Här hittar du svaren på några av de vanligaste frågorna som vi får om mönsterkort.
HDI
Vad är ett mikroviahål?
Enligt den nya definitionen i IPC-T-50M är det en blind struktur med en maximal “aspect ratio” (Förhållandet mellan hålets diameter kontra dess längd) på 1:1, som ansluter ner mot en pad som ligger på ett maximalt djup på 0.25mm mätt från ytan.
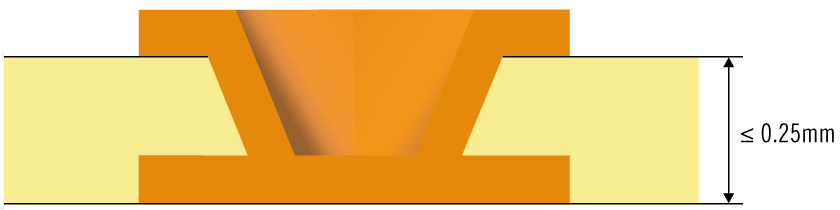
Vad menas med ett blint viahål
Ett hål som går från ett ytterlager men inte genom hela mönsterkortet. Dessa hål kan borras både mekaniskt eller med laserteknik.
Bilden nedan visar ett laserborrat blint viahål.
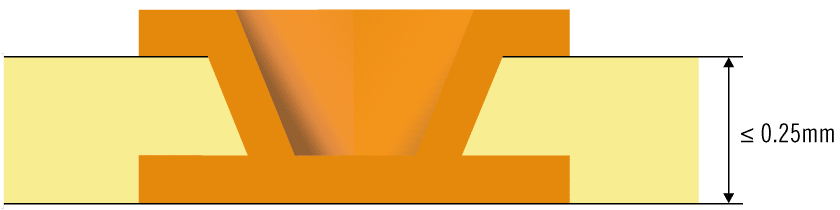
Vad menas med ett begravt viahål?
Det är ett hål som går mellan ett eller flera innerlager på mönsterkortet. Ett begravt viahål borras normalt mekaniskt.
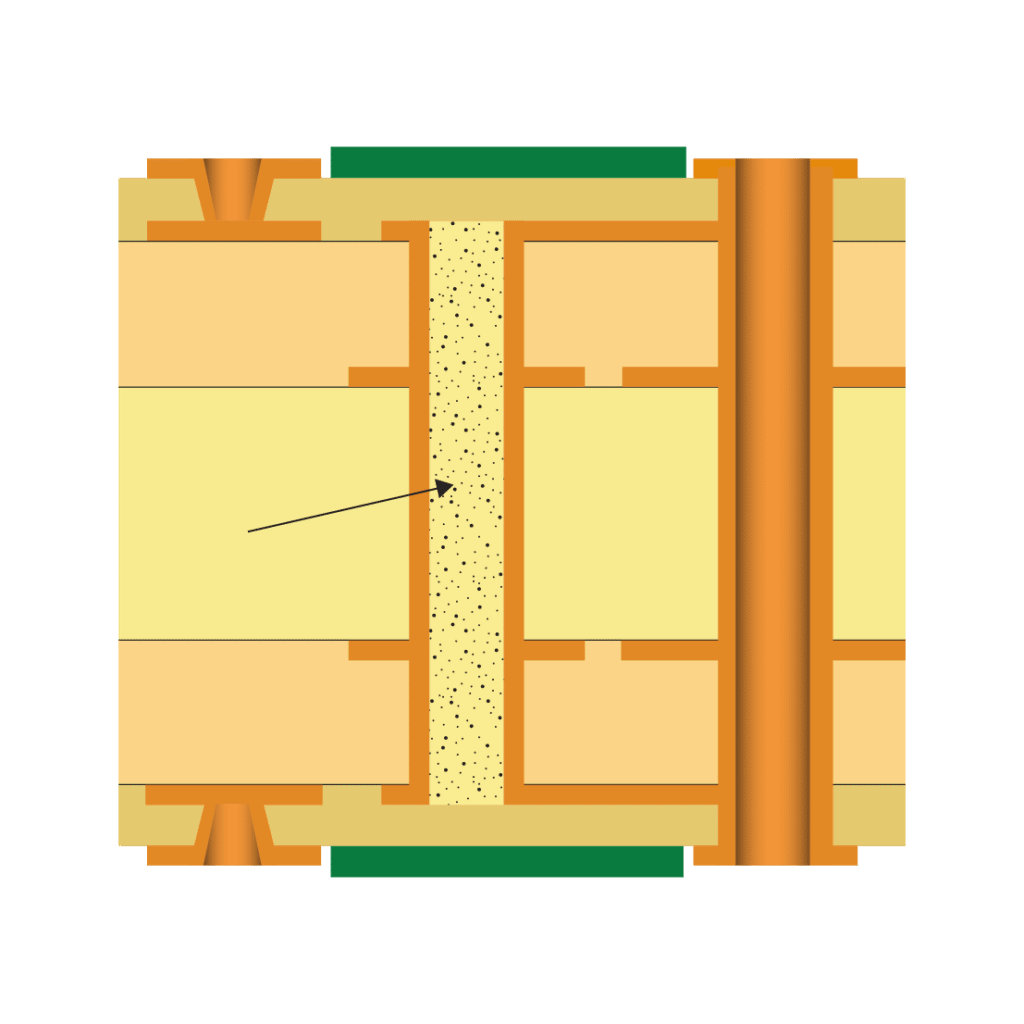
Vad är ett HDI mönsterkort?
IPC-2226 definierar HDI som en design med ett genomsnitt på 20 elektriska anslutningar/cm2 på båda sidor av mönsterkortet. Dessa konstruktioner har normalt små viahål (≤150µm) med smala ledarbredder och isolationer (≤100µm) där viahålen kan vara placerade i SMT paddar och/eller ha tunn dielektrisk tjocklek där mikrovior används.
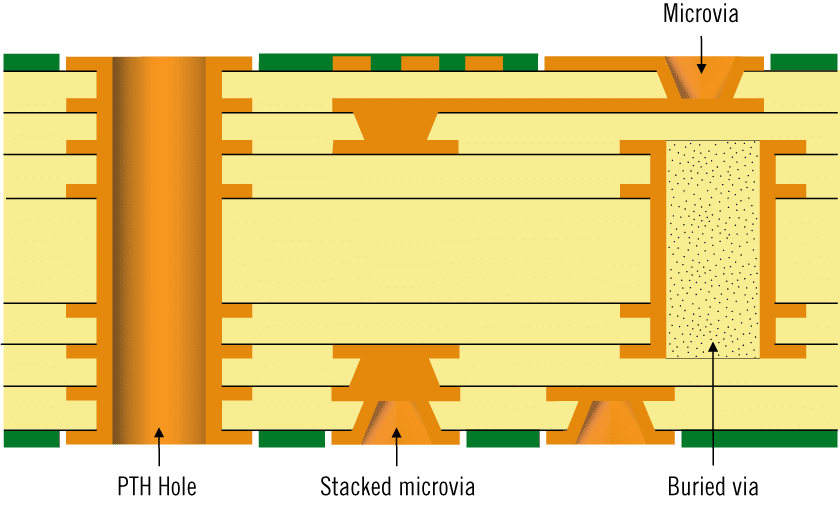
Finns det olika typer av HDI kort?
