When producing PCBs to the Railway Industry, there are certain requirements that need to be considered, fire and testing are key words to this. Read about the EN 45545-2 standard and discover how one of NCABs customers, Leroy Automation, handles the testing of their printed circuits and how NCAB is assisting.
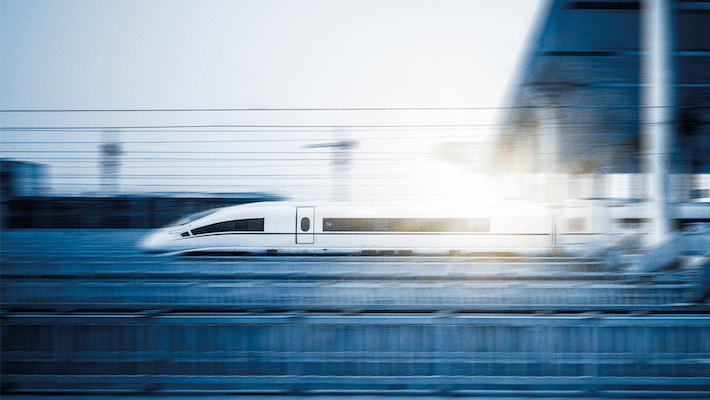
The railway industry has no separate requirements to the manufacturing and acceptability of PCB. However, there is a very important requirement for fire testing – EN-45545-2. This is why, when talking about the railway industry, it is important to refer to the Fire/Smoke regulations aimed at guaranteeing the safety and evacuation of passengers, accompanying staff and potential rescue services.
Important standards for fire and safety
On the European scale, the EN 45545-2 standard (Fire hazard protection in railway vehicles) must be applied. This standard still coexists with country-specific standards.
The reaction to fire tests defined, aim to qualify the products according to their final applications (electrical equipment, seats, floors, walls, ceilings, etc) and must meet a corresponding requirement level (requirement ranging from R1 to R24).
For each requirement there is a series of tests. These tests are mainly aimed at:
● Qualifying the flammability of the materials
● At what scale the materials contribute to a fire
● The smoke released if a fire occurs (toxicity and opacity)
● And the flame propagation.
The EN 45545-2* standard can also be applied, completed with the STM-S-001 or SAM-S-002. In this case, a report is obtained mentioning the level of classification HL1/HL2/HL3** according to the required standard R24/R25, possibly supplemented by a part of R22.
* The essential requirements of EN 45545-2
1/ General
2/ Requirements for the fire behavior of materials and components
3/ Fire resistance requirements for fire barriers;
4/ Fire safety requirements for the design of railway vehicles;
5/ Fire safety requirements for electrical equipment including trolleybuses, guided buses and magnetic levitation vehicles
6/ Fire management and control systems;
7/ Fire safety requirements for flammable liquid and flammable gas installations.
** The risk levels depend on the evacuation of the train
HL1: Tramway (does not pass under any tunnel)
HL2: TGV, TER, RER (80% of the market) Fast and can pass under tunnels
HL3 : Subway, sleeping cars (passing through tunnels)
Tests designation | Tests description |
EN 45545 NF F 16-101 STM-S-001 | Tests as required by R25/Classification I NF EN 60695-2-11 Glow wire test |
Test according to ITC PNL criterion of R22 requirement (STM-S-001) and classification test F NF X 70-100 Gas analysis | |
Complementary test classification F (2/2) NF X 10-702 Determination of the smoke opacity |
The material / soldermask interactions tested by NCAB are:
FR4 Tg150 IT158TC + Taiyo PSR4000-GHP3X + AVR80BA
FR4 Tg170 S1000-2* + Taiyo PSR4000-GHP3X + AVR80BA Green soldermask
FR4 Tg170 S1000-2M + Taiyo PSR4000-G23K Green soldermask + AVR80BA
FR4 Tg170 EM827 + Taiyo PSR4000-GHP3X + AVR80BA
*The S1000-2 material could be replaced in the future by the S1000-2M.
According to EN 45545-2: ”A tested reference corresponds to a given thickness of laminate + a brand and thickness of soldermask + a brand and thickness of conformal coating”. Thickness qualified by NCAB: 1.6 mm.
To dig deeper into the EN 45545-2 standard, we talked to Vincent Laborde, Engineer at Leroy Automation.
Leroy Automation was founded in 1983, it is part of a French group including FEDD, Leroy Automation, Phenix and Team 31, acquired in 2021 by the Argos investment fund. Leroy Automation designs, manufactures and markets automation products and components for the railway, military and industrial markets. Its customers include Alstom, Bombardier, RATP and SNCF.
Purpose to protect people
The EN 45545-2 standard is of the highest importance when it comes to PCBs for the railway industry, Vincent Laborde can explain why it’s so important for the customers.
“Customers use this standard for safety reasons. Fire/Smoke standards have been existing for years in the railway industry. It was the first way of transport to apply them, and the aeronautical standards were modeled on those of the railways. They must be applied in order to prevent accidents that have already occurred, from happening again. Their purpose is to protect people. Sometimes these standards may seem complex, but it is essential to apply them”, says M. Laborde. Cables, in particular, are very restrictive because they are a fire path. The cable reacts like a wick that will transmit the flame from one product to another and amplify the fire phenomenon.
“The Fire/Smoke standard is well done because it takes into account the groupings. Our customers apply these standards at the request of train operators, simply for safety reasons. The origins of fire can be multiple: a heating during braking creating sparks or an act of vandalism (e.g.: defacement, cigarettes)”, says M. Laborde.
