In today’s fast-paced and ever-changing world, the escalating use of electronic products has led to a critical environmental issue – electronic waste. Among the key contributors to this waste stream are Printed Circuit Boards (PCBs), fundamental components in nearly all electronic devices. As a result, the concept of PCB recyclability has gained significant traction, driven by technological advancements and a growing environmental consciousness.
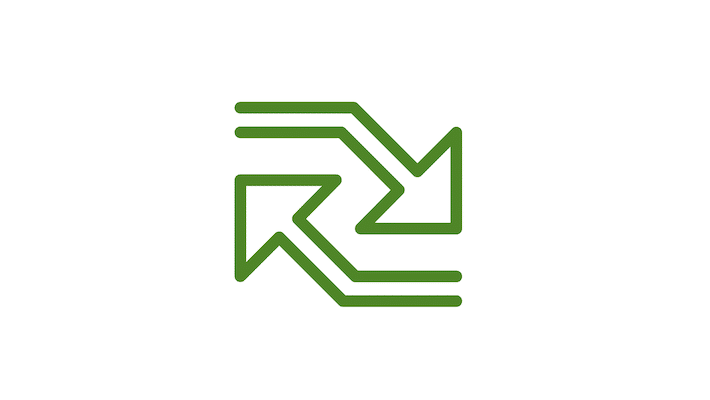
With NCAB’s strong commitment to sustainability, in this blog post I will discuss the concept of circularity in PCB production and its significance in creating more sustainable printed circuit boards, the challenges of recycling PCBs, and the potential of reusing organic PCB residues for new products. Additionally, this blog will highlight a promising project in China that will bring us closer to achieving fully recyclable PCBs.
Understanding Circularity and the Challenge of PCB Recyclability
To begin with, what do we mean by circularity in this context? Circularity refers to the practice of reducing waste at the end of a product’s life. The idea is when we send an electronic product back for waste treatment, we can reuse the scrapped product as raw materials in the production of a similar product. However, achieving true circularity can only be done if we have a homogeneous product, meaning that the product needs to be made from the same group of materials. This, however, is not the case with electronic products, as they consist of a mix of materials.
The assembled PCB is what we can call a homogeneous integration of multiple products; we have the bare PCB, and we have components soldered on the PCBs such as semiconductor packages, resistors, and capacitors. And in order for us to recycle PCBs effectively, we must first remove the electronic components so that we are left with the bare PCB, as that is the product that we now want to recycle. To understand how that can be done, we have to look into what a PCB is made of.
Did you know?
Recyclable PCBs and circularity differ in their scope of recycling. Circularity, in the context of PCBs, refers to the practice of reducing waste and keeping materials at the end of a product’s life. Its aim is to create a closed-loop system where materials are continuously recycled and reintegrated into new PCBs or other products. Whilst recyclable PCBs involves extracting and reusing valuable materials from the board and its components. The focus here is on the end-of-life phase, where the PCB is sent for waste treatment, and various materials like metals and plastics are separated and recycled independently.
The Composition and Bonding of PCBs: Implications for Recycling
As we delve into recycling PCBs, let’s first understand what they are made of. On the surface we have soldermask and marking ink. Below that we have copper conductors in several layers inside the PCB. Additionally, all PCBs have surface finishes, such as tin or gold contacts or connectors. Within the PCB, we also have different versions of epoxy, or a plastic material that encapsulates fibre glass cloths. All of these components are bonded together, which, quite frankly, makes separation a challenging task.
Currently, the only way to break down the PCB is by grinding the complete circuit board, resulting in small particles of metal, fibreglass, resin (epoxy) that are all blended together. Today, we are able to separate the different metals, such as copper and gold, resulting in a residue consisting of resin and fibreglass particles. While the metals can be easily reused, even for new PCBs, the organic residue provides to be useless for PCB production.
Globally, much of this organic residue ends up being wasted in landfills. However, in some countries, this residue becomes a source for generating heat and electricity. The ideal approach would be to reuse these residues for new products, and there are several projects investigating how we can reuse the organic residues from PCBs into new products. The ultimate goal would be to separate glass fibres from the resin to be used as raw materials for new PCB base materials.
Promising Advances: Separating Fiberglass from Epoxy Resin
Currently, one of the major laminate factories in China has developed an FR-4 type fibreglass base material suitable for separating fibreglass from epoxy resin, but so far this has been achieved only in a lab environment. A larger recycling plant is under development. NCAB is closely following how this develops to be industrialized and finally available for commercial recycling of PCBs.
So, when we talk about a recyclable PCB, we should refer to the separation of fibreglass from resin in the organic residue, and the extent to which we can reuse it to produce new PCBs.
Testing the New Material: Assessing Reliability and Characteristics
Let’s take a look into this new material developed in China. How reliable is that material compared to FR-4, the most common PCB base material? What are the characteristics of this material?
Reliability is something we must test to collect data. While the published characteristics must also be qualified, it is worth noting that this material has very similar characteristics to a high-end low halogen (FR-4.1) material.
Due to our relationships with one of the largest laminate manufacturers, in spring, NCAB ordered samples of the FR-4 type base material – even though this is only in the R&D stage. Following receipt, my colleague, Kenneth Jonsson, Technical Manager at our Stockholm lab, conducted a series of common tests, took cross sections, and performed some standard tests. The result was surprisingly good! The tests we did were:
- The samples were thermally stressed 6 times in a laboratory oven set to 260°C for 2,5 minutes each time (J-STD-003D Table 4-6),
- The samples were then dipped 2 times for 10 sec in molten solder according to IPC-TM-650 2.6.8E Test Condition A 288 °C ± 5 °C.