Bilderna nedan visar de viktigaste strukturerna – typ I, typ II och typ III så som de definieras i IPC-2226.
Typ I. Definieras av mikrovia i en nivå antingen på en eller båda sidorna av kortet. Både mikrovia och genomgående hål används för att skapa elektriska förbindelser, begravda viahål används inte.
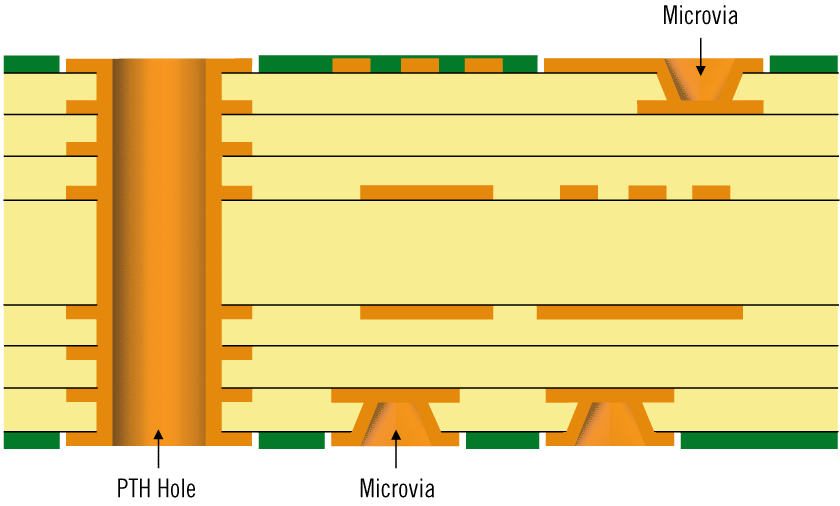
Typ II. Definieras av mikrovia i en nivå antingen på en eller båda sidorna av kortet. Både mikrovia och genomgående hål används för att skapa elektriska förbindelser. Begravda viahål används.
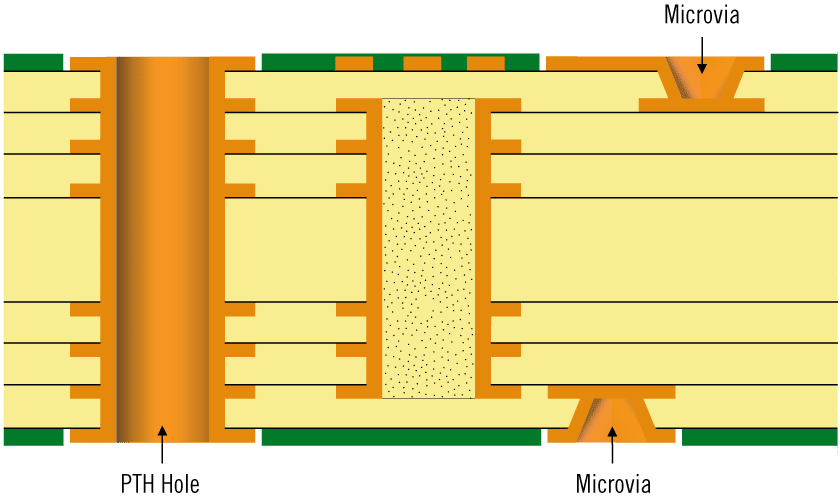
Typ III. Definieras av mikrovior i minst två nivåer antingen på en eller båda sidorna av kortet. Både mikrovia och genomgående hål används för att skapa elektriska förbindelser. Begravda viahål används.
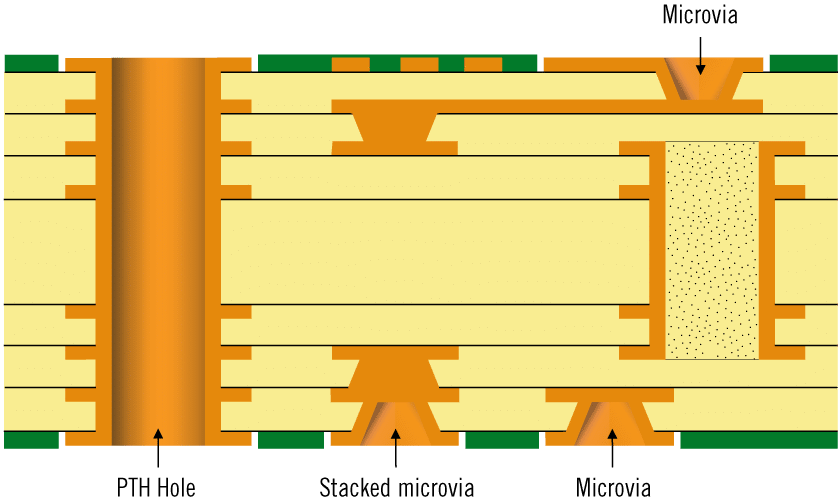
Terminologier för att definiera typen av en HDI-konstruktion:
- 1+n+1 = en nivå mikrovior (som typ I och typ II i exemplen ovan)
- 2+n+2 = två nivåer mikrovior (som typ III i exemplet ovan)
- 3+n+3 = tre nivåer mikrovior (som typ III i exemplet ovan)
FLEX/RIGID-FLEX
Vilka är de tillgängliga typerna för flex- och flex-rigida mönsterkort?
Många olika typer finns. De vanligaste definieras nedan:
Enkelsidigt flexkort (IPC-6013 typ 1) Innehållande ett ledande lager, vanligtvis täckt med ett ”coverlay” alternativt en flexibel lödmask. Kan vara försedd med en eller flera förstyvningar.

Dubbelsidigt flexkort (IPC-6013 typ 2) ) Innehållande två ledande lager med genompläterade hål, vanligtvis täckt med ett ”coverlay” alternativt en flexibel lödmask. Kan vara försedd med en eller flera förstyvningar.

Flexkort med flera lager (IPC-6013 typ 3) Innehållande tre eller fler ledande lager (vanligtvis fyra lager) med genompläterade hål, vanligtvis täckt med ett ”coverlay” alternativt en flexibel lödmask. Kan vara försedd med en eller flera förstyvningar.
