– Tendances, défis et avis d’expert pour une conception et une production optimales
Les circuits imprimés (PCB) sont le composant clé des appareils médicaux modernes. Un circuit imprimé est une interconnexion électrique qui permet à l’alimentation et aux données d’être facilement transférés à l’intérieur d’un appareil. Les circuits imprimés médicaux s’appuient sur ce concept en ajoutant une interconnexion humaine, ce qui signifie que le facteur de forme physique doit répondre à des exigences strictes telles que la petite taille, le faible poids, la haute fiabilité et la sécurité, tout en offrant des fonctionnalités qui répondent aux besoins de la base d’utilisateurs prévue. Par conséquent, la demande de circuits imprimés médicaux fiables et de haute qualité a augmenté de manière exponentielle au fil du temps.
Toute personne qui conçoit un circuit imprimé destiné au domaine médical doit connaître certains éléments essentiels. Dans ce guide, nous verrons quelles sont les dernières tendances sur ce marché en pleine évolution et comment nous pouvons vous aider à trouver la solution optimale pour répondre à vos besoins spécifiques.
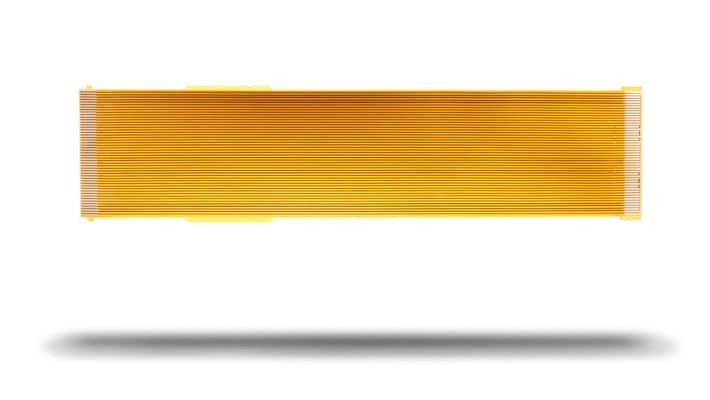
Afin de garantir une communication fiable entre ces systèmes, l’industrie médicale a adopté l’Internet des Objets (IoT). L’utilisation de plusieurs signaux de données et une efficacité accrue est l’un des avantages de cette technologie. De plus, elle facilite le lien entre les différentes pièces d’un appareil ou d’un système, ce qui permet d’en maximiser le potentiel.
L’électronique médicale est en constante évolution, ce qui crée une demande dynamique pour les circuits imprimés nus. Les appareils devenant plus petits, plus denses et plus intelligents, les fabricants de PCB s’efforcent de créer des cartes plus petites et plus complexes, dotées de fonctions sophistiquées tout en offrant des performances fiables. Cette tendance devrait se poursuivre dans les années à venir, car la technologie médicale continue de se développer.
Défis pour l’industrie médicale et les circuits imprimés
L’industrie médicale est très réglementée et exige le respect de normes strictes pour garantir que les dispositifs médicaux fabriqués sont sûrs et efficaces. La sécurité des patients est une préoccupation majeure d’où une demande importante en matière de sécurité et de fiabilité concernant le circuit imprimé.
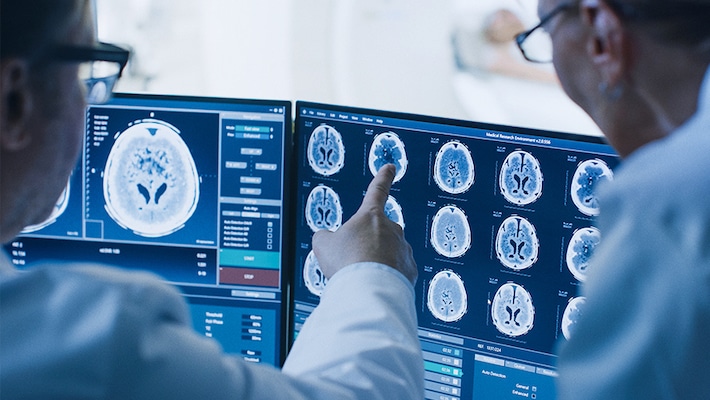
Pour répondre à ces réglementations et à ces exigences, les fabricants doivent tenir compte de facteurs tels que les méthodes de contrôle, l’approbation des installations et les coûts de production élevés.
- Méthodes de contrôle: Le process de fabrication des circuits imprimés doit être contrôlé pour des raisons de fiabilité et de sécurité. Il s’agit notamment de vérifier la température, l’humidité et la pression de l’environnement de fabrication, de s’assurer que les paramètres appropriés sont respectés à chaque étape du process de production et de soumettre les assemblages finaux à divers tests. Les fabricants doivent documenter leurs process de manière exhaustive afin de passer les contrôles réglementaires.
