A number of predominant technical trends are today driving the applications in which PCBs are used. We asked NCAB Group’s Chief Operating Officer Chris Nuttall how he views these developments and their impact they may have on the PCB industry.
What are the new technologies driving the PCB world today?
“It’s not about specific technologies that are driving the PCB world today; it’s more along the lines of some key technology trends, that drive the electronics industry and the related applications themselves. For starters, we now have fifth generation mobile communications, 5G, which is a common topic today. There are other trends that are emerging, that are somewhat dependent upon the development of 5G systems. These trends can be split into ‘people centric’ – related to how technology will affect us. And also ‘smart spaces’ which focuses on technical trends that influence the living or working environment.
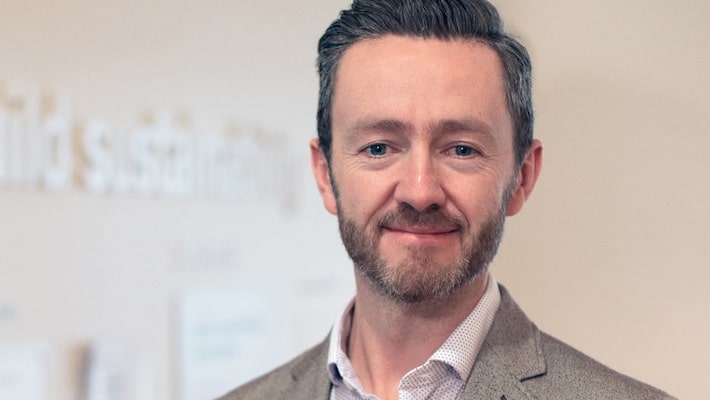
“We’re seeing solutions that are achievable with track and gap on boards that are as low as 30 microns.”
Chris Nuttall
Chief Operating Officer, NCAB Group
IoT, AI and 5G some of the technical trends we see
We have all heard about the Internet of Things (IoT) and artificial intelligence (AI). In combination with the increased data transfer rates available through 5G, they can open up a whole new level of connectivity and communication between devices and things. This enables, for example, developments in smart products such as smart production or hyper automation, advanced robotics, development of public safety functions to support smart cities, the increasing use of autonomous things. These trends go hand in hand with the ability to transmit, transfer, manage and process massive amounts of data in a short space of time with low latency problems. Key features of edge computing.
And then finally, there’s the drive toward human augmentation that not just replaces human capabilities such as prosthetics, but more towards a capability that changes or enhances capabilities. I am not sure exactly how much of this we are seeing right now, but we will see it increase over the next five years.
Some of the trends highlighted form the basis for the development of autonomous cars
“These are some of the technical trends that will I believe have the greatest impact on PCB technology in the foreseeable future. Such high-level trends will of course translate into other technical trends and themselves drive specific applications in various industries. For example in the automotive industry some of the trends highlighted form the basis for the development of autonomous cars; in medicine you’ll find them driving critical functions such as data processing and real time communications between specialists operating on a worldwide level. Similar trends are also very much apparent within military applications, which are driving developments in certain markets.
“As we touched upon in an earlier blogpost, 5G is now being introduced on an ever larger scale. Looking at China alone, they are projecting a user base of 500 million phones, or other such devices, by 2025. In Europe and the US, things are moving a little slower than in Asia, but the trend is definitely here.”
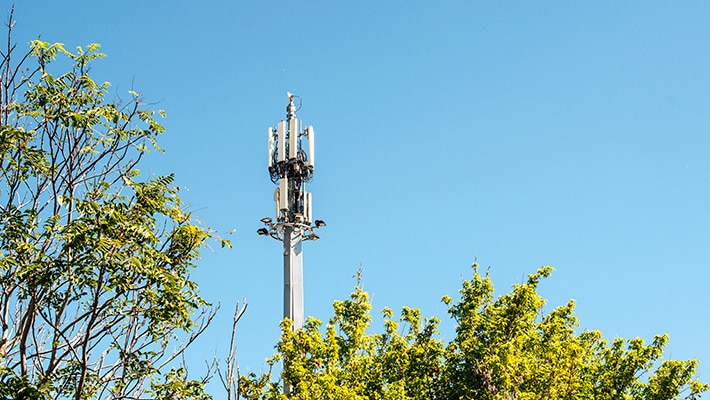
In what ways have these changing scenarios affected the design and manufacture of PCBs?