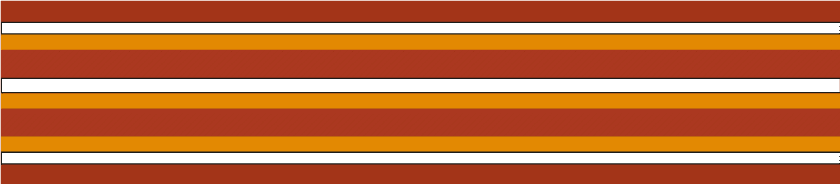
Traditionell flex-rigid konstruktion (IPC-6013 typ 4) Kombination i 3 eller flera lager med rigida och flexibla material innehållande genompläterade hål.
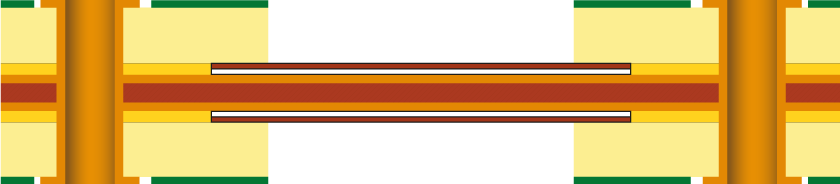
Osymmetrisk flex-rigid konstruktion, där det flexibla lagret placeras på ett ytterlager av den rigida konstruktionen. Innehåller tre eller fler lager med genompläterade hål.
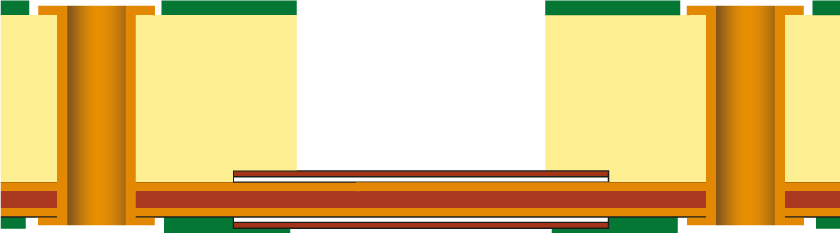
Flex-rigid konstruktion i flera lager med begravda vior / blinda vior som ingår i den rigida delen. Mikrovior kan förekomma. Konstruktionen kan även omfatta rigida strukturer i olika nivåer. Kapaciteten är 2+n+2 HDI-struktur.
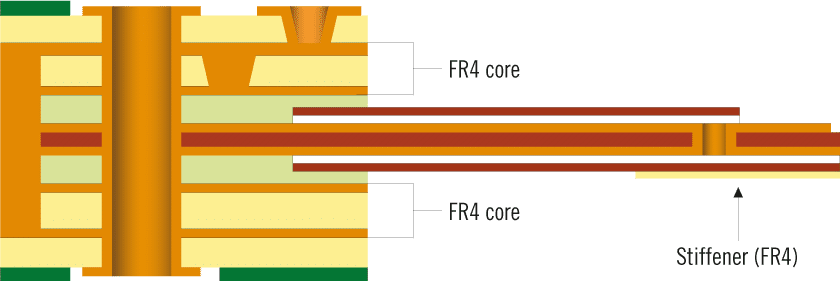
”Book-binder” teknik – en komplicerad lösning
Innehållande ett flertal separerade flexibla kärnor med olika längd för att lättare kunna böjas. Genom att använda denna teknik minimeras de inre flexlagrens kompression.
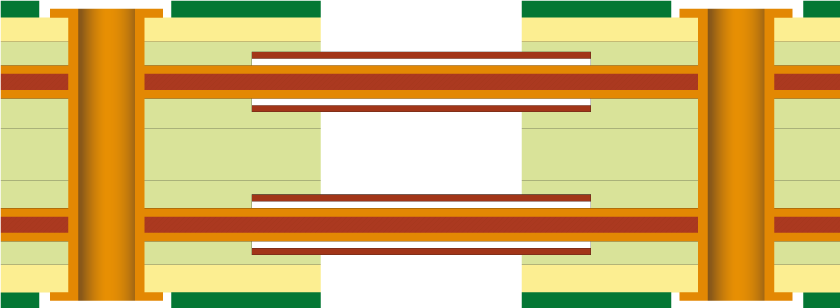
Hur räknar man ut minsta böjradien på flexdelen i en flex-rigid konstruktion?
Rekommendationer för böjradien återfinns i IPC-2223 sektion 5.2.3.3 för både statiska- och dynamiska installationer. En grov indikation på lämpliga värden baserad på flexens tjocklek finns i nedan tabell. Dessa skall ses som en indikation och bör verifieras.

FLEX TYPE | MINIMUM BEND RADIUS |
---|---|
Single sided flex | 3 – 6 x circuit thickness |
Double sided flex | 7 – 10 x circuit thickness |
Multilayer flex | 10 – 15 x circuit thickness |
Dynamic application | 20 – 40 x circuit thickness |
Vad är skillnaden mellan semi-flex och flex-rigida mönsterkort?
Semi-flex-kort är i princip ett normalt mönsterkort med flera lager där de böjbara partierna har djupfräst ner så att en tunnare del återstår. Vanligtvis är den böjliga delen ca 0.25mm tjock och är belagd med en flexibel lödmask. Semi-flex-kort lämpar sig enbart för statiska tillämpningar (flex till montering) eller med ett mycket begränsat antal böjningar.
