The automotive industry is undergoing a revolutionary change. This is a challenging advancement; from reducing emission, to developing self-driving electric cars and trucks, to charging infrastructure. The electronic part in the new energy vehicle is more involved and advanced, and with this in mind, the demands on the PCBs will increase in various ways.
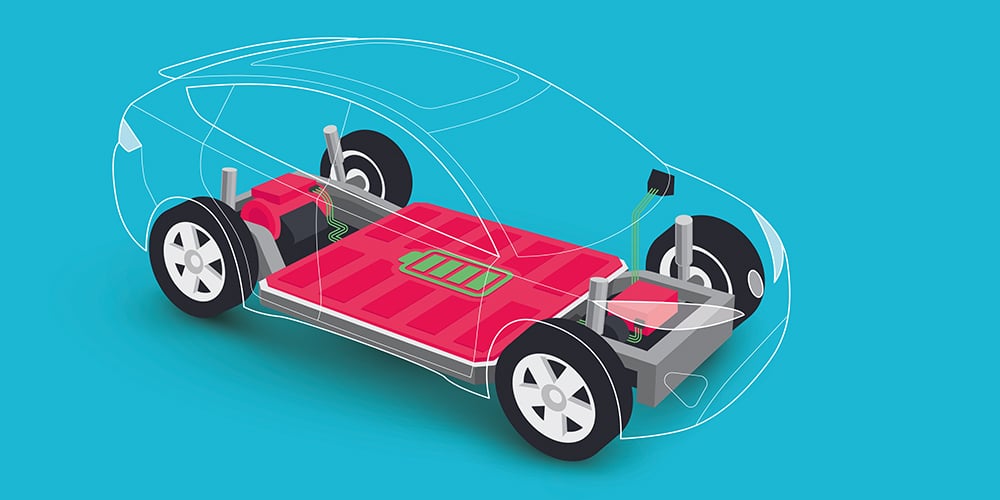
Compared with traditional fuel vehicles, new energy vehicles have a higher degree of electronization, which means that more functions need to be performed through electronic equipment. The reliability of electronic equipment has become the focus of improving vehicle reliability and driving safety.
High reliable PCBs needed
With the higher amount of electronics, how does this affect the PCBs? What is most important to think about in the PCB production process, and as a buyer of PCBs to the automotive industry?
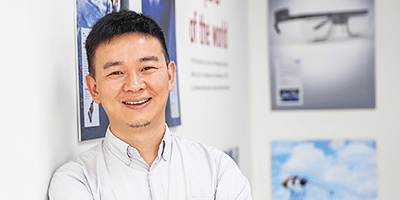
Barry Fang, Field Application Engineer Manager at NCAB Group China will tell us more about PCBs for the new generation of the automotive industry.
Q: In terms of the degree of electronics, what are the differences between new energy vehicles and traditional fuel vehicles?
A: Traditional fuel vehicles consist of an engine, gearbox and body frame, while new energy vehicles have transitioned to the electrification era. From the data point of view, in traditional luxury cars, the cost of automotive electronics accounts for about 25%, and in new energy vehicles the cost is 45%-60%.
The increase in new energy vehicle PCBs mainly comes from onboard chargers, battery management systems, voltage conversion systems (DC-DC converters, inverters, etc.) and other high-voltage and low-voltage devices. According to estimates, the total area of PCBs used in the internal combustion engine and transmission system of traditional fuel vehicles is about 0.04 m2. and the total area of PCBs required for a fuel vehicle with a moderate degree of electronics is about 0.43 m2. However, the total area of PCBs on the powertrain-related equipment alone has reached 0.8 m2.
