PCB HDI (Circuit imprimé HDI)
Associée à notre organisation technique mondiale, cette approche nous permet d’acquérir une connaissance approfondie des exigences et des méthodes de fabrication nécessaires à la réussite des produits HDI. Découvrez nos spécifications techniques pour les circuits imprimés HDI, comment l’IPC définit une carte HDI et obtenez des conseils de conception.
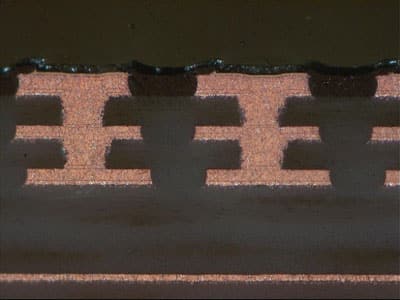
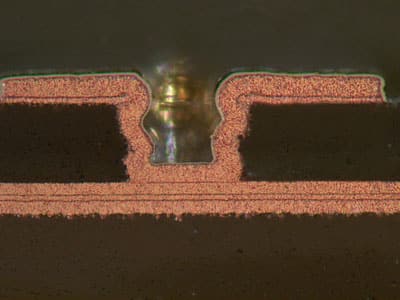
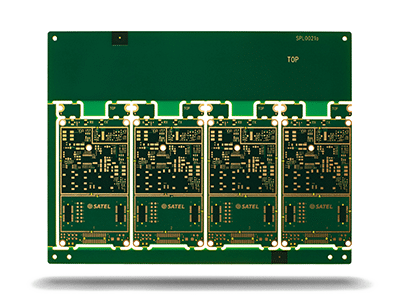
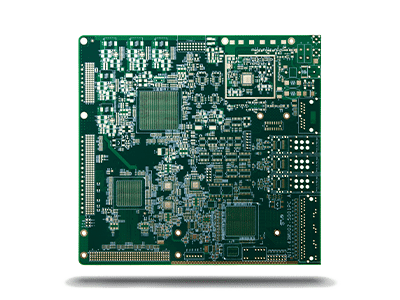
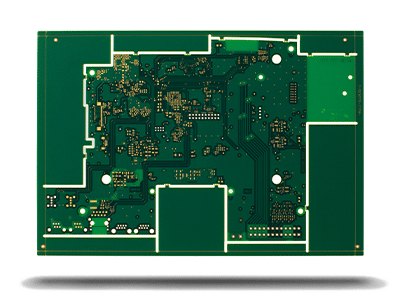
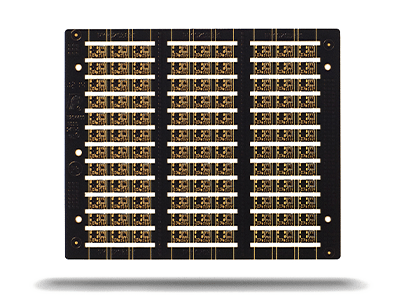
Qu’est-ce qui définit une carte HDI ?
La norme IPC-2226 définit les HDI comme des circuits imprimés présentant une densité de câblage par unité de surface supérieure à celle des PCB classiques. Ils présentent des pistes et des isolements plus fins (≤ 100 µm / 0,10 mm), des vias plus petits (< 150 µm) et des pastilles « capture » (< 400 µm / 0,40 mm), ainsi qu’une densité de pad supérieure (> 20 plots/cm²) à celle des circuits imprimés classiques. Il existe différents types de HDI : type I, type II et type III.
Les différents types de fonctionnalités HDI
Le graphique ci-dessous montre les principales structures – Type I, Type II et Type III telles que définies dans l’IPC-2226.