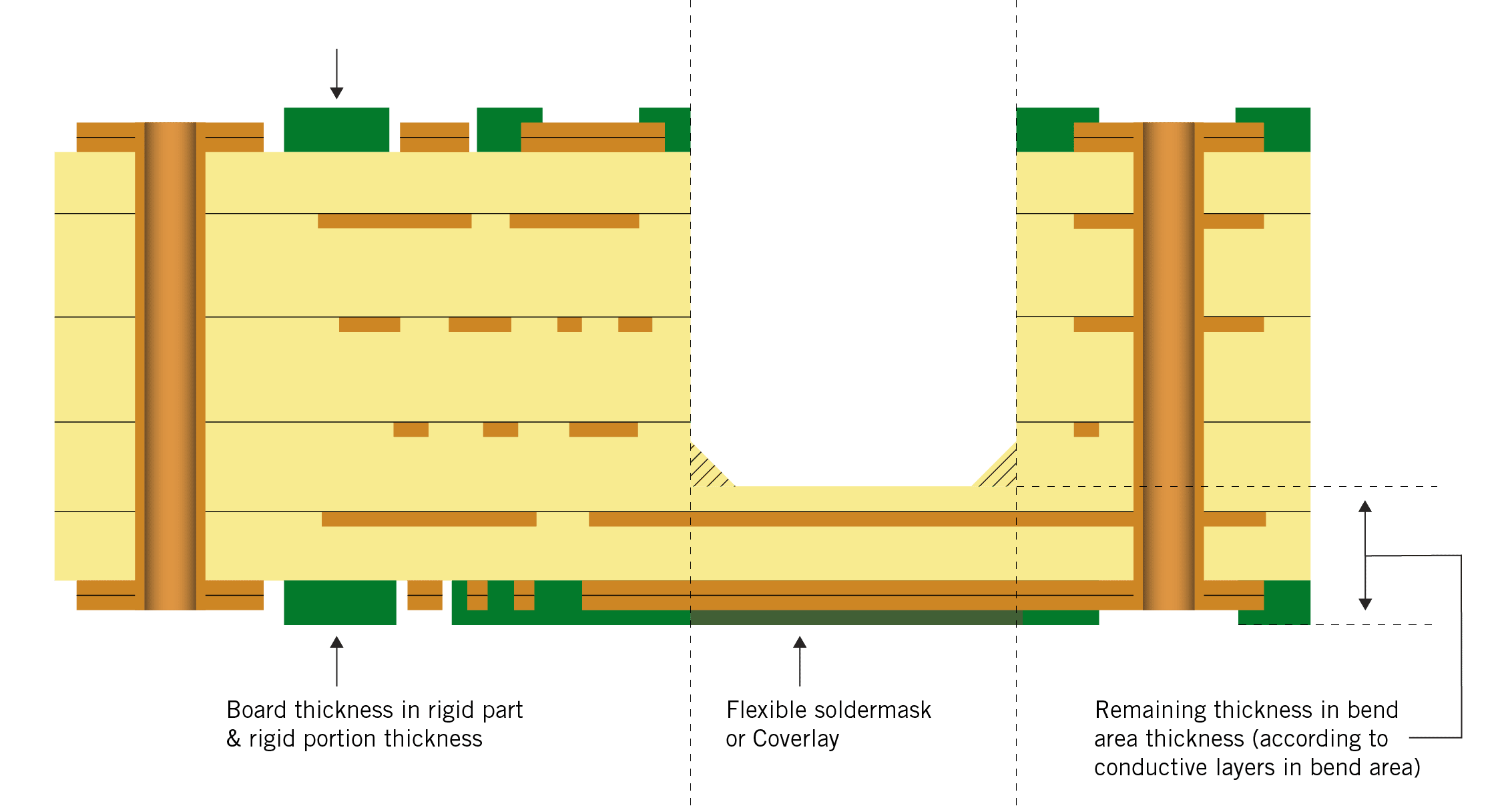
Vad är skillnaden mellan flexmaterial med och utan lim?
I limbaserat material är kopparfolien fäst med adhesiv, vanligtvis epoxi- eller akrylbaserat. Ett limbaserat material är normalt mer kostnadseffektivt, nackdelen är sämre värmetålighet och svårare att genomplätera.
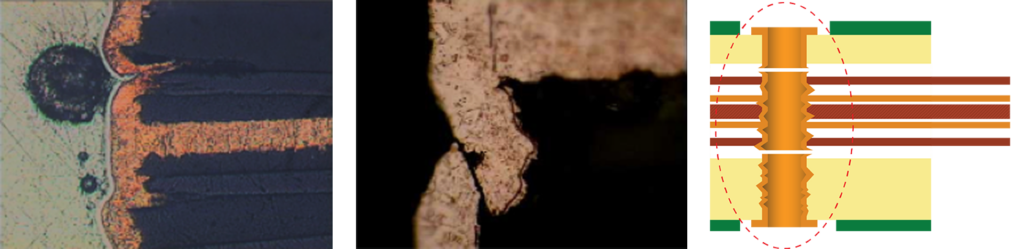
I flexmaterial som är limlösa är kopparfolien fäst direkt ner mot polyimidmaterialet. Ett limlöst material är normalt något dyrare, fördelen är högre värmetålighet och lättare att genomplätera. Detta material rekommenderas framför allt till flex-rigida kort.
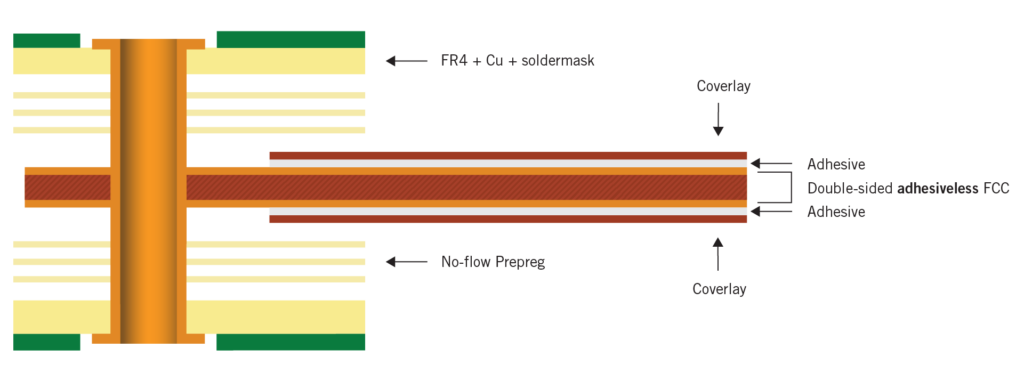
DESIGN RULES
Vilken är minsta padstorlek kontra hål på ytter-/innerlager?
Detta varierar hos olika tillverkare, men generellt kan man säga att de flesta tillverkare kan producera enligt följande:
A = 0.15 mm
B = 0.20 mm
C = 0.30 mm
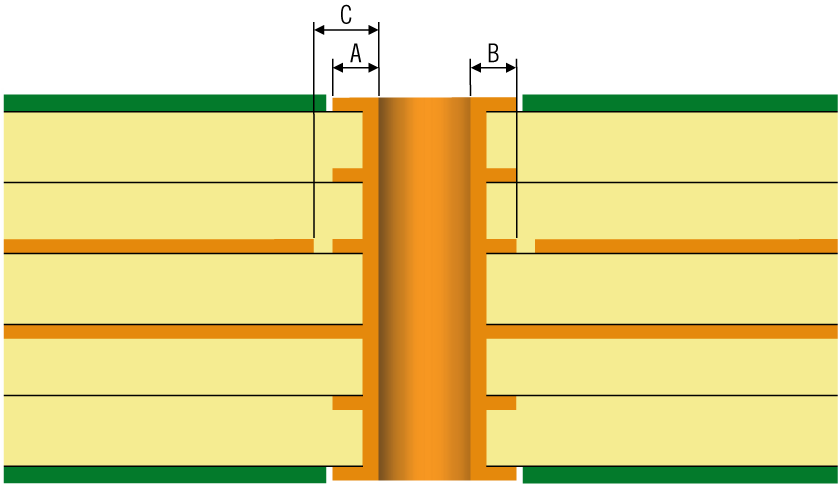
När jag vill ha tjockare ledarbanor än standard, vilka ledarbredder kan jag då använda?