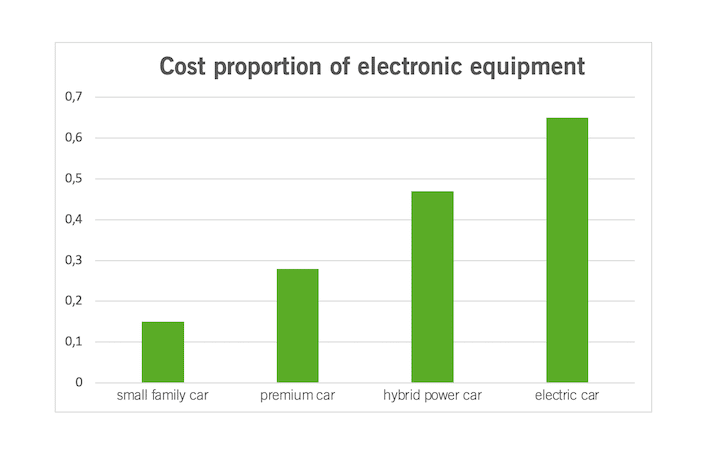
Q: What’s our focus for automotive PCB orders?
A: “Driving Safety” remains our focus. The reliability and safety requirements of automobiles are very high, and the requirements for PCB reliability and environmental adaptability are very strict. Its suppliers must pass IATF/16949 certification.
For different modules, our focus is also different. For example, the power system is used as the power source of the whole vehicle. The PCB in it needs to carry high voltage and high current. At the same time, it is necessary to consider that any PCB failure will cause the vehicle to fail to work normally. So, for the PCB in this system, ensuring its high reliability during the manufacturing process is our focus.
In the Advanced Driver Assistance Systems (ADAS), especially the camera or radar module, the signals carried by the PCB are often high-frequency and high-speed, and the quality of the signal directly affects the vehicle’s judgment of the real-time environment. So, in this area, we focus on the signal integrity or signal quality. At the same time, we also need to pay attention to the fact that the PCBs in ADAS systems are relatively complex, and more advanced solutions such as flex boards, flex-rigid boards, HDI boards, and hybrid boards (using several different materials) will be used, which means the supplier should have a higher capability.
“It is necessary to consider that any PCB failure will cause the vehicle to fail to work normally. So, for the PCB in this system, ensuring its high reliability during the manufacturing process is our focus.”
Barry Fang, Field Application Engineer Manager, NCAB Group China
Q: What are the main aspects to consider in manufacturing?
A: Take the power system as an example — where the PCB needs to carry high voltage, high current, and requires high reliability. From the perspective of the PCB production process, the main aspects are as follows:
1. In the early stage of PCB Layout, it is necessary to fully understand the customer’s product design, and leave sufficient margin according to the customer’s needs (rated power, voltage rating, current carrying capacity, etc.).
- For high voltage requirements, attention should be paid to high and low voltage isolation, air gap, creepage distance, etc. to meet safety requirements during design.
- For high current requirements, use thick copper design, and attention needs to be paid to current voltage drop, current carrying path, feedback, power supply filtering and decoupling issues.
- The PCBs which are the key components of automotive electronics shall comply with the IPC Class 3, and the selection of components shall comply with the vehicle regulations.
2. In the manufacturing process, it is necessary to disassemble the key parameters that affect the current carrying or voltage resistance, and refine it to the specific process link for control and overcome the difficulty of manufacturing due to thick copper. It is embodied in drilling quality, copper plating thickness, precision of conductor line width and spacing and coating of solder mask.
Main aspects to consider with thick copper products:
- Drilling: Overcome the challenges of thick copper and ensure drilling quality. Thick copper products come with some challenges in drilling process, such as the easily cracked inner layer, the over-rough hole wall, and the nail heading. So we need to adopt special graphic design and optimize drilling parameters (rotation speed/ feed speed/retraction speed/drill life) for such problems, evaluate drills suitable for thick copper plates, and select the most suitable combination of parameters through the DOE (Design for Experiment) test to ensure the drilling quality.
- Lamination: It is necessary to ensure that the resin is fully filled and tightly bonded between the lines during the lamination process to ensure reliability. The thicker the copper, the more difficult it is to laminate, and high-level products require attention to the alignment between layers.