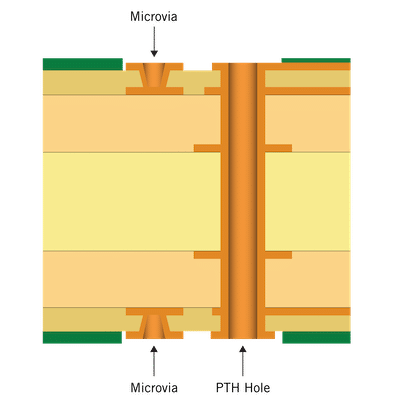
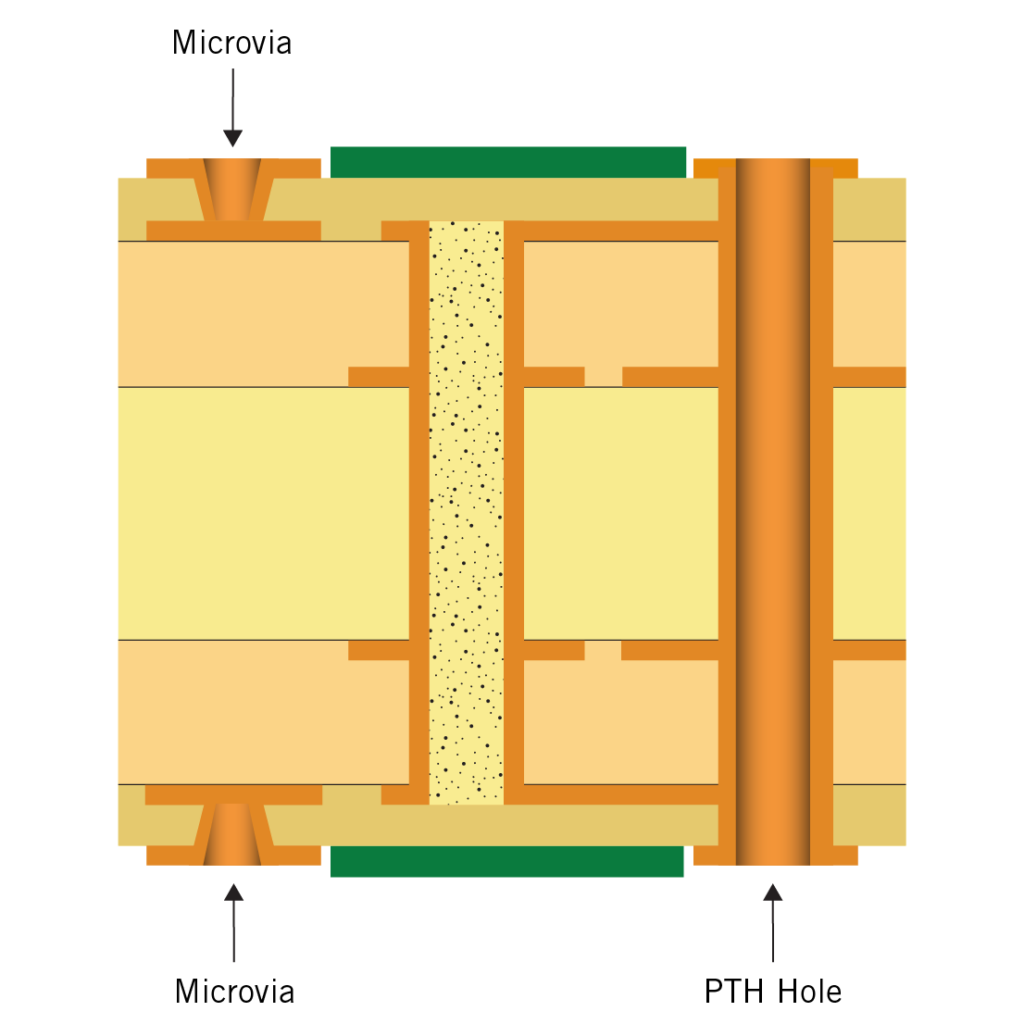
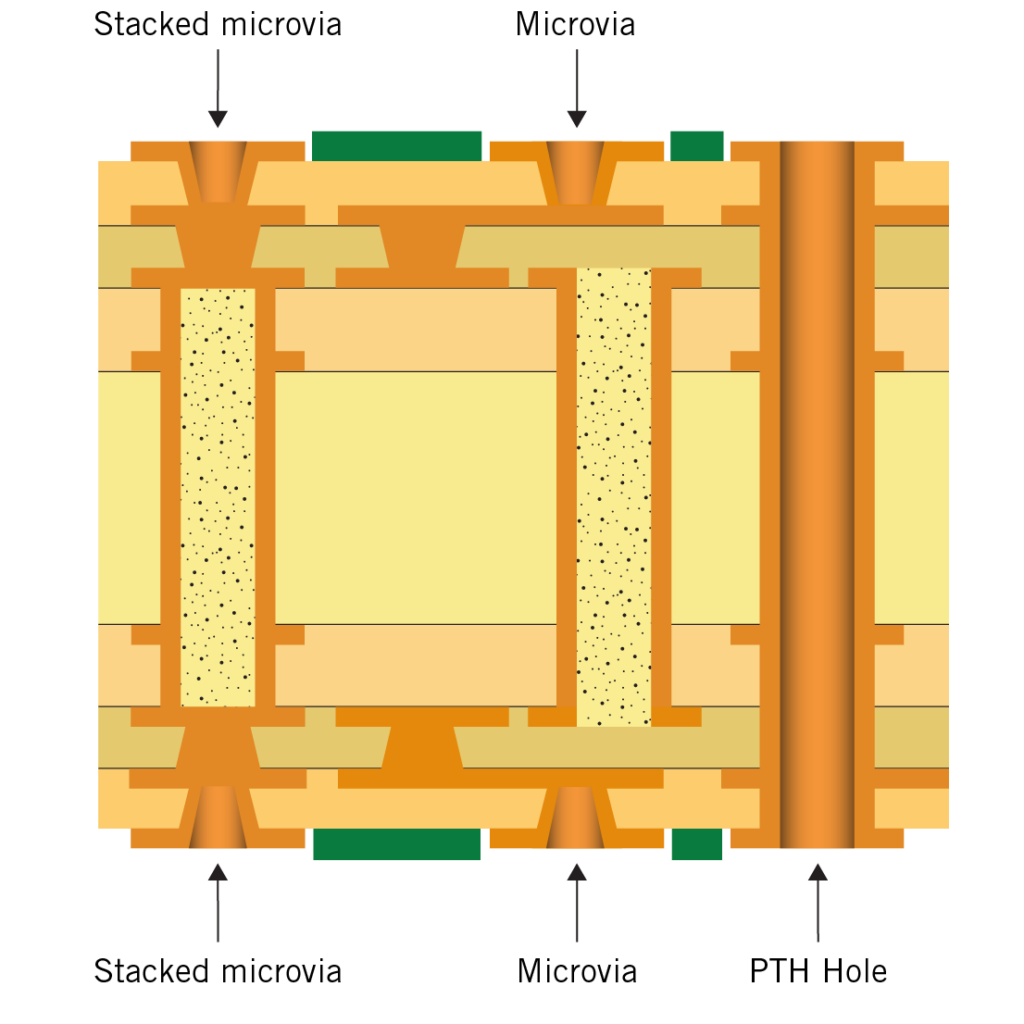
Terminologie de construction pour définir le degré de construction HDI :
- 1+n+1 = une seule couche de microvia (comme dans les exemples de type I et II ci-dessus)
- 2+n+2 = 2 couches de microvia (comme dans l’exemple de type III ci-dessus)
- 3+n+3 = 3 couches de microvia
Nos capacités techniques pour les PCB HDI
Pour plus d’informations sur nos capabilités techniques en matière de circuits imprimés HDI, consultez notre page « Capabilités techniques ». Vous y trouverez également des informations sur les matières, les technologies de circuits imprimés et les types de produits que nous produisons actuellement, ainsi que certaines des tolérances que nous pouvons atteindre.
Ce que vous devez savoir sur la conception et les circuits imprimés HDI
Ci-dessous, vous pouvez en apprendre davantage sur les différents aspects de la conception et des PCB HDI, tels que les erreurs de conception, les règles de conception et les tendances de conception.
