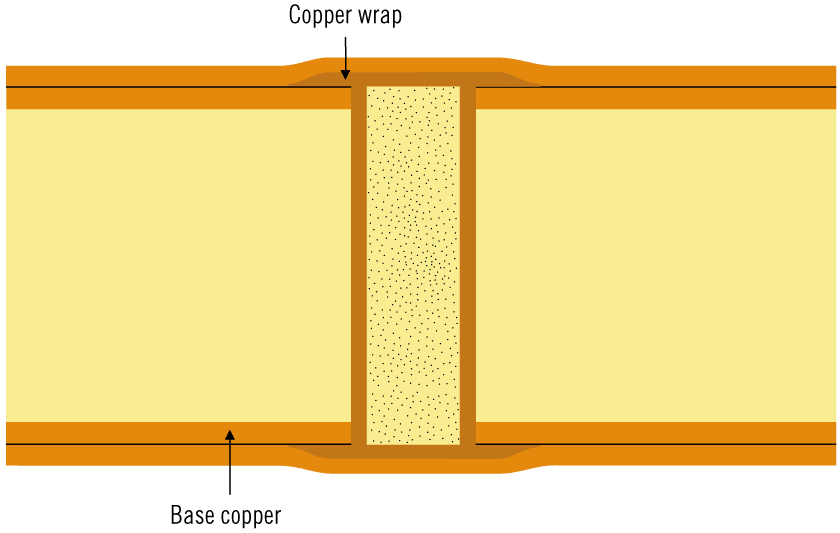
Per i requisiti di classe 2 lo spessore del deposito di superficie della placcatura in rame è di un minimo di 5 um, mentre per i requisiti della classe 3 esso può variare in base alla localizzazione della caratteristica ed alle situazioni interne alla struttura. Per ulteriori informazioni sui requisiti della classe 3 vi preghiamo di consultare i nostri tecnici.
Che cos’è un circuito stampato con il copper coin?
Un PCB con il copper coin è un circuito stampato multistrato ma con l’aggiunta di un pezzo solido di rame, chiamato coin, incorporato nello stack-up del PCB. Ciò consente una connessione termica diretta da un lato all’altro o da uno strato specifico a uno strato esterno.
Cos’è l’impedenza controllata?
Controllare un segnale che viaggia lungo una pista a impedenza controllata, significa controllare le prestazioni e la velocità di tale segnale in un punto lungo il tracciato, in termini di capacità e conducibilità elettrica della pista in questione L’impedenza è misurata in Ohm, è diversa dalla resistenza, che è invece una caratteristica della corrente continua. L’impedenza è una caratteristica della corrente alternata, ciò significa che è relativa alla frequenza.
Esiste più di un tipo di impedenza controllata?
Sì e sono illustrati di seguito.
Impedenza differenziale – impedenza di una coppia di conduttori con segnali di polarità uguali e opposti – stessa ampiezza in anti-fase tra loro.
Impedenza modalità dispari – impedenza di un lato di una coppia di conduttori, entrambi i quali hanno segnali di polarità uguale e opposta – stessa ampiezza e anti-fase.
Impedenza modalità pari – impedenza di un lato di una coppia di conduttori che hanno segnali uguali – stessa ampiezza e stessa polarità.
Impedenza modalità comune – impedenza di una coppia di conduttori che hanno segnali uguali – stessa ampiezza e stessa polarità.
Che cosa si intende con “piazzola termica”?
Per i componenti montati in superficie (SMD), specialmente quelli più piccoli, utilizzare delle piazzole di scarico termico per simulare la stessa massa termica su entrambe le terminazioni, evita l’effetto tombstoning (lapidazione), componenti attorcigliati o persino, nel caso peggiore, la rottura degli stessi per effetto termico.