The most important parameters to consider for the qualification is the standard that establishes them.
“The most important thing is the material interaction (FR4, soldermask and conformal coating). It remains chemistry, so it’s something that has to be tested in the laboratory. It is not an equation that can be solved easily, there are too many unknowns for the fire resistance to be solved by computer models. The standard, depending on the part concerned, will determine different levels of requirements”, says M. Laborde.
For PCBs, this translates into a material interaction: for example, a TG 150 material, a TAIYO PSR4000 soldermask and an AVR-80BA conformal coating. This combination can react completely differently, that’s why the entire interaction between the three elements must be validated.
“10-15 years ago, we did not consider the soldermask but we have seen in the results that it has a great influence because it is the first layer. Then, we have to take into account the different groupings when there are several electronic boards side by side because they can transmit fire to each other”, says M. Laborde.
In relation to PCBs one often talks about the components as well, should the components be taken into account in this qualification?
“It is the weight that is taken into account. Below 10 grams of flammable material, the components are not taken into account because the energy they will generate when burning will be very low. The component itself can weigh more than 10 grams, it is the flammable material that cannot exceed this weight according to the standard”, says M. Laborde.
Vincent Laborde explains that the biggest risk for Leroy Automation, in case of the parameters not being respected, would be a short circuit on one of its products. In case of fire, the product must be able to contain the fire.
“Roughly speaking, the flame test is similar to the stuffed animal test for children: the stuffed animal is exposed to a flame for a certain time, then the flame is cut off. The lint must not be allowed to continue to burn and burn out. It is exactly the same principle with the printed circuit board. 15 years ago, the first tests were disastrous, the whole PCB went up in smoke after 10 seconds”
Vincent Laborde
Engineer, Leroy Automation
“If the product does not respect this standard and causes a fire in a train, Leroy Automation will be held responsible. On the other hand, if the product causes a fire in a train and the company demonstrates compliance with the EN 45545-2 standard, it will not be held liable. A train is worth several million euros, so the risk for Leroy Automation is mainly financial, not to mention the human lives that are priceless”, says M. Laborde.
With human life and potential massive financial risk on stake, testing of the printed circuit boards is of the highest importance. Vincent Laborde explains how Leroy Automation proceeds with testing.
“The testing of printed circuit boards at Leroy Automation is exactly the same. At the time, Leroy Automation advised NCAB France to carry out its tests with CREPIM. We follow the R24, R25 and R22 criteria. We try to make it easy for our main customer, the SNCF, to complete the STMS directly. Even if we have to comply with the EN 45145-2 and STMS 001 standards, the tests carried out are the same: flame and toxicity”, says M. Laborde.
He draws parallels to testing of the printed circuits, to testing of stuffed animals produced for children.
“Roughly speaking, the flame test is similar to the stuffed animal test for children: the stuffed animal is exposed to a flame for a certain time, then the flame is cut off. The lint must not be allowed to continue to burn and burn out. It is exactly the same principle with the printed circuit board. 15 years ago, the first tests were disastrous, the whole PCB went up in smoke after 10 seconds”, M. LABORDE concludes.
There is also the hot wire test. It is a wire that is heated to 850 degrees and that is stuck to the PCB. The goal is that the PCB does not ignite. There are several levels of danger going from HL1 to HL3 (the highest) according to the modes of evacuation of the trains.
“The R22 is no longer concerned by the EN 45145 standard but the SNCF continues to ask for this test to measure the opacity of gasses. If a train has to be evacuated and the fumes are dense, visibility is reduced. It is these gas levels that Leroy Automation will test. There are 6 levels of gas that are toxic to humans”, says M. Laborde.
Testing the printed circuits for the flammability is strictly after the routines, and would need dedicated areas for this, a costly affair one might think. At Leroy Automation they have found a good solution to this.
“The fact that some manufacturers such as NCAB validate the material interaction, is very useful for Leroy Automation which can rely on these tests without having to redo them. We do not have a dedicated laboratory to perform the tests at our facilities, but work with 2 independent laboratories: CREPIM, or LNE (Laboratoire National de Métrologie et d’Essais) to perform our tests”, says M. Laborde.
Validating the material interaction is a definite commercial advantage for both new and existing customers of NCAB. NCAB can certify compliance and provide a report, which can reassure the customers.
Are you interested to know more about how we handle printed circuits for the Railway Industry?
Do not hesitate to contact us.
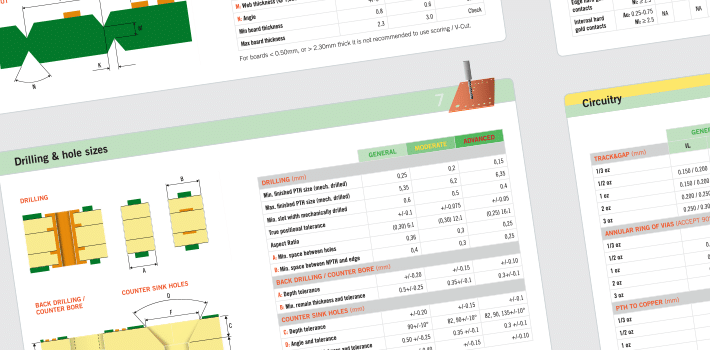
PCB design tools
For more advice about PCB design or applications of PCBs, we
have different PCB tools that can be downloaded for free.