A continuación hemos listado algunas de las preguntas más comunes que recibimos, y aquellos aspectos que son temas de discusión habitual. También puede hacer su pregunta sobre PCB aquí.
HDI
¿Qué es una microvía?
Según la nueva definición del IPC-T-50M, una microvía es una estructura ciega con una relación de aspecto máxima de 1:1, que termina en un punto con una profundidad total de no más de 0,25 mm medidos desde la capa de cobre de partida hasta la capa de destino.

¿Qué quiere decir que una vía es ciega?
Se trata de una vía que transcurre de una capa exterior a una interior, y que por lo tanto no atraviesa todo el PCB. Estas vías pueden realizarse de forma mecánica o empleando tecnología láser.
La imagen muestra una vía ciega taladrada con láser.

¿Qué quiere decir que una vía es enterrada?
Es una vía que atraviesa una o más de las capas internas. Normalmente se hacen con un taladro mecánico.
¿Qué es un PCB HDI?
IPC-2226 define HDI como una placa de circuito impreso con una densidad de pistas por unidad de superficie mayor a las de las placas de circuito impreso (PCB) convencionales. Poseen líneas y espacios entre ellas ≤ 100 µm / 0.10 mm, vías más pequeñas (<150 µm), pads de captura 20 pads/cm2) que las empleadas en la tecnología convencional de PCB.

¿Qué es un PCB Ultra HDI?
Para que un circuito impreso sea considerado PCB Ultra HDI, la placa de circuito impreso debe tener:
- Ancho y distancia entre conductores ≤ 50 µm
- Espesor dieléctrico inferior a 50 µm
- Microvía con diámetro inferior a 75 µm
- Que el producto exceda de lo indicado como nivel C de la norma existente IPC 2226
¿Hay diferentes tipos de HDI?
El gráfico siguiente muestra las estructuras principales: tipo I, tipo II y tipo III conforme a la definición recogida en IPC-2226.
Tipo I. Define una capa de microvía única en uno o a ambos lados del núcleo. Emplea tanto microvías metalizadas como taladros metalizados para la interconexión, usando vías ciegas pero no enterradas.

Tipo II. Define una capa de microvía única en uno o a ambos lados del núcleo. Emplea tanto microvías metalizadas como taladros metalizados para la interconexión. Se usan vías ciegas y enterradas.

Tipo III.Define al menos dos capas de microvía en uno o a ambos lados del núcleo. Emplea tanto microvías metalizadas como taladros metalizados para la interconexión, usa vías ciegas y enterradas.

Terminología de construcción para definir el grado de construcción HDI:
- 1+n+1 = una única capa de microvía (como en los ejemplos anteriores del tipo I y II)
- 2+n+2 = 2 capas de microvía (como en el ejemplo anterior del tipo III)
- 3+n+3 = 3 capas de microvía
FLEX/RIGID-FLEX
¿Cuáles son las estructuras disponibles para PCB flexibles y rígidas-flexibles?
Hay numerosas estructuras diferentes disponibles. Las más comunes se definen a continuación:
Flexible monocara (IPC-60103 tipo 1) Coverlay (poliamida + adhesivo) unido a un núcleo de FPC de una cara sin adhesivo. Con o sin refuerzos.

Flexible de doble cara (IPC-6013 tipo 2) Coverlay unido en ambas caras de un núcleo de FPC de doble cara sin adhesivo (dos capas conductoras) con taladros metalizados. Con o sin refuerzos.

Flexible multicapa (IPC-6013 tipo 3) Coverlay unido en ambas caras de una estructura sin adhesivo que contiene tres o más capas conductoras con taladros metalizados. Con o sin refuerzo. La capacidad es de 4L.

Estructura rígida-flexible tradicional (IPC-6013 tipo 4) Combinación de circuitos multicapa rígidos y flexibles que contiene tres o más capas con taladros metalizados. Capacidad de 22L con capas flexibles de 10L.

Estructura rígida-flexible asimétrica, en la que el FPC está situado en la capa exterior de la estructura rígida. Contiene tres o más capas con taladros metalizados.

Estructura rígida-flexible multicapa con vías enterradas / ciegas (microvías) como parte de la estructura rígida. Se pueden conseguir 2 capas de microvías. La estructura también puede incluir dos estructuras rígidas como parte de una construcción homogénea. La capacidad es una estructura HDI 2+n+2.