Erreurs de conception pour les circuits imprimés HDI
Rien n’affecte autant le coût et la qualité d’un circuit imprimé que sa conception initiale. Vous trouverez ici des informations utiles sur les erreurs de conception courantes, les problèmes de production qu’ils peuvent engendrer et, surtout, la meilleure solution pour les éviter !
ERREURS DE CONCEPTION COURANTES CONCERNANT L’HDI | ERREURS DE PRODUCTION EN FONCTION DE CELA | MEILLEURE SOLUTION |
Diélectrique trop épais pour les vias laser | – Augmentation du temps de perçage laser et baisse de productivité. – Risque élevé de vides lors du processus de placage, notamment au fond des microvias. – Augmentation du prix des PCB en raison de la baisse des rendements. | Utilisez un rapport hauteur/largeur inférieur à 0.8:1. |
Taille de microvia trop petite | – Risque accru que le microvia soit obstrué par un matériau inconnu et ne soit donc pas plaqué de manière satisfaisante. – Risque élevé de d’une mauvaise métallisation du microvia, notamment dans la partie inférieure. – Augmentation du prix des PCB en raison de la baisse des rendements. | – Utiliser des microvias de 100 μm avec un rapport hauteur/largeur inférieur à 0.8:1 pour les microvias destinés au remplissage en cuivre. – Utiliser des microvias de 125 μm avec un rapport hauteur/largeur inférieur à 0.8:1 pour les microvias où le remplissage en cuivre n’est pas requis. |
Géométries trop serrées sous forme de zones de capture et de cible trop petites pour le microvia | – Si la zone cible est trop petite, le risque de la manquer partiellement (dépassement) augmente et les matières adjacentes à la pastille seront brûlés jusqu’à la couche suivante. – Si la zone de capture est trop petite, elle risque d’être brisée, ce qui n’est acceptable pour aucune classe de l’IPC-6016. | Si possible, utilisez une pastille de départ plus large de 200 μm que le microvia. Pour des géométries plus serrées, consultez NCAB |
Exigences trop strictes sur les « dimple » (fossettes) autorisées sur les microvias remplis de cuivre | Augmentation du prix des PCB en raison de rendements réduits. | Placez l’exigence de fossette à un maximum de 25 μm. |
Exigences trop strictes sur l’épaisseur du placage des vias bouchés. (POFV ou VIPPO) | Affecte le déroulement du process. Avec une épaisseur de métallisation raisonnable, tous les vias peuvent être percés en une seule opération, ce qui simplifie grandement le process. Une métallisation trop épaisse réduit les possibilités de produire des couches externes avec des pistes fines ou une faible isolation. | Définissez les exigences conformément à la norme IPC-6012 classe II et exigez uniquement ≥ 6 μm comme épaisseur de métallisation. |
Le bouchage de vias époxy nécessite de nombreuses tailles de vias différentes, cela s’applique aussi bien aux vias enterrés qu’aux vias traversants | Il est difficile de contrôler que des bulles ne se forment pas dans le bouchon final et qu’il n’y aura pas de problème de remplissage complet. | Une seule taille de vias bouchés est préférée. Si plusieurs tailles doivent être bouchées, maintenez-les dans une plage de 0,15 mm. |
Placement de microvias | Si les microvias sont placés directement sur les surfaces CMS, des vides inutiles peuvent apparaître dans les joints de soudure lors du soudage par refusion. Le prix des microvias est plus élevé si ceux-ci sont remplis de cuivre. | Retirez les microvias des surfaces CMS si possible. S’il n’y a pas d’emplacement pour l’option 1, placez les microvias directement dans la pastille et exigez un remplissage en cuivre. |
Distance trop faible entre les trous décalés et les microvias – microvias ou microvias – vias enterrés | Si les microvias décalés sont placés trop près les uns des autres, le trou superposé risque d’empiéter sur le trou sous-jacent, ce qui entraînerait un mauvais placage. Ce problème peut être résolu par une mauvaise métallisation des microvias sous-jacents ou par une métallisation supplémentaire s’il s’agit de vias enterrés, ce qui entraîne une augmentation des coûts et des risques. | Concernant les microvias, conservez une distance de 0,30 mm entre les trous si possible, sinon, descendez à 0,25 mm. Exemple : un microvia de 0,10 mm et un trou enterré de 0,25 mm donnent des entraxes de 0,475 mm et 0,425 mm.
|
N’hésitez pas à nous contacter si vous avez besoin d’aide pour la conception de votre circuit imprimé ; nous serons ravis de vous aider !
