But.. At some point we still need to be able to demonstrate that the product that we have supplied is correct, not just in terms of the physical characteristics, but also against that specification that ultimately determines functionality. Have the correct materials been used? Do we have the correct dielectric spacing? Etc.
This is where the NCAB Group has implemented what we see as market leading certificate of compliance report that does exactly that.
Some may call this document a first article inspection report, or an outgoing report but as this is our final piece of the production process that verifies that all that has gone before is correct, we call it our certificate of compliance. Whilst a first article report is used only for the first batch delivered, NCAB Group provides this document for each code date supplied from our partner factories in China and unlike an inspection report, this document is a complete report that covers not just internal or externally visible features but provides complete measured and verified data.
The aim of this document is for our customer to be fully assured that each new batch from our approved factories, have been thoroughly verified in accordance against customer or NCAB specifications.
Oh, did we mention this also comes at no extra cost?
What does this document cover?
The report starts by providing a confirmation statement that PCBs we have shipped are compliant with purchasing specifications and/or drawings (typical quality documents). This section also confirms that customer part number, the customer purchase order, the code date so that any incoming goods department can match against their own documents. This statement also confirms that all our PCBs are 100% electrically tested and passed.
Moving on from this overview statement, we include statements regarding ROHS and REACH conformity.
Next we have the Outgoing Report section and this is where we start to get into the detail and this is seen as one of the most important parts of the report.
Why? One example is that this is where we compare the specification or demands for the material such as the base materials, soldermask and silkscreen against what we have used in the construction of the boards. We also confirm brand used along with the batch number for the traceability.
Controlling different aspects of the board
However this is not enough and we continue to look at other aspects that can not only influence compliance, but also have an impact on the reliability of the product, such as surface finish thicknesses, internal and external base copper along with finished copper thickness for both surface, through holes, microvia holes, cap plating, etc..
We are control freaks and this is the conformity that helps us sleep at night.
Did we mention that the surface finish thickness is verified by x-ray florescence? For ENIG, the factory check the nickel and the gold thickness and we know that both have an impact on how good the product solders.
Talking of copper thickness verification, this can only be completed through verification of the microsection. The copper thickness is verified using both the copper average and the min copper thickness according to IPC-A600 class 3 (so 25µm min and 20µm min). Even if you require IPC class 2 we will always supply class 3 copper as standard.
If the design specifically includes such designs then as stated the factory will verify the copper thickness in buried or blind vias, and the copper wrap or copper cap thickness.
We don´t like surprises
All the internally observable criteria’s are checked according to IPC-A600 or IPC6012 (Plating Crack, Plating Void, Copper Crack…). The quality of the drilling is also checked by measuring the roughness of hole (<25µm).
Microsections should include the smallest via hole location and shall be evaluated after 3 cycles of thermal stress (288°C+/-5C, 10 seconds).
To ensure no surprises when the boards come to be assembled we also demand that solderability tests are carried out in order to confirm that the finish on the product is actually “solderable”. Solderability of all surfaces shall be as per J-STD-003 and the result must demonstrate ≥ 95% wetting on each pad.
NCAB also knows that in many cases the electrical characteristics of the product are sensitive and in many cases we have to build the boards with a specific, pre-defined construction in mind that has critical dielectric spacing, between conductor layers, needed. As such, when we do our microsections we also confirm that the board thickness and the stack-up are according to the master drawing – the copper thickness on each layers (internal and external layers) are measured. Each dielectric thickness is measured.
Beyond the demands of IPC
If the PCB has some impedance requirements included, then the factory will document the demands including trace width/spacing, the impedance value for each layers and then measure the impedance on the finished product, along with an image that verifies the construct used.
Other, more standard elements that we verify include the outline of the physical PCB along with the hole sizes and in pour report the dimensions form the master drawing are defined and checked with actual results listed. The more complex the board, then the more measurements we may have to take.
Each and every board from each and every batch we supply is also subjected to cleaning before packing. Not only this but we have our factories test a representative boards according to IPC-TM-650 2.3.25 so that we can be sure that any ionic contamination level shall not be greater than 1.00μg/cm² of sodium chloride equivalent ionic contamination. This is above and beyond the demands of IPC and the final result along with a scan of the result graph is provided inside the report.
Finally, we know that some customers like to have a solder sample or a sample that they can use as a point of reference for future evaluation or reference. So…. As standard this is included as part of the report, the customer will receive the “solder sample” along with a corresponding microsection (and impedance coupons if it’s required by the customer) should they be needed.
Perhaps this is something that you have not noticed before, perhaps you have never had the need, but if you wish to review the document to understand why we are proud of this final piece of verification then you can find this in the NCAB box that has been sealed using Dark Blue tape (width 15-25mm) around the top of box.
We know that when all requirements, or specifications, are met, it has achieved quality.
READ MORE ABOUT OUR PRODUCT SPECIFICATION »
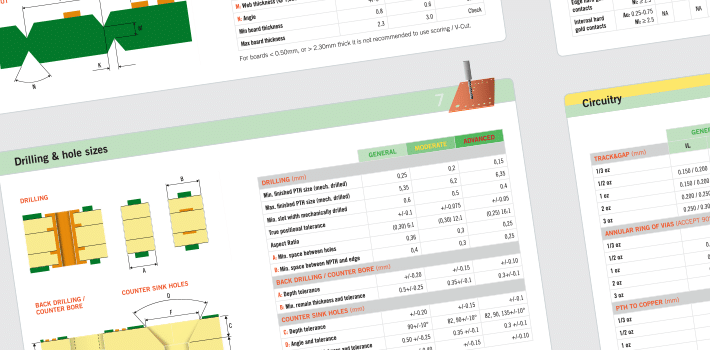
PCB design tools
For more advice about PCB design or applications of PCBs, we
have different PCB tools that can be downloaded for free.