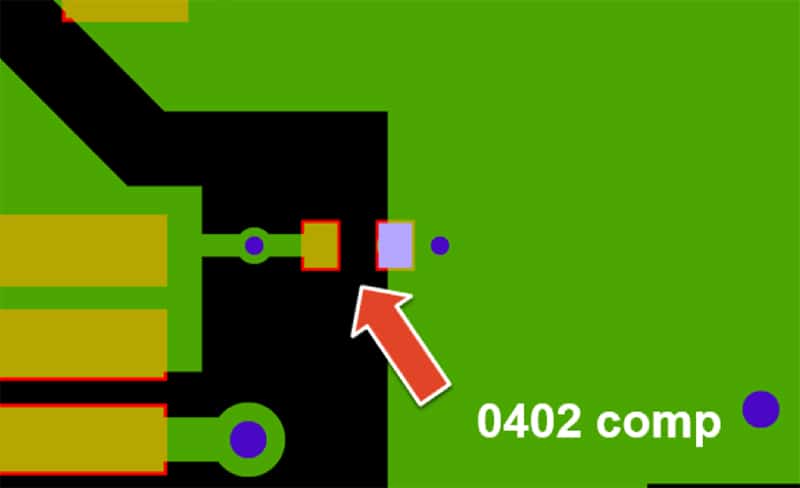
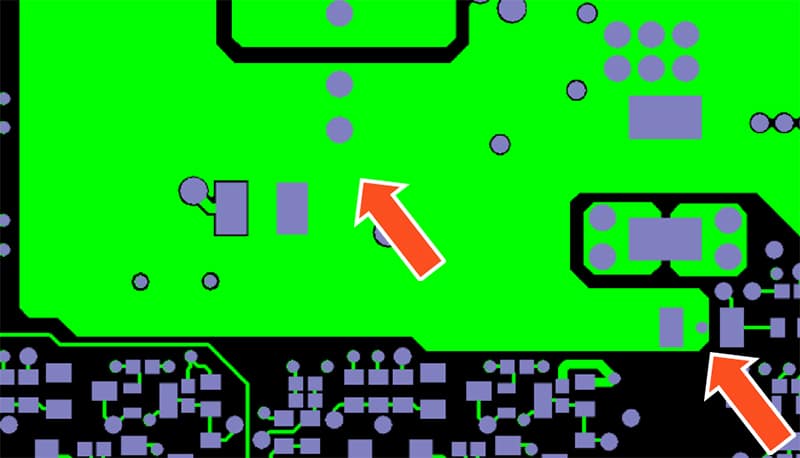
Per i componenti montati su foro (HMD), utilizziamo piazzole di scarico termico nei piani interni degli strati, per contribuire alla bagnabilità del foro. Le formule per le piazzole di scarico termico si possono consultare nella serie IPC-2220.
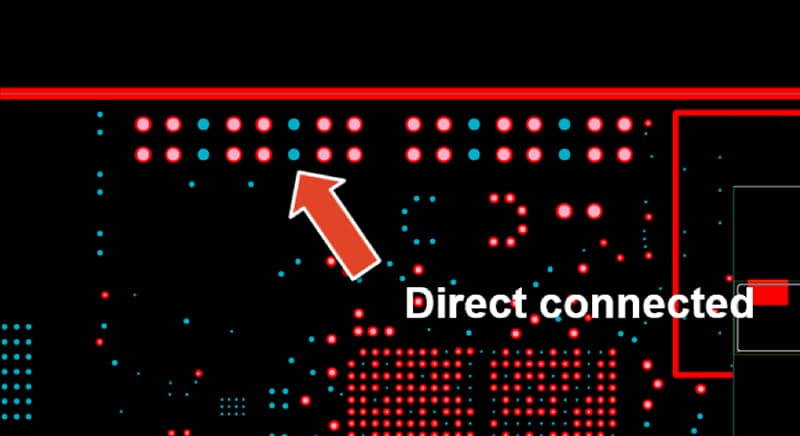
Nella documentazione tecnica di fornitura deve essere aggiunta l’approvazione per l’aggiunta di teardrop?
Secondo le nuove IPC-6012D, sezione 3.4.2, è consentito aggiungere i teardrops al tracciamento quando le schede devono essere conformi alle classi 1 e 2.
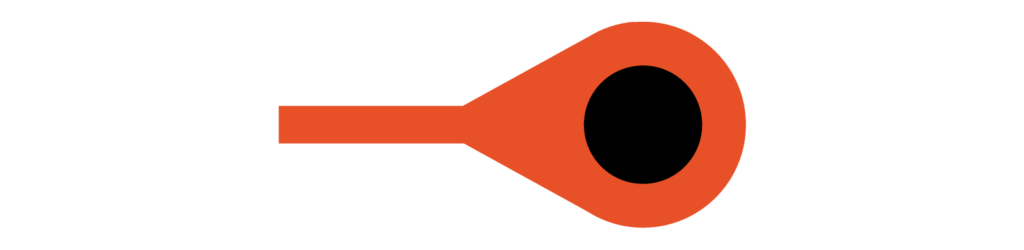
Se non si vogliono teardrop, evidenziarlo nella documentazione di fornitura. Aggiungere comunque una sufficiente corona circolare.
Che cos’è la tecnologia del back-drilling ?
