Due to an increased demand for advanced materials to support the growth in 5G applications, many laminate manufacturers have increased the production and output of high-performance or high-speed material at the expense of standard performance materials. The current situation is having a negative effect on the supply of standard performance material (low-to-mid Tg). The consequence of the situation is that demand for the standard materials is greater than supply, and we face shortages as a result of this imbalance. And it is not just 5G that is to blame; many designs for the automotive industry are fueling demand for advanced laminates.
Why are laminate manufacturers prioritizing high-performance materials? The answer is simple; they can charge more per panel for the advanced laminates. For example, a factory can sell a sheet of high-speed, low loss-material for antennae or base stations for almost six times as much as they can sell a sheet of standard FR-4. The goal of laminate manufacturers is the same as any other industry – to make money – and when a new market opens up with what appears to be endless possibilities, they focus their floor space on the higher-margin product.
Since the demand exceeds the supply of standard material, the direct consequence is an increase in lead times, from today’s 2–7 days up to possible 3+ weeks, depending on the material and factory. In extreme cases, we have seen 45+ days material lead time for materials that were easily procured in less than a week six months ago. We are also being made aware of some materials being subject to an increase in pricing. The impact of both availability and pricing will be felt throughout the PCB industry.
As is always the case, planning will be the most important factor. Forecasting your circuit board demand will allow you to communicate with your board supplier as to your requirements; this will also allow the supplier time to allocate material, even before an order is placed. The larger the PCB requirement, the more important this becomes since manufacturers will sometimes keep small amounts of materials in stock but will buy on-demand for the larger builds.
Another way to address this issue is to maintain an open dialogue with your PCB supplier. It is important to consider materials and their availability during the design phase of your PCB and not rely on one particular brand of material to minimize potential impacts to lead time. Allowing for material equivalents instead of a specific brand will allow the board supplier more freedom to choose the material with the shortest lead time and/or the best pricing.
NCAB Group’s recommendation is not to specify one specific brand or type of material wherever possible, as this can ultimately limit the supply chain options in terms of who can support the project. While many well-known brands of material are widely in use, there are occasions where some factories have several material brands or preferences that achieve the required material specification. Availability and price can then become factors as to which brand will be used.
This does not mean that you cannot specify known materials—far from it. If you have experience with a material that you know works for your product, then it can simply be referenced with a comment stating “or equivalent”; then, technicians and procurement teams can review and offer you an alternative that will meet the functional needs without compromising performance.
Every well-known manufacturer of material will have their product categorized in accordance with IPC-4101 (specification for base materials for rigid and multilayer printed boards) with the aim of this specification being to identify and categorize performance characteristics. Using this categorization approach is ideal as it defines the characteristics of the base material in detail; it also allows the manufacturer to follow the IPC-4101-xxx categorization, enabling them to select wisely and ensuring performance is nothing less than expected.
We anticipate that the laminate manufacturers will find ways to adjust to the new demands and eventually increase the production of the low-to-mid Tg materials, as has happened with the other crisis the PCB industry has faced. But until this happens, we will all need to modify the way we think about laminate stock. Perhaps we will need to look at laminate as a component and plan our needs accordingly.
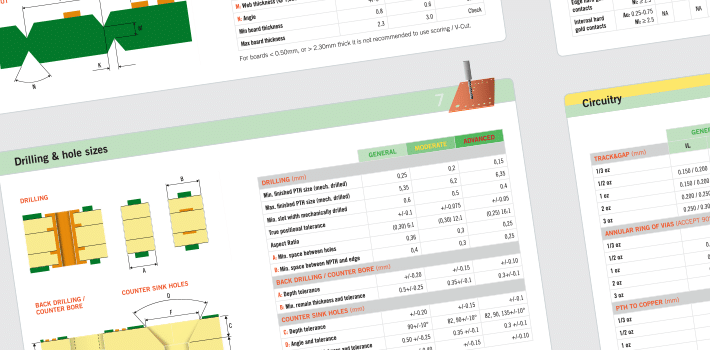
PCB design tools
For more advice about PCB design or applications of PCBs, we
have different PCB tools that can be downloaded for free.