Zestawiliśmy poniżej listę niektórych pytań, na które często udzielamy odpowiedzi, i tematów, które często są przedmiotem dyskusji.
HDI
Czym jest mikroprzelotka (microvia)?
Zgodnie z nową definicją podaną w IPC-T-50M mikroprzelotka to otwór ślepy z maksymalnym współczynnikiem 1:1, wywiercony na docelowej powierzchni styku do głębokości całkowitej nie większej niż 0,25 mm od pola pochłaniającego foli do docelowej powierzchni styku.
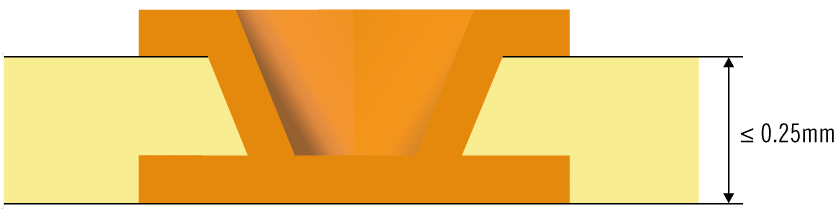
Czym jest ślepa przelotka?
Jest to otwór biegnący od warstwy zewnętrznej do warstwy wewnętrznej, jednak nieprzechodzący na wylot całej płytki PCB. Otwory takie można wiercić mechanicznie lub za pomocą lasera. Ilustracja pokazuje wywierconą laserowo ślepą przelotką.
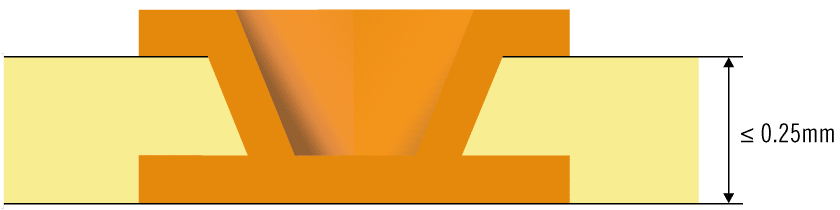
Co to znaczy przelotka zagrzebana?
Jest to otwór przenikający przez jedną lub kilka warstw wewnętrznych PCB. Otwory te zwykle są wiercone mechanicznie.
Czym jest płytka HDI PCB?
Norma IPC-2226 definiuje HDI jako płytkę drukowaną o większej gęstości połączeń (ścieżek) na jednostkę powierzchni niż w przypadku konwencjonalnych płytek drukowanych (PCB). Cechuje się ona cieńszymi ścieżkami i odstępami ≤ 100 µm / 0,10 mm, mniejszymi przelotkami (<150 µm) i polami pochłaniającymi (ang. capture pads) 20 pól/cm2) niż w przypadku konwencjonalnej technologii PCB.
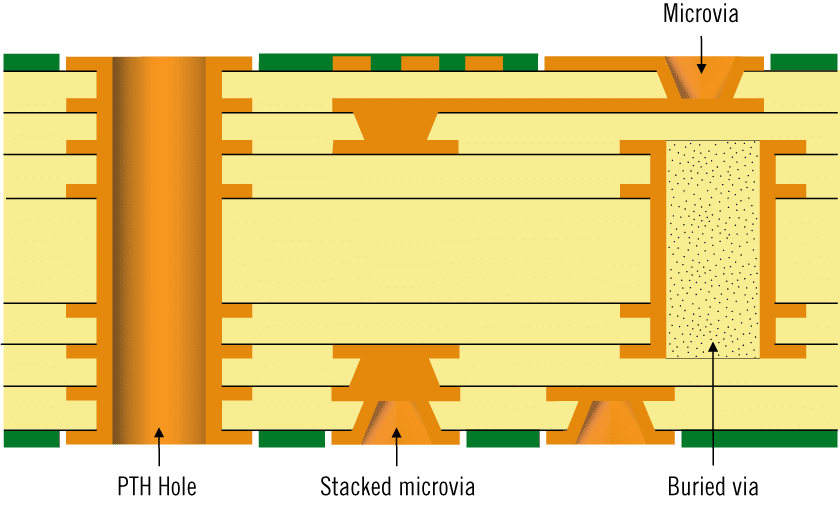
Czy płytki HDI są zróżnicowane pod względem cech?
Poniższa ilustracja przedstawia strukturę główną płytek typu I, II i III zgodnie z definicją normy IPC-2226.
Type I. Pojedyncza warstwa mikroprzelotek z jednej lub z obydwu stron rdzenia. Do połączeń stosowane są zarówno mikroprzelotki metalizowane, jak i metalizowane otwory przelotowe (PTH), z użyciem przelotek ślepych (ang. blind via), ale bez przelotek zagrzebanych (ang. buried via).
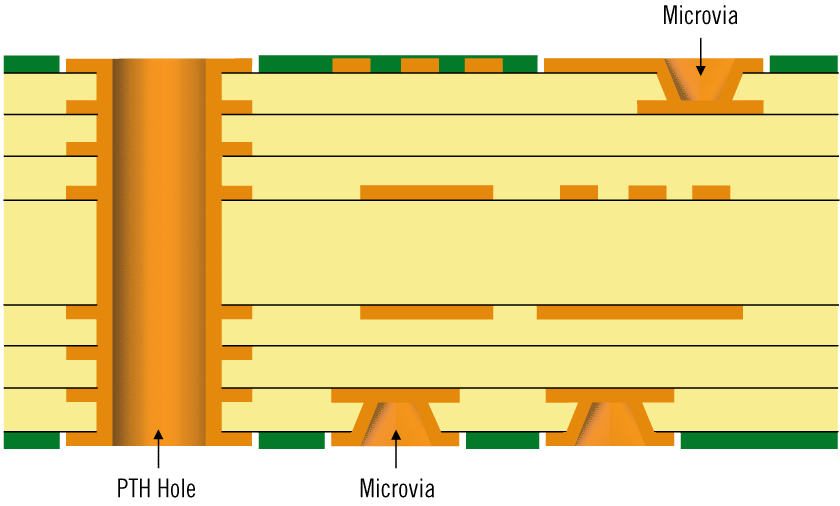
Type II. Pojedyncza warstwa mikroprzelotek z jednej lub z obydwu stron rdzenia. Do połączeń stosowane są zarówno mikroprzelotki metalizowane, jak i metalizowane otwory przelotowe (PTH). Występują zarówno przelotki ślepe (ang. blind via), jak i przelotki zagrzebane (ang. buried via).
