What is the difference between adhesive and adhesiveless flex systems?
Builds that use adhesive systems rely on adhesive to bond the copper to the flex core. As such this adhesive layer along with full coverlay, penetrates into the rigid construction and directly into the hole. The greater expansion coefficient of the adhesive increases the risk of through hole problems, such as cracks and via hole failures as a result of the expansion, while having this material within the hole itself can lead to hole wall copper formation issues resulting from poor desmear of adhesive.
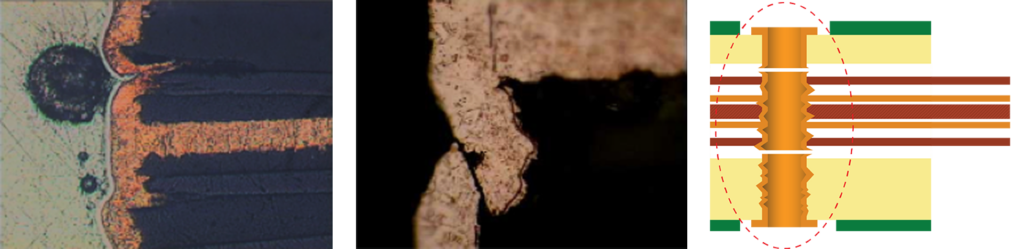
The solution to improving via / through hole reliability was to move towards an adhesiveless copper clad system (copper bonded directly to the polyimide) and limit the overlap of the coverlay into the rigid part of the board. This ensures a much more reliable through hole structure without adhesive penetrating into the hole. This is by far the most common approach to rigid flex.
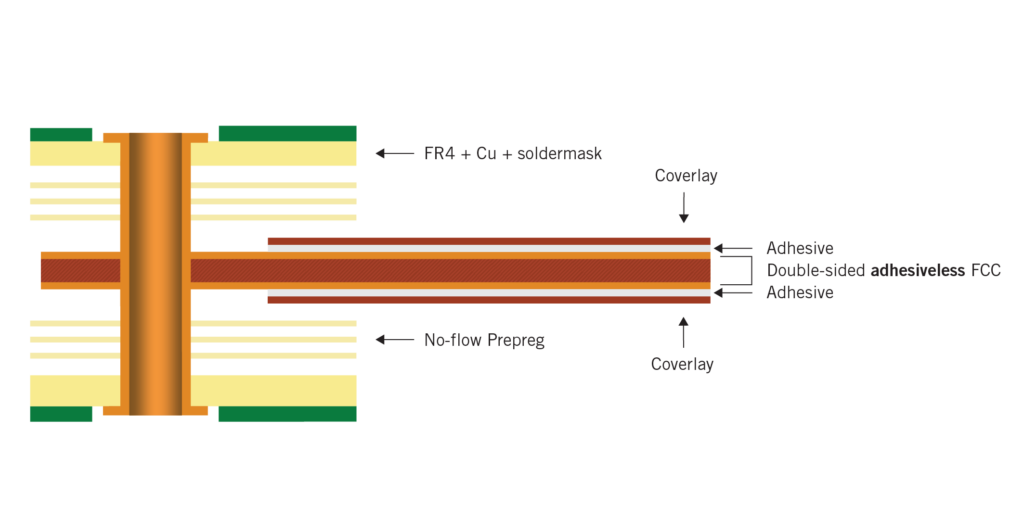
What is the difference between semi-flex and rigid flex?
Semi flex is effectively a ‘standard’ multilayer PCB, built using specific types of FR4 that has been depth to a specific tolerance so that the resulting thinner area provides a flexible / bending section of the traditionally rigid FR4.
Semi flex is suitable for static applications (flex to install), or with very limited number of bends.
