PCBs used in fire safety products, such as fire detectors and fire panels, are generally a less complex design. However, these products exist to save lives and their reliability is crucial. Sourcing reliable PCBs is fundamental for fire safety industry manufacturers in order to pass demanding tests and prevent expensive and damaging field failures in their end-products.
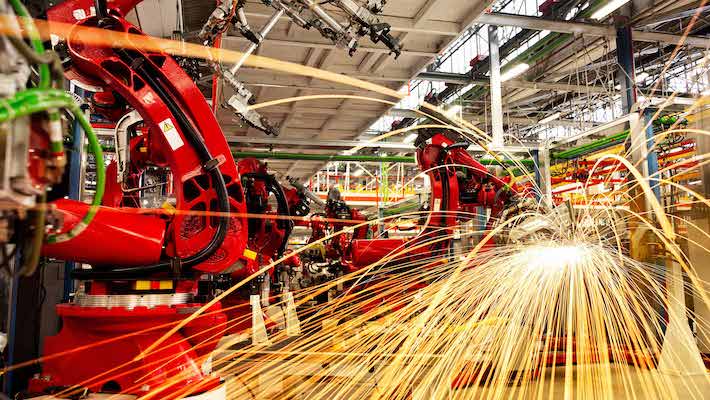
When producing PCBs for the fire safety industry, there are some specific challenges. Although these boards are, generally speaking, not particularly complex, as they usually consist of two- to four-layer constructions and have a standard specification, there are, nevertheless, constraints when it comes to board size and power consumption. End-products have a long service life and the PCBs in them have to endure harsh environments and be resistant to shock. Robustness and reliability are key for end-products that are supposed to do one thing, but do it well, especially when people’s health and even lives are at stake.
What is important when making PCBs for the fire safety industry?
To achieve the desired reliability in PCBs for the fire safety industry, you need robust design, an ability to get maximum performance out of factories, and, in some crucial areas, go beyond IPC Class 2 requirements in your PCB specification.
We have a strong position as a supplier to the industry, with a large number of customers and many hundreds of projects behind us. The PCBs we deliver to the industry predominantly end up in wired and wireless fire detectors used in residential or commercial buildings. We also supply boards used in fire panels and alarm systems.
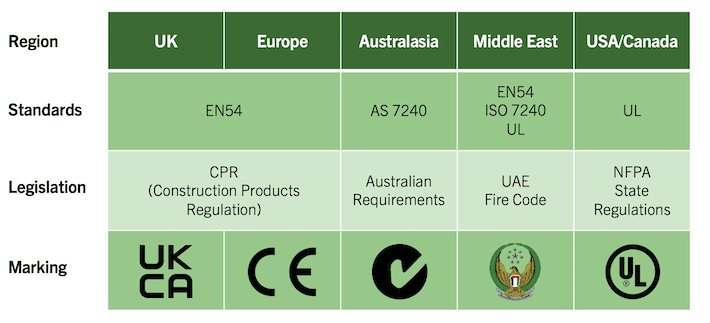
Key specifications for reliability
We have our own bespoke PCB specification that is used for all PCBs we supply to customers. Several important PCB features specified are unique for us and/or go beyond the industry standard IPC Class 2. This is one of the factors that make it possible for us to provide a more reliable product than many of our competitors. When it comes to the fire safety industry, a few of these features are especially important to ensure robust and reliable end-products:
- 25 micron nominal hole plating as per IPC Class 3
Going beyond the 20 micron copper plating specified in IPC Class 2 to a more robust 25 micron plating is proven to be ideal with regards to the shock testing of fire safety products. The risk of copper cracking at the distress is reduced and thereby the risk of failing the test. - Specified soldermask thickness
This requirement, that goes beyond IPC altogether, ensures a better soldermask coverage with less low-spot weak areas. This is proven to help protect the copper in the SO2 corrosion testing of fire safety products, thereby reducing the risk of failure. - No track welding or open circuit repair
Although repairs can be very well executed, they always constitute a risk compared to a board that has not been repaired. Reliability demands products that are spot-on. - Only internationally known base materials used
No locally sourced or unknown materials are accepted. This ensures the use of materials that are fit to purpose and will deliver what they are meant to. - Tight control on age of specific finishes
Customers do not use all boards immediately on delivery. If the age of certain finishes is not under control it can cause problems for solderability and increase the risk of moisture ingression, making the board less reliable. - Tolerance for copper clad laminate is IPC4101 class B/L
Control of dielectric spacing is becoming more critical to the functionality of products. - Robust qualification and release process for every purchase order
The customer can rest assured that all board specifications have been verified through the release process.
Maximum performance out of factories
Although the technical challenges are far from insurmountable when producing PCBs for the fire safety industry, factories still need to perform at their maximum to ensure the required reliability of the boards. Our Factory Management team are present at factories daily especially in the key factories where most of the fire safety industry PCBs are manufactured, to ensure that all our specifications and quality demands are met.
Sustainability increasingly in focus
Like in many other industries today, sustainability is an ever more important trend and a driving factor for developments within the fire safety industry. Having become ISO-26000 accredited already in 2014 and adhering to that practice since then, we follow up and report on the group’s sustainability efforts annually. We are now seeing more and more customers signing up to different sustainability programs and are working alongside them in this.
In PCB manufacturing, we aim at making production as sustainable as possible. Working with our customers we are looking to design for sustainability, considering things like PCB circuit sizes and efficient panel utilization. Producing more boards from the same panel means reducing the amount of material and energy going into production while at the same time minimizing the amount of waste from it.