Règles de conception pour PCB HDI
Plus de 30 % des données Gerber que nous recevons présentent des problèmes. Elles peuvent contenir des informations ambiguës, des erreurs, des conflits de règles de conception, des informations manquantes et des contradictions entre les données et les spécifications. Pour éviter toute erreur dès le départ, nous avons élaboré nos règles de conception, qui servent de checklist. Voici un extrait de ces règles pour les circuits imprimés HDI.
L’intégralité de ces règles de conception est téléchargeable gratuitement.
Piste et isolement minimum pour la métallisation de la plage
IPC-4761 TYPE VII PLUGGING / VIPPO / POFV
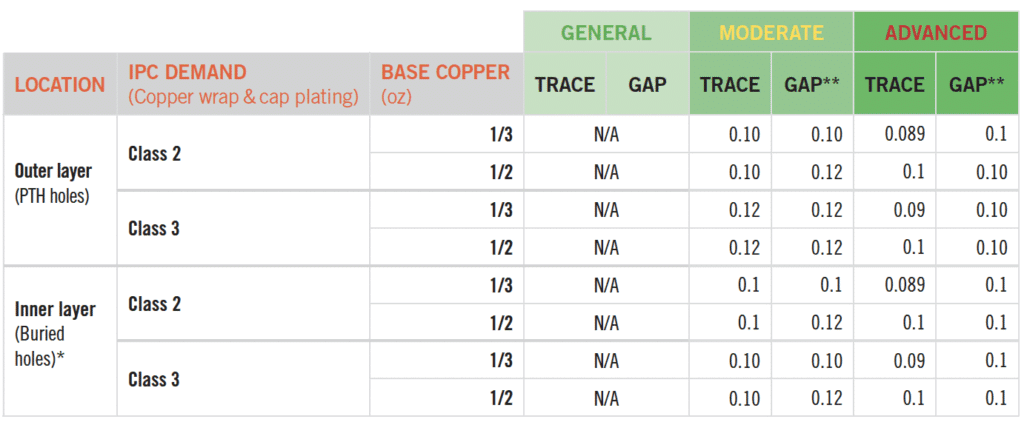
* Valable uniquement pour la phase externe d’un noyau enterré nécessitant un revêtement de protection, généralement lorsqu’un microvia est empilé sur un trou enterré.
** Pour une conception plus stricte, veuillez consulter votre contact technique NCAB local afin d’examiner chaque projet au cas par cas.
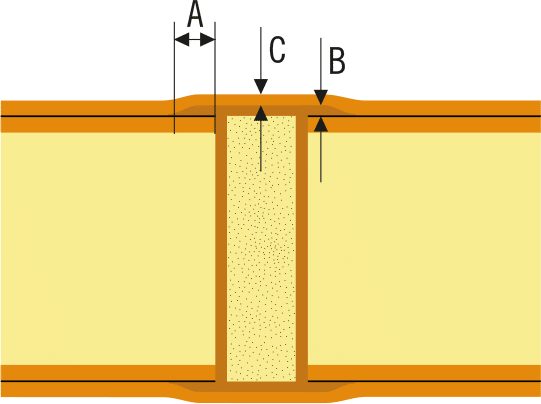
B. Épaisseur minimale de l’enroulement de cuivre : 5 µm pour les classes 2 et 3
C. Métallisation minimale de la plage : 12 µm pour la classe 3, 5 µm pour la classe 2
Nous proposons des règles de conception pour PCB HDI, mais aussi pour les PCB multicouches, Ultra HDI, flexibles/rigides-flexibles, semi-flexibles, en cuivre, les protections de vias, les empilements et les impédances.
