Flexible printed circuit boards allow large circuits to be placed in relatively small spaces. They also offer designers and engineers more latitude to avoid designing an entire product around the spatial requirements of a rigid circuit board. When choosing PCBs that can bend into place, electrical engineers have a choice between using flex and semi-flex PCBs. Following is a basic overview of how these two types of PCBs differ and their uses in modern electrical devices.
How are semi-flex PCBs different from flex PCBs?
The key technological difference between a flex PCB and a semi-flex PCB is that a flex PCB is built on a flexible polymer film base. Circuit patterns are built into the film with conductive material and a thin coating layer is added to protect the circuit. The film makes the entire board flexible, allowing it to be bent and manipulated easily without damage.
A semi-flex PCB, by contrast, can only be bent in certain areas that have been made to flex. As a result, the PCB will only bend in predetermined ways and at defined points. The graphics below illustrate the concept of a semi-flex PCB.
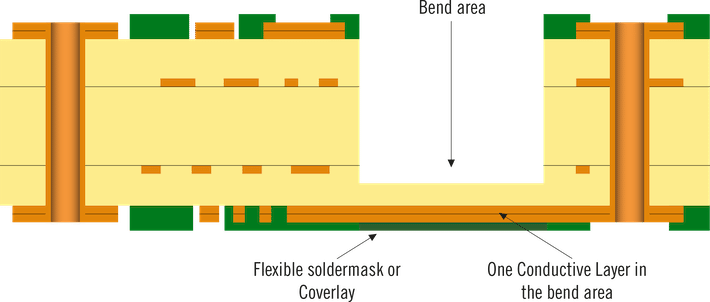

With the exception of the flex areas, a semi-flex PCB is stiff and more akin to a traditional rigid PCB. This is because semi-flex PCBs are manufactured using the manufacturing process ‘controlled depth routing’ or ‘milling’ down the FR4 material on the PCB until it is extremely thin and flexible. The flexible section is then treated to prevent cracking, allowing it to bend more or less freely. Here we can also see a microsection image of a semi-flex PCB.
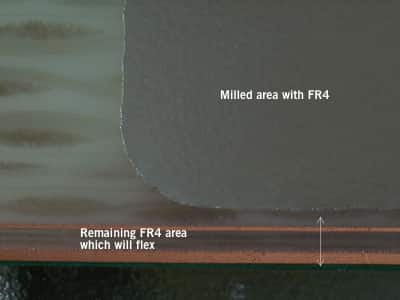
Semi-flex PCBs can also be manufactured by using thin core laminates. Laminates as thin as .005 mil. are utilized for static flex applications. RA (rolled annealed) copper foils is recommended to prevent cracking and allow for a more robust flex.
One of the most crucial differences between semi-flex and flex PCBs from a design perspective is the fact that a semi-flex PCB can only bend a limited number of times. While ordinary flex PCBs can be bent many times over without damage, a semi-flex PCB will crack or break with repeated flexing. As a result, semi-flex PCBs are best used in flex-to-install applications. Most semi-flex boards can, however, bend more than once. This allows for both installation and future maintenance with minimal risk of damage, provided the PCB isn’t stressed with frequent bending.
Advantages of semi-flex PCBs
Semi-flex PCBs offer a variety of advantages for electrical engineers and designers. First and foremost, semi-flex PCBs can save space in much the same way as flex boards. The ability to bend during installation allows a comparatively large board to be installed in a small, confined space. When designed and manufactured correctly, semi-flex PCBs are also quite reliable.
Semi-flex PCBs also offer considerable cost savings when compared to flex circuit boards. This is because the flexible portion of the board is achieved by reducing the thickness of the FR4 material via controlled depth milling. Flex PCBs, by comparison, use a much more expensive polyamide substrate to achieve their greater flexibility. While there are still situations in which the enhanced bending capabilities of a flex PCB are required, it’s best to use semi-flex PCBs where possible to control costs.
General semi-flex PCB design rules
As with all PCBs, the best practices involved in designing robust, reliable semi-flex PCBs are extensive. There are, however, some general rules electrical engineers should keep in mind when designing a semi-flex PCB.
Perhaps the most important of these guidelines is that while the flexible portion of the board may run along either the X or Y plane, it should always run in one direction. While it is possible to construct boards with both X and Y directional flex areas, the cost is higher due to the need for additional manufacturing steps.
The positioning of component holes is also important when designing a semi-flex PCB. A good rule of thumb is to leave at least one millimeter of space in between any component holes on the PCB and the flexible portion of the board.
Finally, designers should plan their boards in such a way that the flexible area can be produced with a single run of a milling router to thin out the FR4 material. Making multiple passes may create weak points that will become problematic when bending the circuit board for installation or for later maintenance.
When to use semi-flex PCBs
Semi-flex PCBs are well-suited to situations in which a PCB must be bent only for installation and projected future maintenance. Their flexible nature also makes semi-flex PCBs a good design choice for applications in which space is a major consideration. If the bent area of the circuit board will undergo dynamic stress, however, it’s better to select a flex PCB.
Semi-flex PCBs can be found in many common applications. Automobiles, industrial equipment and even safety electronics make extensive use of this circuit board category. A variety of factors affect the choice between rigid, flex and semi-flex PCBs. These factors include available space, stress requirements, thermal property requirements and budget. Picking the correct type of PCB is critical to successfully engineering and manufacturing electronics products. To learn more about the capabilities of these PCB varieties, you can download our semi-flex or flex PCB design guidelines, or Contact Us at one of our local offices to learn more.
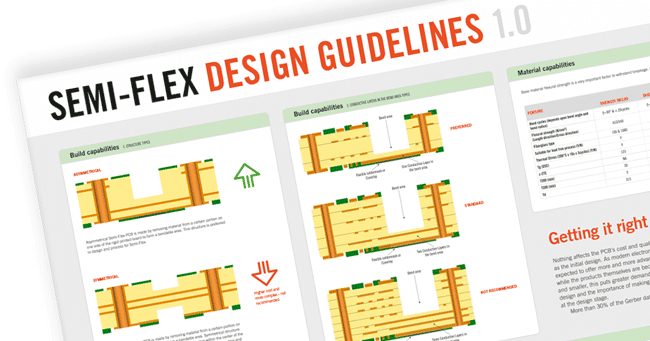
Download our design guidelines for Semi-Flex PCBs
To prevent getting it wrong from the start, we have put together our design guidelines, to use as a checklist.