Generellt gäller att ju tjockare baskoppar, desto bredare ledare bör det vara. En tumregel är att vid 18 µm baskoppar bör inte ledaren vara smalare än 0.1 mm (4 mil) och vid 105 µm baskoppar bör inte ledaren vara smalare än 0.25 mm (10 mil), observera att isolationen inte bör vara mindre än ledarbredden.
Vilken koppartjocklek kan jag förvänta mig på ett färdigt mönsterkort?
Kopparfolie för både inner och ytterlager tillverkas i fördefinierade tjocklekar. Exempelvis 18um (1/2oz) 35um (1oz) 70um (2oz). Eftersom mönsterkortet processas i många steg så har IPC gjort upp regler kring vilken slutlig koppartjocklek som är acceptabel på både innerlager och ytterlager på ett färdigt mönsterkort.
Nedan visas exempel på tjocklek på kopparfolie och den minsta tillåtna färdiga koppartjockleken som framgår i IPC-6012.
Det är viktigt att förstå vad just din produkt kräver för att fungera optimalt och göra upp en specifikation som tar hänsyn till de fördefinierade kopparfolierna. Det är exempelvis inte att rekommendera att specificera min 70um på ett innerlager då detta i praktiken innebär att man måste använda sig av en folie på 105um vilket fördyrar kortet. För mer information, kontakta våra tekniker.
Koppartjocklek för innerlager på färdigt kort | |
Kopparfolietjocklek | Minsta koppartjocklek på färdigt kort |
1/2 oz. | 11.4 um |
1 oz. | 24.9um |
2 oz. | 55.7um |
External conductor thickness after plating and processing | ||
Kopparfolietjocklek | Minsta koppartjocklek på färdigt kort klass 2 | Minsta koppartjocklek på färdigt kort klass 3 |
1/2 oz. | 33.4um | 38.4um |
1 oz. | 47.9um | 52.9um |
2 oz. | 78.7um | 83.7um |
Skall vi ta bort eller behålla kragar utan funktion på innerlager?
Det står tydligt i IPC-2222A punkt 9.1.4 att tillverkaren inte ska ta bort dessa. Många fabriker ber dock om tillstånd att ta bort dem för att minska riskerna för kvalitetsbrister och ge ett bättre utbyte. Om de inte är avgörande för funktionen rekommenderar vi att de får tas bort.
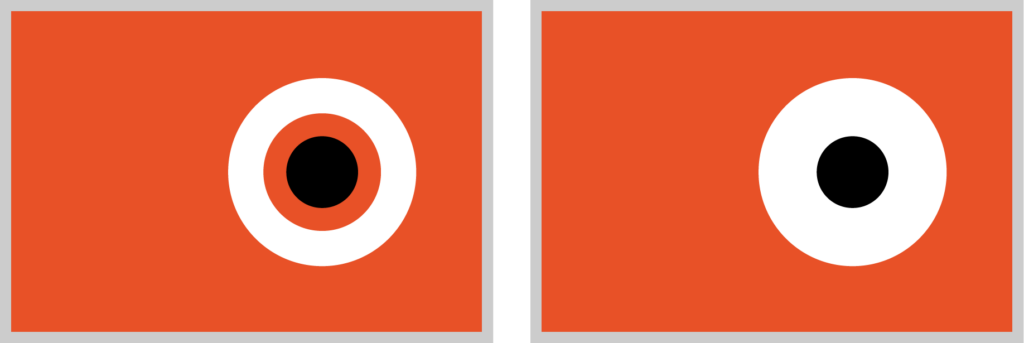
Vad menas med ”same net spacing”?
“Same net spacing” innebär att avståndet från koppar till koppar i samma elektriska nät är för litet för att det ska gå att producera enligt Gerber-filen. De allra flesta CAD-program har en DRC-funktion, Design Rule Check. Denna hittar normalt sådana fel eftersom det är en parameter som sätts innan man börjar CAD-arbetet. Problemet är att det är lätt att glömma att sätta denna parameter även för samma elektriska nät. Detta kommer att rättas till i fabrik, men felet skapar onödiga tekniska frågor och fördröjning i produktionsprocessen.
Varför behövs det så stort avstånd från hålkant till koppar för icke pläterade hål?
När man borrar hål i mönsterkortet vill man borra alla hål, både pläterade och opläterade, vid samma tillfälle. Detta för att för att uppnå bästa möjliga positionsnoggrannhet. För att inte de opläterade hålen ska bli pläterade måste de täckas över innan kortet pläteras och då måste det finns plats runt hela hålet för övertäckningen. Värdet beror på koppartjockleken. Vid normal baskoppartjocklek (18µm) är 0,3mm från hålkant till koppar önskvärt, absolut minst 0,2mm.
TERMINOLOGY
Vad är ”aspect ratio”?
Förhållandet mellan hålets diameter och kortets tjocklek. När en fabrik anger att de kan tillverka med ett ”aspect ratio” på 8:1 innebär det exempelvis en håldiameter på 0.20 mm i ett 1.60 mm tjockt mönsterkort.
För HDI-strukturer så är ett ”aspect ratio” för mikrovior begränsad till 1:1, med 0.7-0.8 är att föredra för enklare plätering.
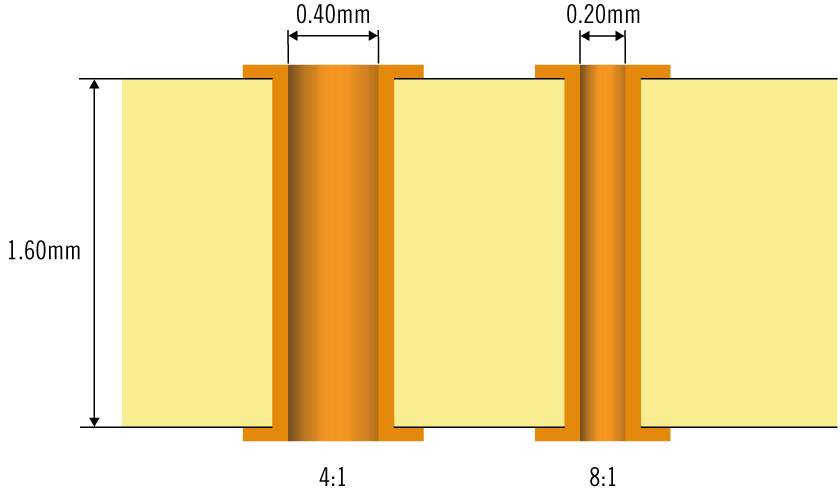
Vad är kopparomslutning (”Copper wrap”)?
Kopparomslutning är en obruten plätering av koppar som går från hålväggen och ut över viapaddens yta (eller upp på ytan på ett innerlager om kortet har begravda vior) med en längd på minst 25 um.