“It’s the continuation of an already established trend. PCBs are having to incorporate a greater number of layers, increasing density of features supported with smaller track and gaps and smaller hole sizes. In the past, a PCB with multiple layers and type 1 HDI structure used to be looked upon as groundbreaking. Today, ten-layer HDI structures aren’t unusual. We’re seeing solutions that are achievable with track and gap on boards that are as low as 30 microns. It took a long time to get down from 100 microns to 75, and further down to 60 microns, which a small number of NCAB’s factories can support today. Some of our factories are commissioning new equipment and establishing the process controls and experience to enable even higher density. Looking beyond our factories, those at the real forefront of technology, are already producing printed circuit boards with less than 30 microns.
“It’s not about specific technologies that are driving the PCB world today; it’s more along the lines of some key trends, that drive the electronics industry and the related applications themselves.”
Chris Nuttall
Chief Operating Officer, NCAB Group
More complex components
“As components such as semiconductors become more both more common and more complex, we are also seeing more and more growth in IC substrates which acts as the connection, think of a smaller high density PCBs that sits between the component and the circuit board. These substrates have a very high density and support power and signal distribution as well as some level of heat dissipation. It opens up for very small conductor width and insulation distances as well as fine hole sizes. Today, IC substrates are already used in the higher end boards and are becoming more commonplace.
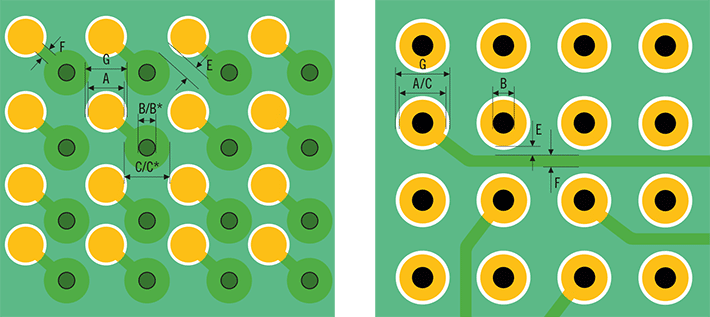
And where would you say NCAB’s factories are when it comes to the latest technology?
“This forms part of our strategy for working with the factories and having a strong enough relationship that they will share with us their direction and thoughts regarding the next five years. If we look at our more technically competent factories, they are already looking at much more complex structures, some are already supplying IC substrates and others are working towards volume solutions when it comes to track and gap widths of 30 μm. That’s less than half of what they are currently approved to manufacture right now. This level of increased density and complexity will only continue to grow going forward.
The need for more printed circuit boards of higher complexity will increase
“As more and more products are developed as part technical trends areas, the need for more printed circuit boards of higher complexity will increase too. This means that the pace of change will see that technology looked upon as cutting edge today, will become standard technology tomorrow. That’s why our more technologically advanced factories are gearing up to ensure that they will be positioned to support higher complexity, greater structures, such as any layer builds, finer pitch and occasionally different materials. This will lead to demands for new equipment, new raw materials and production lines taken to the next level. For example, we will see the balance continue to move towards increased solutions for direct imaging as opposed to solutions focussing on the traditional photo tool imaging processes.
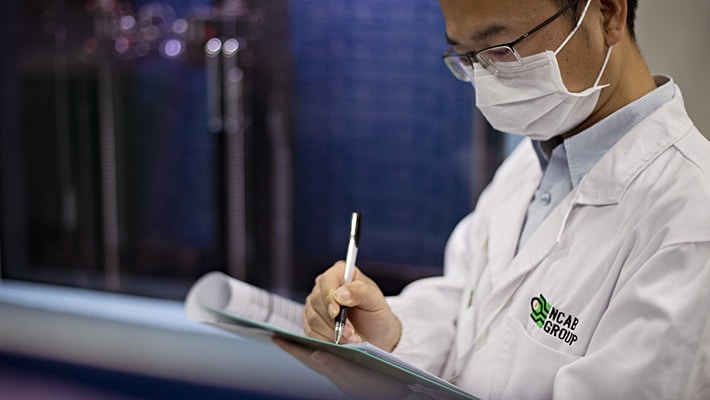
“We live in fascinating times. If you look at some of the key manufacturing equipment available today, it’s amazing. Only a few years ago one would have thought that these things were way ahead on the technical horizon, but now they are here. Moore’s law, that says the density of microchips doubles every two years, is absolutely happening.”
What challenges, apart from technical, lie ahead in the PCB manufacturing world?
