The benefits of via-in-pad designs are well documented. From reduction of inductance to increased density, via-in-pad has become an essential tool for designers when navigating the routing challenges of fine pitch array packages that have become mainstays in today’s BOMs but there are trade-offs that must be considered.
The basic concept is elegant. The via-in-pad design methodology allows the designer to place the via right beneath the component contact pad. Hence the reduction of inductance plus the added benefit of improved routing density which can lead to higher density per layer. The net result is more routing in less space and a smaller PCBs footprint. It is another miniaturization tool that can drive cost down.
However, there are trade-offs when implementing via-in-pad technology. The process may increase the PCB cost. The reason is that the via-in-pad technique requires both additional process steps and extra materials. Added costs are found in both the extra materials used, including epoxy or metal based via fill materials and copper cap plating processes, as well as added process steps like vacuum via fill, curing, planarization and secondary plating operations. There is also the general challenge that results from producing a higher density PCB.
On the design side there are numerous benefits that can be exploited in via-in-pad technology. If via fill is done with thermally conductive materials such as copper or silver epoxy pastes, the design can also be used to provide a site specific thermal management solution. Copper pastes as an example have a 10 – 15 W/mK thermal conductivity compared to solder mask fill at 0.25 W/mK. For high speed designs, the lower intrinsic inductance created by proximity is ideal to improve signal speeds regardless of material selection. DFA benefits include excellent planar via plugging that results in improved ionic cleanliness as well as a more planer surface that is ideal for low profile components.
Not all designs need via-in-pad. There are some added benefits such as in thermal management and high speed designs where the advantages should be weighed against the costs. However if you are looking at via-in-pad as an option for improving routing for high I/O count in packages below 0.8mm pitch, it can become your most valuable go-to tool.
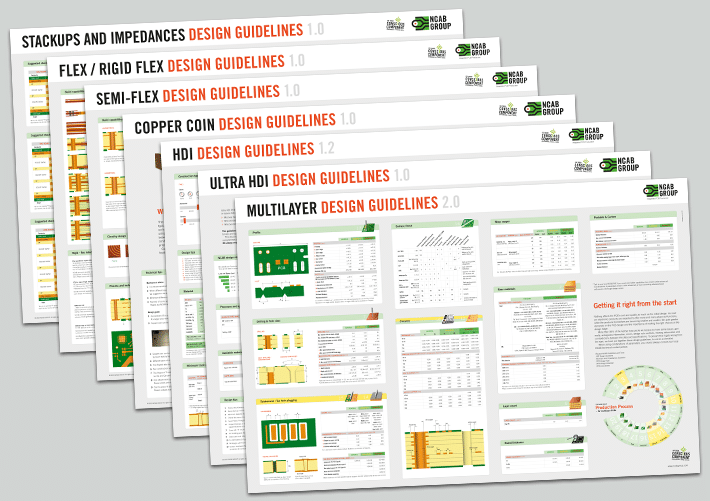
PCB design guidelines
Get it right from the start with our PCB design guidelines. To prevent getting it wrong from the start, we have put together our design guidelines, to use as a checklist.