Nelle applicazioni ad alta frequenza occorre evitare la perdita di segnale in tutti gli aspetti del progetto; quindi quando due strati sono collegati e il segnale deve passare da uno strato all’altro, deve attraversare un foro passante che li collega.
Nelle applicazioni ad alta frequenza è fondamentale evitare la perdita di segnale; quindi quando due strati sono collegati e il segnale deve passare da uno strato all’altro, deve attraversare un foro passante che li collega.
Per esempio, se il segnale deve passare dallo strato 1 allo strato 2 in una scheda elettronica da 20 strati, parte della struttura del foro di via è considerata come “eccesso”; per questa applicazione la soluzione migliore è rimuovere dal foro il rame in eccesso, perché funge da antenna e incide sul segnale.
Utilizziamoquindi la tecnologia del back-drilling (profondità controllata nell’asse z) perrimuovere con macchine di foratura il rame in “eccesso” presente nelforo, quindi riduciamo il cilindro del foro metallizzato alla massimaottimizzazione ed ottenere cosi una migliore stabilità del segnale. Idealmente,quanto più corto è il residuo (il rame in “eccesso”), tanto miglioreè il risultato.
La dimensione di unforo back-drill deve essere in genere 0,2 mm più grande del foro di viacorrispondente.
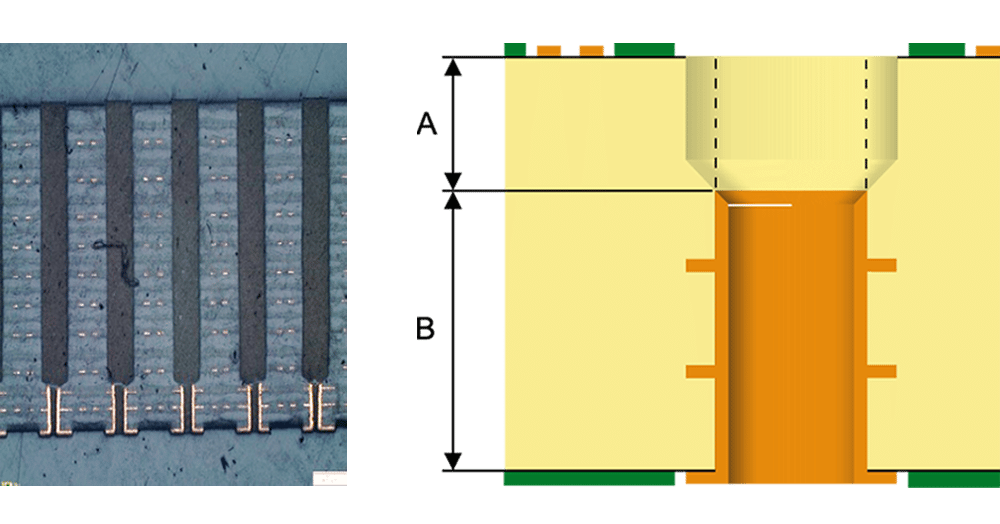
BACK DRILLING / COUNTER BORE (mm) | |||
---|---|---|---|
A: Depth tolerance | +/-0.20 | +/-0.15 | +/-0.10 |
B: Min. remain thickness and tolerance | 0.5+/-0.25 | 0.35+/-0.1 | 0.3+/-0.1 |
Che cos’è la resistenza termica?
In questo video potete imparare a conoscere la resistenza termica e la conduttività termica.
Cosa significa “marcatura UL”?
La sicurezza è cruciale nell’industria elettronica. Quando si parla di fattori come sicurezza antincendio ed elettrica, è fondamentale che gli utenti possano fare affidamento sul prodotto finito. Ciò significa che sia i circuiti stampati che i materiali in essi contenuti devono essere all’altezza degli standard più elevati. Per garantire che le schede siano conformi, è diventata prassi comune certificare i materiali costitutivi o il PCB stesso, a norma UL.
Tanto per cominciare, che cos’è UL? Le lettere UL sono l’acronimo di Underwriters Laboratories. Perché è importante il riconoscimento UL? UL è un ente di certificazione molto importante e gode di buona reputazione nel settore del circuito stampato. Si tratta di un ente di certificazione insostituibile nel testare la sicurezza antincendio ed elettrica dei PCB. I clienti di tutto il mondo, comprese aziende cinesi molto conosciute, richiedono che gli stabilimenti di produzione siano in grado di ottenere il riconoscimento UL per i propri prodotti. Avere il riconoscimento UL è perciò molto importante per gli stabilimenti di circuiti stampati per produrre schede elettroniche sicure ed essere in grado di accedere al mercato internazionale.
VIA HOLE
Quale tipo di tappatura è raccomandata per il foro via?
