We know that good reliability is secured by achieving a good balance between verification on a product level and verification of the process. It cannot be achieved by screening or sorting on a product level – you cannot ‘inspect in’ good quality or reliability as the old adage goes.
Classifications according IPC
- Class 1: General Electronic Products
Consumer products, some computer and computer peripherals
Cosmetic imperfection is not important
Major requirement is function of the completed printed board. - Class 2: Dedicated Service Electronic Products
Communication equipment, sophisticated business machines, and instruments
High performance and extended life are required, and for which uninterrupted services is desired, but is not critical.
Certain cosmetic imperfections are allowed - Class 3: High Reliability Electronic Products
Continue performance is critical
Life support
Equipment downtime cannot be tolerated
Often used for: Medical, military, aerospace, automotive
However, it is not as simple as taking any design and then demanding class 3 compliance, the design itself must allow support for the demands of IPC class 3 – for example the relationship between the drill size and pad size drive the requirement for annular ring.
Choosing the right factory
This takes into account the challenges in terms of factory selection, as, in many cases, the quality of the factory has a direct relationship to the process control in place that governs the ability of the factory to achieve those demands.
We carefully select the factories who we believe are able to work with us and the varying demands of our customers.
The audit qualification is the culmination of a long and detailed process and is performed by three experts from NCAB Factory Management and that takes place during 3 – 4 days and covers the full process (from receipt of the order to shipping) with the focus on the production process the most detailed.
Wendy Liu, Quality Manager NCAB Group China during an audit.
NCAB Group PCB Product Specification
This level of evaluation and review of process control and ability to achieve tighter acceptance levels is what enables us to have confidence in the promotion of our class 3 solutions.
However, when we look at the extra verification demands associated with IPC class 3, we understand that the amount of verification drives the unit cost upwards dramatically and for some applications this is absolutely justified, yet for others the justification between verification and cost is a difficult one.
This does not detract from the quality or the underlying reliability of the product, it is simply that the extra costs are incurred due the heightened verification to prove that the process controls have worked well, specifically when we consider the number of microsections to review internally observable characteristics.
This is where our class 3 solutions offer a credible option for our customers. We maintain the IPC demands associated with the product and process control and verify the ability of the factory to achieve the requirements of the design, yet the amount of verification is where we propose the cost effective solutions to the customer based upon the application itself:
NCAB Level 1
Full verification according to IPC-6012 table 4-2, 4-3
– Meeting end customer demands
– Limited supply chain options
– Extremely high cost
– Recommended for product with extreme demands (nuclear, deep sea, aviation applications)
NCAB Level 2
Production and verification according to IPC A 600, IPC 6012, micro-sectioning according to table 4-2 and 4-3 AQL 4.0. Except for less than 26 manufacturing panels when two micro-sections per production batch applies.
– Meeting the majority of main end customers’ demands (also high reliability)
– Fairly cost effective
– Dual sourcing possible / less limitations on supply chain
– Recommended for product with very high demands (medicine, industrial)
NCAB Level 3
Production and verification according to IPC A 600, IPC 6012, two micro-sections/production batch.
– Meeting a specific end customers’ demands
– Cost effective
– Multi sourcing possible
– Recommended for most products (industrial, automotive)
Whilst we have touched upon 3 key aspects of reliability that relate directly to the IPC standards (Design and capability, Process control and Verification), there is one final point that cannot be underestimated and that is the product specification – without a good product specification it is almost impossible to both convey and verify that the product meets the demands.
This is why we have defined our own PCB Product Specification as it is the small details which can make all the difference and even though the equipment and process controls may be the same across different sources, our PCB product specification details exactly what we want and our training with the factories QA teams ensure that they truly understand and can achieve it. In doing this we have confidence that our PCB’s have quality and reliability built into them.
Mickaël Cavoleau, is part of NCAB’s Technical Council and been involved in the assembly part of the electronics supply chain with a lead French EMS company, he has insight into what is needed on a bare board level in order to meet the reliability demands of the final product.
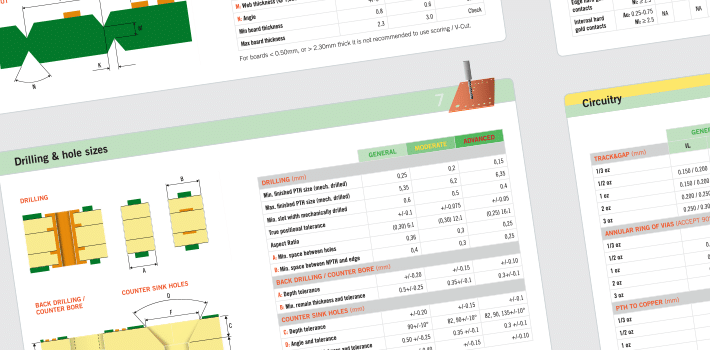
PCB design tools
For more advice about PCB design or applications of PCBs, we
have different PCB tools that can be downloaded for free.