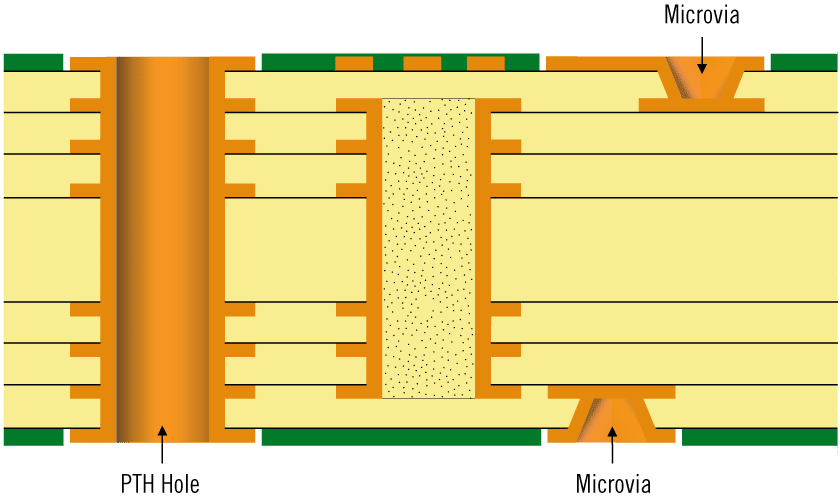
Type III. Przynajmniej dwie warstwy mikroprzelotek z jednej lub z obydwu stron rdzenia. Do połączeń stosowane są zarówno mikroprzelotki metalizowane jak i metalizowane otwory przelotowe (PTH). Występują zarówno przelotki ślepe (ang. blind via), jak i przelotki zagrzebane (ang. buried via).
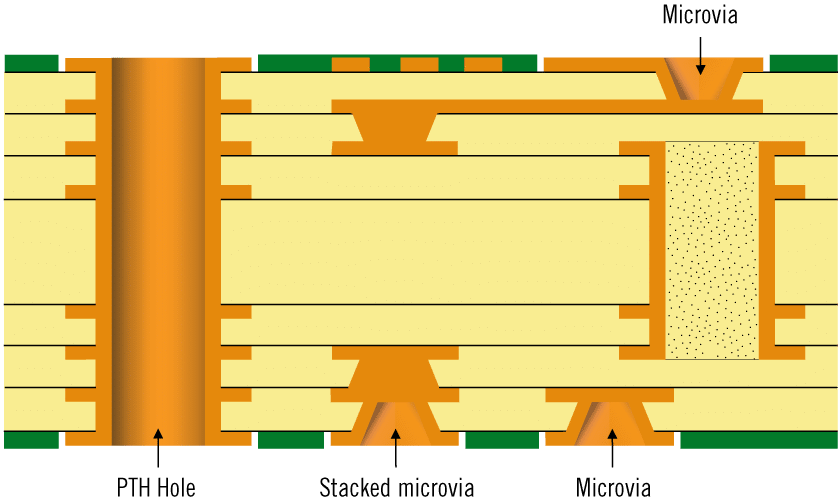
Terminologia określająca stopień złożoności konstrukcji płytki HDI:
- 1+n+1 = pojedyncza warstwa mikroprzelotek (typ I i II powyżej)
- 2+n+2 = 2 warstwy mikroprzelotek (typ III powyżej)
- 3+n+3 = 3 warstwy mikroprzelotek
FLEX/RIGID-FLEX
Jakie są dostępne struktury dla giętkich i sztywno-giętkich płytek drukowanych?
Istnieje wiele różnych struktur. Najczęstsze z nich zdefiniowano poniżej:
Jednostronna elastyczna (IPC-60103 typu 1) Warstwa wierzchnia (poliamid + klej) przyklejona do bezklejowego jednostronnego rdzenia elastycznej płytki drukowanej. Z usztywnieniami lub bez.

Dwustronna elastyczna (IPC-6013 typu 2) Warstwa wierzchnia przyklejona po obu stronach bezklejowego dwustronnego rdzenia elastycznej płytki drukowanej (dwie warstwy przewodzące) z platerowanymi otworami przelotowymi. Z usztywnieniami lub bez.

Wielowarstwowa elastyczna (IPC-6013 typu 3) Warstwa wierzchnia przyklejona po obu stronach bezklejowej konstrukcji zawierającej trzy lub więcej warstw przewodzących z platerowanymi otworami przelotowymi. Z usztywnieniami lub bez. Możliwe są cztery warstwy.
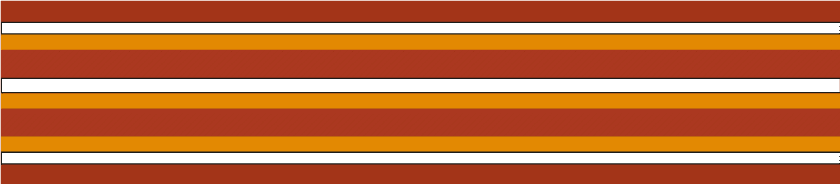
Tradycyjna sztywno-giętka konstrukcja (IPC-6013 typu 4) Wielowarstwowa kombinacja obwodów sztywnych i giętkich zawierająca trzy lub więcej warstw z platerowanymi otworami przelotowymi. Możliwe są 22 warstwy z 10 warstwami giętkimi.
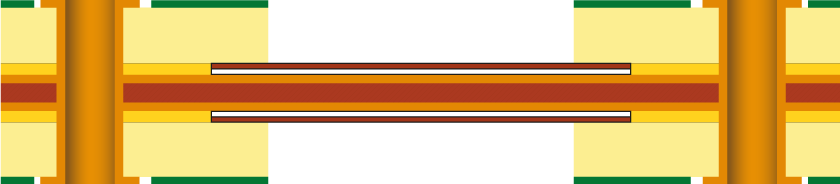
Asymetryczna sztywno-giętka konstrukcja, w której giętka płytka drukowana znajduje się na zewnętrznej warstwie sztywnej konstrukcji. Zawiera ona trzy lub więcej warstw z platerowanymi otworami przelotowymi.
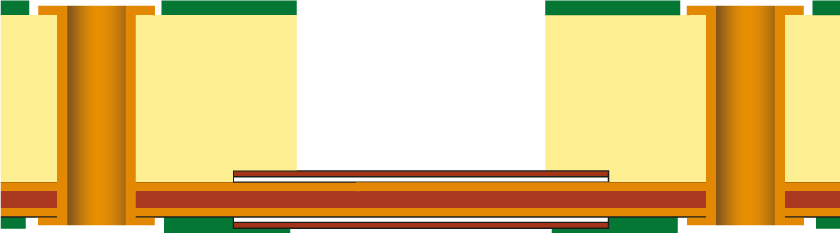
Sztywna, wielowarstwowa, giętka konstrukcja z zagrzebaną/ślepą przelotką (mikroprzelotką) jako częścią sztywnej konstrukcji. Możliwe są 2 warstwy mikroprzelotki. Konstrukcja może również obejmować dwie sztywne struktury jako część jednorodnej budowy. Możliwa jest struktura o dużej gęstości połączeń (HDI) w konfiguracji 2 + n + 2.
