Electronic devices are becoming more and more complex as the years go by. This means that the printed circuit boards (PCBs) must be designed with precision and care to ensure that the end product is successful. The most important thing to remember is that high-power circuits are not just a single component but a system. The system has to be designed with consideration for all its components, including the circuit board, electronic devices, thermal management, and power supply.
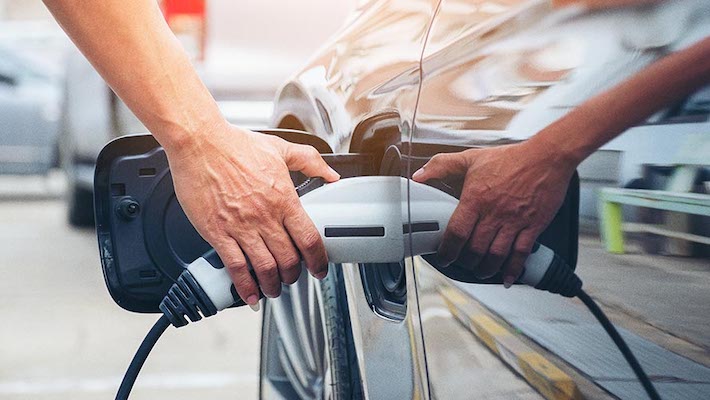
Some of the applications and end-products that require high-power circuit design are:
- Industrial power supply
- Servo motors
- EV charging
The following are some examples of high-power circuit design:
- A charging system used for EV batteries
- A projection TV that needs at least 300 watts of electricity
- Heat management systems for spacecraft
- Projection screens with more than 3000 lumens
- Thermoelectric coolers that require 5 kW of power
High-Power Considerations for Design
High-power applications are those that require a lot of power to operate. This is usually because they are used in devices that need to be able to run for a long time without being plugged in.
High-power circuits are defined as having a voltage or current of an order of magnitude higher than that used in a low-power circuit. Designers must ensure that the circuit operates at the proper voltage and current and has enough cooling and safety provisions. The following are aspects that need to be considered in the high-power design.
Thermal management
High-power electronics have a larger heat flux than low-power electronics, so it is important to consider thermal management in high-power designs. This heat needs to be managed for the circuit board not to overheat and fail. Thermal management can be achieved using a combination of passive and active cooling methods. Passive cooling includes using materials with low thermal conductivity, such as plastics or ceramics, which are used for insulating purposes. Active cooling includes using fans or liquid coolers to dissipate heat from the circuit board.
Materials
The material commonly used in PCBs is FR4, with high power applications, the material properties become more important than less demanding applications because of the increased thermal stress. The material properties most commonly connected to this application are high Tg as well as high Td Stable Coefficient of thermal expansion (CTE, value of expansion when heated) and in some cases a high Comparative tracking Index (CTI, value of ability to resist unwanted current flow between traces).
Solder mask
The solder mask is a protective layer that is applied to the surface of the PCB. It protects the copper from corrosion and contamination. The solder mask technique can be classified into two types: wet and dry. Wet solder masks are applied by dipping or spraying a liquid solder mask onto the board surface, while dry solder masks are applied as a sheet polymer onto the board surface. High power PCB design requires special consideration for solder mask technique because high power boards are more susceptible to corrosion and contamination than low power boards. While dry film offers a more consistent coating, dry films have become less common in mainstream fabrication.
Layout
Most high-power PCBs will use some type of design that fall into one of two categories: layout or reference design. Layout refers to how the components are laid out on the PCB, while reference designs are usually done with specific layouts in mind. The layout of the PCB board needs to be designed in a way that it can handle the high power components and also reduce noise generation. Some rules need to be followed when designing a high-power PCB board. These rules are:
- The ground loops should be minimized as much as possible.
- The voltage should not exceed the maximum voltage rating of any component on the board.
- Noise generation should be minimized by using low inductance tracks and low capacitance vias.
- The board should be designed to support heat dissipation.
- The board should be designed to reduce the chances of electrostatic discharge (ESD) damage.
- Any traces that are not critical must be protected with a ground plane.
Component placement
The high power component placement is a design technique that is used to reduce the thermal resistance of the PCB. This technique is used when there are high-power components on the PCB. This can be done in two ways:
- The first way is to place the components close to each other and use a small copper area for heat dissipation.
- The second way is to place the components far from each other and use a large copper area for heat dissipation.
Trace width and thickness
The thickness of the copper traces is determined by the power that will be applied to them. The higher the power, the thicker the trace needs to be. The width of a trace is determined by its function. Internal traces are narrower than external ones because they are not exposed to outside interference. Ground planes are wider than internal or external traces because they need to dissipate more heat and have a larger surface area for grounding purposes.
What Design Advice Do We Recommend?
The first thing to consider is heat dissipation. The higher the power, the more heat will be generated, and the more heat will need to be dissipated from the board. This means that you will need to use larger copper areas, more vias, and thicker layers of insulation material to keep your board from overheating. There is also a possibility to incorporate copper coin technology into the design. You can learn more about this emerging technology here.
How Do You Maintain Safety and Reliability Within Design Parameters?
The following are some precautions that should be taken into account when designing a high power PCB:
- The design should be done by an experienced engineer who knows the effects of high power on the PCB design while also consulting with their PCB supplier.
- The design should take into account the effects of heat on the components and layout.
- The design should take into account the effects of electromagnetic interference (EMI) on other devices near the device being designed.
- The design should take into account any potential hazards that may arise due to over-voltage or over-current conditions, such as fire, smoke, or explosion.
- The design should comply with RoHS and IPC standards for safety and reliability as well as CE, CCC, and UL Certifications.
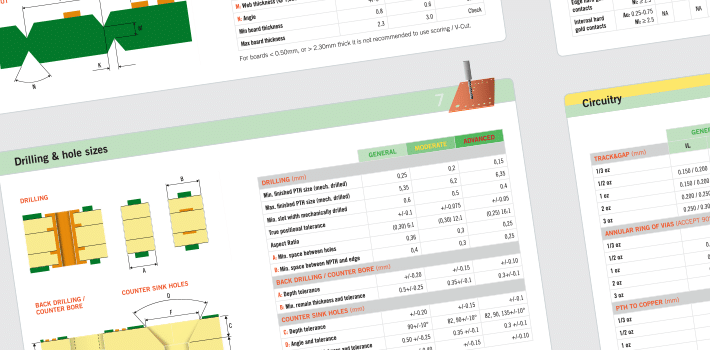
PCB design tools
For more advice about PCB design or applications of PCBs, we
have different PCB tools that can be downloaded for free.