“An important challenge for the factories is to build up their knowledge of design and manufacturing experience at the same rate as equipment, raw materials and new solutions become available. The factories will be under pressure to develop this knowledge, while at the same time making sure to balance the learning process with their core businesses so as to generate revenue combined with good yields from their production here and now. Research and development teams will need to work faster. That is why NCAB’s evaluation process includes keeping a close eye on the factories’ development plans on a two to five years’ perspective.
“An important challenge for the factories is to build up their knowledge of design and manufacturing experience at the same rate as equipment, raw materials and new solutions become available.”
Chris Nuttall
Chief Operating Officer, NCAB Group
Smaller and more complex components due to the technical trends
“With the component industry following similar trends they are driving component foot prints smaller and finer pitch, PCB suppliers have to be able to meet the changing requirements. To meet customers’ needs, factories must invest in equipment, materials and building knowledge. It affects everything – pattern transfer, imaging, soldermask, plating, pre-treatment, surface treatment and so on. It is one thing to have the right equipment, you also need the right raw materials and the right processes combined within the right knowledge for it to work well and to get a reliable product at the end of day.
NCAB’s approach is clear, we are not aiming to be at the cutting edge of technology. We will only approve such technology when we know the processes are stable and proven in terms of producing a good end- product that meets our customer demands. However, it is necessary that we do know where the technical horizon is and how close the factories are to that edge.
Presence in Taiwan as well
“Through the acquisition of Bare Board Group, we have expanded the breadth of our operations and therefore our exposure to differing geographies in terms of printed circuit board production. Taiwan now accounts for nine per cent of our spend on printed circuit boards and whilst we are still at the early stages of really getting to know the factories, the initial signs are that some of the capabilities we see in the factories there, are adding to the technology levels that we have been able to offer within our product portfolio. There are some encouraging signs that, as we work through our defined qualification and approval processes, such factories may well enable NCAB to offer our customers increased solutions on both a technology driven and a supply chain level.
Areas being developed within PCB manufacturing
- Multi-layer boards with more and more layers.
- Flex and flex-rigid boards.
- Increasingly complex HDI structures that use IC substrates to enable track and gap as small as 20-30 μm and very tiny via holes.
- Direct imaging where the pattern is printed directly on the material.
- Higher degree of automation in manufacturing.
- New surface finishes.
How is the printed circuit board industry geographically affected by the development?
“If you look at industry forecasts which were admittedly made before the covid-19 pandemic, they estimate that the value of the global PCB market this year would be about 67 billion dollars compared to 64 billion dollars in 2019. That figure is estimated to reach 70-75 billion dollars in 2023. China accounts for just over half, 52-53 per cent, of this. The forecast is that that whilst the technology levels will continue to rise, the output by region will remain fairly consistent at around the same level, certainly for the next four to five years.
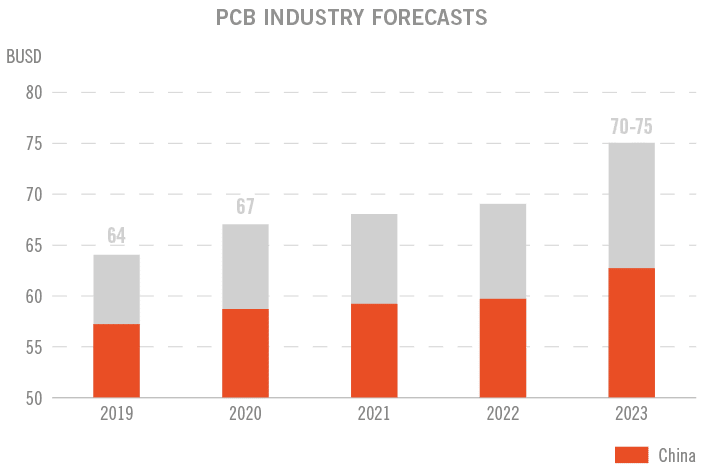
Things are moving faster and faster in China
“We see that the time it takes for new technology, developed in other markets in Asia, Europe and the USA, to migrate to China is constantly decreasing. Many of the bigger producers within the industry run R&D facilities or a have a smaller factory in Europe or the US, while having a larger volume based factory in China and this approach is a key factor in speeding up the technology transfer. I think we will soon see a situation where technology or product develop runs concurrently as time to market becomes even more critical. Things are moving faster and faster in China and we have seen that there is strong government focus on the developing the country’s industries so that they become closer to the very forefront of technology.
