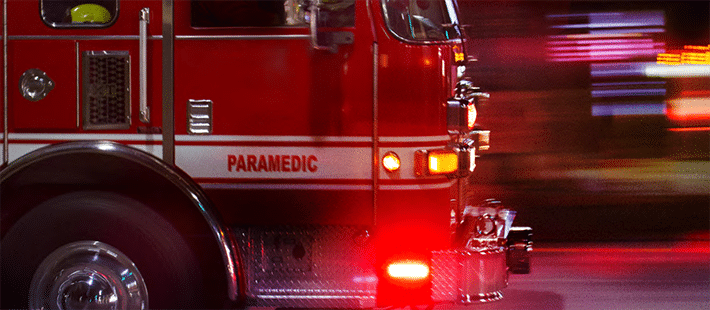
Reliability is a key factor right from the start of the PCB production process. If a PCB has a reliability issue, the end product itself is at risk. The important thing is getting it right first time. Trying to improve reliability once the product is designed and in production can lead to massively high costs for the product owner. In some cases, for example, medical equipment or motor vehicles, it could even become a matter of life and death.
PREVENT PROBLEMS IN TIME
Creating reliable PCBs is very much about considering all aspects that can affect reliability as early as possible in the production process. If there are problems with the PCB design, that is the best time to tackle them.
“You can’t compare a PCB to other components, its design has been tailored to a specific product and specific application. As a component, its role is critical. A good board design improves the reliability of the end product and lessens the risk of failure,” says Ryan Pellow.
“Perhaps the most important thing to focus on is ensuring that the track and gap on the board is appropriate to the required copper thickness. With the type of components we are getting today, you need smaller track and gap, which means you need to use less (thinner) copper,” emphasizes Steve Shipway.
Before you go too far into any design, it is vital the designers know exactly what is achievable with the specified copper weight requirements. If changes are needed to the layer stack up, for example if some high power areas are needed on the board, it should be designed to ensure that those high power sections are in the inner layers. You need to avoid the outer layers, since that is where the fine-pitch components are located. This approach makes the board easier to produce.
“The higher the technology, the greater the effort required to design the board optimally for manufacturing. That is the only way you can make sure they will ultimately function reliably,” says Steve Shipway.
“In high-technology products there is far less room for errors, with less tolerances applied in every single process. That’s why all aspects of the PCB design needs to be strengthened. A better design increases the reliability of the product and reduces the risk of failure,” says Ryan Pellow.
THE RIGHT FACTORY FOR THE TYPE OF BOARD IN QUESTION
Once the design is completed, you normally can’t turn to the same factory and just ask them to manufacture a more advanced board. You have to make sure the manufacturer has the appropriate capability and competence to produce the kind of board in question.
“Although the manufacturing processes for a 2 layer & HDI PCB are similar to each other, the technology is very different. To ensure reliability, the factory needs a higher level of understanding and control of the manufacturing process,” says Steve Shipway.
The “final inspection” is the penultimate step in the production process. Here, the PCB undergoes an ocular examination by NCAB-approved quality controllers, using our standard specifications requirements. The board is compared to the Gerber file using AVI, which is faster than the human eye – the process is, however, monitored by our controllers.
At the same time, one should strive to design boards in a way that they can be manufactured reliably by as many factories as possible. In this way, you can attain better lead times and a better cost picture, while maintaining quality.
“Manufacturing PCB´s is often challenging when it comes to applying the very latest technology required by the component manufacturers. That’s why it is important to avoid the hassle of doing things unnecessarily,” says Steve Shipway and cites an example: “If you can avoid designs containing, six or seven different layers of blind or buried vias to track out a BGA [component] and reduce it to a standard multilayer board, you should do so. This does away with all the extra drilling and plating processes and significantly reduces costs, whilst at the same time improving the manufacturability of the product.
“If you keep your manufacturing options as open as possible through a smart design, this will also allow you to switch production from one factory to another, which reduces the risks one is exposed to. If one factory is underperforming or dealing with some kind of issue, you would be able to move the production to another facility. The last thing you want is a PCB design that limits you to using a single factory,” Steve Shipway states.