Estructura book-binder y air-gap – una estructura compleja Los espacios entre las capas flexibles permiten una mejor flexión del FPC. Las capas flexibles pueden ser de distintas longitudes en las construcciones book-binder para minimizar la compresión de las capas flexibles internas en el radio de doblado.

¿Cómo se calcula la longitud correcta de la parte flexible de una estructura rígida-flexible para permitir un radio de doblado mínimo?
La recomendación detallada se encuentra en la norma IPC-2223, sección 5.2.3.3 tanto para curvaturas estáticas como dinámicas, y es la que se debería utilizar en la verificación del diseño. Aquí puede encontrar unas guías de diseño básicas en función del espesor del material flexible:

FLEX TYPE | MINIMUM BEND RADIUS |
---|---|
Single sided flex | 3 – 6 x circuit thickness |
Double sided flex | 7 – 10 x circuit thickness |
Multilayer flex | 10 – 15 x circuit thickness |
Dynamic application | 20 – 40 x circuit thickness |
¿Cuál es la diferencia entre semiflexible y rígido-flexible?
Una PCB semiflexible es en la práctica una PCB multicapa «estándar», creada usando tipos concretos de FR4 a la que se hace un rebaje hasta un espesor específico, de manera que el área más fina resultante ofrece una sección flexible / de doblado del FR4 tradicionalmente rígido. El producto semiflexible es adecuado para aplicaciones estáticas (flexible para instalar) o que se va a doblar un número limitado de veces.

¿Cuál es la diferencia entre los sistemas flexibles con y sin adhesivo?
Las construcciones que usan sistemas con adhesivo usan ese adhesivo para unir el cobre al núcleo flexible. Así, esta capa adhesiva, junto con coverlay completo, penetra en la construcción rígida y directamente en el orificio. El mayor coeficiente de expansión del adhesivo aumenta el riesgo de problemas en el taladro, como la formación de grietas y fallos del taladro como resultado de la expansión; tener este material en el taladro en sí puede hacer que surjan problemas de formación de cobre en la pared del taladro debido a una eliminación insuficiente del residuo del adhesivo.

La solución para mejorar la fiabilidad de las vías o los taladros fue pasar a un sistema revestido con cobre sin adhesivo (cobre unido directamente a la poliimida) y limitar la superposición del coverlay en la parte rígida de la tarjeta. Esto garantiza una estructura del taladro mucho más fiable sin que el adhesivo penetre en el taladro. Este es de lejos el enfoque más frecuente de las estructuras rígidas-flexibles.

DESIGN RULES
¿Cuál es el tamaño de taladro mínimo de pad en las capas internas y externas?
Varía entre fábricas, pero en general se puede decir que la mayoría de los fabricantes las pueden fabricar de la siguiente manera:
A = 0.15 mm
B = 0.20 mm
C = 0.30 mm

Cuando necesito pistas más anchas de lo normal, ¿qué anchura de pistas debo usar?

En general, cuanto mayor sea el espesor de la base de cobre, más ancha debería ser la pista. Una regla básica es que con un espesor de cobre de 18 µm la pista no debería ser más estrecha que 0.1 mm (4 mil) y que con un espesor de cobre de 105 µm la pista no debería ser más estrecha que 0.25 mm (10 mil).
¿Cuál será el espesor final del cobre?
En algunas ocasiones existe la percepción errónea de que los distintos espesores de cobre ofrecen unos resultados exactos y que estos no varían durante la producción de PCB. Por ejemplo, 1 onza = 35 um o ½ onza = 18 um.
Sin embargo, IPC-6012 ha detallado el espesor mínimo aceptable del cobre tanto en las capas internas, debido a las tolerancias permitidas para el espesor de la lámina de cobre base, como en las externas debido además a la cantidad de cobre depositada durante los procesos de metalizado.
A continuación se muestran algunos de los pesos de cobre más estándar y cuál es el espesor final permisible.
Es fundamental entender qué espesor se necesita y especificarlo correctamente; si no, se puede especificar por exceso o por defecto, lo que puede acarrear costes innecesarios o problemas en el diseño. Para obtener más información, consulte a nuestros técnicos.
Espesor final de cobre en las capas internas | |
Peso base de cobre | Espesor final mínimo |
1/2 oz. | 11.4 um |
1 oz. | 24.9um |
2 oz. | 55.7um |
Espesor final de cobre en las capas externas | ||
Peso base de cobre | Espesor final mínimo en Clase 2 | Espesor final mínimo en Clase 3 |
1/2 oz. | 33.4um | 38.4um |
1 oz. | 47.9um | 52.9um |
2 oz. | 78.7um | 83.7um |
¿Debemos eliminar o mantener los pads no funcionales?
En el punto 9.1.4 de IPC-2222A se define claramente que el fabricante no debe eliminarlos, pero muchas fábricas piden permiso para hacerlo y así conseguir un mejor rendimiento en la producción. Si no son cruciales para la función, recomendamos considerar que se permita su eliminación.