- A 10*20mm microsection was taken and inspected for defects.
In the report, Kenneth writes: “No deviation against IPC-A-600 could be seen, and no evidence of material degradation could be seen. The material’s CTE properties seem good since there is no evidence of pad lifting. The material seems to be able to handle the heat well since there is no evidence of resin recession.”
One point we did note is that we observed clear demarcation lines between each prepreg in a way not seen before on rigid CCL material. While these demarcation lines seem to be rather unchanged after thermal stress, which is good, they can still be weak points when applying mechanical stress.
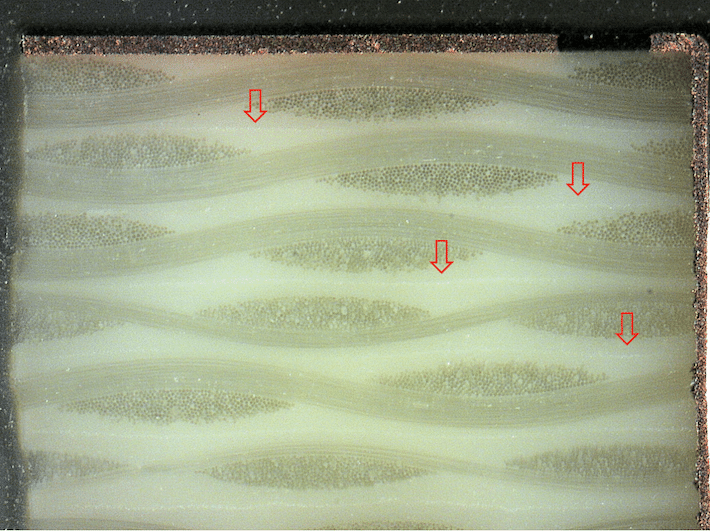
Additionally, we noticed some hole roughness where the drill bit has ripped out part of the fibre bundles, indicating drilling parameters need to be fine-tuned.
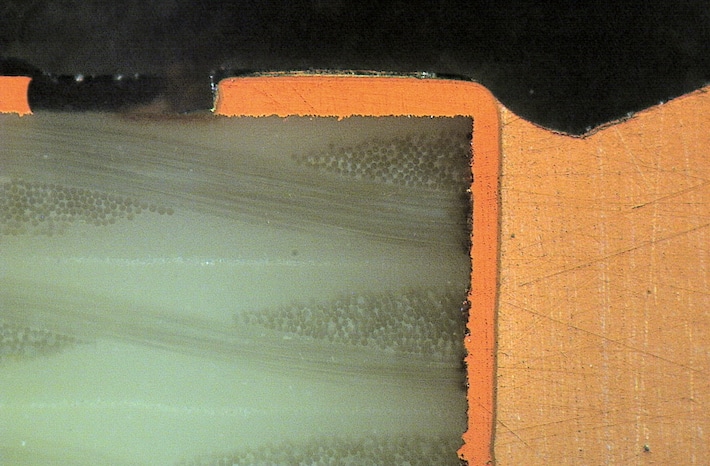
Moving Forward: Plans and Uncertainties for Recyclable PCBs
So, what’s next? We have done tests, but we haven’t yet sent any boards for assembly, which is our next step. Our plan is to assess the material’s performance and reliability in real-life scenarios, and to do long-term reliability tests. In conclusion, to confirm reliability, we need data.
Your question now might be; when can we order PCBs on this material, and when can we test the circularity? Unfortunately, we don’t have a definite answer yet. As per our plans, we will order more boards, test them, and send them to customers that are willing to do field tests. For the recycling, we will follow up the laminate factory very closely and share with our customer as we go.
Additionally, another factor that can speed up the concept of PCB recyclability is the interest among standardization organisations like IPC and UL, and papers presented in global conferences.
Overall, as the concept of PCB recyclability gains momentum, we need to explore the challenges of achieving true circularity due to the heterogeneous nature of electronic products. Testing and development of a new material in China show promising results for separating fiberglass from epoxy resin, contributing to the goal of recyclable PCBs. While uncertainties remain about the timeline for fully recyclable PCBs, continued research and collaboration hold the potential to accelerate progress in the recycling and sustainable use of PCBs.
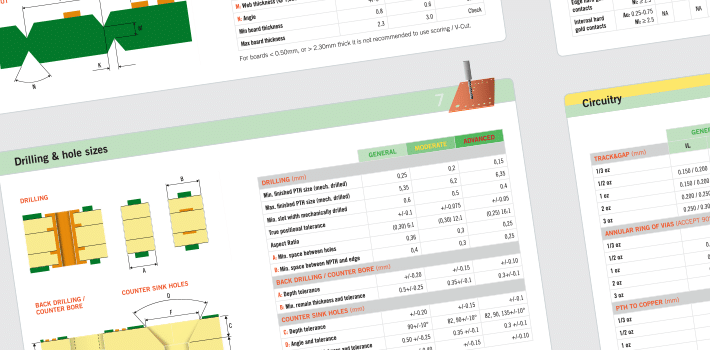
PCB design tools
For more advice about PCB design or applications of PCBs, we
have different PCB tools that can be downloaded for free.