TOUGH DEMANDS ABOVE AND BEYOND INDUSTRY STANDARDS
One factor behind achieving reliable circuit boards is to ensure that they meet the industry standard IPC requirements. NCAB Group has taken this a step further and produced its own standard product specification. At present, it comprises up to 103 different requirements and criteria that the factories must follow when manufacturing for NCAB. It is a real time document that is being continuously built on and improved in cooperation with customers. Several of the requirements are considerably tougher than those stated in IPC class 2.
“PCBs cannot be treated like other components because there are so many levels to take into account. The industry standard IPC applies to many different types of products, requirements and performance levels. In the case of PCBs, it is unable to cover everything. But for the product owner, an unreliable board involves huge risks and that’s why it is worth taking all aspects into consideration,” Ryan Pellow explains. “Through all the years that NCAB has been supplying PCBs, it has built up a wealth of knowledge covering factors affecting the boards’ quality and reliability. It might involve such things as material selection, true hole copper thickness or the solder mask used in manufacturing, or selecting the peelable mask that gives the best end result, and so on. This is the kind of knowledge that NCAB has compiled in its standard requirements specification.
“It covers specific areas where a higher degree of control is necessary. For example, the factories must use only approved brands for the materials that are used in manufactured. For the plating of the hole wall, 25 μm thickness of the copper must be achieved, which exceeds IPC class 2. No track welding or open circuit repairs are allowed if the boards are to be approved and there are requirements for factors such as cleanliness.
“In fact, we also define clear cosmetic requirements for the PCBs. Multiple scratches on the board can suggest accuracy and care issues during the manufacturing process, which could affect reliability,” Ryan Pellow continues.
FREEDOM UNDER RESPONSIBILITY – AND CONTROL
It is not always easy to navigate through the demands to be placed on a factory. For example, it may seem like a good idea to specify an exact material of a precise brand to ensure adequate control. It may sound like a contradiction, but in such a case, it might be safer to settle for an IPC standard (IPC 4101) and a number of approved brands.
“The factory will then be free to choose the material that it has the greatest experience with and which is best suited to its manufacturing processes. Forcing a specific choice on to the factory can create problems, since it could impact the reliability of their processes, compared to if they had used a material they are familiar with,” Ryan Pellow explains.
Wendy Liu, Quality Manager and Jerry Zheng, Production Quality Engineer NCAB Group China outside a factory.
Having your own staff and expertise in place at the factories is also important as a means of checking that the specifications are met. This also means that you can help the factories grow their business if needed.
“NCAB’s factories know why we apply these high standards and why we go beyond IPC. We help them live up to our high demands and they can improve their manufacturing ability in general. Our model leads to a win-win-win relationship that our customers, factories and ourselves will benefit from,” says Steve Shipway.
“Just as we strive to be a partner for our customers, for example by helping them with the design of PCBs, we also work closely with the factories to help them improve their offering and reliability,” says Ryan Pellow. “While a factory may just be focused on a specific technology, NCAB has built up an enormous breadth of knowledge that includes almost all types of PCBs. We are ready to share this experience, to the benefit of both our customers and the factories,” he concludes.
Read the article in another language
The Newsletter InFocus no 2 is also available in Chinese, Danish, German, Spanish, Finnish, French, Italian, Polish, Russian and Swedish.
Download them here »
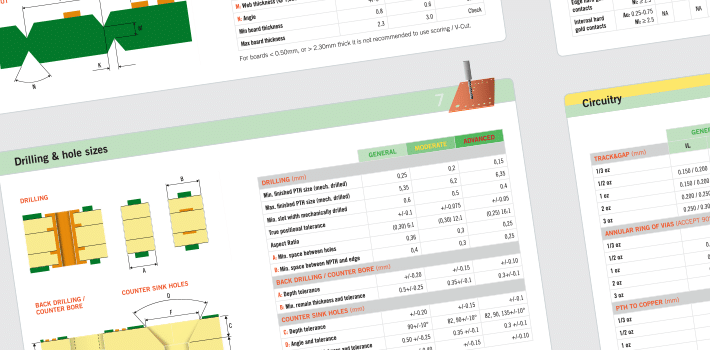
PCB design tools
For more advice about PCB design or applications of PCBs, we
have different PCB tools that can be downloaded for free.