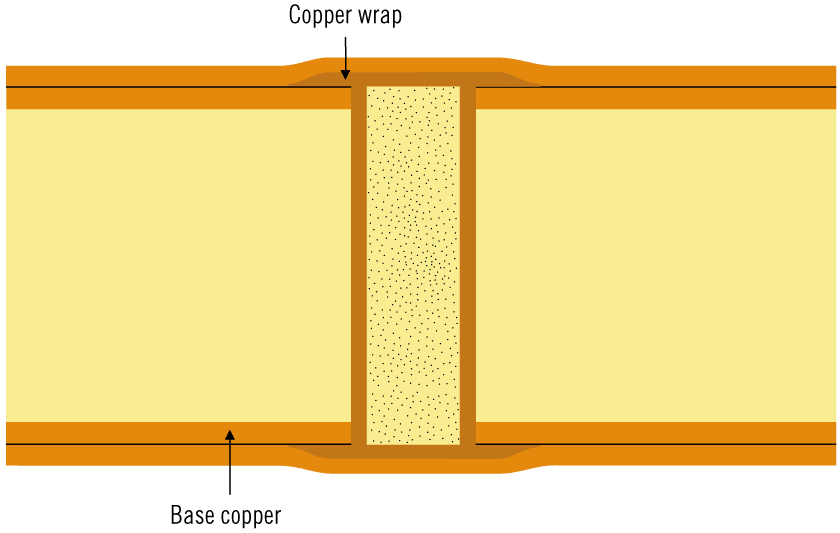
För klass 2 krävs att tjockleken på ytbeläggningen av kopparomslutningen är minst 5um. För klass 3-krav kommer detta att variera beroende på var denna funktion ligger i uppbyggnaden. Kontakta våra tekniker för mer information om krav på klass 3 krävs.
Vad är kontrollerad impedans?
Kontrollerad impedans är en signal som utbreder sig längs en ledare. Att kontrollera impedansen innebär att bestämma hur signalen uppträder eller hur fort den färdas längs ledaren. Signalen är relaterad till den aktuella ledarens resistans, kapacitans och konduktans. Impedansen mäts i ohm och är inte samma sak som resistans, vilket är en likströmsegenskap. Impedansen är en växelströmsegenskap, vilket innebär att den är frekvensberoende.
Finns det flera typer av kontrollerad impedans?
Ja, och de förklaras nedan:
Differentiell impedans – Impedansen i ett ledarpar där signalerna har samma amplitud men går i motfas.
Odd-mode-impedans – Impedansen hos den ena ledaren av ett ledarpar när ledarna drivs med signaler i motfas och har samma amplitud.
Even-mode-impedans – Impedansen hos ena sidan av ett ledarpar när ledarna drivs med signaler i fas som har samma amplitud.
Common-mode-impedans – Impedansen hos ett ledarpar när det drivs med signaler i fas som har samma amplitud.
Vad menas med termiska paddar?
För komponenter som är anslutna i plan på ytterlager skall termiska anslutningar användas för att simulera samma termiska massa i båda termineringarna. Detta för att undvika Manhattan-effekten (tombstoning), vridna komponenter och i värsta fall trasiga komponenter. Manhattaneffekten är mest påtaglig när det gäller mindre ytmonterade komponenter.
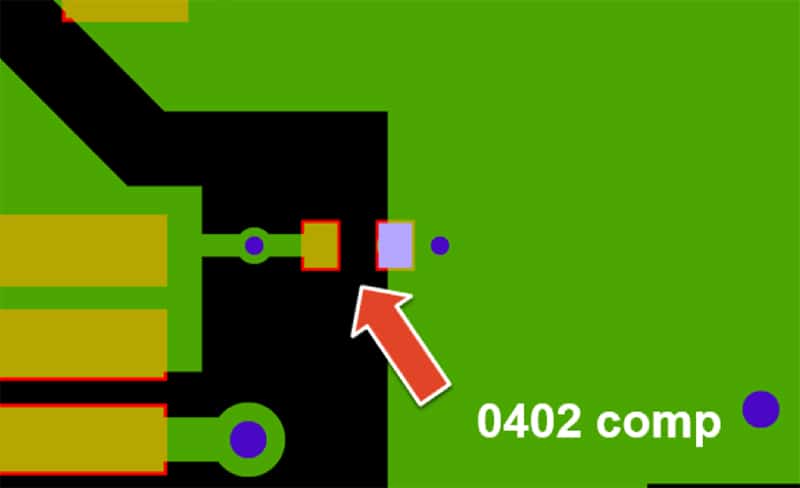
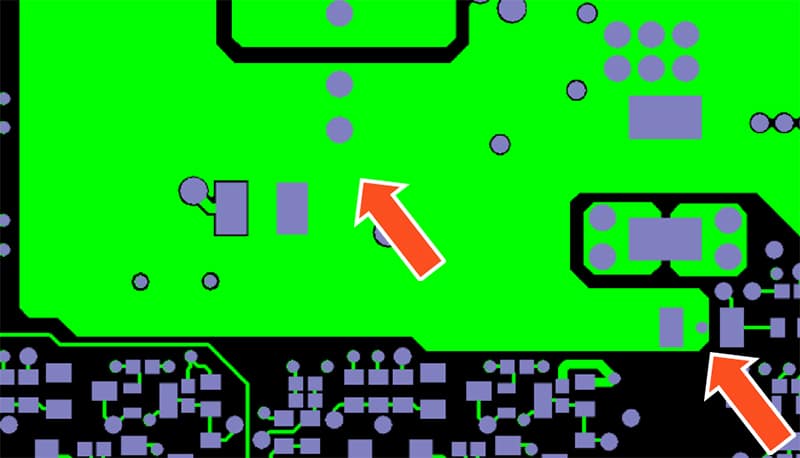
För hålmonterade komponenter som är anslutna i plan på innerlager används ”thermal reliefs” på de inre lagerplanen för att underlätta vätning i hålet. Formler för designen av “thermal reliefs” finns i IPC-2220-serien.
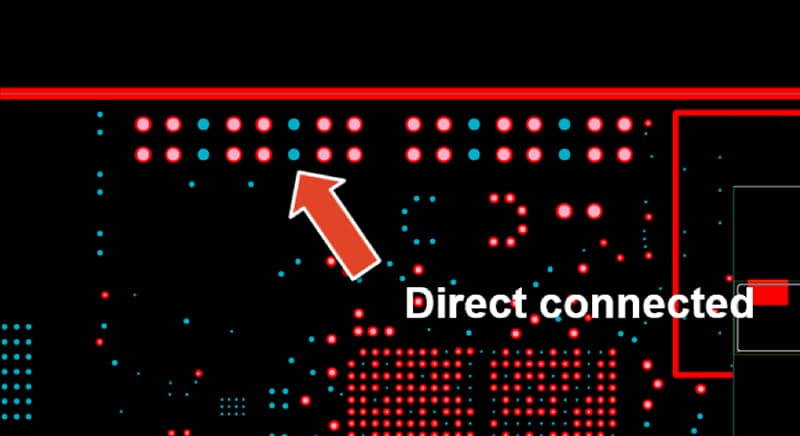
Bör man ange i inköpsunderlaget att kragförstärkningar är tillåtna?