¿Que significa la separación entre las mismas líneas de señal (net)?
«Mismo espaciado de net» significa que la distancia de cobre a cobre dentro de la misma señal eléctrica está demasiado cerca para poder fabricarse de acuerdo con los archivos Gerber. Como está dentro de la misma señal, el DRC (comprobación de reglas de diseño) en el software CAD del cliente no avisa de este fallo. Es importante que el cliente establezca correctamente los límites al iniciar un nuevo diseño. La distancia mínima entre cobre y cobre suele ser correcta, pero no se establece el mismo valor dentro de la misma señal (net). No es un problema muy grave, pero provoca retrasos y preguntas técnicas innecesarias.
¿Por qué se exige una distancia tan grande del borde del taladro al cobre para los orificios no metalizados (NPTH)?
Al realizar los taladros en la placa de circuito, es conveniente taladrar todos los agujeros con la misma configuración para obtener la mejor precisión de posición de los agujeros. Los agujeros no metalizados deben bloquearse durante el proceso de metalizado (de lo contrario, también se metalizarán). Para poder bloquear el NPTH necesitamos espacio entre el borde del agujero y el cobre. La distancia necesaria está relacionada con el espesor del cobre. Para un espesor de cobre estándar (cobre base de 18µm), un buen valor es 0,3mm y definitivamente no menos de 0,2mm.
TERMINOLOGY
¿Qué es la “relación de aspecto”?
Es la relación entre el diámetro del taladro y su profundidad. Cuando un fabricante afirma que su producción tiene una “relación de aspecto” de 8:1 significa, por ejemplo, que el diámetro de un taladro es 0.20 mm para un PCB de espesor 1.6 mm.
En estructuras HDI, la relación de aspecto máxima admitida para la microvía es normalmente 0.8:1, pero es preferible 1:1 para facilitar el metalizado.
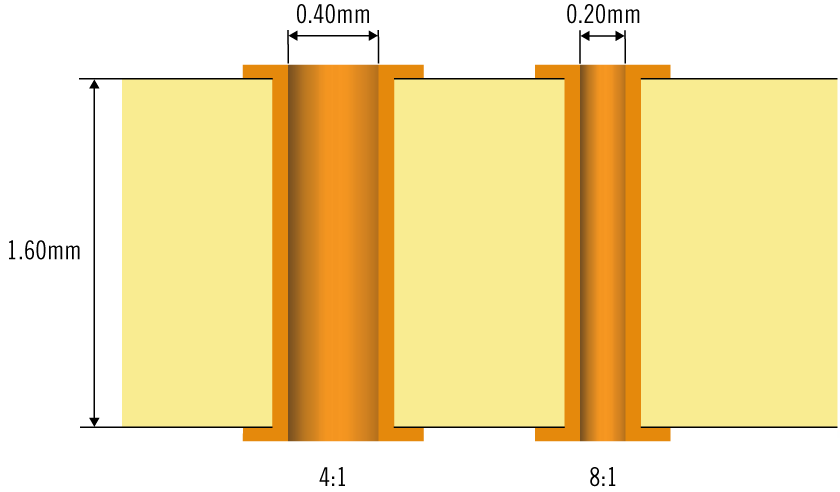
¿Qué es la envoltura de cobre?
La envoltura de cobre es la aplicación continua de cobre enchapado que se pone dentro del metalizado del taladro y se extiende a la superficie del PCB (o la superficie del núcleo de la capa interior si forma parte de una estructura HDI) con un mínimo de 25 µm.