Articles de blog sur l’HDI
Dans quelques articles de blog, nous avons exploré les facteurs clés d’une production réussie de circuits imprimés HDI et analysé les tendances de conception de ces circuits. Découvrez un extrait ci-dessous.
Tendances de conception pour les circuits imprimés HDI
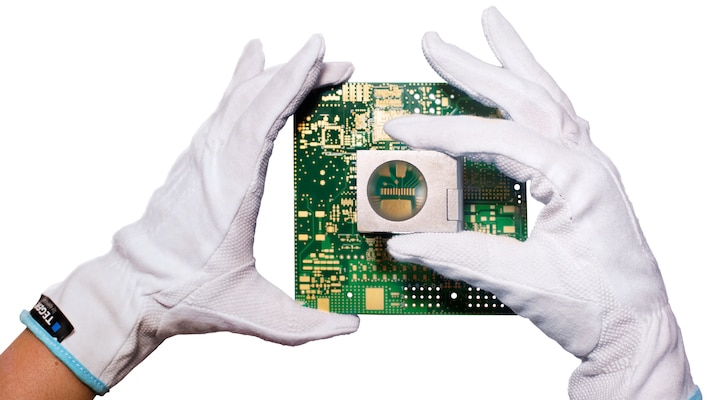
La miniaturisation des composants électroniques accélère l’évolution des circuits imprimés vers une complexité impensable il y a quelques années seulement. Ces PCB exigent davantage de fonctionnalités et de performances, tout en étant plus fins et plus légers. Cela exige un processus de conception et de production très rigoureux. Pour développer ce type de circuits imprimés, nous avons besoin de solutions pour une plus grande densité de connexions et un plus grand nombre de couches.
La conception de plus en plus étroite implique une réduction de l’espace disponible pour le routage, ce qui se traduit par des pistes plus fines et des isolements avec des trous traversants de diamètre toujours plus petit.
Quelques remarques sur les conceptions HDI :
- Les trous borgnes sont des trous laser sur les faces externes.
- Les trous enterrés sont des trous laser pour connecter les couches intermédiaires.
- Nous avons également besoin de préimprégnés et de stratifiés CCL plus fins que les produits multicouches conventionnels.
Lorsque le projet est poussé à l’extrême, il est clair que l’ensemble du processus de conception doit suivre certaines directives, du concepteur au fournisseur de circuits imprimés.
PCB HDI : faites le bon choix de la conception à la production en volume
Deux facteurs clés contribuent au succès de la production de circuits imprimés HDI : d’abord, faire les bons choix dès la conception, puis choisir avec soin l’usine capable de répondre aux exigences techniques spécifiques du projet.
Qu’il s’agisse d’électronique grand public, d’informatique, d’automobile ou de technologie médicale, la tendance générale est à la miniaturisation. Il ne s’agit pas seulement d’une réduction de la taille du produit fini, mais aussi de la taille des composants eux-mêmes, ce qui nécessite des assemblages plus denses et des fonctionnalités plus compactes.
L’apparition de ces produits électroniques de plus en plus sophistiqués a conduit à la généralisation des circuits imprimés plus avancés. Ces spécifications exigent des solutions d’interconnexion haute densité (HDI) avec un plus grand nombre de couches et davantage de connexions en surface et à l’intérieur du circuit imprimé, utilisant des conducteurs de plus petite largeur et des espaces plus étroits entre eux.