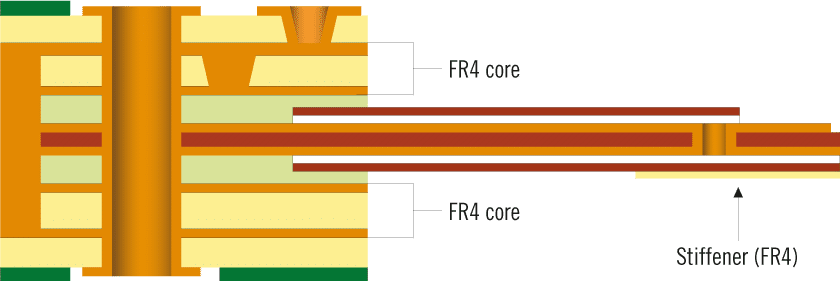
O budowie książki-segregatora i ze szczeliną powietrzną – budowa złożona, z przestrzeniami między warstwami giętkimi, aby umożliwić lepsze zginanie giętkiej płytki drukowanej. W konstrukcjach o budowie książki-segregatora warstwy giętkie mogą mieć różne długości, aby zminimalizować ściskanie wewnętrznych warstw elastycznych w promieniu gięcia.
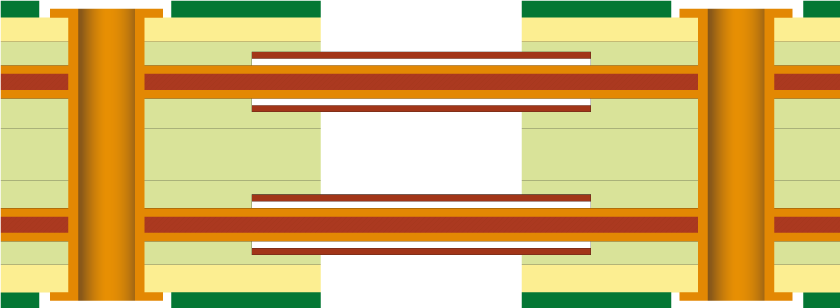
Jak obliczyć prawidłową długość giętkiej części sztywno-giętkiej struktury, aby uwzględnić minimalny promień gięcia?
Szczegółowe zalecenia można znaleźć w IPC-2223, rozdziały 5.2.3.3, zarówno dla zgięć statycznych, jak i dynamicznych, które powinny być stosowane do ostatecznej weryfikacji projektu. Jednak niektóre podstawowe wytyczne oparte na grubości materiału giętkiego można zobaczyć poniżej:

FLEX TYPE | MINIMUM BEND RADIUS |
---|---|
Single sided flex | 3 – 6 x circuit thickness |
Double sided flex | 7 – 10 x circuit thickness |
Multilayer flex | 10 – 15 x circuit thickness |
Dynamic application | 20 – 40 x circuit thickness |
Jaka jest różnica między płytką półgiętką a sztywno-elastyczną?
Płytka półgiętka jest w rzeczywistości „standardową” wielowarstwową płytką drukowaną, zbudowaną przy użyciu określonych typów FR-4, które zostały pocienione do określonej tolerancji, dzięki czemu uzyskany cieńszy obszar zapewnia elastyczny / zginany odcinek tradycyjnie sztywnego FR-4. Płytka półgiętka nadaje się do zastosowań statycznych (giętka do montażu) lub o bardzo ograniczonej liczbie zgięć.
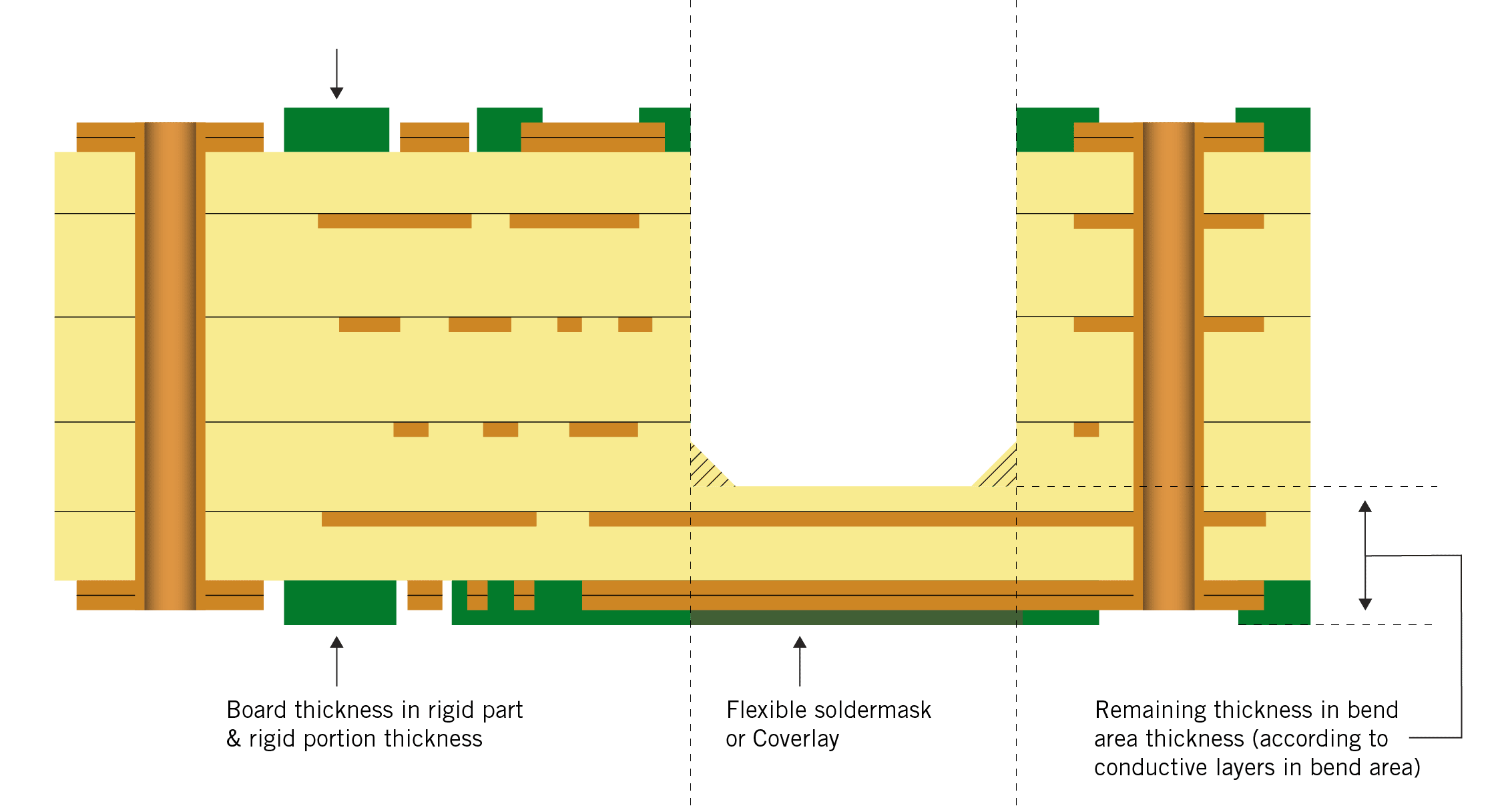
Jaka jest różnica między giętkimi systemami klejowymi a bezklejowymi?