Para las exigencias de la clase 2, el espesor de la aplicación superficial de la envoltura de cobre es de 5 µm, como mínimo, pero para las de la clase 3 cambiarán en función de la ubicación de esta característica dentro de la construcción. Le rogamos que solicite más información sobre las exigencias de la clase 3 a nuestros técnicos.
¿A qué se llama “moneda de cobre” en un PCB?
Un PCB con “moneda de cobre”, es una placa de circuito impreso multicapa a la que se ha añadido una pieza maciza de cobre, llamada moneda, incrustada en el apilamiento de la placa. Esto permite una conexión térmica directa de un lado a otro o de una capa específica a una capa exterior.
¿Qué es una impedancia controlada?
Tener en cuenta la señal de la PCB a medida que se desplaza por una pista controlando la impedancia significa que controlamos el rendimiento o la velocidad de esa señal en un punto de una pista. Está relacionado con la resistencia, la capacitancia y la conductancia de la pista en cuestión. La impedancia también se mide en ohmios, y es distinta de la resistencia, que es una característica de la CC. La impedancia es una característica de la CA, lo que significa que está relacionada con la frecuencia.
¿Hay más de un tipo de impedancia controlada?
Sí, los hay y se explican a continuación:
Impedancia diferencial – Impedancia de un par de conductores con señales de polaridad igual y opuesta – la misma amplitud en antifase entre sí.
Impedancia para el modo impar – Impedancia de un lado de un par de conductores que tienen ambos señales de polaridad igual y opuesta – la misma amplitud y antifase.
Impedancia para el modo par – Impedancia de un lado de un par de conductores que tienen señales iguales – la misma amplitud y la misma polaridad.
Impedancia para el modo común – Impedancia de un par de conductores que tienen signos iguales – la misma amplitud y la misma polaridad.
¿Qué es un pad térmico?
Para los componentes de SMD, en especial los más pequeños, se usan pads de descarga térmica para simular la misma masa térmica en ambas terminaciones a fin de evitar el movimiento de los componentes durante el proceso de soldadura o, en el peor caso, su rotura.


Para los componentes convencionales, usamos pads térmicos en los planos de la capa interna para ayudar a mojar la pared del taladro. En la serie IPC-2220 se pueden encontrar fórmulas para los pads térmicos.

¿Qué es la resistencia térmica en un PCB?
En este vídeo puedes aprender sobre la resistencia térmica y la conductividad térmica.
¿Se debe añadir la autorización para agregar lágrimas en la documentación de la PCB?
De acuerdo a la nueva norma IPC-6012D sección 3.4.2, está permitido añadir lágrimas en las pistas cuando las PCB son de clase 1 y 2.

Si no desea lágrimas, remárquelo en la documentación de la PCB. Pero añada suficiente corona.
¿Qué es la tecnología back-drilling?
Para aplicaciones de alta frecuencia necesitamos evitar la pérdida de señal y, por tanto, cuando una capa se conecta con otra y la señal viaja de una capa a otra debe pasar a través de un orificio de la vía que conecta las capas. Si la señal va a pasar de la capa uno a la capa dos de una tarjeta de 20 capas, por ejemplo, entonces parte de la estructura de la vía se considera como «exceso» y para esta aplicación es mejor eliminar el exceso de cobre de este orificio, ya que actúa como antena y afecta a la señal.
Utilizamos el back-drilling (profundidad controlada en el eje z) para retirar el «exceso» de cobre del orificio a fin de obtener una mejor estabilidad de la señal. Cuando menor sea la profundidad («exceso» de cobre) mejor será el resultado. El tamaño de back-drilling debe ser normalmente 0,2 mm mayor que la vía correspondiente.