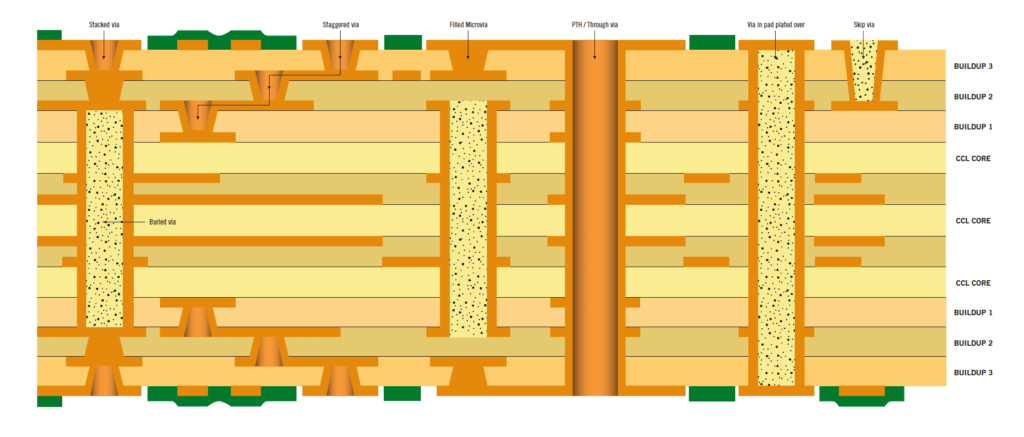
Le nombre accru de couches, associé à la technologie microvia, nécessite également l’utilisation de préimprégnés et de noyaux plus fins que dans les cartes fabriquées de manière conventionnelle, ce qui entraîne également des exigences accrues pour les usines.
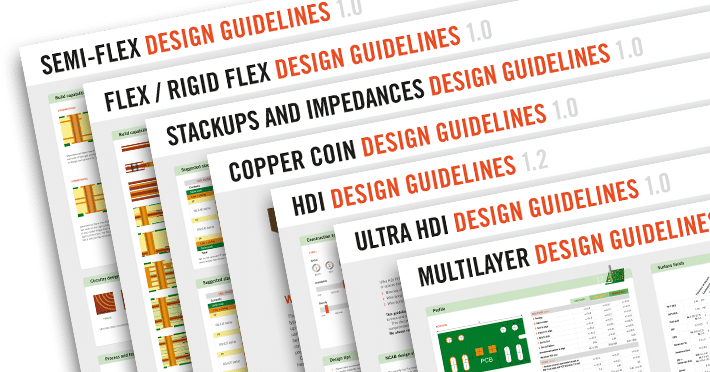
Téléchargez nos règles de conception pour PCB HDI
Pour éviter de partir sur de mauvaises bases, nous avons mis au point des règles de conception afin de vous aider à concevoir votre circuit imprimé.
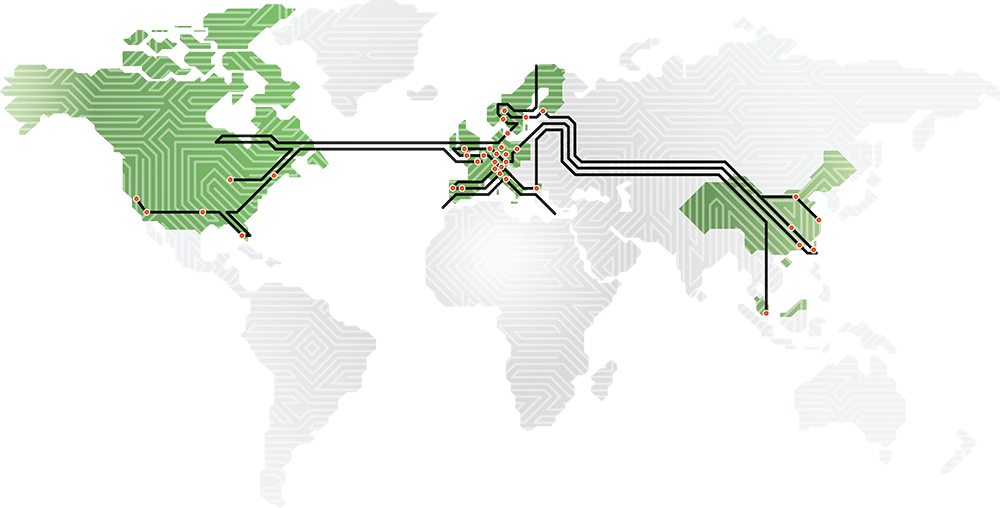
Contactez-nous
Vous pouvez toujours contacter votre bureau local NCAB si vous avez besoin de plus d’informations ou de support. Nous serons heureux de vous aider.