Struktury wykorzystujące systemy klejowe polegają na użyciu kleju do łączenia miedzi z elastycznym rdzeniem. Jako taka, warstwa kleju wraz z pełną wierzchnią warstwą przenika do sztywnej konstrukcji i bezpośrednio do otworu. Większy współczynnik rozszerzalności kleju zwiększa ryzyko problemów z otworami przelotowymi, takich jak pęknięcia i uszkodzenia otworów przelotowych w wyniku rozszerzalności, a obecność tego materiału w samym otworze może prowadzić do problemów z tworzeniem się miedzi w ściankach otworów wynikających ze złego zanikania kleju.
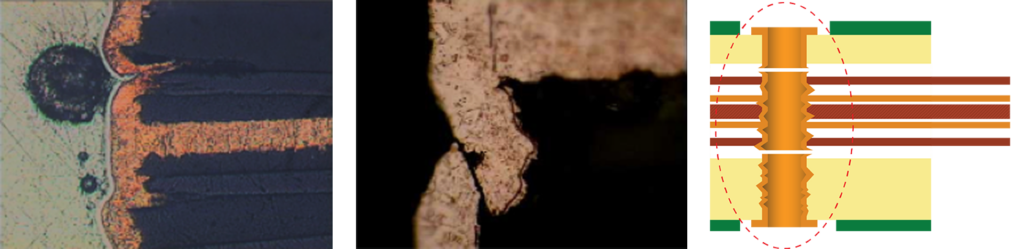
Rozwiązaniem poprawiającym niezawodność przelotki / otworu przelotowego było odejście w kierunku bezklejowego systemu platerowania miedzią (miedź połączona bezpośrednio z poliamidem) i ograniczenie nakładania się warstwy wierzchniej na sztywną część płytki. Zapewnia to znacznie bardziej niezawodną strukturę otworu bez wnikania kleju w otwór. Jest to zdecydowanie najczęstsze podejście stosowane do płytek sztywno-giętkich.
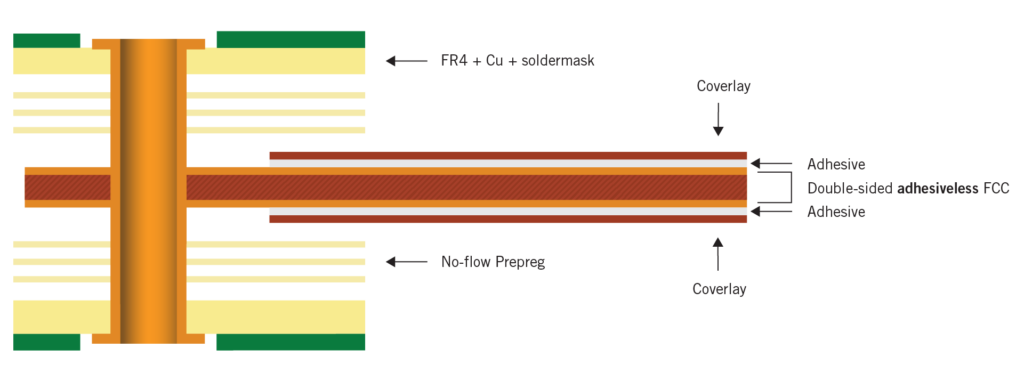
DESIGN RULES
Jaki jest minimalny rozmiar pola lutowniczego na warstwie zewnętrznej/wewnętrznej?
Jest to zależne od producenta, ale ogólnie można powiedzieć, że większość z nich produkuje płytki przy następujących stosunkach wielkości:
A = 0.15 mm
B = 0.20 mm
C = 0.30 mm
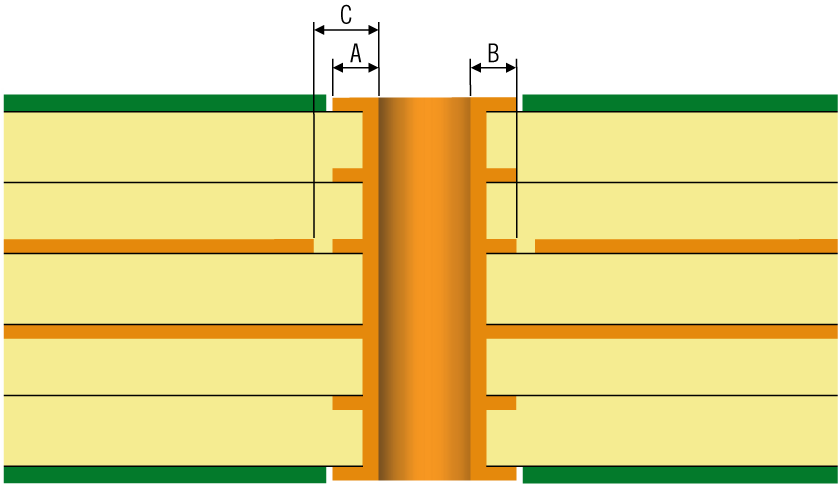
Gdy potrzebne są mi ścieżki szersze, niż standardowe, jaką szerokość powinienem zastosować?

Mówiąc ogólnie, im grubsza warstwa miedzi, tym szersze powinny być ścieżki. Praktycznym podejściem jest zasada, że przy warstwie miedzi o grubości 18 µm ścieżka nie powinna być węższa, niż 0,1 mm (4 mil), a przy warstwie miedzi o grubości 105 µm ścieżka nie powinna być węższa, niż 0,25 mm (10 mil).
Jak dużo powstanie miedzianych produktów?
Panuje błędne przeświadczenie, że miedź o danej wadze zapewnia pewną dokładnie określoną grubość i nie ulegnie ona zmniejszeniu podczas produkcji płytek PCB. Na przykład 1 oz = 35um lub ½ oz. = 18 um.
Jednakże w normie IPC-6012 wyszczególniono minimalną dopuszczalną grubość folii miedzianej oraz folii po metalizowaniu. Dane te zostały oparte na dopuszczalnych tolerancjach dla folii miedzianej oraz redukcji metalizowania miedzi podczas kolejnych procesów przetwarzania.
Poniżej wyszczególniono niektóre masy miedzi oraz dopuszczalne grubości wykończenia.
Przede wszystkim należy dokładnie określić specyfikację. W przeciwnym wypadku można podać zbyt wysoką lub zbyt niską specyfikację, co prowadzi do zbyt wysokich kosztów produkcji. Aby uzyskać więcej informacji, należy skontaktować się z naszymi technikami.
Grubość wewnętrznej warstwy foli po przetworzeniu | |
Podstawowa waga miedzi | Minimalna grubość wykończenia po przetworzeniu |
1/2 oz. | 11.4 um |
1 oz. | 24.9um |
2 oz. | 55.7um |
Grubość zewnętrznego przewodnika po metalizowaniu i przetworzeniu | ||
Podstawowa waga miedzi | Minimalna grubość wykończenia po przetworzeniu | Minimalna grubość wykończenia po przetworzeniu |
1/2 oz. | 33.4um | 38.4um |
1 oz. | 47.9um | 52.9um |
2 oz. | 78.7um | 83.7um |
Czy powinniśmy usuwać lub pozostawiać niefunkcjonalne podkładki?