BACK DRILLING / COUNTER BORE (mm) | |||
---|---|---|---|
A: Depth tolerance | +/-0.20 | +/-0.15 | +/-0.10 |
B: Min. remain thickness and tolerance | 0.5+/-0.25 | 0.35+/-0.1 | 0.3+/-0.1 |
¿Qué es la «marca UL»?
La seguridad es crucial en el sector de la electrónica. Es fundamental que los usuarios puedan confiar en el producto acabado cuando se piensa en factores como la seguridad eléctrica y contra incendios, lo que significa que tanto la PCB como los materiales que contienen deben satisfacer los más altos estándares. Para asegurarse que las tarjetas cumplen esos estándares, es habitual obtener la certificación UL de la propia PCB o los materiales que la forman.
En primer lugar, ¿qué es UL? Las letras UL corresponden a Underwriters Laboratories. ¿Por qué es importante el reconocimiento UL? UL es una importante autoridad y disfruta de enorme reputación dentro del sector de las PCB. La empresa es irreemplazable a la hora de analizar la seguridad eléctrica y contra incendios. Clientes de todo el mundo, incluidas empresas chinas de renombre, exigen a las fábricas que obtengan el reconocimiento UL. Contar con este reconocimiento es por tanto muy importante para las fábricas de PCB para producir tarjetas seguras y poder acceder al mercado internacional.
VIA HOLE
¿Qué tipo de maclado de taladros de vía se recomienda?
El tipo de maclado recomendado para productos estándar (sin incluir taladro de vías cubiertas) es IPC 4761 tipo VI rellenado y cubierto, con el objetivo completamente lleno, aunque en la especificación general de NCAB Group se recoge ≥ 70 % como aceptable. La imagen que aparece a continuación muestra el tipo VI con cobertura de máscara de soldadura líquida.

El rellenado por una sola cara no se recomienda (incluyendo el tipo II con cobertura y cubierta superficial tipo «carpa») debido a la posibilidad de que se produzca el atrapamiento de productos químicos o bolas de soldaduras en el caso de acabados HASL (con o sin plomo).
¿Qué son las vías cubiertas?
Una vía está cubierta si se añade enchapado encima del taladro de la vía de modo que la superficie esté completamente metalizada con un espesor de enchapado de tapa / cobre de 5 µm para las exigencias de la clase 2 o 12 µm para las de la clase 3.

Esto depende del material empleado para el relleno de la vía, siendo resina epoxi en contraposición a máscara de soldadura, ya que el epoxi reducirá al mínimo el riesgo de que aparezcan burbujas de aire o la dilatación del relleno durante la soldadura. Esto se puede clasificar dentro de IPC-4761 como tipo VII – taladros de vía rellenos y cubiertos. Esto se emplea principalmente para diseños con vía en pad o aplicaciones BGA que requieren densidades elevadas.
MATERIAL
¿Tengo que emplear un material FR4 con Tg (Tg = temperatura de transición vítrea) alta para soldaduras sin plomo?
No, no es necesario. Hay muchos factores a tener en cuenta, p. ej. el número de capas, el espesor del PCB y la correcta comprensión del proceso de ensamblaje (número de ciclos de soldadura, tiempo por encima de 260°, etc.). Algunas investigaciones han mostrado que un material con un valor Tg estándar ha presentado un comportamiento mejor que el de algunos materiales con un valor Tg mayor. Tenga en cuenta que el valor Tg se supera incluso con la soldadura «con plomo».
Lo verdaderamente importante es el comportamiento del material con temperaturas por encima del coeficiente Tg (post Tg), de este modo conocer los perfiles de temperatura a los que estará sujeta la placa le ayudará a evaluar las características de rendimiento necesarias.
¿Qué características del material deben observarse durante la selección del mismo?
Las principales que consideraríamos en primer lugar incluyen:
CTE
Una medida que indica el coeficiente de dilatación del material cuando se calienta. Crítico en el eje Z, generalmente por encima de la Tg y la dilatación es mayor. Si CTE es insuficiente, podrían producirse fallos durante el ensamblaje, ya que el material se dilata rápidamente por encima de la Tg.

Los materiales pueden tener la misma Tg pero CTE diferentes, un CTE inferior es mejor. Igualmente, algunos materiales pueden poseer coeficientes Tg mayores, pero tener un CTE post Tg mayor (peor).
Tg / TEMPERATURA DE TRANSICIÓN VÍTREA
El coeficiente Tg es la temperatura en la que el material pasa de material relativamente rígido similar al vidrio a convertirse en un material más elástico y flexible similar al plástico. Es importante tener en cuenta que las propiedades de los materiales cambiarán al igual que en la Tg de arriba.
Td / TEMPERATURA DE DESCOMPOSICIÓN
Es una medida de degradación del material. El método de análisis mide cuando se pierde un 5% del peso del material, el punto en el que se compromete la fiabilidad y puede producirse la delaminación.
Para una mayor fiabilidad del PCB se requiere Td ≥ 340℃