The factories become more familiar with the higher technologies
“If you compare with other manufacturing markets around Asia, China has considerable advantages, despite increasing costs. The Chinese PCB industry today has an advantage in so far as it has all the ingredients in place – knowledge, experience, infrastructure, raw materials, equipment and so on. This helps to maintain a technology gap between China and other lower cost countries and this is a key factor in the outlook for China for the immediate future. The other element that fuels this trend is that as the factories become more familiar with the higher technologies they are able to increase their technical offerings and grow revenue, which in turn means that they can also set aside funds for further investments and development thus keeping the cycle moving in a positive direction. Those trying to play catch up face testing times and big technical jumps are not only difficult to achieve, but also costly.
“The Chinese PCB industry today has all the ingredients in place – knowledge, experience, infrastructure, raw materials, equipment and so on.”
Chris Nuttall
Chief Operating Officer, NCAB Group
Niche board manufacturers in more countries
“There will be room for niche board manufacturers in other countries as well. Factories in countries such as South Korea, Taiwan and Japan can not only support their local markets in excellent ways, but also compete with a high degree of specialization, high technical standards and in some cases shorter lead times. At the same time, technically less advanced boards can be manufactured at a competitive cost in countries such as India, Thailand and Malaysia.
“If we look at what history has taught us, in China, we’ve seen that the shift from low technology to high technology can happen relatively fast, so one must not ignore events in other countries or underestimate their capacity to grow in terms of technology and competitiveness. But with the rapid development I have been talking about, with increasingly complex PCBs and higher demands from customers, the risk is that the gap will become increasingly difficult to bridge. It isn’t easy for those countries with less advanced manufacturing to quickly make major technology changes within their industries, so I think we will continue to see that technology gap continue for some time to come.“
Main technical trends that drives development
- 5G – the fifth-generation mobile communication.
- IoT – Internet of Things, when more and more things incorporate built-in electronics and internet connection, enabling them to communicate and be controlled over Internet.
- AI – Artificial Intelligence, programs that mimic human behaviour and thinking and can often improve their own algorithms through machine learning
- Human augmentation – Using technology to augment humans on a physical level (exoskeletons linked to brain implant) or cognitive level (AI working with humans to develop intelligence scenarios)
- Hyper-automation – Taking robotic automation to the next level using AI to automate all possible business processes, in some cases providing increased learning, agility and responses.
- Autonomous things – Physical devices that use AI to automate functions and actions (ranges from cars to homes, from delivery drones to warehouses or complex assembly processes)
Do you see any long-term implications of the covid 19 pandemic for the PCB production?
“I cannot say for certain that it has significantly impacted the technological side of things – it might have slowed down local tech support, but certainly not stopped things. If anything, it has intensified, as time to market has now become even more important. If we look at the factories, we have been through a phase where their operations slowed down slightly within certain areas, sectors, and customer segments. In China and Taiwan, the major investment linked to the 5G rollout has helped balance this.
The factories that did well before the crisis have been able to do more business with existing customers
“Globally, we have seen how customers have looked to consolidate their supply chains, so I don’t think that NCAB’s factories have experienced any major fall due to the temporary shutdowns in China, Europe and the USA. The factories that did well before the crisis have been able to do more business with existing customers. Other, smaller factories that make low end or cheap printed circuit boards have struggled when lead times started to be cut and they had to keep the factory running despite cuts in production.
“The pandemic has impacted European factories in so far as they have to tackle the challenge posed by the social distancing and other rules and restrictions implemented to contain the spread of Covid 19.
“Regardless of what part of the world we are talking about, we can generally say that the factories that had sound finances and efficient operations before the crisis are the ones that are managing it best. They will emerge stronger once its over. “
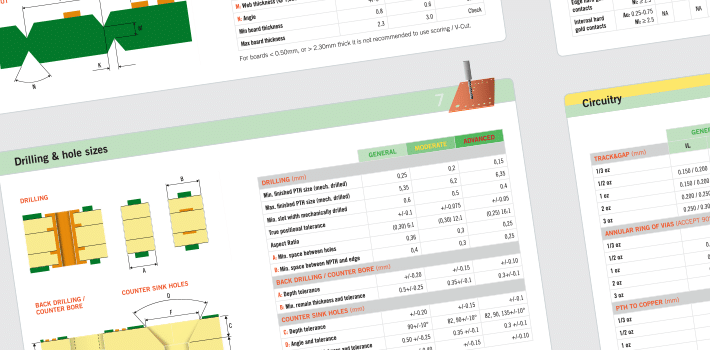
PCB design tools
For more advice about PCB design or applications of PCBs, we
have different PCB tools that can be downloaded for free.