W IPC-2222A punkt 9.1.4 jasno określono, że wytwórca nie powinien ich usuwać, ale wiele zakładów prosi, aby je usunąć w celu osiągnięcia lepszej wydajności produkcji. Jeśli nie są one krytyczne dla działania, zalecamy umożliwienie ich usunięcia.
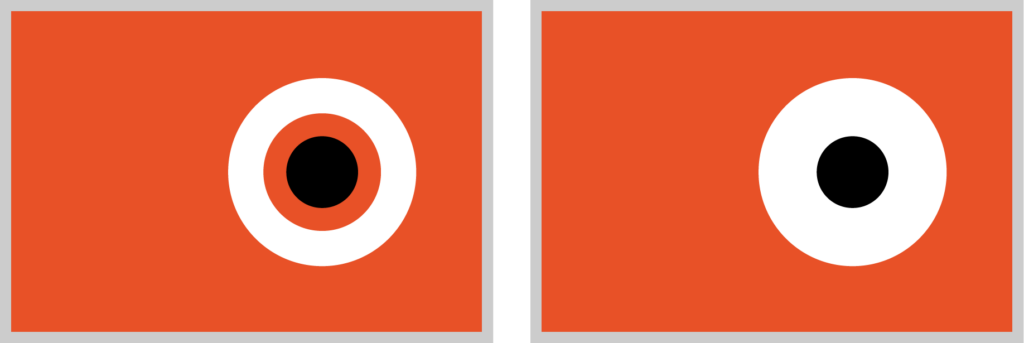
Co oznacza ten sam odstęp netto?
„Ten sam odstęp netto” oznacza, że odległość miedź-miedź w tej samej sieci elektrycznej jest zbyt mała, aby można ją było wyprodukować zgodnie z plikami Gerber.
Ponieważ znajduje się w tej samej sieci, DRC (kontrola reguł projektowych) w oprogramowaniu CAD klienta nie alarmuje o tym problemie. Ważne jest, aby klient przy rozpoczynaniu nowego projektu prawidłowo ustalił granice. Minimalna odległość miedź-miedź jest zwykle ustawiona prawidłowo, ale brakuje jej ustawienia tej samej wartości w tej samej sieci. Nie jest to duży problem, ale powoduje opóźnienia i niepotrzebne pytania techniczne.
Dlaczego istnieje zapotrzebowanie na tak dużą odległość od krawędzi otworu do miedzi w przypadku otworów nieplaterowanych (NPTH)?
Kiedy wiercisz otwory w płytce drukowanej, chcesz wywiercić wszystkie otwory w tym samym zestawie, aby uzyskać najlepszą dokładność położenia otworów. Otwory nieocynkowane należy wtedy zablokować podczas procesu galwanizacji (w przeciwnym razie również będą galwanizowane). Aby móc zablokować NPTH, potrzebujemy odstępu między krawędzią otworu a miedzią. Potrzebna odległość jest związana z grubością miedzi. Dla standardowej grubości miedzi (18µm miedzi bazowej) dobrą wartością jest 0,3mm i zdecydowanie nie mniej niż 0,2mm.
TERMINOLOGY
Co to jest współczynnik proporcji ( ang. „aspect ratio”)?
Jest to stosunek średnicy otworu do jego długości. Gdy producent stwierdza, że współczynnik proporcji produktu wynosi 8:1, oznacza to, że na przykład średnica otworu wynosi 0,20 mm w płycie o grubości 1,60 mm. W przypadku płytek HDI odpowiedni współczynnik proporcji dla mikroprzelotki to typowo 0,8:1, przy czym preferowany jest współczynnik 1:1 jako ułatwiający metalizowanie.
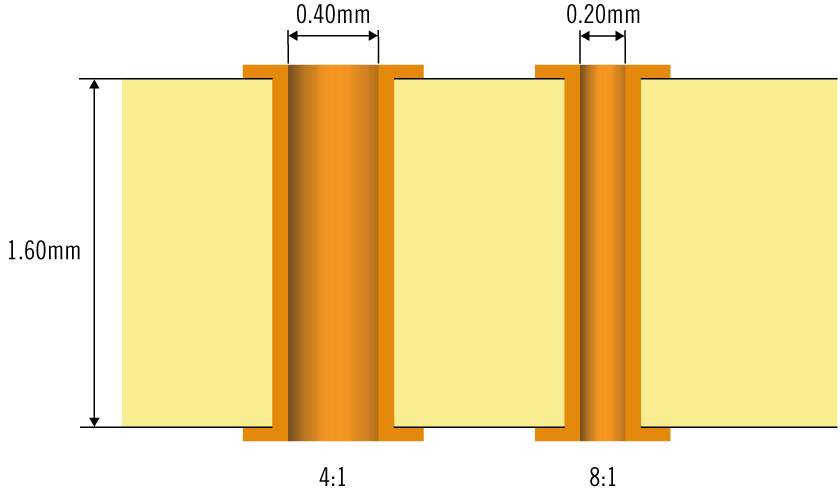
Czym jest owijka miedziana?
Owijka miedziana (ang. copper wrap) to ciągła warstwa cynowanej miedzi umieszczona wewnątrz tulei otworu i wyprowadzona na powierzchnię płytki PCB (lub powierzchnię warstwy wewnętrznej w przypadku płytek HDI) na co najmniej 25 µm.
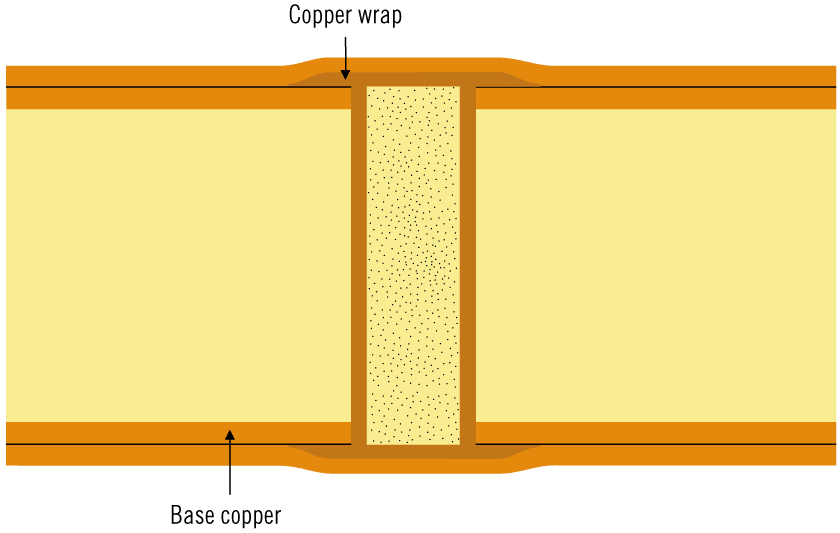
W przypadku wymagań klasy 2 grubość warstwy powierzchniowej miedzi to przynajmniej 5 µm, natomiast dla klasy 3 grubość zależy od umiejscowienia otworu. Prosimy o kontakt z działem technicznym w celu uzyskania dalszych informacji na temat wymagań klasy
Czym jest kontrolowana impedancja?