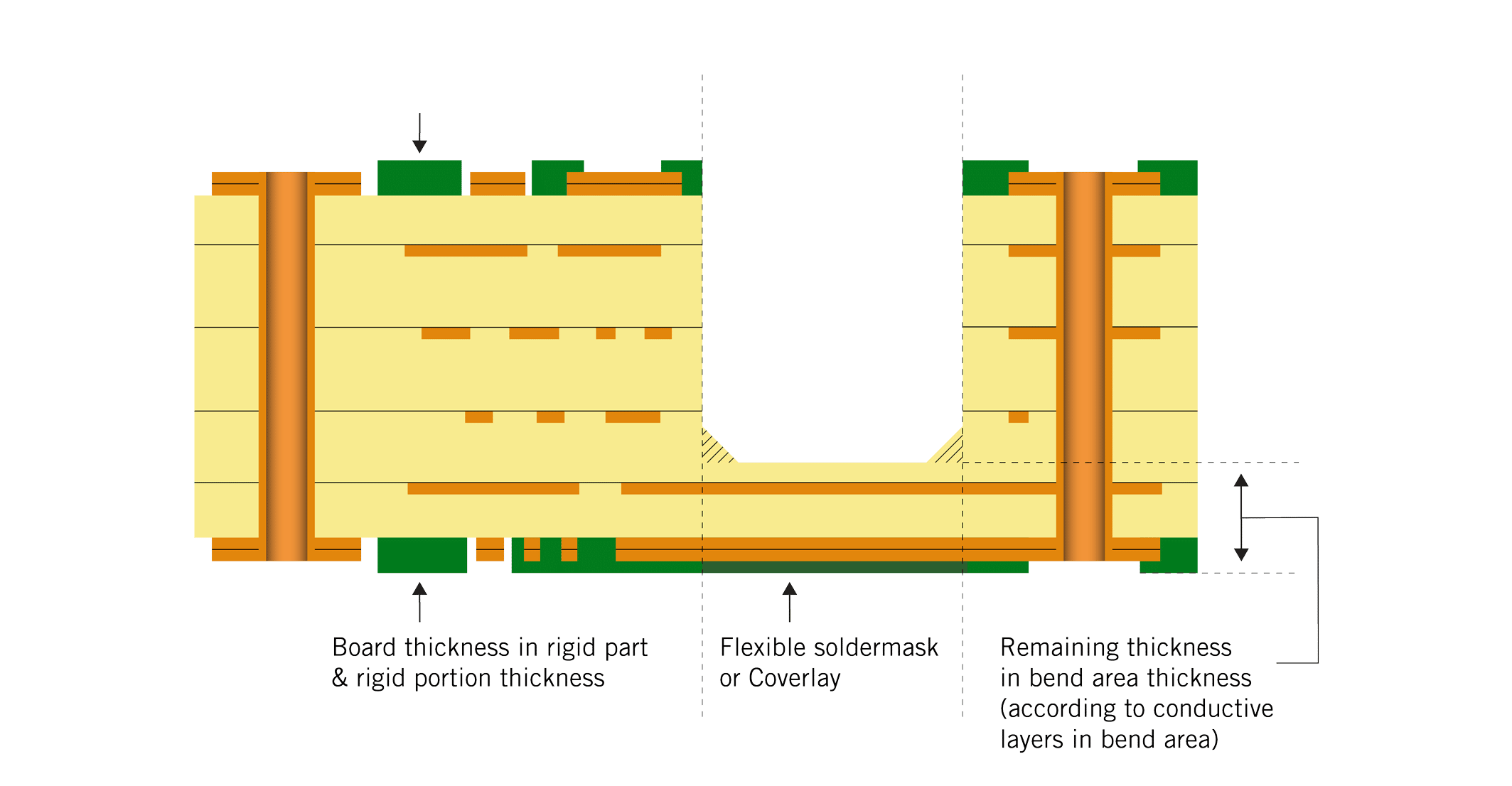
How do you calculate correct length of flex part of a rigid flex structure to allow for minimum bend radius?
Detailed recommendations can be found in IPC-2223, sections 5.2.3.3 for both static and dynamic bends and should be used for final design verification. However, some basic guidelines based upon the thickness of the flex material can be seen below:

FLEX TYPE | MINIMUM BEND RADIUS |
---|---|
Single sided flex | 3 – 6 x circuit thickness |
Double sided flex | 7 – 10 x circuit thickness |
Multilayer flex | 10 – 15 x circuit thickness |
Dynamic application | 20 – 40 x circuit thickness |
What are the available structures for flex and rigid flex PCBs?
There are numerous, different structures available. The more common ones are defined below:
Single sided flex (IPC-60103 type 1) Coverlay (polyimide + adhesive) bonded onto an adhesiveless single sided FPC core. With or without stiffeners.

Double sided flex (IPC-6013 type 2) Coverlay bonded onto both sided of an adhesiveless double-sided FPC core (two conductive layers) with plated through holes. With or without stiffeners.