- Approbation de l’installation: Les fabricants de dispositifs médicaux doivent également obtenir l’approbation des organismes de réglementation avant de fabriquer des produits destinés à la vente. Ils doivent notamment s’assurer que tous les équipements sont correctement entretenus et calibrés, qu’ils disposent d’un plan de contrôle qualité adéquat et qu’ils fournissent des preuves de conformité aux normes applicables. Dans le cadre de ce processusd’approbation, les installations doivent également faire l’objet d’inspections périodiques pour s’assurer qu’elles sont toujours conformes.
- Contraintes de production: Il existe des contraintes inhérentes aux circuits imprimés médicaux en raison de leur taille et de leur complexité. Certains matériaux utilisés, comme le cuivre ou l’argent, peuvent ne pas convenir à certaines applications en raison de leur réaction avec d’autres matériaux. En outre, les fabricants doivent également tenir compte de l’impact des interférences électromagnétiques (EMI) sur les performances de leurs produits.
- Coûts de production élevés: La production de circuits imprimés médicaux est une entreprise coûteuse car les fabricants doivent acheter des équipements et du matériel haut de gamme, suivre des processus spécifiques et se conformer à toute une série de réglementations.
Facteurs clés à prendre en compte lors de la conception et de la production d’un PCB destiné au médical
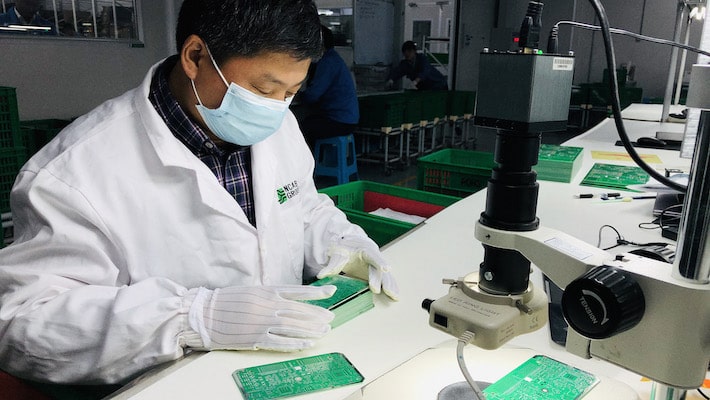
Lors de la conception de PCB destinés à l’industrie médicale, plusieurs facteurs clés doivent être pris en compte afin de garantir leur sécurité :
- L’intégrité du signal est importante pour les circuits imprimés médicaux car les signaux électriques doivent rester à l’abri du bruit et des interférences lorsqu’ils circulent sur les pistes. Pour cela, il est essentiel de veiller à ce que la disposition du circuit imprimé et la sélection du routage respectent les meilleures pratiques.
- La conformité EMI/EMC doit être prise en compte car les interférences électriques peuvent affecter non seulement le fonctionnement de l’appareil, mais aussi celui d’autres appareils ou systèmes situés à proximité.
- La consommation d’énergie est également un facteur clé à prendre en compte lors de la conception d’un circuit imprimé, car certains dispositifs médicaux peuvent nécessiter des niveaux d’énergie très faibles pour être portables ou fonctionner sur batterie. Il est essentiel de veiller à ce que l’agencement de la carte n’entrave pas les gains d’efficacité énergétique et que les matériaux choisis réduisent les besoins en énergie sans compromettre les performances.
- La conception pour la fabrication (DfM) doit être prise en compte car les PCB sont soumis à des normes strictes de précision et de qualité telles que l’IPC 6012 classe 3.
- Une fiabilité élevée des circuits imprimés est primordiale car la défaillance d’un dispositif médical peut mettre des vies en danger. Il convient de sélectionner des pièces capables de résister à l’environnement prévu, y compris aux fluctuations de température et aux niveaux d’humidité, afin de minimiser l’usure prématurée ou la défaillance.
- Le contrôle qualité est essentiel afin de s’assurer que les PCB répondent aux normes et spécifications requises par l’industrie médicale. Le processus de fabrication doit être étroitement surveillé et contrôlé afin de garantir que les PCB sont fabriqués dans le respect des tolérances, des dimensions et des propriétés électriques requises.
- Traçabilité – les fabricants de dispositifs médicaux doivent être en mesure de tracer chaque composant, y compris le circuit imprimé, depuis le fournisseur jusqu’au produit fini. Pour ce faire, ils doivent respecter scrupuleusement les protocoles de traçabilité, le suivi des lots et l’attribution des numéros de série. Les fabricants de dispositifs médicaux doivent également réaliser une documentation complète comprenant les registres du processus de fabrication, les résultats des tests et les rapports de validation.