Rozważmy sygnał w płytce drukowanej, który przemieszcza się wzdłuż ścieżki, kontrolowanie impedancji oznacza kontrolowanie jakości lub prędkości tego sygnału w punkcie wzdłuż ścieżki. Jest ono związane z opornością, pojemnością i przewodnością danej ścieżki. Impedancja również mierzona jest w omach, różni się ona od rezystancji, która jest cechą prądu stałego. Impedancja jest cechą prądu przemiennego, co oznacza, że związana jest ona z częstotliwością.
Czy istnieje więcej niż jeden rodzaj kontrolowanej impedancji?
Tak, istnieje i zostało to wyjaśnione poniżej:
Impedancja różnicowa – Impedancja pary przewodników o równych i przeciwnie spolaryzowanych sygnałach – taka sama amplituda w przeciwfazie ze sobą.
Impedancja modu nieparzystego – Impedancja jednej strony pary przewodników, które mają równe sygnały o przeciwnej polaryzacji – taka sama amplituda i przeciwfaza.
Impedancja modu parzystego – Impedancja jednej strony pary przewodników, które mają równe sygnały – taka sama amplituda i taka sama polaryzacja
Impedancja sygnału wspólnego – Impedancja pary przewodników, które mają równe sygnały – taka sama amplituda i taka sama polaryzacja.
Co to jest podkładka termiczna?
W przypadku elementów SMD, zwłaszcza tych mniejszych, należy użyć podkładek termicznych, aby zasymulować tę samą masę termiczną na obu końcach w celu uniknięcia zginania, skręcania lub nawet, w najgorszym przypadku, złamania elementów.
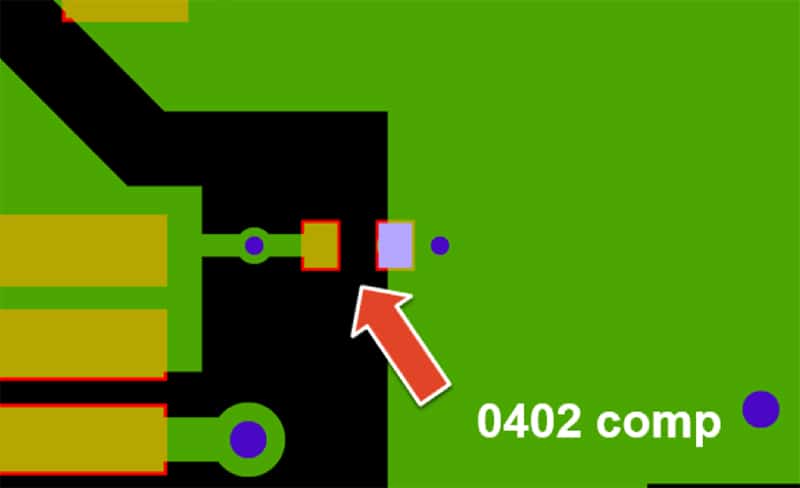
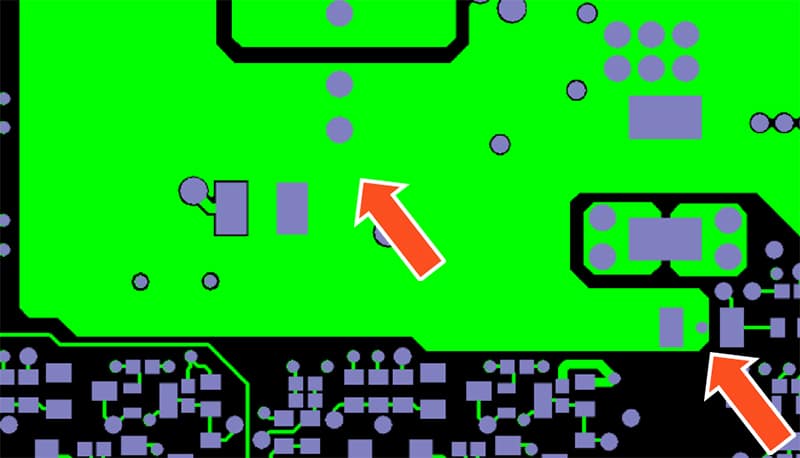
W przypadku elementów montowanych w otworach (HMD) stosujemy reliefowe podkładki termiczne na płaszczyznach warstwy wewnętrznej, aby pomóc zwilżyć wnętrze otworu. Wzory na reliefowe podkładki termiczne można znaleźć w serii IPC-2220.
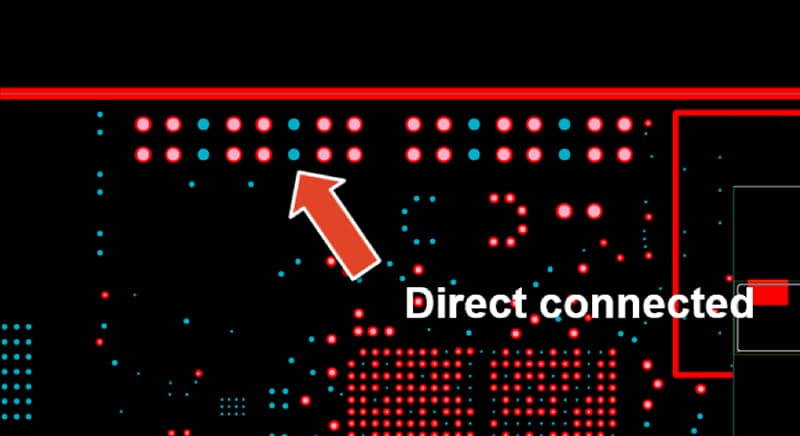
Czy w dokumentacji zamówienia należy dodać zgodę na dodanie łezki (teardrop)?
Zgodnie z nową sekcją 3.4.2 IPC-6012D dozwolone jest dodawanie tzw. teardrop do ścieżki , gdy płytki maja spełniać zgodność z klasami 1 i 2.
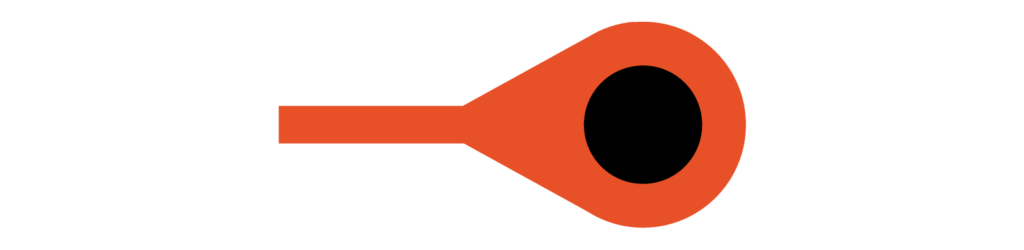
Jeśli nie chce się łezek, należy zaznaczyć to w dokumentacji zamówienia. Ale należy dodać wystarczający pierścień.