La tipologia preferita di tappatura per il prodotto standard (che non include il foro di via “capped”) è il tipo VI IPC 4761 riempito e rivestito, con l’obiettivo del riempimento completo. L’immagine presentata sotto mostra il tipo VI con copertura della maschera di saldatura liquida.
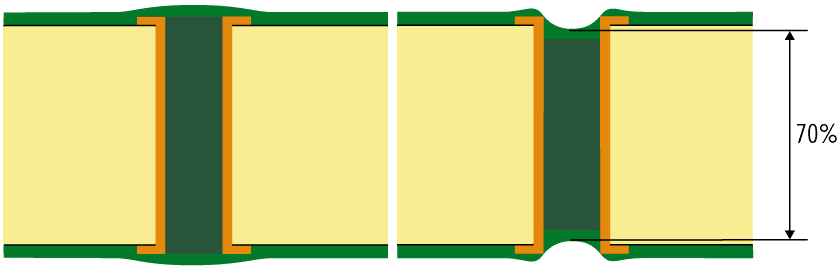
La tappatura su lato singolo non è raccomandata (compreso tipo II tendinato e rivestito) per via del rischio di deposito di prodotti chimici o della presenza di sfere di saldatura nelle finiture HASL (Lead free e SnPb).
Cos’è un foro di via capped?
La tecnologia capped via prevede il riempimento dei fori dopo la placcatura degli stessi, in modo che la superficie sia completamente metallizzata con un spessore minimo di rame/placcatura di 5 um per i requisiti di classe 2, o 125 um per i requisiti di classe 3.
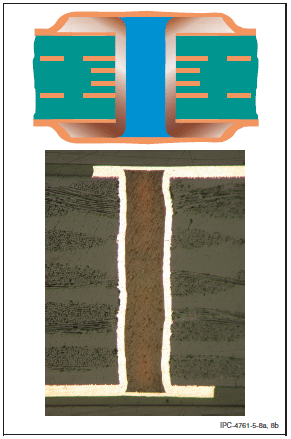
Si muove dall’assunto che il materiale di riempimento sia resina epossidica anziché maschera di saldatura, poiché la resina epossidica riduce al minimo il rischio di soffiature o l’espansione del riempimento durante le operazioni di saldatura. Ciò può essere classificato in IPC-4761 come fori di tipo VII – filled e capped via. Solitamente questa tecnologia viene utilizzata per progetti con applicazioni “via in pad” o BGA, in cui sono richieste caratteristiche di elevata densità.
MATERIALE
Per la saldatura senza piombo devo utilizzare un materiale FR4 con un Tg elevato (Tg = temperatura di transizione vetrosa)?
No, non necessariamente. Ci sono molti fattori da tenere in considerazione, ad esempio il numero di strati, lo spessore del PCB ed anche una buona comprensione del processo di assemblaggio (numero di cicli di saldatura, durata delle temperature superiore a 260 gradi, ecc.). Alcune ricerche hanno dimostrato che un materiale con un valore Tg “standard” ha fornito prestazioni addirittura migliori rispetto ad alcuni materiali con un valore Tg più elevato. Si noti che il valore Tg viene superato anche con la saldatura a piombo.
L’elemento di maggiore rilevanza è il comportamento del materiale a temperature superiori al valore di Tg (post Tg); così, conoscere i profili di temperatura a cui la scheda sarà sottoposta vi aiuterà a valutare le caratteristiche prestazionali necessarie.
Quali caratteristiche considerare nella scelta del materiale del circuito stampato?
Le principali caratteristiche che prenderemmo in considerazione per prime includono:
CTE
Una misura della capacità di dilatazione termica di un corpo. Critica in asse Z – tipicamente superiore alla Tg e l’espansione è maggiore. Se la CDT è insufficiente possono verificarsi dei guasti durante l’assemblaggio, perché il materiale si espande rapidamente al di sopra della Tg.
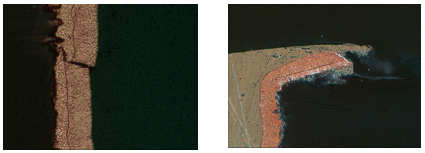
I materiali possono avere la medesima Tg ma una diversa CDT – È preferibile una CDT più bassa. Allo stesso modo alcuni materiali possono avere valori di Tg più elevati, ma anche una CDT più elevata (eventualità peggiore) post Tg.