Enligt nya IPC-6012D punkt 3.4.2 tillåts mönsterkortstillverkaren lägga till kragförstärkningar på mönsterkort som skall uppfylla klass 1 & 2.
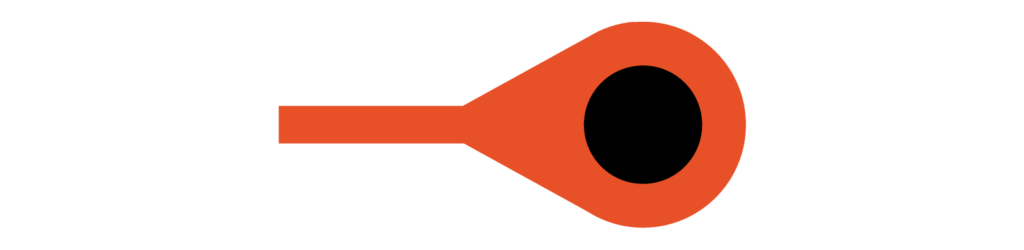
Om du inte tillåter att kragförstärkningar läggs till måste detta anges i inköpsdokumentationen. Se bara till att hålkragen räcker till.
Vad innebär ”back-drilling”?
Vid högfrekventa tillämpningar måste vi förhindra signalförluster. När signalen färdas från ett lager till ett annat måste den passera ett viahål som kopplar samman lagren. Om signalen t.ex. ska gå från lager ett till lager två i ett kort med 20 lager, betraktas den del av via-strukturen som går mellan lager 3 och 20 som ”överflödig”. I detta fall är det lämpligt att ta bort den del av hålet som inte används eftersom den fungerar som antenn och påverkar signalen negativt.
Back-drilling används för att ta bort den del av hålet som är överflödig (kontrollerad djupborrning i z-axeln) för att borra bort den ”överflödiga” delen av hålet och får därigenom en mer stabil signal. Ju kortare stubben är på den överflödiga delen av hålet, desto bättre blir resultatet. Back-drilling-storleken bör normalt vara 0,2 mm större än motsvarande via.
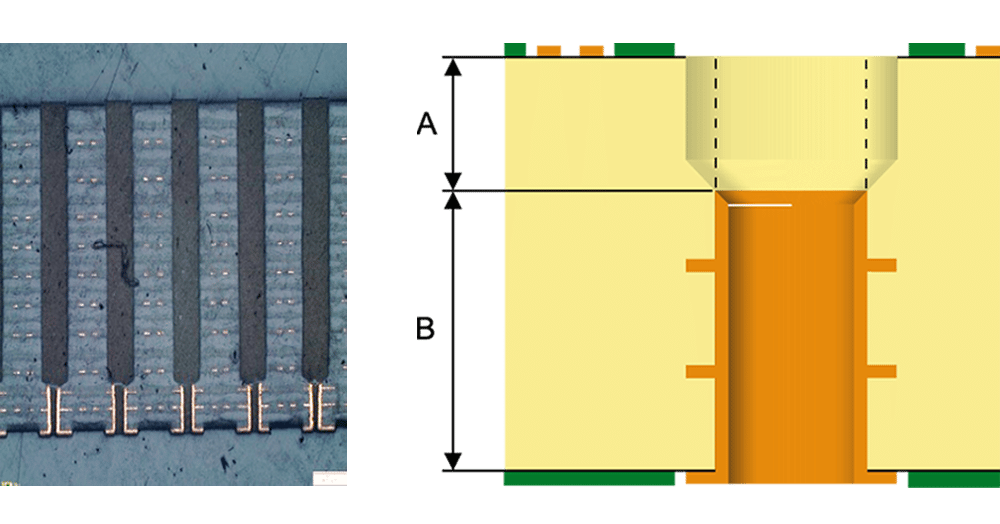
BACK DRILLING / COUNTER BORE (mm) | |||
---|---|---|---|
A: Depth tolerance | +/-0.20 | +/-0.15 | +/-0.10 |
B: Min. remain thickness and tolerance | 0.5+/-0.25 | 0.35+/-0.1 | 0.3+/-0.1 |
Vad betyder ”UL-märkning”?
Säkerhet är A och O i elektronikbranschen. Användarna måste helt enkelt kunna lita på den färdiga produkten i fråga om faktorer som brand- och elsäkerhet. Märkningen innebär att mönsterkorten med dess ingående material har testats och godkänts av (UL) Underwriters Laboratories på en rad parametrar enligt uppgjorda standarder som till exempel brandklassning. Att kunna erbjuda UL certifierade mönsterkort är mycket viktigt för alla mönsterkortsfabriker som vill agera på den internationella marknaden.
Vad är ett ”copper coin” mönsterkort?
Ett copper coin mönsterkort är ett flerlagerskort med ett tillägg av en solid kopparbit, ett så kallat ”coin” (mynt), inbäddat i mönsterkortets stack-up. Detta möjliggör en direkt termisk anslutning från den ena sidan till den andra eller från ett specifikt lager till ett yttre lager.
Läs mer om copper coin
VIA HOLE
Vilken typ av viahålsplugging rekommenderas?
För standardprodukter där fyllda och överpläterade vior enligt IPC-4761 Type VII inte krävs rekommenderar NCAB IPC-4761 Type VI-b, ”fyllda och täckta”. Bilden nedan visar lödmaskfyllt och täckt viahål. Epoxyfyllning är ett annat bättre alternativ, dock är kostnaden något högre.
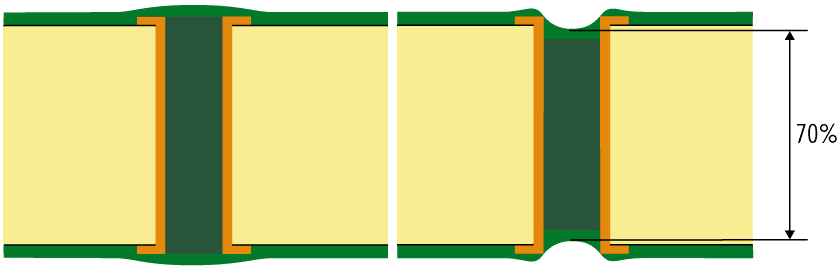
Enkelsidig pluggning/täckning rekommenderas inte p.g.a. att kemikalier från tillverkningen lätt blir instängda i hålet, även lodkulor kan uppträda när ytbehandlingen är HASL (Hot Air Solder Leveling).
Vad är ett överpläterat viahål?
Det är när viahålet fylls med epoximassa och sedan täcks med ett lock av pläterad koppar och kategoriseras av IPC-4671 som typ VII – fyllt och täckt viahål. Koppartjockleken på locket ska vara minst 5µm för klass 2 och 12µm för klass 3.