T260 / T288 / RESISTENCIA A LA DELAMINACIÓN
Se trata de un método para determinar el tiempo que el espesor del PCB necesita para modificarse irreversiblemente a una temperatura predefinida (260 o 288 en este caso), o lo que es lo mismo, cuando el material se dilata hasta un punto en el que se produce la delaminación.
¿Tengo que usar un material FR4 con alto Td (temperadura de descomposición) para soldadura sin plomo?
Se prefiere un valor Td mayor, especialmente si la placa posee una técnica compleja y está sometida a varias refusiones, pero esto puede conllevar costes mayores. Conocer su proceso de ensamblaje puede ayudarle a adoptar las decisiones adecuadas.
¿Cual es la diferencia entre los métodos de endurecido “Dicy” y “noDicy” para las fibras FR4?
“Dicy” (Dicyandiamina) es con diferencia el método de endurecido más común para este tipo de fibras; normalmente se obtienen valores de Td entre 300 y 310°C. En cambio, los sistemas “noDicy”, como los que realizan la curación de la fibra con fenoles, tienen un Td entre 330 y 350°C y por lo tanto pueden resistir mejor las altas temperaturas.
¿Qué significa “CAF”?
CAF (Conductive Anodic Filament) quiere decir que habrá una reacción electroquímica entre al ánodo y el cátodo de cobre, lo que puede generar un cortocircuito interno en el material.
¿Cuál es el mejor acabado superficial para la soldadura sin plomo?
No hay una “superficie mejor”; todas las superficies tienen sus ventajas y sus inconvenientes. La que se elija depende de muchos factores. Le recomendamos que consulte con nuestros técnicos o que revise la información sobre acabados superficiales en esta misma sección de la web.
¿Cuáles son las normas respecto a retardantes de llama? ¿Hay alguna norma nacional contra el TBBP-A que se usa principalmente en electrónica?
No, los resultados de los estudios efectuados demuestran que no es posible prohibirlo por razones prácticas.
¿Cuál es la diferencia entre un retardante de llama reactivo y uno añadido?
El retardante de llama reactivo está químicamente ligado a la resina epoxi y no se disolverá ni migrará del producto como consecuencia del proceso de limpieza de la placa.
¿Cuántos ciclos de refusión puede soportar un material FR4?
Es difícil dar la respuesta adecuada, pero hemos hecho ensayos con materiales con hasta 22 ciclos de refusión, cuatro de ellos con una temperatura máxima de 270º C. La exigencia después de 22 ciclos de refusión es considerable y el material se puede degradar, pero todas las conexiones continuaron funcionando.
Nuestra recomendación es elegir un material con un coeficiente alto donde haya más de 6 capas y el espesor supere los 1.6 mm.


RoHS
¿Es requerido marcar los PCB que cumplan con las directivas RoHS o WEEE?
No, pero, por razones prácticas, los PCB que contienen HASL libre de plomo deberían estar claramente identificados como compatibles con RoHS para evitar el riesgo de confusión con los que contienen HASL con plomo.
¿Están los PCB compatibles con RoHS también libres de halógenos?
No necesariamente. La directiva RoHS prohíbe dos retardantes de llama basados en el bromo, PBB (bifenil polibromado) y PBDE (éter de difenil polibromado). El que se usa habitualmente en los circuitos impresos está también basado en el bromo, el TBBP-A (tetrabromobifenol A).
¿Cuál es tu pregunta sobre PCB?
Si no encuentra la respuesta que está buscando, o desea más detalles, por favor, póngase en contacto con nosotros y estaremos encantados de ayudarle.
Su información de contacto se guardará y se utilizará para ponernos en contacto con usted con una respuesta a su pregunta. La dirección de correo electrónico que ha proporcionado puede ser utilizada para enviarle información que creamos pueda resultar interesante. Su información de contacto sólo será utilizada por NCAB Group. Al pulsar «Enviar» estará de acuerdo con esto. Para obtener más información sobre cómo NCAB Group procesa su información personal, consulte nuestra Política de privacidad.