- Copper plating: It is essential to ensure hole copper thickness and copper surface uniformity..
- Etching: The thicker the copper, the more difficult it is to etch the trace. It is necessary to control the line width and spacing accuracy of the conductor to ensure that it meets the current-carrying and voltage-resistant requirements.
- Solder mask: When there is high copper thickness, some special processes may be required to achieve the overall thickness. For example, multiple printing is required to separate copper surface and the substrate surface ensuring the quality of soldermask and avoiding copper leakage or yellowing of the pins (due to thin soldermask).
- Special design: Semi-metallized hole, metal edging design, etc.
Q: How do you view the future development of new energy vehicles?
A: Smart roads + smart cars are the ultimate direction of smart transportation and autonomous driving. New energy vehicles are also developing towards electrification, intelligence, networking and signal transmission.
First of all, the technology is more mature. Although it is said that the cruising range of new energy vehicles has reached 400 to 500 kilometers, the actual cruising ability varies. So here’s still a lot of room for improvement on how to maximize motor efficiency under various complex road conditions. Secondly, the driving system is more user-friendly, and the driving experience will become a key point for car companies to differentiate and attract users. Furthermore, the travel is more intelligent. The development of 5G+C-V2X Internet of Vehicles gradually helps to understand real-time information exchange between vehicles and all factors that may affect the vehicle, reduce accidents and optimize the traffic environment to achieve autonomous driving.
The development of technology will inevitably be accompanied by the iteration or new requirements of electronic equipment, which will inevitably lead to new PCB requirements. At the same time, more advanced PCB solutions such as HDI, flexible boards and semi-flex boards will be used more and more.
Whether it is from the reliability of the PCB or the long-term consideration of the brand, it is particularly important to choose an experienced, professional and reliable supplier.
Q: What added value can NCAB provide to automotive electronics customer?
A: Vehicles are not only a travel tool, but also closely related to the personal safety of drivers and passengers. Vehicle manufacturers need to understand and control the source of PCBs used in their products, as this involves the critical construction of the product and the impact on their brand reputation.
As a reliable supplier, NCAB can provide professional technical support and services in the whole process from design to manufacturing, helping to create high-quality and reliable PCBs. In the early design stage, we have an experienced PCB design team, which can provide valuable engineering suggestions in the layout stage according to the specific product requirements of different customers, carry out design optimization and help customers to get it right from the start.
“More advanced PCB solutions such as HDI, flexible boards and semi-flex boards will be used more and more.”
Barry Fang, Field Application Engineer Manager, NCAB Group China
At the same time, incorporating Design for Excellence (DfX) services into the design process to ensures that design files can be delivered seamlessly to manufacturing. In the post-manufacturing stage, we will select the most reliable and stable factory under the premise of meeting customer demands, and only use the factory for in the areas where it excels. Our factory management team also conducts quality control onsite to ensure that the products perform as expected.
Questions?
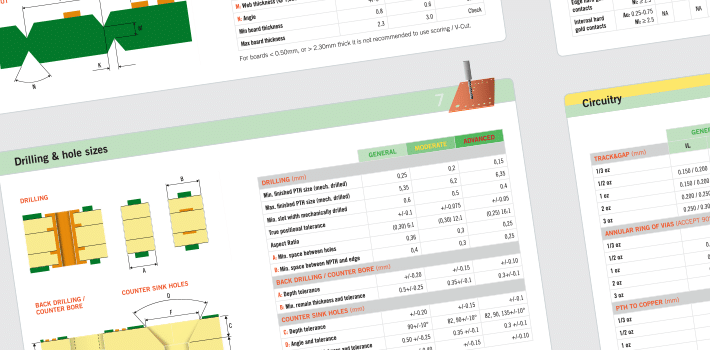
PCB design tools
For more advice about PCB design or applications of PCBs, we
have different PCB tools that can be downloaded for free.