Multilayer flex (IPC-6013 type 3) Coverlay bonded on both sides of an adhesiveless construction containing three or more conductive layers with plated through holes. With or without stiffener. Capability is 4L.
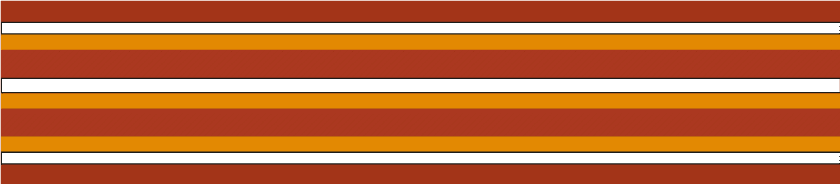
Traditional rigid flex construction (IPC-6013 type 4) Multilayer rigid and flexible circuit combination containing three or more layers with plated through holes. Capability is 22L with 10L flex layers.
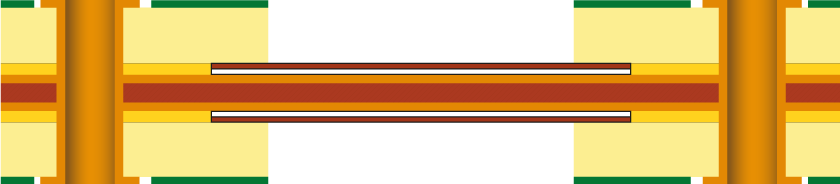
Asymmetrical rigid flex construction, where the FPC is situated on the outer layer of the rigid construction. Containing three or more layers with plated through holes.
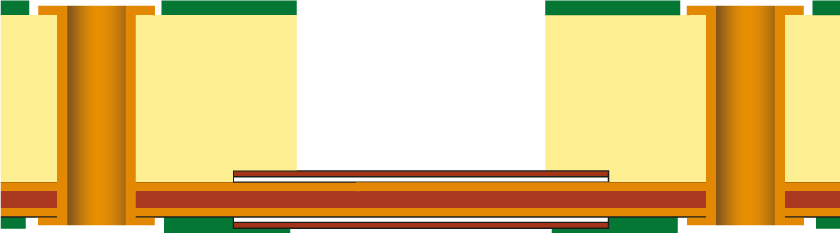
Multilayer rigid flex construction with buried / blind via (microvia) as part of the rigid construction. 2 layers of microvia are achievable. Construction may also include two rigid structures as part of a homogeneous build. Capability is 2+n+2 HDI structure
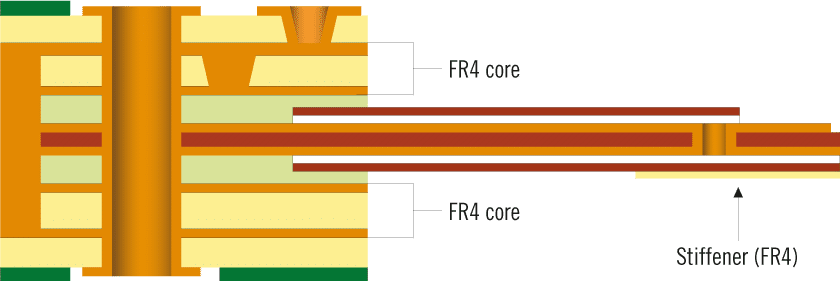
Book-binder and air-gap build – a complex build. With spaces between layers of flex to allow for improved flexing of the FPC. Flex layers may be of different lengths on the book-binder constructions to minimize compression of inner flex layers within bend radius.
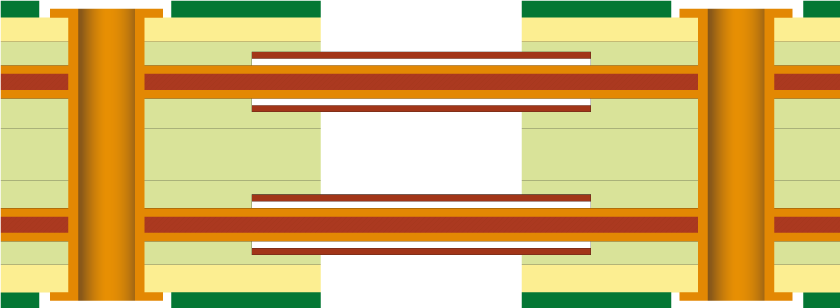