Czym jest technologia fazowania?
W zastosowaniach o wysokiej częstotliwości musimy zapobiegać utracie sygnału, a zatem gdy jedna warstwa jest połączona z drugą, a sygnał przemieszcza się z jednej warstwy do drugiej, musi przejść przez otwór łączący warstwy. Na przykład, jeśli sygnał ma przejść z warstwy pierwszej do drugiej na płytce 20-warstwowej, wówczas część struktury przelotki uważana jest za „nadmiar” i dla tego zastosowania najlepiej jest usunąć nadmiar miedzi z tego otworu, ponieważ działa on jak antena i wpływa na sygnał.
Fazowania (kontrolowana głębokość w osi Z) używamy do wywiercenia „nadmiaru” miedzi w otworze w celu uzyskania lepszej stabilności sygnału. Idealnie, im krótsza pozostałość („nadmiar” miedzi), tym lepszy wynik. Rozmiar wiertła do fazowania powinien być zwykle o 0,2 mm większy niż odpowiadająca mu przelotka.
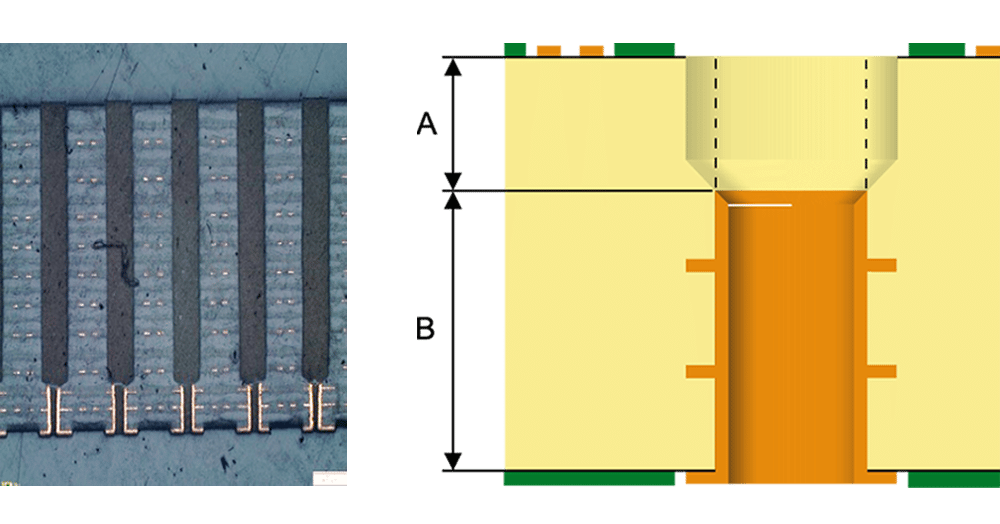
BACK DRILLING / COUNTER BORE (mm) | |||
---|---|---|---|
A: Depth tolerance | +/-0.20 | +/-0.15 | +/-0.10 |
B: Min. remain thickness and tolerance | 0.5+/-0.25 | 0.35+/-0.1 | 0.3+/-0.1 |
Co oznacza „oznakowanie UL”?
W przemyśle elektronicznym kluczowe jest bezpieczeństwo. Ważne jest, aby użytkownicy mogli polegać na gotowym produkcie, biorąc pod uwagę takie czynniki, jak bezpieczeństwo przeciwpożarowe i elektryczne, co oznacza, że zarówno płytka drukowana, jak i zawarte w niej materiały muszą spełniać najwyższe standardy. Aby zapewnić zgodność płytek, powszechną praktyką jest certyfikowanie przez UL materiałów składowych lub samej płytki drukowanej.
Na początek, czym jest UL? Litery UL oznaczają Underwriters Laboratories. Dlaczego uznanie UL jest ważne? UL jest ważnym autorytetem i cieszy się dobrą opinią w branży płytek drukowanych. Firma jest niezastąpiona w zakresie testowania bezpieczeństwa przeciwpożarowego i elektrycznego. Klienci z całego świata – w tym dobrze znane firmy chińskie – pożądają producentów mogących zdobyć uznanie UL. Uznanie UL jest zatem bardzo ważne dla fabryk produkujących płytki drukowane, aby produkować bezpieczne płytki i uzyskać dostęp do rynku międzynarodowego.
VIA HOLE
What type of via hole plugging is recommended?
The preferred type of plugging for standard product (not including capped via hole) is IPC 4761 type VI filled and covered, with target being complete fill. The image below shows type VI with liquid soldermask coverage.
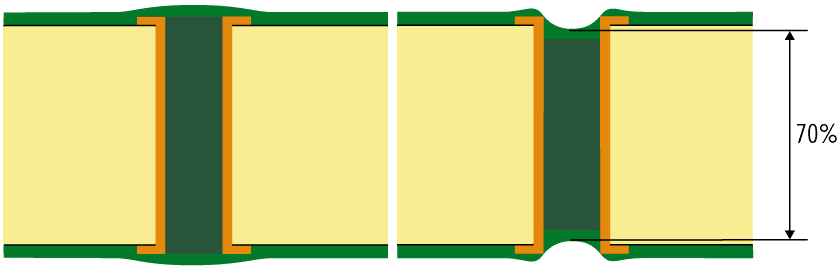
Single sided plugging is not recommended (including type II tented and covered) due to concerns over entrapment of chemistry or likelihood of solderballs being present with HASL finishes (LF and SnPb).
Czym jest przelotka pokrywana?
Przelotka pokrywana jest to przelotka metalizowana z naddatkiem, przez co metalizowana jest cała powierzchnia przelotki. Minimalna grubość miedzi/pokrycia wynosi 5 µm w przypadku wymaganej klasy 2 oraz 12 µm w przypadku wymaganej klasy 3.
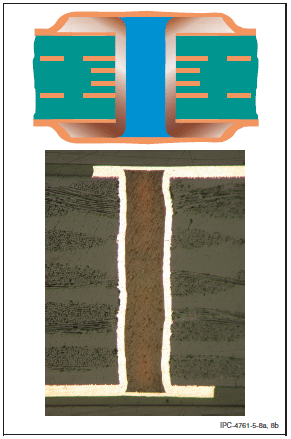
Uzależnione jest to od wypełnienia przelotki żywicą epoksydową zamiast maską lutowniczą, ponieważ żywica pozwala zminimalizować ryzyko powstawania pęcherzyków powietrza lub rozszerzania się wypełnienia w trakcie lutowania. Przelotkę taką można skategoryzować w ramach normy IPC-4761 jako typ VII – przelotki wypełnione i pokryte. Z reguły są one stosowane w przypadku przelotowych pól lutowniczych lub w zastosowaniach BGA.
MATERIAL
Czy konieczne jest stosowanie materiału FR4 o wysokiej temperaturze zeszklenia (Tg) w przypadku lutowania bezołowiowego?