- Sélection des matériaux – les matériaux utilisés dans les PCB médicaux doivent être soigneusement sélectionnés pour s’assurer qu’ils sont compatibles avec l’utilisation prévue de l’appareil, la méthode de stérilisation et les exigences réglementaires. Les matières utilisées doivent également être exemptes de contaminants et d’impuretés susceptibles d’avoir un impact sur la sécurité et l’efficacité de l’appareil.
- Contrôles environnementaux – l’environnement de fabrication doit être contrôlé afin de garantir que les PCB sont fabriqués dans un endroit propre et contrôlé, exempt de contaminants et de particules susceptibles d’avoir un impact sur leur performance ou leur sécurité.
- Essais et validation : Les circuits imprimés doivent être testés et validés pour s’assurer qu’ils répondent aux normes et spécifications requises. Il s’agit notamment de tester les performances électriques, les performances environnementales et la compatibilité avec les autres composants de l’appareil.
Normes auxquelles doivent répondre les PCB médicaux
Les PCB sont les composants essentiels de nombreux dispositifs médicaux et doivent répondre à des normes strictes afin de garantir la sûreté, la qualité, la fiabilité et la sécurité de ces produits. Ces normes régissent la manière dont un fabricant conçoit et construit l’assemblage du circuit imprimé d’un dispositif médical.
Tous les circuits imprimés doivent également répondre aux normes de certification UL pour pouvoir être intégrés dans des dispositifs médicaux. Ces normes impliquent le test de divers paramètres électriques et mécaniques, tels que l’élévation de température, la rigidité diélectrique, la résistance au feu, etc…
Le fabricant de circuits imprimés peut également être certifié ISO pour la gestion de la qualité. La norme ISO 13485 est spécifique au secteur médical, associée à la certification ISO 9001, qui s’adresse spécifiquement aux fabricants de dispositifs médicaux.
Principales considérations de votre fournisseur de circuits imprimés
Pour la fabrication d’un produit médical, votre fournisseur doit comprendre l’importance de fournir des PCB d’une qualité et d’une fiabilité supérieures. Des ingénieurs et des techniciens compétents doivent intégrer une méthodologie complète comprenant la conception, la fabrication, les essais et la documentation.
Tout d’abord, votre fournisseur doit entreprendre une analyse complète des paramètres de votre circuit imprimé. Il doit s’assurer que tous les composants sont compatibles avec les matières choisies et que la fiabilité des signaux est garantie pour les conceptions à grande vitesse. Il doit également tenir compte des conditions environnementales telles que les températures extrêmes ou l’humidité lors de la sélection du matériau approprié.
Une fois la conception approuvée, il est temps de lancer le prototypage et les essais. Pour garantir la qualité du produit, les prototypes sont souvent fabriqués dans les mêmes conditions que la série.
Après le prototypage, un lot de pré–série est fabriqué, souvent pour la certification du produit final. Ce lot ne permet généralement pas de modifications par rapport au lot initial et doit être fabriqué de la même manière et dans les mêmes conditions que la production finale.
Enfin, après la pré-série, la production série peut commencer. Il est conseillé que votre fournisseur effectue des contrôles qualité pendant et après la production, afin de garantir un produit fini de haute qualité. Un rapport sur le premier article détaillant la qualité de la construction doit être inclus dans chaque lot comme preuve de la qualité.
Chez NCAB, la qualité et la sécurité sont notre priorité. Notre approche globale garantit que votre produit est conçu, fabriqué et testé selon les normes les plus strictes, afin d’assurer la conformité et la fiabilité de votre dispositif médical.
NCAB produit des circuits imprimés pour différentes applications médicales
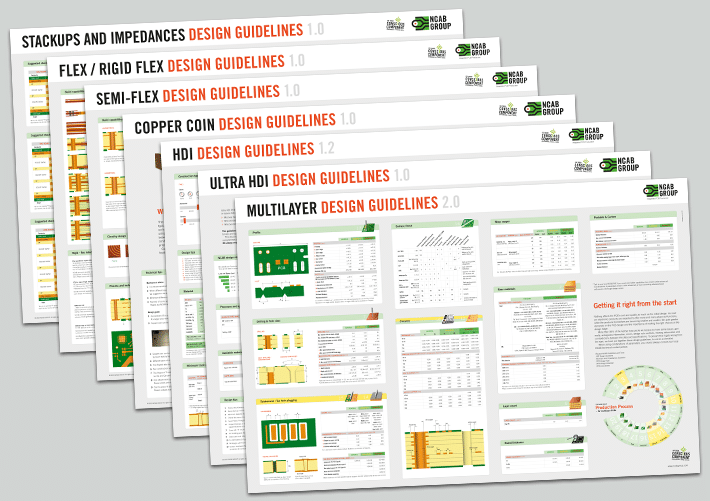
PCB design guidelines
Get it right from the start with our PCB design guidelines. To prevent getting it wrong from the start, we have put together our design guidelines, to use as a checklist.