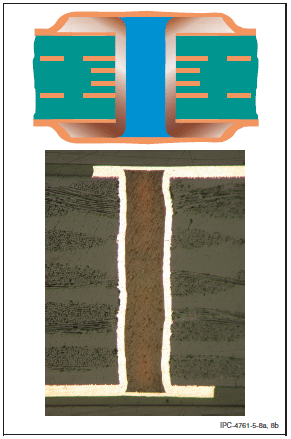
Denna pluggning används främst för designer med via i pad eller i BGA applikationer med hög densitet. Även testpunkter som är placerade i viahål kan behöva denna typ. För klass 2 är kravet att koppartjockleken på omslutningen minst 5um, men för klass 3 varierar kravet beroende på var i designen den är placerad. Kontakta våra tekniker för ytterligare information om klass 3 kraven.
MATERIAL
Måste jag använda ett FR4-material med högt Tg (Tg = glasomvandlings-temperaturen) vid blyfri lödning?
Nej, inte nödvändigtvis. Det är många faktorer som inverkar, t ex antal lager, koppartjocklek, minsta håldiameter, tjocklek och svårighetsgraden på kortet. Vissa undersökningar har visat på att ett material med ”standard” Tg-värde t.o.m. har presterat bättre än vissa material med högre Tg. Notera att även vid ”blyad” lödning överstigs Tg-värdet. Genom att känna till hur materialet beter sig vid temperaturer över Tg-värdet (post Tg) kan man samla in tillräcklig information för att göra det rätta materialvalet för produkten.
Vilka materialegenskaper är viktiga vid val av material?
De viktigaste parametrarna är:
CTE
Ett mått på hur mycket materialet expanderar när det värms upp. Det som är kritisk är expansionen i Z-led, alla epoxybaserade material har normalt två faser av expansion, en lägre expansionsgrad vid temperaturer under Tg och en högre expansionsgrad vid temperaturer över Tg.
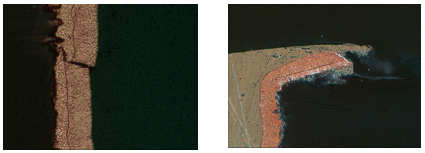
Om materialets CTE egenskaper inte är anpassat till dom temperaturcykler som det utsätts för under montage och i drift så finns det stor risk att mönsterkortet fallerar genom att pläteringarna i hålen brister / mattas ut.
Tg / GLASOMVANDLINGSTEMPERATUR
Tg-värdet är den temperatur då materialet ändras från ett förhållandevis styvt tillstånd till mer elastiskt och böjbart. Viktigt att känna till är att vid temperaturer över Tg så förändras materialegenskaperna.
Td / NEDBRYTNINGSTEMPERATUR
Detta är ett mått på nedbrytningen av materialet. Metoden mäter när 5% av materialet förlorat vikt – den punkt vid vilken tillförlitligheten äventyras och delaminering kan inträffa. För mönsterkort med högre tillförlitlighetskrav och multipla lödoperationer rekommenderas Td ≥ 340 ℃.
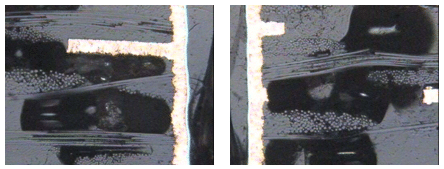
T260 / T288 / TID TILL DELAMINERING
En tidsangivelse på hur länge materialet klarar att utsättas för en fördefinierad temperatur (260°C eller 288°C) innan det delaminerar. T.ex. 30 minuter.
Måste jag använda ett FR4-material med högsta Td (Td = nedbrytnings-temperatur) vid blyfri lödning?
Ett högre Td-värde kräver ett bättre material vilket är att föredra om kortet utsätts för flera / krävande omsmältningslödningar. Att ha koll på sin monteringsprocess underlättar valet av rätt material.
Vad är skillnaden mellan ”Dicy” resp. ”nonDicy” som härdsystem i FR4-epoxin?
Dicy (Dicyandiamine) är det i särklass vanligaste härdsystemet för epoxin, detta ger normalt ett Td-värde på ca 300–310°C medan ett ”nonDicy” d.v.s. Phenolic Cured Epoxi har ett Td-värde på ca 330–350°C och står därför emot den högre temperaturen bättre.
Vad menas med ”CAF”?
CAF (Conductive Anodic Filament), betyder att det blir en elektrokemisk reaktion mellan koppar anod och katod, vilket kan ge en kortslutning internt i materialet.
Vilken ytbehandling är ”bäst” för blyfri lödning?
Det finns ingen ”bästa ytbehandling”, alla ytbehandlingar har sina för- och nackdelar. Vad man ska välja beror på många faktorer. Rådgör gärna med våra tekniker.
Vad är det som gäller avseende flamskyddsmedel, blev det ett nationellt förbud mot TBBP-A som är den dominerande i elektronik?
Nej, utredningen kom fram till att det inte är praktiskt möjligt att förbjuda TBBP-A.
Vad är skillnaden mellan flamskyddsmedel tillsatt i reaktiv, resp. additiv form?
Ett reaktivt tillsatt flamskyddsmedel är kemiskt bundet till epoxyn (en ny molekylkedja har bildats) och kan därför inte lakas ur vid exempelvis deponering. Ett additivt flamskyddsmedel är däremot inte kemiskt bundet och därför finns risk för urlakning. I epoxybaserade mönsterkort (FR4, FR5) så är flamskyddsmedlet reaktivt tillsatt.
Hur många omsmältningar tål FR4 – material?
Det går inte att ge ett rakt svar på det eftersom det är helt beroende på vilken lödprofil man använder sig av. Vår rekommendation är att välja ett mer högpresterande material (Högre Td, Lägre CTE) när det är fler lager än 4 och framförallt tjockare kort än 1.6mm.
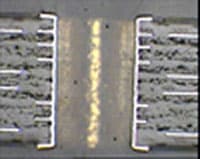
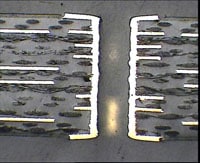
RoHS
Kräver RoHS- eller WEEE-direktiven märkning av mönsterkortet?
Nej, men av praktiska skäl bör mönsterkort som har blyfri varmförtenning märkas med tydlig märkning som anger RoHS-kompabilitet p.g.a. risk för förväxling med blyad varmförtenning.
Är RoHS-kompatibla mönsterkort även halogenfria?
Nej, inte nödvändigtvis. RoHS-direktivet förbjuder två bromerade flamskyddsmedel, PBB (PolyBromerade Bifenyler) och PBDE (PolyBromerade DifenylEtrar). Det som normalt används i mönsterkort är ett bromerat flamskyddsmedel som heter TBBP-A (Tetra BromoBisPhenol A).