Nie, nie jest to konieczne. Należy tutaj uwzględnić szereg czynników, np. liczbę warstw, grubość płytki PCB oraz dokładnie rozpoznany cykl montażu (liczba operacji lutowania, czas w temperaturze powyżej 260 stopni itp.). W niektórych badaniach wykazano, że materiał o „standardowej” temperaturze Tg sprawdzał się nawet lepiej niż pewne materiały o wyższej wartości Tg. Uwaga: nawet w przypadku lutowania z ołowiem wartość Tg jest przekraczana.
Najważniejsze jest zachowanie materiału w temperaturach powyżej wartości Tg (ang. post Tg), dlatego wiedza na temat tego, jakim temperaturom będzie poddawana płytka, pomoże ocenić konieczność posiadania określonych cech.
Na jakie cechy materiałów należy zwracać uwagę podczas ich doboru?
Główne cechy, na które należy zwrócić uwagę to:
CTE
A Miara podatności na rozszerzanie po podgrzaniu. Cecha ta ma krytyczne znaczenie w osi Z − typowo powyżej Tg rozszerzalność jest większa. Niedostateczny współczynnik CTE grozi usterkami podczas montażu, ponieważ materiał będzie rozszerzał się gwałtownie powyżej temperatury Tg.
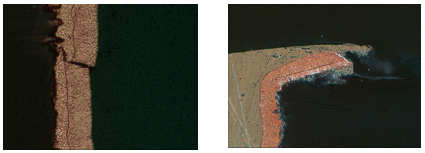
Materiały mogą mieć tę samą temperaturę Tg, ale odmienne współczynniki CTE − lepszy jest niższy współczynnik CTE. Podobnie niektóre materiały mogą mieć wyższe wartości Tg a jednocześnie wyższe (gorsze) wartości CTE powyżej Tg.
Tg / TEMPERATURA ZESZKLENIA
Tg to wartość temperatury, przy której materiał zmienia się z względnie sztywnego, podobnego do szkła, w materiał bardziej elastyczny i giętki. Należy wziąć pod uwagę, że po przekroczeniu temperatury zeszklenia właściwości materiału ulegną zmianie.
Td / TEMPERATURA ROZKŁADU
Jest to miara degradacji materiału. Za pomocą metody analitycznej wyznacza się punkt, w którym ubywa 5% masy materiału − jest to punkt zagrożenia niezawodności oraz ryzyka wystąpienia rozwarstwienia. Płytki PCB o wyższej niezawodności będą wymagały Td ≥ 340℃
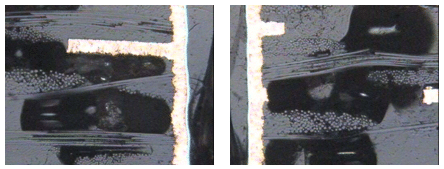
T260 / T288 / CZAS ROZWARSTWIENIA
Jest to metoda wyznaczenia czasu, po upływie którego grubość płytki PCB ulega nieodwracalnej zmianie w ustalonej wcześniej temperaturze (w tym przypadku 260 lub 288 stopni), czyli momentu, w którym materiał rozszerzy się w takim stopniu, że ulega rozwarstwieniu.
Czy muszę używać laminatu FR4 o wysokiej temperaturze rozpadu (Td) do lutowania bezołowiowego?
Pożądana jest wyższa wartość Td, szczególnie jeśli płytka cechuje się wysokim stopniem skomplikowania i wymaga dużej liczby cykli topnienia lutowia, co jednak może prowadzić do wyższych kosztów. Znajomość procesu montażu pozwoli dokonać właściwego wyboru.
Jaka jest różnica pomiędzy „dicyjanodiamidem” i „bez dicyjanodiamidu” jako utwardzaczem żywicy epoksydowej w laminacie FR4?
Dicyjanodiamid jest zdecydowanie najczęściej stosowanym utwardzaczem dla tej żywicy; normalnie wartość Td wynosi dla niego 300–310°C. Natomiast utwardzacze „bez dicyjanodiamidu”, np. utwardzona żywica fenolowa, wykazują wartość Td około 330–350°C, więc wytrzymują wyższe temperatury.
Co oznacza angielski skrót „CAF”?
CAF (Conductive Anodic Filament) dotyczy zjawiska przewodzenia wzdłuż włókien laminatu, czyli reakcji elektrochemicznej pomiędzy miedzianą anodą, a katodą, co może spowodować powstanie wewnętrznego zwarcia w materiale.
Jaka powierzchnia płyty PCB nadaje się najlepiej do lutowania bezołowiowego?
Nie istnieje powierzchnia „najlepsza”; każda powłoka ma swoje zalety i wady. Wybór zależy od szeregu czynników. Prosimy o skontaktowanie się z naszym personelem technicznym lub przejrzenie informacji na temat wykończeń powierzchni na naszej stronie internetowej.
Jakie zasady obowiązują w zakresie środków uniepalniajacych, czyż nie wprowadzono ogólnokrajowego zakazu używania TBBP-A, środka, który dominuje w przemyśle elektronicznym?
Nie, dochodzenie wykazało, że z przyczyn praktycznych używania tego środka nie można zabronić.
Jaka jest różnica pomiędzy dodaniem środka zmniejszającego palność w postaci reaktywnej lub addytywnej?
Reaktywny środek zmniejszający palność łączy się z żywicą epoksydową I nie rozpuszcza lub oddziela się od produktu jako element składników odpadów.
Ile cykli lutu lutowania rozpływowego może wytrzymać materiał FR4?
Ciężko jest udzielić precyzyjnej odpowiedzi, jednak przeprowadziliśmy próby na materiałach do 22 cykli topnienia, z których cztery o temperaturze szczytowej 270°C. Odkształcenia po 22 cyklach topnienia są znaczne i materiał może ulec degradacji, jednak wszystkie połączenia pozostają funkcjonalne.
Zalecamy, aby wybierać materiał wyższej klasy w przypadku więcej niż 6 warstw i grubości przekraczającej 1,6 mm.
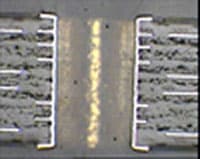
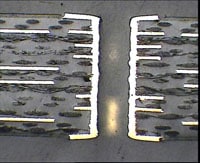
RoHS
Czy dyrektywy RoHS lub WEEE wymagają oznakowania płyty PCB?
Nie, ale z praktycznych powodów PCB, które mają bezołowiowe HASL powinny być wyraźnie oznaczone, stwierdzając ich zgodność z RoHS ze względu na ryzyko pomylenia z ołowiowym HASL.
Czy płyty zgodne z RoHS również nie zawierają halogenów?
Niekoniecznie. Dyrektywa RoHS wyklucza używanie dwóch zawierających bromki typów środków uniepalniających: PBB (polibromowane bifenyle) i PBDE (polibromowane etery difenylowe). W płytach PCB zwykle stosuje się bromowany środek uniepalniający o nazwie TBBP-A (tetrabromobisfenol A).