Tg / TEMPERATURA DI TRANSIZIONE VETROSA
Il valore Tg è la temperatura alla quale il materiale si modifica, passando dallo stato di materiale simile al vetro con ragionevole rigidità ad un materiale più elastico e flessibile, simile alla plastica. Questo è un fattore importante, perché al di sopra della Tg le proprietà dei materiali cambieranno.
Td / TEMPERATURA DI DECOMPOSIZIONE
Questa è una misura della decomposizione del materiale. Il metodo di analisi misura il punto in cui si registra un decremento ponderale del materiale pari al 5%, ossia il punto in cui l’affidabilità è compromessa e può verificarsi una delaminazione.
Un PCB più affidabile richiederà una Td ≥ 340° C.
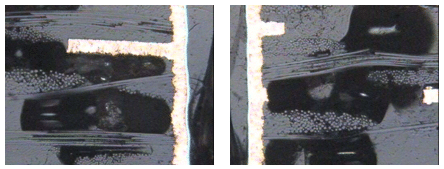
T260 / T288 / TEMPO DI DELAMINAZIONE
Questo è il metodo per determinare il momento in cui lo spessore del PCB è irreversibilmente cambiato ad una temperatura predefinita (in questo caso 260 o 288) – ossia quando il materiale si espande a tal punto da determinare una delaminazione.
Per la saldatura senza piombo devo utilizzare un materiale FR4 con la Td più elevata (Td = temperatura di decomposizione)?
Un valore Td più elevato è preferibile soprattutto se la scheda è tecnicamente complessa ed esposto ad una serie di saldature di rifusione, ma questo può comportare costi elevati. Conoscere il proprio processo di assemblaggio può contribuire a rendere le scelte giuste.
Qual è la differenza tra “DCD” e “non DCD” come sistema d’indurimento della resina epossidica in materiali FR4?
La DCD (diciandiammide) è di gran lunga il sistema d’indurimento più comune per questa resina epossidica; fornisce normalmente un valore Td di circa 300-310 °C mentre una “nonDCD”, cioè un’epossidica fenolica curata, ha un valore Td di circa 330-350 °C e presenta dunque una migliore resistenza alla temperatura più elevata.
Cosa significa l’acronimo “CAF”?
CAF (filamento conduttivo anodico) significa che ci sarà una reazione elettrochimica tra l’anodo e il catodo di rame, il che può provocare un cortocircuito interno nel materiale.
Quale superficie di circuito stampato è preferibile per la saldatura senza piombo?
Non esiste una “superficie migliore”; tutte le superfici hanno i loro pro e contro. Quella da preferire dipende da numerosi fattori. Vi invitiamo a consultare i nostri tecnici od a rivedere le informazioni sulle finiture delle superfici riportate in questa sezione del sito.
Quali sono le regole per quanto riguarda i ritardanti di fiamma? In elettronica esisteva un divieto nazionale contro il TBBP-A?
No, l’indagine ha rivelato che per ragioni di ordine pratico il divieto non è possibile.
Qual è la differenza tra il ritardante di fiamma aggiunto in forma reattiva ed in forma additiva?
Il ritardante di fiamma reattivo è legato chimicamente alla resina epossidica e non si dissolve, migrando fuori dal prodotto sotto forma di residuo.
A quanti cicli di riflusso possono resistere i materiali FR4?
È difficile fornire una risposta precisa, ma abbiamo condotto dei test del materiale con un massimo di 22 riflussi, quattro dei quali a temperatura di picco di 270 °C. Lo stress dopo 22 riflussi è notevole ed il materiale può degradarsi ma tutte le connessioni hanno mantenuto la loro funzionalità.
La nostra raccomandazione è di scegliere un materiale di grado superiore, che presenti un numero di strati superiore a 6 ed uno spessore superiore a 1,6 mm.
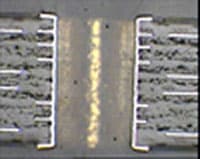
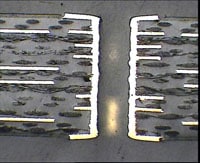
RoHS
Le direttive RoHS o WEEE richiedono la marcatura del circuito stampato?
No, ma per motivi pratici i PCB che hanno HASL senza piombo devono essere indicati chiaramente affermando la loro compatibilità RoHS a causa del rischio di confusione con HASL piombo.
I PCB conformi alla direttiva RoHS sono anche privi di alogeni?
No, non necessariamente. La direttiva RoHS vieta due ritardanti di fiamma, brominati, i PBB (bifenili polibromurati) e i PBDE (eteri di bifenile polibromurati). Ciò che viene normalmente utilizzato nei PCB è un ritardante di fiamma brominato chiamato TBBP-A (Tetrabromobisfenolo A).